摘要
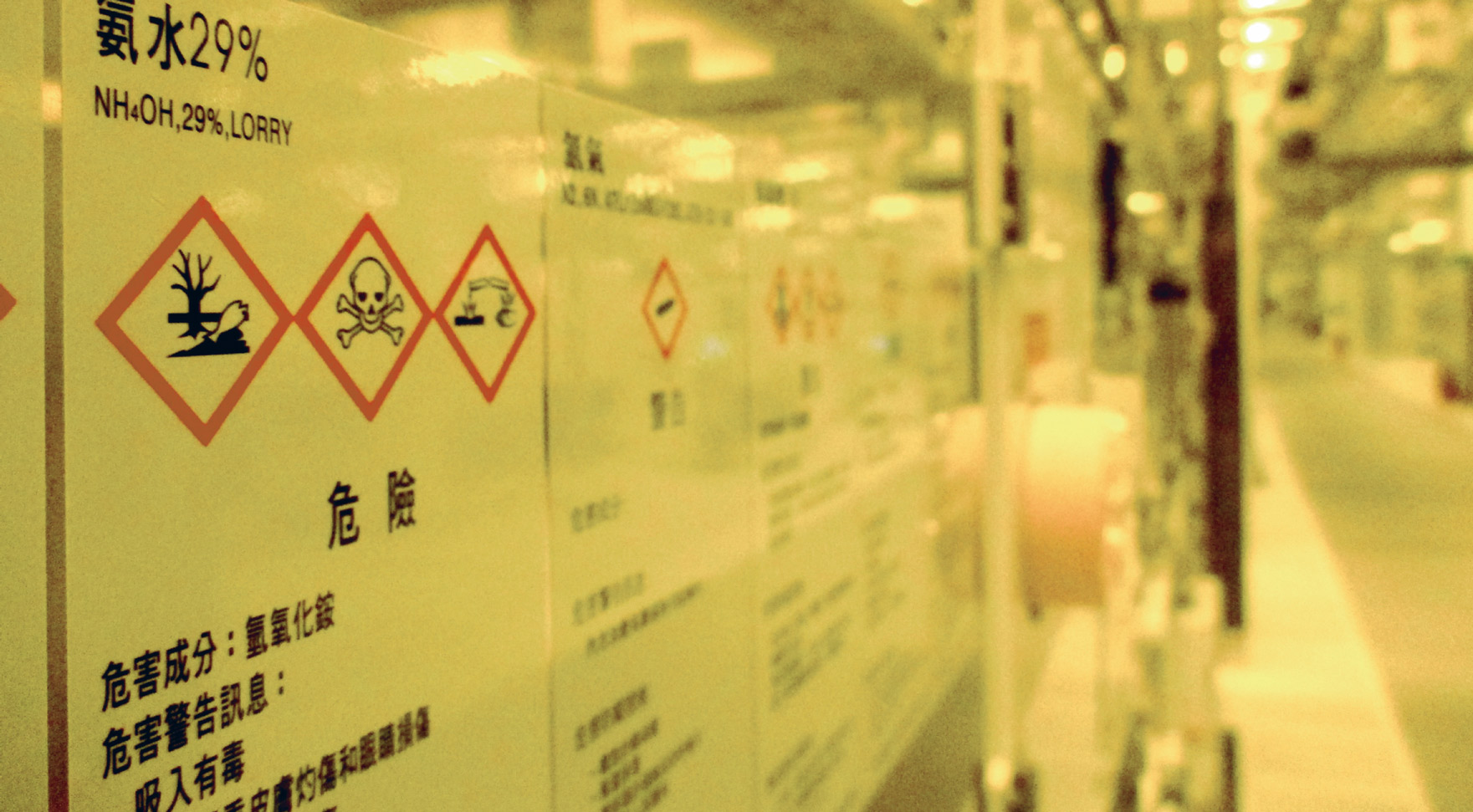
對半導體製造業大廠而言,水資源的高度依賴性與廢水排放需求,為汙染減量與環境改善之標竿,近年政府特別將氨氮廢水視為重點改善目標,各科學園區藉由訂定放流汙水納管限值或規劃除氮廢水系統積極因應,面對日益嚴格之氨氮減量管制,為確保放流水質符合氨氮管制限值,以及達到廠區自我要求改善目標,本文研究磷酸銨鎂沉澱法(Magnesium Ammonium Phosphate, MAP)搭配廠區現有廢水回收系統做聯合操作,應用於氨氮減量改善計畫中證實有效,可提供未來長期系統配置新方法之參考,並於水質異常時,做為緊急處理之應變方案。
前言
隨著近年來環保意識抬頭且水資源時空分配不均之環境下,水汙染成為全球化熱門議題,大量工業廢水排放所造成的河川水質惡化問題日益受到重視。氨氮是水環境中重要的監測汙染源之一,也是導致水體優養化之主要營養鹽,其具有強急毒性易造成水中生物立即性之危害,高濃度之氨氮廢水一旦排入河川湖泊,極易導致水質迅速惡化,或微生物及藻類大量繁殖,消耗水中溶氧使既有生態系統瓦解。因此,氨氮為環境水質檢測下之重要指標之一。
水中之氨氮依據酸鹼值不同,分別以一定比例之銨離子(NH4+)與氨(NH3)之形態存在,此類物質對水中生物危害極大(氨的實驗大鼠口服半致死量:LD50= 50mg/Kg),隨著水循環中硝化菌的分解作用,會逐步分解成毒性較低之亞硝酸根離子(NO2-)與硝酸根離子(NO3-)(LD50=3236mg/Kg),但過程中每莫耳氨將會消耗二倍氧氣,導致水中溶氧不足間接致使生物危害,在筆者先前研究中發現,氨氮為環境水質惡化之主要關鍵因子,許多重要水質指標之變化,如導電度、TOC、BOD、COD和大腸桿菌數的升高,以及溶氧的大幅降低,都與水中氨氮濃度有密切之關係(Chang et al., 2015)。
在半導體事業中,晶圓製造所使用之含氨物質主要為氨水(29%)、光阻清洗液、NMD-W(2.38%)以及二氧化矽蝕刻液、氟化銨等,此類產業因使用大量含氮化學品,其氨氮排放總量約占全國總氨氮排放量之34%之多,竹科之納管紀錄顯示原始氨氮廢水甚至高達1020mg/L,硝酸鹽氮卻大多小於50mg/L,其總氮成分為氨氮貢獻比例最高,在竹科仍高達1100mg/L(李玫,2014),如此可見,科學園區之氨氮汙染著實嚴重,自然硝化作用分解之速率遠不及於氨氮的排放速率,因此環保局已重新修訂放流水標準,將氨氮排放標準納入新增列管。