摘要
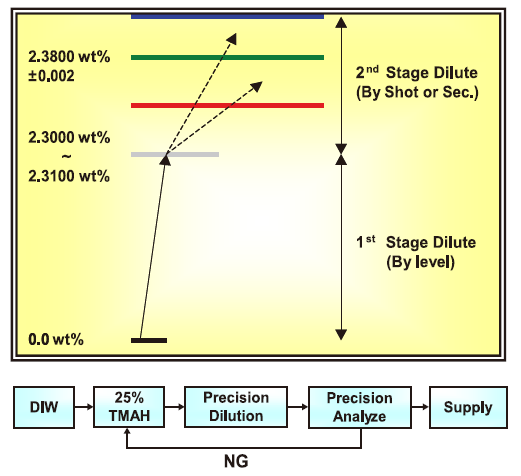
老廠翻新-突破現有桎梏創造綠色及安全工作環境
Keywords / Developer,Electronic Form,Cloud Data
隨著半導體製程不斷進步,工廠持續關注環保與職業安全,致力實現綠色製造和降低現場作業環境風險。F8廠區藉由黃光製程提升後原物料變更的契機,改良顯影劑供應方式,以2.38%TMAH槽車取代25%TMAH 混酸系統供應,停止高風險換酸作業,促成更安全的工作環境。因為TMAH供應系統分析模式的變化進一步降低TMAH排放。並且隨著4G網路普及,積極導入電子表單及iPad作業,並可連結現場氣櫃操作,降低作業風險。電子化表單可提高作業效率,減少紙張使用,完成了綠色製造的目標。
As semiconductor processes continue to advance, factories are actively focusing on environmental protection and occupational safety, striving to achieve green manufacturing and reduce on-site operational environmental risks. In F8 plant area, opportunities arising from changes in raw materials post-enhancement using photolithography processes have led to improvements in the supply of photoresists. The 2.38% TMAH tanker has replaced the 25% TMAH mixed acid system to eliminate high-risk acid exchange operations, thereby fostering a safer work environment. Furthermore, changes in the analysis mode of the TMAH supply system have further reduced TMAH emissions. With the widespread adoption of 4G networks, the active