摘要
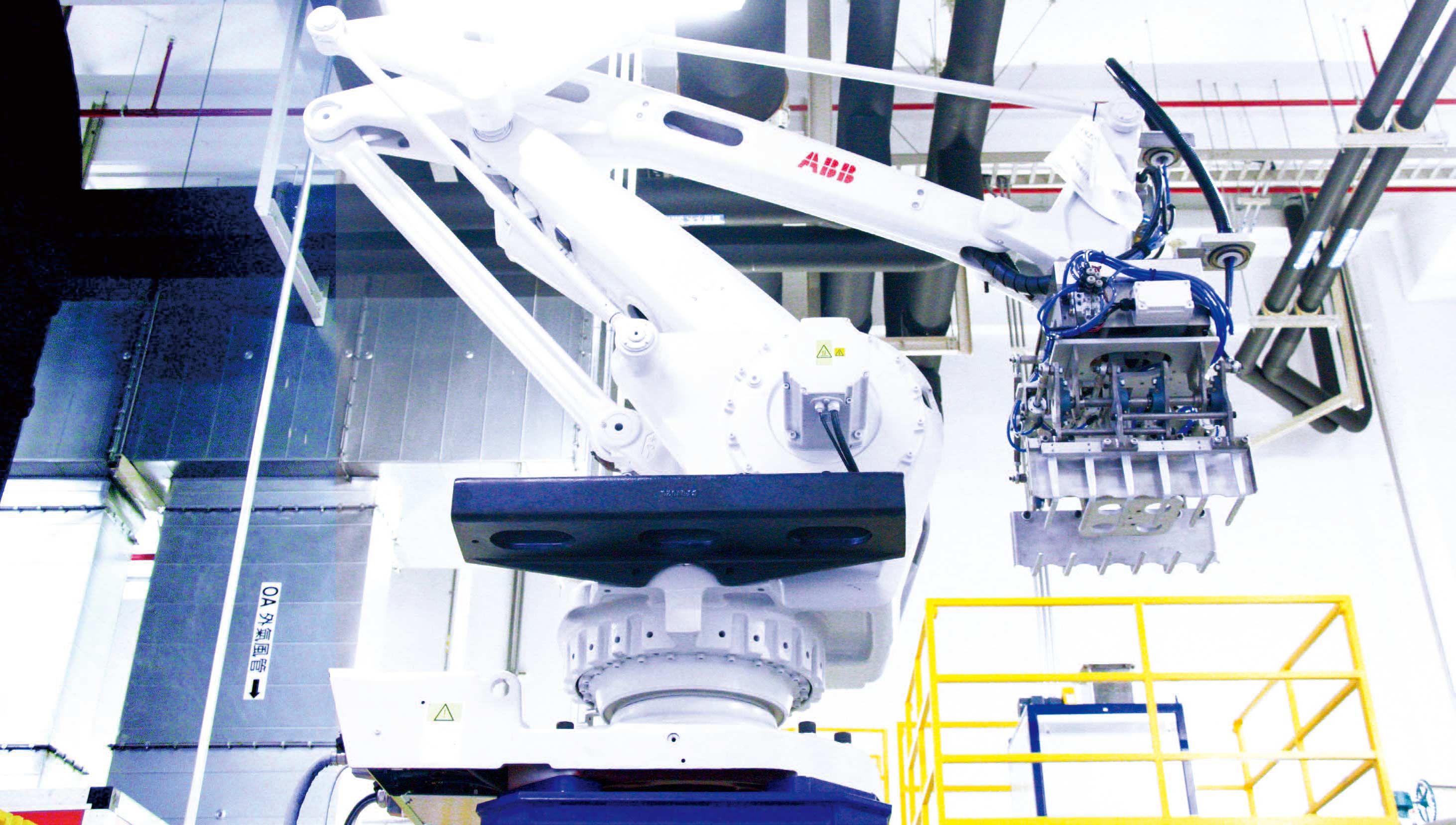
半導體廢硫酸回收轉製成工業級硫酸銨乾燥技術探討
Keywords / Ammonia Removal3,(NH4)2SO42,Sulfuric Acid6,Caustic Wastewater2
前言
2018年開始硫酸銨廢液躍居製程最大宗廢棄物,導致委外清運處理成本居高不下。除了以硫酸銨提濃進行源頭減量,更重要的是思考如何將硫酸銨廢液活化再利用。於是2018年F15A申請為台積首座跨足化工產業廠房,建置第一套半導體業硫酸銨乾燥結晶系統(產業類別第18化學材料製造業、主要產品第181類基本化學材料,原登記文號中商字第1070015617號,2018/08/29獲中科管理局核准),並於2018年底產出台積第一批工業級硫酸銨成品委外銷售,成功開啟了資源再生活化的康莊大道。
文獻探討
結晶技術探討
結晶是指物質從氣態或液態轉變成具有一定形狀堅硬晶體的過程,被廣泛應用在化工產業中進行溶液中溶質的純化,一般將結晶技術以降低溶質在溶劑中的溶解度方法來區分,可分為反應式結晶(Reaction Crystallization)、蒸發式結晶(Eva-porative Crystallization)、降溫式結晶(Cooling Crystallization)及反溶劑式(Antisolvent Crystallization)結晶四種,而在硫酸銨結晶技術的選用上,蒸發式結晶占80~90%。蒸發式結晶利用熱能去除溶液中的水分,使硫酸銨溶液達到過飽和狀態進而產生結晶,結晶成品的品質受硫酸銨母液濃度、結晶罐蒸發速率等諸多變數影響,如何控制含晶量比例,建立最適化之生產操作條件,實為最重要之結晶管理機制。(毛國芳,1992)。
結晶裝置之設計是以原始蒸發裝置為基礎發展而來,從古老的圓鍋、小方鍋、小平鍋、大平鍋進化到近代工業用的蒸發結晶罐,並且循環方式又分為正、逆循環。這類結晶罐為早期運用於化工產業較普遍形式。為強化熱傳導與蒸發效率,更同時用以提高產品質量與粒度為目的進行設計,在蒸發過程中嚴格控制液態原料的過飽和度、晶核形成及成長環境,產出符合需求的結晶產品,設計合適的結晶罐,以獲得更大的結晶顆粒,因此藉由更動結晶罐內部構造,衍伸出各種不同形式結晶罐,因應不同入出料產品需求(張方坤,2018)。