環保署於101年10月12日公布之「科學工業園區汙水下水道系統之放流水標準」將氨氮廢水視為重點改善目標,進行二階段管制政策,第一階段自民國102年7月1日起,既設廠管制限值為75mg/L,如短期內無法達標需進行額外氨氮減量工程改善者,擬定削減計畫且通過後可延後至民國104年1月1日起實施,隨後至民國106年1月1日起,管制限值更緊縮至30mg/L。因此,各半導體大廠之氨氮減量改善勢必成為無可避免之重要課題,必須嚴格且有系統地解決其廢水氨氮過高之現況。
水處理廠區氨氮來源
各廠區放流廢水氨氮現況
現行台積電實施更嚴格的自主管理,其放流水氨氮濃度控管小於50 mg/L,竹、中、南科各廠區積極致力於改善放流氨氮濃度,透過每週氨氮改善會議、製程廢液排放參數修改或是水系統運用改良之方式,正逐步地降低中。研發中心廠區因製程變動快速,廢水水質狀況變化劇烈,相較量產廠而言更難以掌握,部分廠區出現高濃度偶發事件,亦列為重點改善及監控項目。
廢水處理系統之氨氮來源
在半導體廠中,製程廢水以其主要成分與物化性質進行初步分類,藉由各別專管排放至廠區廢水系統進行處理,絕大多數經由多道淨化過程去除水中有害物質後,再行回收二次運用,而剩餘具有較高濃度雜質之濃縮廢水則與二次運用之廢水排放至汙水下水道由科管局接續納管。
2015年於某十二吋晶圓廠做廢水氨氮來源成分現況調查,大部分氨氮來自於氫氟酸製程廢水(HFD),占總氨氮排放量達47%,且因排放水量大,其氨氮總質量貢獻亦遠超過其他廢水處理系統。其次如機台洗滌塔回收水(LSR) 與酸性廢液/酸性有機廢液回收水(AWR/AOR) 之逆滲透濃縮廢水(ROR),也分別佔有20%與16%之放流氨氮濃度貢獻,此三大系統共占氨氮總量之83%,日氨氮排放量為163Kg。
廠區氨氮處理方法