implementation of electronic forms and iPad operations, which can be linked to on-site fume hood operations, helps reduce operational risks. The digitization of forms enhances operational efficiency, reduces paper usage, and achieves the goal of green manufacturing.
1.前言
F8從世大積體電路製造公司建廠至今已運轉逾20年,隨著半導體製程不斷進步工廠對於環保及職安的觀念也隨之上升,如何突破現有作業環境限制達到提升綠色製造並改善現場作業風險,成為廠務面臨的一大課題。本文主要在分享F8如何於不影響工廠生產的前提下,突破現有老舊設備限制,減少廢液排放並提供安全的工作環境。
文章中將本次目標分為兩個主題攻堅: ➀隨著F8黃光製程轉換,顯影劑由KTM-25P轉換為NMD-3 2.38%,廠務藉此機會將擾人的高風險化學品25%TMAH消滅,供應模式由混酸機制改為槽車灌充供應,減少TCM每日更換25%TMAH化學桶作業負擔,並從其中達到減少廢液排放的目標;➁配合廠內4G網路全面升級,廠務作業電子化表單(Facility e-Operation Management, FeOM)上線使用,取代現行紙本表單解決儲存困難及查找資料不易的問題(圖1),紙本表單儲存佔據空間且人員查找資料時需逐頁檢視曠日費時。紙本表單數值需由TGM手動抄寫,填寫錯誤或是超過規格而未察覺。電子表單改善TGM現場抄寫數值錯誤及人為判讀風險。e.g.氣瓶櫃鋼瓶更換表單由紙本留存改為雲端抓取SCADA各項數值並儲存於網站,忠實紀錄更換步驟每一筆數值。將此項技術展開至所有廠務例行性更換作業舉凡化學槽車灌充、廢液抽清、氣體槽車更換等,減少紙本表單的使用並提升查找資訊的便利性。
圖1:經年累月紙本作業表單查找不易
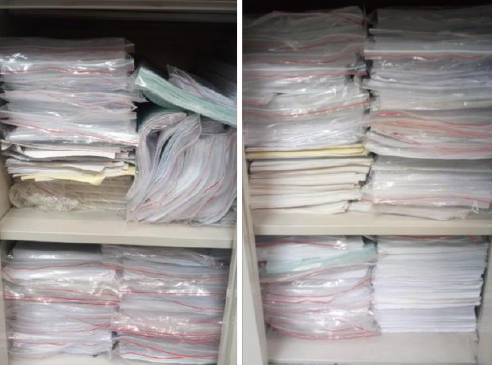
2.文獻探討
2.1 25%TMAH高風險化學品接觸危害案例