結晶罐的種類
目前普遍用於化工產業的結晶罐有FC (Force Circulation)、OSLO、DTB (Draft Tube Crystallizer)三種型式,其中以FC構造最為簡單,結晶罐體積較小,產出成品粒徑最小(0.7~2.6mm),DTB罐體型式以軸流式泵浦作為控制單元,有效進行結晶顆粒尺寸控制(2.6~6mm),OSLO結晶罐體積最為龐大,一般設計於戶外使用,用於產出成品粒徑要求較高產業(>6mm) 圖1 (GEA,1881)。
圖1、結晶罐類型
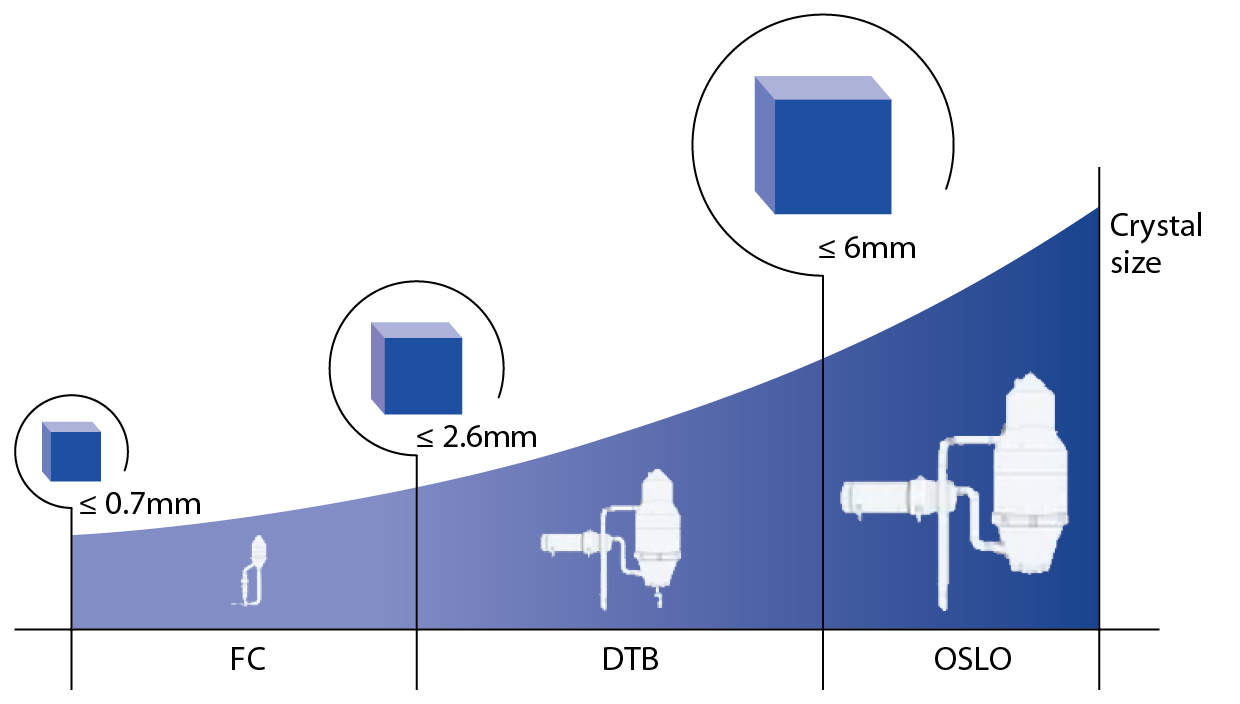
FC型式結晶罐 (Forced Circulation crystallizer)
FC型結晶罐 圖2由結晶罐、強制熱交換器、強制循環泵及抽真空系統四個主要單元組成。結晶罐內溶液由強制循環泵提供動能使溶液流經熱交換器不斷循環,維持結晶罐內蒸發所需溫度,輔以抽真空系統抽除結晶罐內蒸發所產生的蒸汽,使結晶罐內維持負壓狀態降低蒸發所需溫度。FC型式結晶罐由於簡便的設計與運轉方式於化工產業廣泛使用,因其產出之結晶以硫酸銨而言相對較小,故大多僅用在較低產能或因硫酸銨溶液中含有高濃度不純物,而無法產出粗粒徑硫酸銨結晶的地方,例如氣洗設備排水或較大結晶罐濃排水等。
圖2、FC結晶蒸發罐
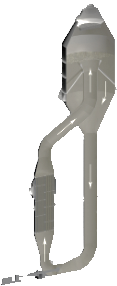
OSLO型式結晶罐
OSLO (挪威奧斯陸) 圖3 Krystal A/S的F. Jeremiassen於1924年發明了這款結晶罐,並用設計起源城市的名稱為它命名。OSLO與FC型式結晶罐運作原理相仿,差別在於OSLO結晶罐下半部體積較大,為求得較大尺寸結晶產品,結晶在蒸發室析出後沿內管緩慢沉降至罐體下半部使晶體間發生碰撞結合,以得到較大尺寸晶粒,然而物料在導流管內開始汽化,產生過飽和度,形成晶體,由於流體的流動及結晶罐壁面溫度相對內部較低,會在分離室壁面附近形成最大過飽和區,而容易在結晶罐內壁發生結垢,晶垢長到一定的程度隨液面波動而脫落,會進一步造成管道堵塞,並且由於過飽和度分布不均,晶體的粒度也不好控制(黃欣等,2019)。