現行之工業廢水氨氮處理應用方式多元,一般分為生物處理、化學加藥處理以及物理處理等三大類,生物處理多半利用硝化菌作用以分解水中氮化合物,使其產生毒性較低之硝酸鹽氮,如硝化脫氮(SBR、MBR)、生化混合、人工濕地以及流體化床等,此法較不適用於環境空間有限以及高濃度氨氮廢水之廠區條件。化學處理如折點加氯、電化學沉降、高級氧化及磷酸銨鎂沉澱法,折點加氯為早期處理氨氮廢水盛行之普遍方法,但龐大的加藥成本造成效益不對等與後續餘氯問題難以控制為其最大缺點,物理處理方法如離子交換、RO濃縮、氣提法、脫氣膜法等,為現行普遍利用之廢水除氮方法(如 表一所示)。
處理技術 |
處理原理 |
優點 |
缺點 |
---|---|---|---|
氣提法 |
在高鹼度環境將NH4+ 轉為NH3,以曝氣方式使氨氣液散 |
技術成熟穩定,程序及設置簡單,運行成本低 |
易生成水垢問題,且需額外於氣提塔後設置氨氣吸收裝置 |
折點加氯法 |
添加氯氣或次氯酸將NH4+反應成N2去除 |
設置成本低廉、操作簡單 |
加藥成本高,且有後續餘氯處理問題易造成環境危害與風險 |
離子交換法 |
以陽離子交換樹脂置換廢水中NH4+ |
系統建置與運轉技術成熟,可搭配現行廠區既有設備 |
成分複雜之含氨再生廢液去化問題難以處理 |
生物處理法 |
建置硝化菌生長環境或生物薄膜,以硝化作用分解水中氮化合物 |
較無產生難以處理之後續廢液問題且方式自然 |
生物加藥成本高,環境條件限制較嚴格,且無法處理高濃度氨氮廢水,反應時間較長 |
脫氣膜法 |
高鹼度環境下利用脫氣膜以硫酸吸收廢水中氨氮形成硫酸銨溶液 |
初設成本與系統管路佔地面積小,操作方便無氨氣逸散問題,處理效率高 |
於極高濃度氨氮廢水中處理效率較佳,無法面對低濃度但大量之氨氮廢水 |
磷酸銨鎂沉澱法 |
添加Mg2+與PO43-,與水中NH4+形成MgNH4PO4結晶沉澱 |
氨氮去除率高,並可同時去除廢水中磷酸根與氟離子,部分產物可再製成材料 |
加藥比例較難控制,並有大量沉澱物去化問題 |
脫氣膜硫酸銨循環法
傳統式氨氮廢水處理普遍利用氣提塔在高鹼度環境下將水中氨元素轉為氨氣(NH3),近年來新式之脫氣膜提供液相與液相之間等相物質交換方式,有別於傳統氣相與液相之間吸收,可大幅降低系統體積與複雜度,降低危害風險,以低成本高效率之優勢成為目前普遍利用之氨氮處理方法。