根據行政院環保署統計自2007年至今台灣工廠發生多達35起的化學品/氣體洩漏導致人員傷亡及環境危害[1]其中包含兩起TMAH接觸事件造成三名人員死亡,從接觸到死亡僅半小時。截至2021年台積電只剩下F8使用25% TMAH(KTM-25P),TMAH含有OH−基及TMA+基,OH−基使TMAH為鹼性且具腐蝕性可對人體造成化學性灼傷;TMA+基為神經毒素會抑制呼吸肌肉功能,導致呼吸停止、心跳減緩嚴重至腦部缺氧死亡,高濃度TMAH接觸皮膚因強鹼性腐蝕皮膚後加快神經毒的吸收使受災者於15~30分鐘後產生急性中毒[2],甚至呼吸及心跳停止而導致死亡。
2.2 氣體洩漏危害案例及防範
更換鋼瓶程序非常繁瑣且需要大量人為判讀操作的步驟,稍有不慎就會因為判讀誤差導致氣體洩漏。氣體洩漏事故會造成眾多財物損失甚至人員傷亡[3],以1984年印度博帕爾事件為例 : 農藥廠洩漏異氰酸甲酯,瞬間死亡人數達2,259人,大約8,000人於接下來的兩周內喪命,並且有數萬人永久殘疾[4]。氣體洩漏的防範是非常重要的課題。
2.3 電子化表單契機
在資訊發達的時代,使用電子化表單管理現場資訊已經是不可避免的趨勢,不僅可減少儲存紙本資料的空間並且具備快速查找資料的便利性[5]。探討使用電子化表單系統直接雲端抓取廠務監控系統(supervisory control and data acquisition, SCADA)數值,排除人為誤判的可能性[6]。
3.實驗方法
3.1 25%TMAH混酸系統與2.38%TMAH 槽車供應系統架構比較
F8早期顯影劑供應模式為將25%TMAH(KTM-25P)以DI稀釋至2.38%後供應至線上機台。因應黃光製程轉換需求新原物料NMD-3,廠務藉此機會導入NMD-3槽車供應取代高風險25%TMAH混酸系統(圖2)。原25%TMAH混酸系統採逐步漸進式混酸,取樣量測濃度後補償TMAH原液再次取樣量測直至達到需求濃度,平均一次混酸需約2~3次補償(圖3),導致額外的分析廢液排至水課TMAH放流系統,若變更為使用槽車供應僅需灌充前沖洗>3分鐘後取樣送測,可避免額外化學品浪費。
圖2:F8顯影劑供應示意圖

圖3:F8 2.38%TMAH混酸步驟
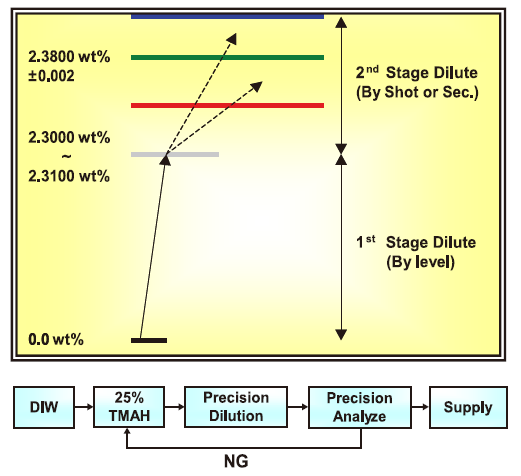
3.2 顯影劑供應系統不同架構中找出減廢契機
依據實驗當時2022/02 F8顯影劑用量為2,200L/Day,依據混酸比單桶220L 25%TMAH可混酸為2,300L 2.38%TMAH供應,平均一天需更換一桶25%TMAH,每日約需完成混酸3筆,然而因為採取階段式混酸,取樣分析而排放廢液約9L/Day。單台NMD-3槽車供應量為6,600L,使用量約3天/車,單次取樣送測排放廢液約為10L,排放量約為3.3L/Day,改為槽車供應可達成減少廢液排放171L/Month的成效(表1)。