圖3、OSLO結晶蒸發罐
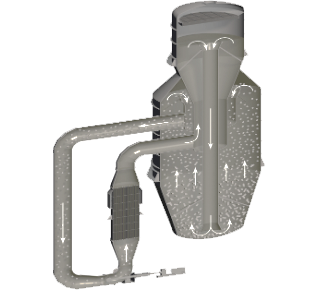
DTB 型式結晶罐
DTB (Draft Tube Battle)結晶罐 圖4又稱渦流結晶罐,DTB結晶罐分別排出兩股流體,一股為含有產品晶體的漿料,另一股則是含有少量粉末的母液(飽和溶劑)。DTB結晶罐特有的晶體形成區域和經過淨化的母液使它能夠定義運動參數,從而確定成核速度和晶體生長速度。DTB型式結晶罐的特色在於內部導流管與擋板的設計,內部導流管設計為上方開口較大形式,使液體流至液體表面時流速較為緩和,避免發生潑濺,減少結晶罐內部壁面的晶疤生成;擋板將結晶罐內分成兩區域,結晶區:在該區域進行實際結晶過程,進料由結晶罐導流管底部進入,通過軸流泵的推動將溶液送往液面過飽和區形成結晶,軸流泵可設計於結晶罐上方或下方,如安裝於上方缺點為軸心易發生結垢現象,如安裝於下方可避免此問題,但安裝於下部的軸流泵則須注意易發生洩漏的問題;分級區:在分級區的頂部設有物料出口,藉由擋板設計控制流體向上的流速對結晶顆粒進行分級,較小的結晶顆粒會被導引往強制熱交換器再製成新的結晶顆粒。
圖4、DTB結晶蒸發罐
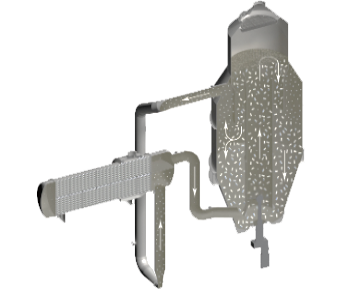
結晶罐比較
FC型式結晶罐產出顆粒粒徑與結晶罐設計高度呈正相關,在結晶罐高度相同的狀況下FC型式產出的結晶粒徑較小,且結晶罐內溶液擾動及強制熱交換器熱能提供皆仰賴強制循環泵,故結晶罐內流體流速較無調整,容易於液面產生噴濺,若操作不慎壓縮機吸入溶液將導致故障。DTB型式結晶罐利用軸流泵控制內部溶液滯留時間,可有效控制結晶粒徑大小,但需注意軸流泵需保持運轉狀態,若停止時間過長結晶罐內葉片周圍會有結晶產生,直接啟動會造成軸流泵損壞。OSLO型式結晶占地較大,所產生之結晶粒徑也最大顆,但因其內部溶液飽和狀態無法有效控制,故易於內部產生較大結晶,增加停機清洗的人員負擔 表1。
Type |
FC |
DTB |
OSLO |
---|---|---|---|
粒徑 |
<0.7mm |
<2.6mm |
<6mm |
結垢 |
輕微 |
輕微 |
嚴重 |
所需空間 |
小 |
中 |
大 |
優點 |
占地面積較小,單元簡化 |