運用此法之氨氮廢水處理系統主要分為三大類來源,包含機台排放鹼性廢水回收處理系統、鹼性洗滌塔排放廢水處理系統及機台排放氟化銨廢水處理系統,三者共同處理單元包含活性碳過濾塔去除H2O2、脫氣膜(MD)模組進行氨氮交換、硫酸銨循環槽與硫酸銨清運槽,鹼性廢水回收系統另配備逆滲透模組將氨氮濃度進行一次濃縮,以利後續脫氣膜交換效率提升(詳細流程如圖一)。
圖一、廠區現有氨氮處理系統流程示意圖

磷酸銨鎂沉澱法 (Magnesium Ammonium Phosphate, MAP)
若氨氮廢水處理方式僅依靠脫氣膜氨氮系統處理高濃度氨氮廢液,但是面對前述來源調查中HFD、LSR、AWR等含高比例游離氨氮之系統卻無相對應處理能力,且一旦遭遇上游製程端瞬間排放過高濃度氨氮進入此類系統,或該氨氮系統異常失效,將無法確保放流水符合管制標準。因此,利用後續化學沉降方法做進一步把關,或聯合搭配現有系統做風險分配操作,採用加藥方式使氨氮藉由結晶沉澱去除,可提升氨氮濃度控制之穩定度,亦做為去氮操作之備用後援計畫。
磷酸銨鎂沉澱法操作簡單,所生成之產物為磷酸銨鎂,為一種難溶於水的白色結晶(Ksp=2.51×10-13),通常以六水合物形態存在,俗稱鳥糞石,可回收做為農業用緩釋肥、飼料添加物、化學試劑、阻火劑與水泥黏接劑等多元用途,故以磷酸銨鎂沉澱法做為氨氮去除工法時,可同時達到資源回收再利用之目的。MAP法中氨氮、鎂離子與不同型態磷酸根之化學反應方程式如下式(1)~(3)所示,若水體中含有亞磷酸根或次磷酸根,反應則會額外釋出氫離子使水體pH降低。
NH4+(eq) + Mg2+(eq) + PO43-(eq) + 6H2O ↹ MgNH4PO4ּ • 6H2O(s) ......................... 式(1)
NH4+(eq) + Mg2+(eq) + HPO43-(eq) + 6H2O ↹ MgNH4PO4ּ • 6H2O(s) + H+ ................ 式(2)
NH4+(eq) + Mg2+(eq) + H2PO43-(eq) + 6H2O ↹ MgNH4PO4ּ • 6H2O(s) + 2H+ ................ 式(3)