顯影劑供應系統比較 | |||
---|---|---|---|
供應模式 | 25%TMAH混酸 | 2.38%TMAH 槽車供應 | ![]() |
單槽/桶可供應量(L) | 2310 | 6600 | |
單次分析排放廢液(L) | 1 | 10 | |
分析作業頻率(次/天) | 9 | 0.33 | |
排放廢液(L/天) | 9 | 3.3 |
3.3 開發智能系統電子表單
既有紙本表單建立至電子化系統後,現場人員依照電子表單說明操作,降低操作風險,電子表單的建置具有五項目標(圖4) :
- 紀錄更換原物料:紀錄原物料Barcode,並建立原物料過期提醒機制;
- 操作人員權限管理:經過認證完成人員方可登入使用電子表單;
- 氣櫃保壓規格管理:表單內建程式管制不同氣體不同測漏規格,避免人為誤判;
- 現場作業表單:針對不同類型氣瓶櫃可對應不同作業表單;
- 各項作業表單管理:廠務電子表單集中於網站管理,可隨時查找資料。
圖4:電子表單建置的5項目標
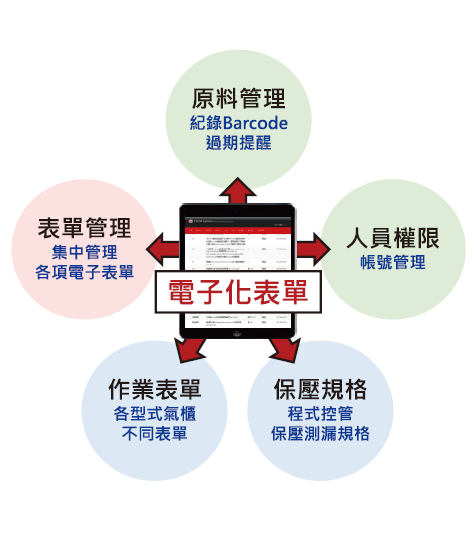
3.4 電子表單雲端抓取數值應用
各項表單電子化後,已完成將現場表單留存於FeOM網站供隨時查詢調閱之成效,但表單中各項數值仍需由現場作業人員自行填寫,無法忠實呈現數值,存在人員抄寫誤差導致程式誤判的風險。後續與FMCS合作開發雲端抓取SCADA數值功能,電子表單直接抓取氣瓶櫃數值避免人員自行填寫的錯誤(圖5)。
圖5:電子表單雲端抓取數值示意圖
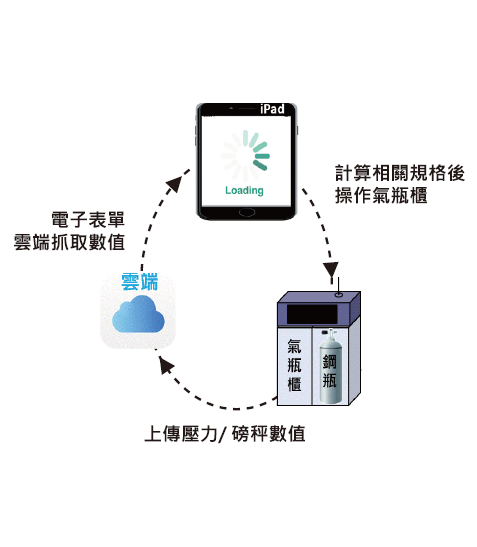
4.結果與分析
4.1 顯影劑由25%TMAH混酸系統改為2.38%TMAH槽車供應達成減廢
實驗證明顯影劑由25%TMAH混酸改為2.38%槽車供應可有效降低每日更換化學桶作業所造成工時損失並改善人員接觸高風險化學品風險。更換化學桶每日需求1名工程師及2名TCM至現場執行Level-1作業時間約0.5小時,每個月耗費約45工時/月。改為使用2.38%TMAH灌充後,作業風險降低為例行性作業,每三天灌充一車,需求1名TCM現場確認槽車灌充資訊約2小時,每個月耗費約20工時/月於槽車接車,每個月可減少25小時工時損耗,每年即可節省300小時(表2)。
工作項目 | 25%TMAH Drum更換 | 2.38%TMAH槽車收車 | |
---|---|---|---|