可控制停留時間,有效達成粒徑控制 |
成品粒徑較大 |
缺點 |
成品粒徑較小,易發生噴濺導致壓縮機故障 |
需注意電力供應穩定,避免軸流泵停止運轉 |
結晶罐內飽和狀態較難控制,大顆粒結晶易滯留於結晶罐內,不適用於連續生產操作 |
硫酸銨結晶系統運轉實務
FC型硫酸銨結晶系統運轉實務
結晶蒸發系統操作包含許多重要參數,各項因子往往牽一髮而動全身,F15A於2018年開始以FC型結晶罐進行硫酸銨結晶產出的模組試驗,其流程圖如 圖5,系統產出硫酸銨成品極易受操作參數影響,以下針對各項參數做說明及探討。
圖5、FC系統流程
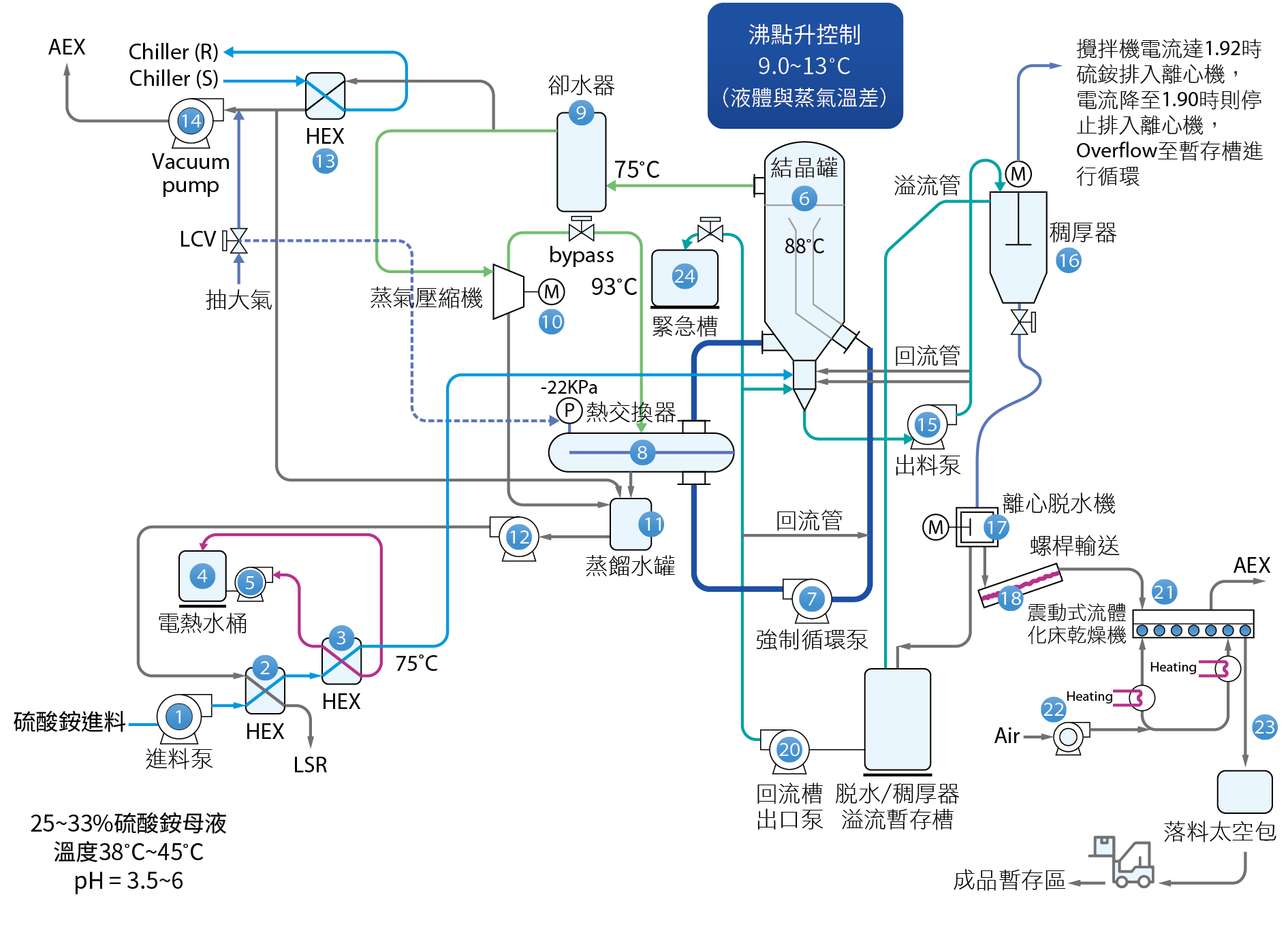
入料溫度控制
系統由電熱供應啟機升溫一次熱源,藉由(2)(3)板熱進行熱交換,將來源母液升溫達一次蒸氣產生溫度,本系統設定為75度
壓縮機啟機頻率控制
結晶罐內母液持續藉由強制循環泵循環(7),透過強制熱交換器升溫,待結晶罐內母液溫度達75度以上(結晶罐內一次蒸氣產生),壓縮機(10)逐步升載將該股蒸氣加壓,達成溫升後再藉由強制熱交換器將來源母液升溫,如此達成循環升溫效果,但壓縮機升載頻率不宜過快,電流控制約不超過額定電流值±10%,避免過載跳脫。
結晶罐內母液溫度
結晶罐(6)內溶液溫度可藉由溫度計回傳監測,操作溫度會影響結晶罐蒸發速率並改變結晶成核及成長速率,蒸發速率愈低晶體成長速率愈慢,產出之結晶顆粒愈小。本案操作溫度在85~95度,當操作溫度大於95度時,代表結晶罐內不純物濃度過高,會開啟濃排並補入新鮮母液降低結晶罐內不純物濃度使操作溫度恢復至操作區間。而溫度若低於85度除了影響蒸發速率外,會使結晶罐內飽和度上升導致結晶析出,經驗上溫度低於60度結晶會大量析出 圖6,堵塞結晶罐與管路。
圖6、硫酸銨過飽和溶液冷卻析出結晶
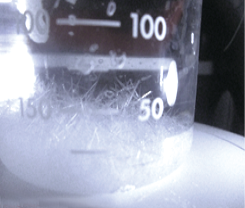
結晶罐內比重(濃度)檢測