眾多文獻顯示MAP在工業廢水當中為一確實可行之除氮策略,面對高濃度與低濃度之氨氮廢水皆有顯著成效,詳細研究成果比較列於 表二,在合理的加藥量下反應於偏鹼環境10~50分鐘,即有超過八成之氨氮去除率。在現行台積十二吋廠運行條件下,鄒安華(2007)之研究相對符合廠區現況,在pH10環境中加以與氨氮濃度相等之磷酸與1.4倍之鎂離子,反應僅需五分鐘即可達成91.5%之氨氮去除率,適宜作為後續實驗之參考依據。
研究主題 |
pH |
[NH4+] :n[PO43-] :n[Mg2+] |
反應時間 |
廢水氨氮濃度 (mg/L) |
氨氮去除率 (%) |
參考文獻 |
---|---|---|---|---|---|---|
以磷酸銨鎂法搭配中央合成及反應曲面法實驗設計探討科學園區聯合污水廠廢水中氨氮去除之研究 |
10 |
1.0 : 1.75 : 1.67 |
30 |
87 |
81.9 |
林后志(2014) |
MAP沉澱法處理高濃度氨氮廢水工藝應用 |
9.5 |
1.0 : 1.3 : 1.4 |
40 |
2275 |
94.1 |
吳珊蔚(2013) |
磷酸銨鎂沉澱法處理高濃度氨氮廢水實驗研究 |
8.5-10.0 |
1.0 : (1.2-1.4) : 1.2 |
10 |
360 |
96.0 |
劉俊(2013) |
化學沉澱法處理高濃度氨氮廢水試驗研究 |
9.0 |
1.0 : 0.9 : 1.2 |
50 |
2100 |
84.9 |
吳立(2009) |
化學沉澱法從氨氮廢水中回收磷酸銨鎂 |
10 |
1.0 : 1.0 : 1.4 |
5 |
200 |
91.5 |
鄒安華(2007) |
磷酸銨鎂沉澱法去除NH3-N的影響因素及應用研究 |
8.5 |
1.0 : 1.2 : 1.4 |
10 |
631 |
81.0 |
晏波(2005) |
磷酸銨鎂沉澱法除氮效益分析
MAP試驗於某十二吋廠區中進行模擬,面對含有高濃度氨氮之HFD廢水系統,勢必首要針對其進行改善,實驗計畫於HFD氯化鈣加藥沉降水中氟離子後,再進行MAP加藥二次處理以去除大量水中氨氮,實驗水樣採集於HFD廢水處理系統汙泥斜板沉降槽上澄液(氨氮濃度90~140mg/L),做降尺度瓶杯試驗。