需求人力(人) | 3 | 1 | ![]() |
耗費工時(小時) | 0.5 | 2 | |
作業頻率(次/天) | 1 | 0.3 | |
每月工時(工時/月) | 45 | 20 |
25%TMAH Drum Dip-tube需委由供應商(多聯科技)運回湖口工廠進行初步清潔後交回廠務使用,每週需額外派車至園區收送25%TMAH Drum空桶及Dip-tube,增加運輸燃料成本及增加碳排放,依據公路車輛燃料成本及動態碳排係數對照表[7]計算,以大貨車平均時速80公里/小時行駛於國道計算往返新竹-湖口,每年清洗的運輸碳排放為565.76公斤,如式⑴,可藉由變更為顯影劑槽車供應改善此情況。
20(km/趟) x 544(碳排放係數, g/km) x 52(週/年) = 565,760g/年 式⑴清運大貨車碳足跡計算
使用2.38%TMAH槽車供應較25%TMAH混酸排放廢液減少約5.7L/Day,發現配合黃光製程原物料轉換改為槽車供應同步觀察到水處理TMAH放流濃度由23ppm→20ppm亦有下降趨勢 ,達到減少廢液排放的成效(圖6)。
圖6:M202~M207 TMAH放流濃度
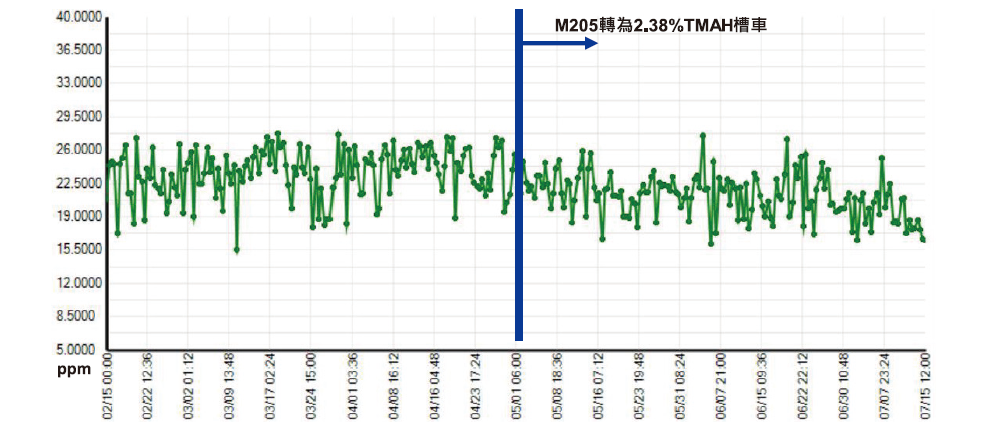
4.2 智能系統電子表單達成氣體洩漏防範成效
將各項作業表單電子化,並建立廠務電子表單管理平台(FeOM)(圖7)彙整各項作業表單:鋼瓶更換、化學桶更換、氣體槽車更換、廢液抽清及小瓶酸借還管理,提供快速及便利查詢功能,提升自動化管理機制。配合廠區iPad應用及4G網路升級,建立FeOM應用程式供現場人員使用(圖8)。
圖7:FeOM網頁介面

圖8:FeOM iPad介面
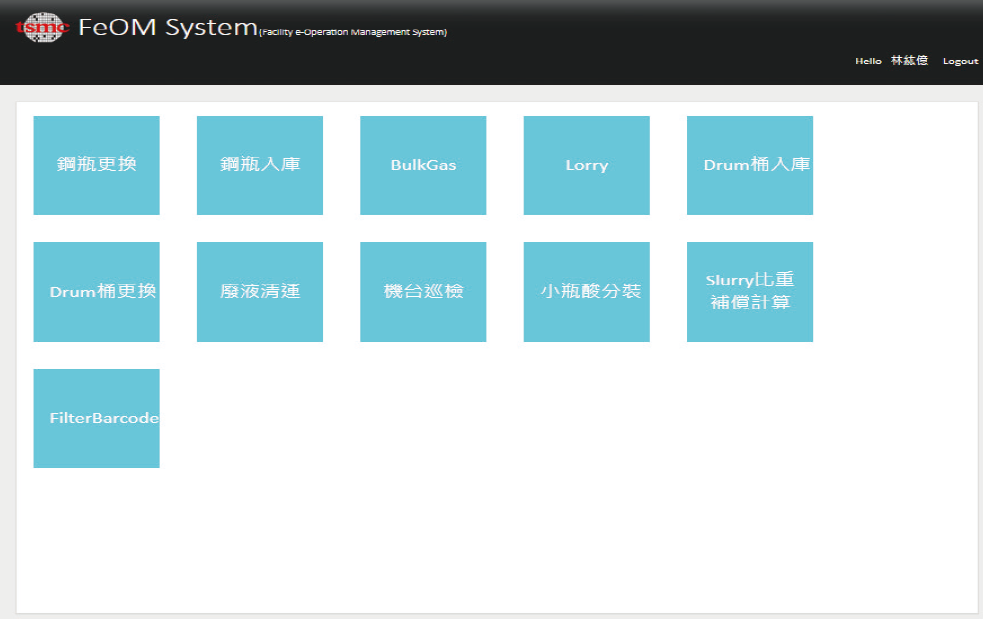
電子化表單上線後,TGM刷取氣瓶櫃條碼後可自動引導出對應氣瓶櫃更換表單,可依據表單指示逐步操作氣瓶櫃(圖9),相關作業壓力規格皆內建於表單,若是輸入壓力不符無法繼續執行表單,取代人腦自行判斷的錯誤機會。
圖9:電子表單應用邏輯說明
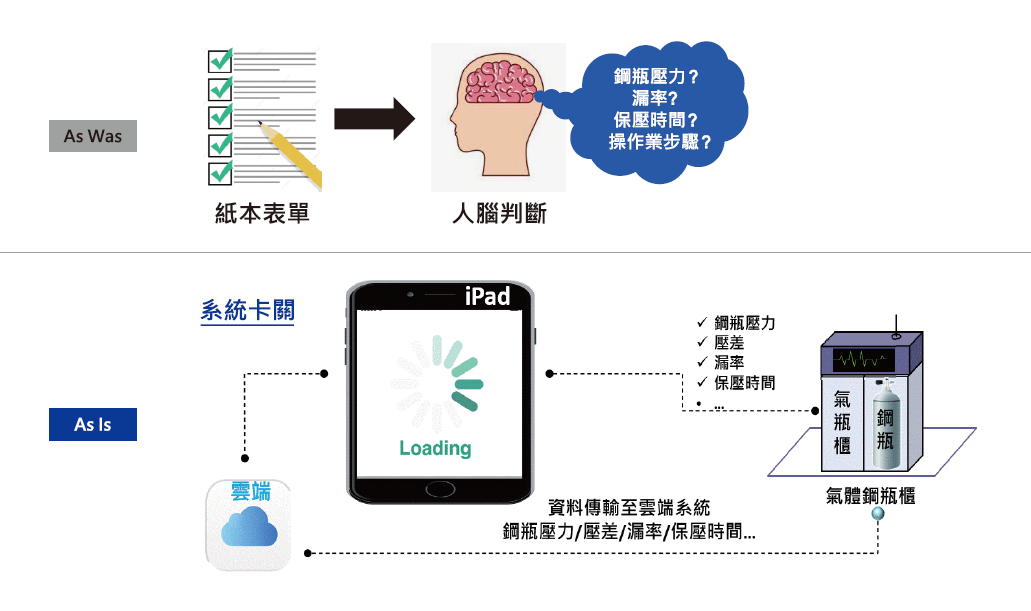
完成電子作業表單後,團隊思考若仍是採用人為抄寫數值的方式總是功虧一簣的感覺,於是團隊利用電子表單系統雲端抓取氣瓶櫃數值,利用FeOM Server向廠務inSQL DB 索取特定Tag-name資料後回傳至作業表單,為達到自動抓取數值的目標,需建置氣瓶櫃各項資訊(圖10)對應氣瓶櫃數值Tag-name,經歷多方測試後自動取得數值後完成,執行表單填寫數值欄位時可直接抓取雲端資料忠實呈現氣瓶櫃數值。