比重是觀察結晶技術的重要因子,母液體導入系統後,需於出料泵取樣(15)確認濃度變化,以200ml 燒杯盛裝提濃後母液,扣除燒杯空重後,重量除體積可計算得知比重,對照比重與濃度關係圖可得知母液濃度 圖7。現場操作經驗比重在1.22~1.26換算濃度約40%~45%,為適當操作濃度區間,又稱為硫酸銨結晶介穩區。當溶液濃度達到45%以上屬過飽和溶液結晶成核速率大於生長速率適合晶核產生;而當溶液處於介穩區,結晶成長速率大幅上升,適合結晶粒徑成長;若硫酸銨濃度>50%則屬於不穩定區,系統操作於此區間將導致結晶過量增長,易發生管路堵塞與結晶罐內結垢狀況,使系統難以維持穩定。
圖7、硫酸銨濃度與溫度比重關係
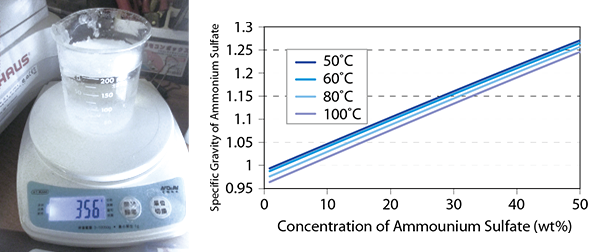
出料固液比檢測
溶液中固體含量與稠厚器攪拌機電流呈正相關,本系統設計以稠厚器攪拌機電流作為稠厚器下料判斷依據,故建立固液比與攪拌機電流的關係式極為重要。本系統開始運轉後定時於出料泵取樣,以imhoff cone量桶觀察固液體比例 圖8,再使用濾紙過濾秤重獲取固體成分方式換算固液體成分比例。本系統量測之固液比與攪拌機反饋電流關係紀錄如 表2。
圖8、硫酸銨半成品晶漿固液體比例

攪拌機電流 |
結晶罐溫度 (A) |
蒸氣溫度 (B) |
沸點升 (A)-(B) |
壓縮機出口蒸氣溫度 |
真空度 |
固液比 |
---|---|---|---|---|---|---|
AMP |
°C |
°C |
°C |
°C |
Kpa |
g/ml |
1.908 |
89.4 |
78.3 |
11.1 |
92.7 |
-56.8 |
6.93% |
1.906 |
89.2 |
78 |
11.2 |
92.7 |
-56.8 |
4.42% |
1.902 |
88 |
78 |
10 |
92.7 |
-56.8 |
3.37% |
1.900 |
87.6 |
77.3 |
10.3 |
92.7 |
-59.2 |
3.14% |
1.898 |
88.6 |
78 |
10.6 |
92.7 |
-57.7 |
1.64% |
<1.898 |
85 |
78 |
7 |
92 |
-65 |
1.64% |
轉換率
由實際導入來源濃度25~33%液態硫酸銨製成乾燥成品,其中包括半成品稀釋、氯離子累積排放等操作,由實務經驗得知,1公噸液態硫酸銨去除水分後可製成0.3公噸再生產品,轉換率約30%。
DTB型結晶罐系統介紹與設計
經歷FC型式結晶罐實廠操作經驗,考量F15A現場建置環境用地、結晶罐高度限制以及對成品粒徑的要求,最後選用DTB型式結晶罐作為作為正式硫酸銨結晶系統的主體,以下針對DTB型式結晶罐系統做詳細流程及設計需注意事項介紹 圖9。
圖9、DTB系統方塊圖
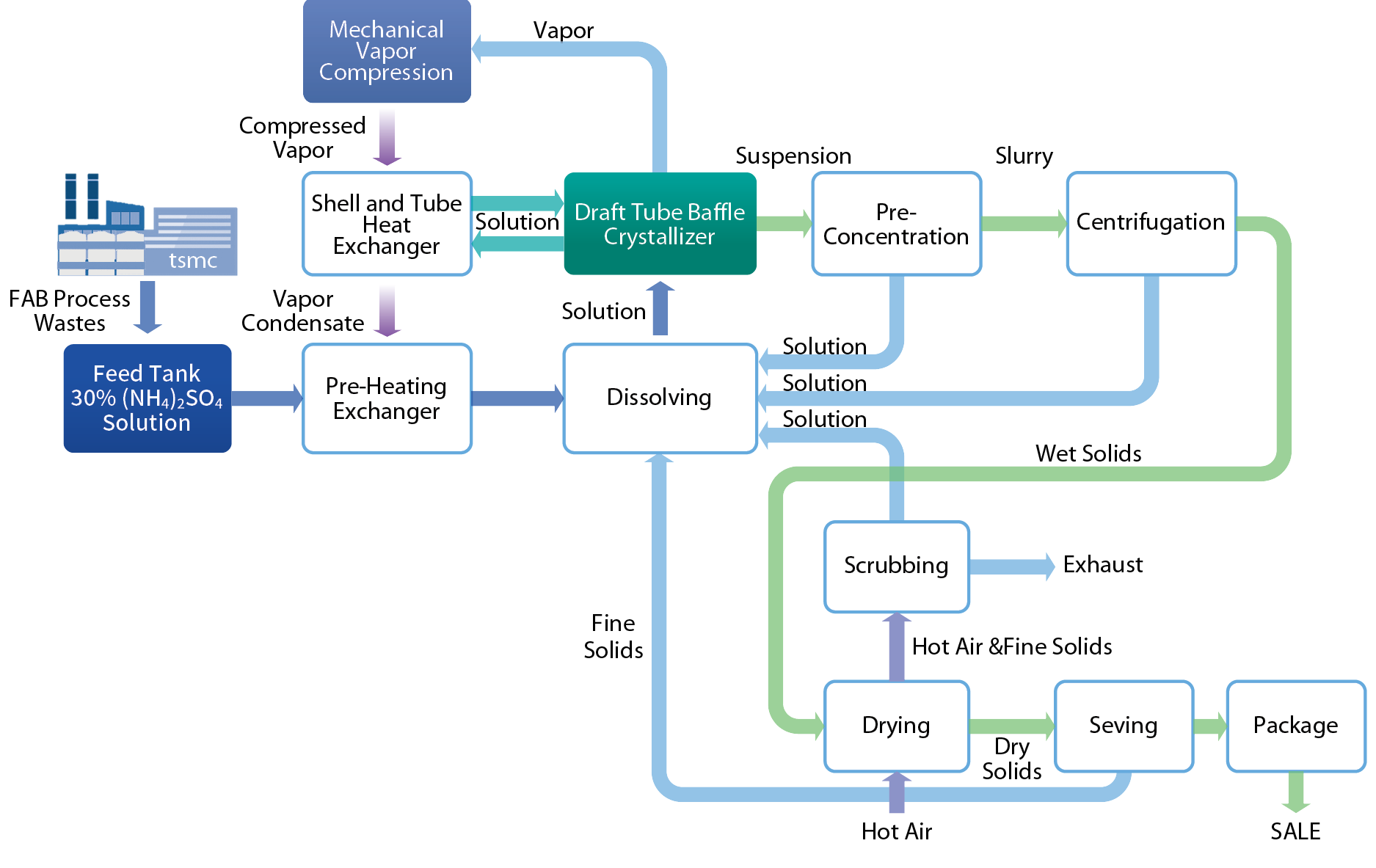
DTB硫酸銨乾燥系統流程
從氨氮廢水資源化系統產出的液態30%硫酸銨(溫度25℃),由收集槽輸送進入板式熱交換器 (Pre-Heating Exchanger),將溫度升溫至96℃後進入母液罐(Dissolving Tank),母液罐回收多股回收溶液及固體成份,包含有水旋風固液分離器(Pre-Concentration)和離心脫水機(Centrifugation) 過濾後過飽和溶液、濕式洗滌塔洗滌水(Scrubbing) 和振篩機(Sieving) 過篩後粒徑較小成品,經由母液罐攪拌混和後,槽體內硫酸銨濃度上升至37%。母液罐出口母液泵採連續運轉,透過結晶罐液位計控制母液罐出口比例控制閥件,以維持結晶罐液位於適當的高度。結晶罐外則設置有殼管式強制循環熱交換器(Shell and Tube Heat Exchanger),透過強制循環泵進行結晶罐外循環,並以蒸汽對母液進行熱交換,達成母液升溫效果,最終結晶罐中硫酸銨母液溫度上升至沸點80~90℃的工作溫度。
結晶乾燥系統於初啟動時,需以電加熱器對來源硫酸銨母液進行升溫,待母液進入結晶罐產生一次蒸氣後,真空系統將一次蒸氣抽至蒸氣再壓縮機(Mechanical Vapor Re-compression)對一次蒸氣加壓產生高溫高壓的二次壓縮蒸汽。本專案設計有兩段串聯式蒸氣壓縮機,蒸汽經由壓縮機後溫度由85℃上升至100℃,此高溫蒸氣可回用至管殼式熱交換器與硫酸銨溶液進行熱交換維持結晶罐內溫度,熱交換後蒸氣發生相轉換形成100℃冷凝水流入蒸餾水罐,此蒸餾水罐內100℃冷凝水會再由泵浦輸送至板式熱交換器對來源母液進行升溫,最終完全取代電加熱器。