圖10:電子表單實際操作說明
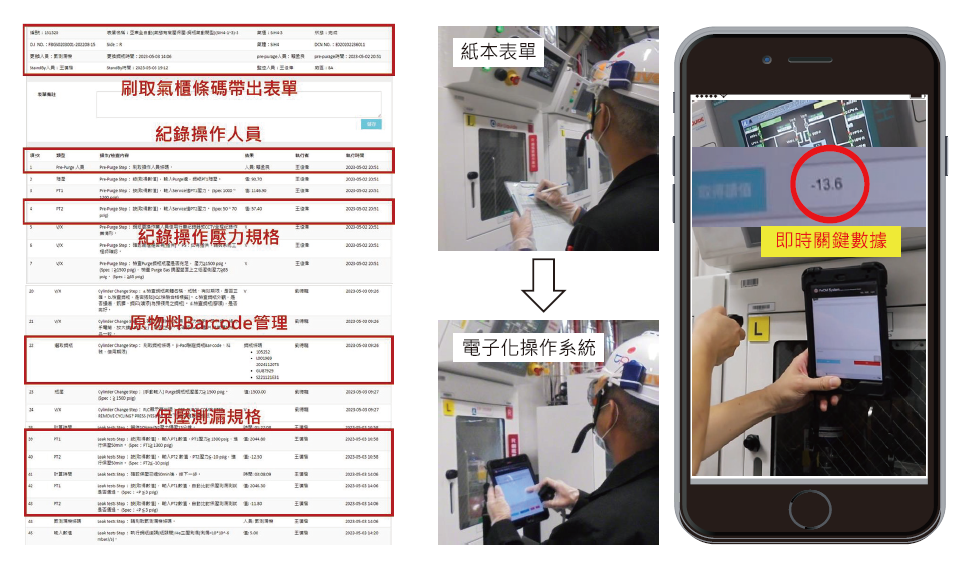
建立電子表單管理平台控管F8 GC原物料更換紀錄取代現場紙本抄表紀錄,將更換資訊直接上傳雲端留存,逐項紀錄各步驟。減少紙本資料留存的空間,且可以有效查詢相關資訊。統計將操作表單電子化後,每年可節省42,850份紙本表單。
5.結論
隨著老廠製程提升及現場通訊設備升級,F8廠務亦積極從中尋找改善契機。藉由黃光製程提升更換原物料的機會以2.38%TMAH 槽車取代現行25%TMAH混酸系統,降低廠內高風險更換作業頻率由1天1次降為0次,每年減少工時損耗300小時,並消除高風險化學品25%TMAH化學品存放於台積電風險(圖11)。因為取消25%TMAH Drum Dip-tube往返運送減少碳排量565公斤/年,最終因為由25%TMAH漸進式混酸分析機制改為槽車逐車取樣減少排放量每月171L,F8 TMAH排放濃度由23ppm降至20ppm,找出減少廢液排放的機會。
圖11:台積廠內無25%TMAH庫存

F8氣化課開發智能系統並將電子表單應用於iPad,供TCGM現場作業使用,電子表單的智慧連結氣櫃、表單及作業規格,藉由廠內氣體洩漏案件統計(圖12)發現可有效降低現場作業風險。並由雲端直接取得氣瓶櫃數值,降低人為抄寫誤差,也成功改善紙本表單儲存及查找不易的問題,並因為紙本表單電子化的原因,每年減少使用48,850份紙本表單。
圖12:廠內氣體洩漏案件數量
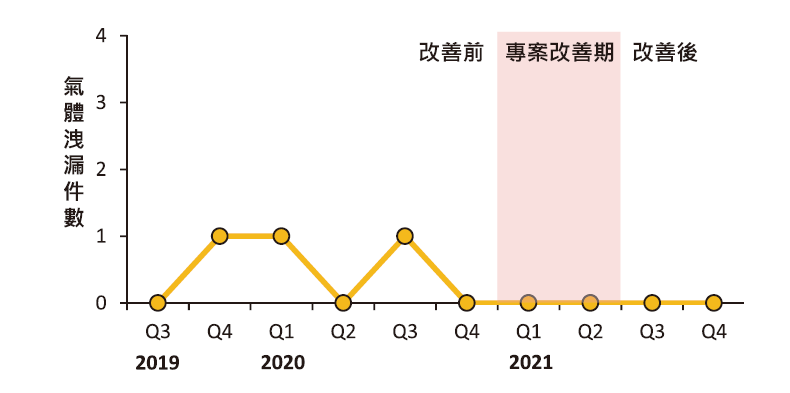
藉由全面翻新改善F8氣化課達成兩項設定目標,消除台積電高風險25%TMAH化學品,開發智能系統電子表單並使用雲端抓取數值,降低現場作業安全風險。
參考文獻
- 行政院環保署毒物及化學物質局網頁。
- 吳政龍,氫氧化四甲基銨暴露致死個案報告與相關文獻回顧,奇美醫院報告,2014。
- 陳光漢,半導體產業之保險與風險淺論,工業安全科技季刊,經濟部工業局,2003。
- 大西洋雜誌,博帕爾事件,2014。
- 曾貴群,可支援多種裝置的企業電子表單程式開發,中原大學碩士班論文,2015。
- 王聖淵,鋼瓶更換電子化管理系統建置與安全危害分析-以半導體廠為例,交通大學碩士班論文,2018。
- 公路車輛燃料成本及動態碳排係數對照表,2018。
留言(0)