結晶過程一般可分為三個階段,過飽和溶液的形成、晶核的生成和結晶的成長階段。結晶罐中高溫母液於液體表面(不穩區)發生閃蒸,將飽和溶液濃度提升為過飽和溶液使硫酸銨晶核析出,伴隨結晶罐內部(介穩區)沉降過程晶粒間碰撞,結晶顆粒將獲得成長,其中晶粒增長程度與結晶顆粒於結晶罐內滯留時間成正比關係。當結晶罐內固成分比重提升後,經由密度計即時監測達到設定值,出料閥件即會開啟出料,將35%固成分晶漿打入水旋風固液分離器,使固液比提升至50%,再進入離心脫水機進行水分脫除,此時固成分比例提升至96%,剩餘水分最後由熱風乾燥床(Drying)去除,最終產出成品含水率<1%,該成品進入振篩機過篩粒徑尺寸,成品達標後進入包裝程序,完成一系列結晶成品生產流程。
DTB硫酸銨乾燥系統設計要領
材質選用上,高濃度硫酸銨具腐蝕性,其中氯離子濃度於高溫系統中更易加劇腐蝕速度,因此與硫酸銨溶液接觸的設備與管材建議使用316L不銹鋼或2205雙相鋼(22%鉻,2.5%鉬及4.5%鎳氮合金)以上不銹鋼材。
管路設計上,因高濃度溶液輸送管道易產生結晶堵塞問題,因此於設計階段需盡減少彎頭,將管道截彎取直,並包覆加熱帶,避免高濃度晶漿冷卻或流速下降導致管路堵塞;此外,非持續性流動管道需設計有傾斜角度及60度熱水清洗口,避免硫酸銨溶液殘留導致管路結晶阻塞。
60度清洗水配置上,結晶罐頂部蒸發室需配置沖洗桶壁管路,以60度熱水進行沖洗效果尤佳,此機制可避免結晶罐桶壁結晶附著、增長、如顆粒附著增長後,大型顆粒剝落後將沉降導致出料管路堵塞。卻水器內卻水格網,設計於壓縮機前攔截小顆粒或泡沫,該格網亦需配置沖淋水進行洗滌,避免濾網堵塞影響蒸發效能。離心脫水機於啟機預熱或進行濾籠清洗程序時需使用60度熱水,定期清洗可避免離心機濾網堵塞導致脫水效果下降。後段乾燥設備亦需配置沖淋水,如發生結垢狀況便於進行保養清潔工作,搭配保養排放、儀錶含氨廢液排放水之回收機制,避免系統因保養清洗工作或異常洩漏狀況影響污水廠放流水質。
結晶罐底部高濃度管路閥件選用,於FC型式硫酸銨結晶系統實務上,曾遭遇結晶罐出料蝶閥被結晶卡死的狀況,後續將閥件更換成桶底閥(Tank Flush Valve),有效解決結晶淤積,閥件堵塞或晶漿流量異常變化的問題。
脫水機選型上推進式離心脫水機(Pusher Type Centrifuge)之脫水效果優於臥式離心脫水機,搭配預增稠/水旋風分離器(hydro cyclone)進行物料預提濃有效確保離心脫水機脫水效能。
結論
秉持「廢棄物極小化、資源極大化」的處理原則,台積公司於2015年開發廢硫酸及氨氮廢水前處理系統,並於2017年擴大應用於各廠,透過廠內再生後的廢硫酸循環做為吸收劑與廢水中氨氮結合轉製為硫酸銨廢液委外再利用。2018年更進一步利用硫酸銨蒸發結晶技術結合機械式蒸氣再壓縮技術建立台積第一套硫酸銨結晶系統,將硫酸銨廢液轉製成工業級硫酸銨產品銷售,成功將使用後的廢硫酸與氨氮廢水結合再生為有價資源循環利用,減少原先需委外處理廢硫酸約90,409噸(等同減少等量之工業級硫酸外購量)及硫酸銨廢液1,956噸,創造新台幣1.8億/年效益(減少委外再利用費用及再生產品銷售費用)[7]。
結晶系統有別於水處理系統,本案初期以FC型式結晶系統累積運轉實務經驗,除了運轉操作熟悉還包含管道設計、沖淋水配置及設備材料選用等方面。最終基於現場用地及產品粒徑考量,選用DTB型式結晶罐作為正式硫酸銨結晶系統的主體,結合先期運轉實務經驗,於竹、中、南科同步建置正式硫酸銨結晶系統,預期在不久的將來,廠內所有硫酸銨廢液將100%轉製為工業級硫酸銨出售,達成硫酸銨廢液零外運的里程碑。
參考文獻
- 王彥飛,蒸發結晶,天津科技大學,2006。
- 毛國芳,硫酸銨結晶技術及品質探討,臺肥月刊,44卷12期,頁51-59,2003。
- 殷萍、衛宏遠(民98)。pH值對硫酸銨溶解度及結晶介穩區的影響,化學工業與工程,26卷2期,2009。
- 張方坤的個人博客,工業結晶的常用方法及工作原理,http://blog.sciencenet.cn/u/zhangfangkun。
- Hofmann G.,Paroli F., Van Esch J., “Crystalli-zation Of Ammonium Sulphate: State Of The Art And New Developments.” Journal ofChemical engineering transactions, Chem Eng Trans, Vol. 17, pp.657-662, 2009.
- 黃欣、陳業鋼、蘇楠楠、盧海嬌、李靜、李娟芬、郝紅勛,高鹽廢水分質結晶及資源化利用研究進展。化學工業與工程,1卷,2019。
- 丁瑞華,台積電的循環經濟藍圖及資源再生技術,廠務季刊,33卷,頁32~ 43,2019。
留言(0)