根據文獻對MAP氨氮去除率影響因子研究結果顯示,影響磷酸銨鎂沉澱效率之因素主要為反應環境酸鹼值、加藥比例、反應時間與水中其他離子干擾等,故實驗分別針對上述各因素進行單獨研究,找出最佳結果。實驗於250ml燒杯中進行,水樣體積皆為150ml,磷酸根離子由86%磷酸提供,並以10%氯化鎂溶液做為鎂離子添加來源,pH分別以NaOH及HCl溶液做控制,反應終點氨氮濃度檢測採HACH氨氮試劑(26069-45)以分光光度計法測定。
反應最佳pH值試驗
欲了解MAP反應在不同pH環境下,針對HFD系統斜板汙泥沉降槽上澄液廢水之除氮效率,於pH8~10.5區間內進行氨氮去除率實驗分析,另為釐清廢水中其他複雜離子干擾程度,特以超純水配製氯化銨溶液進行對照實驗,觀察相同pH條件下差異性,初始藥品添加比例以相對於氨氮各1.68倍濃度之磷酸與氯化鎂做加藥控制。
實驗結果顯示HFD廢水與氯化銨溶液同於pH10.0下擁有最佳氨氮去除率(如 圖二所示),但HFD廢水成效較氯化銨溶液明顯偏低。鄒安華(2007)以X射線針對磷酸銨鎂沉澱物分析結果顯示,當pH值8.0-10.0時,沉澱物特徵波峰與MAP標準品波峰位置相符,隨pH上升波峰強度逐漸增強;當pH 11時,雖然沉澱物仍以磷酸銨鎂為主,但已有Mg3PO4生成,導致PO43-與Mg2+被大量消耗造成氨氮去除率下降;在pH=12時,MAP特徵波峰將消失,沉澱物以 Mg(OH)2為主,故氨氮去除率不佳。本研究目的係為以磷酸銨鎂沉澱法去除HFD系統出口之氨氮,故取最佳結果pH10.0作為後續實驗酸鹼值設定。
圖二、HFD 處理廢水與氯化銨溶液於各pH 條件下之氨氮去除率
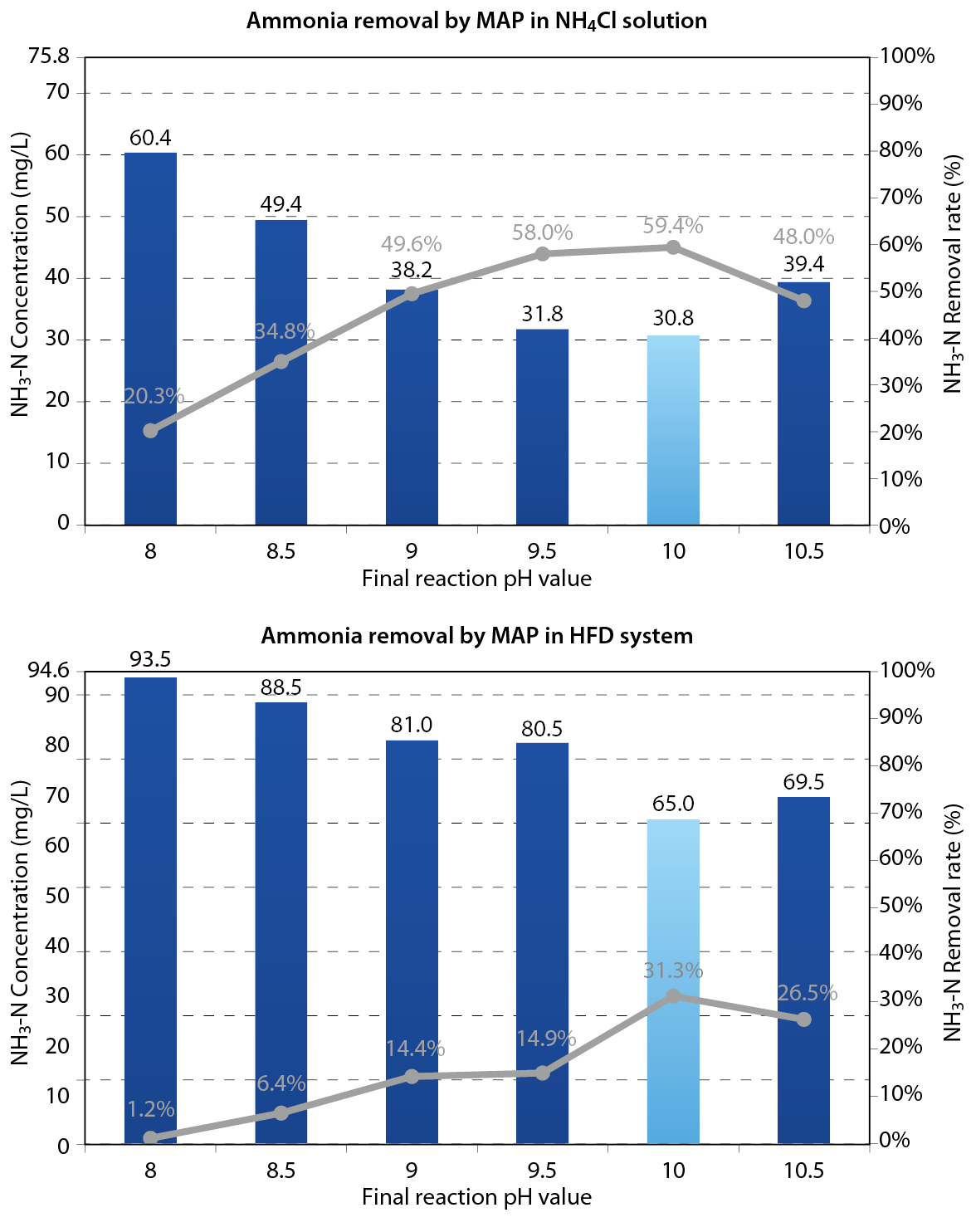
該HFD系統廢水因前段過量添加氯化鈣,水體中含高濃度鈣離子,廢水中高量鈣離子易與磷酸反應,消耗MAP所需之磷酸使氨氮去除率大幅降低,此為實驗結果中HFD廢水氨氮去除率較乾淨氯化銨溶液低之原因。過程中添加磷酸於pH>6.0後即呈現白濁狀態,係因水中鈣離子與磷酸根反應生成磷酸鈣及氟磷酸鈣沉澱,此現象伴隨F-同時沉澱使水中氟離子濃度大幅削減。
磷酸加藥定量分析
以pH10.0之環境做磷酸根定量試驗,找出足量之磷酸根加藥量,磷酸根定量試驗發現將原本磷酸根濃度由1667ppm提升至2779ppm可將氨氮去除率由28.1%顯著提升至54.5% 圖三,隨後實驗以此濃度比例做磷酸根修正加藥量。
圖三、磷酸根加藥濃度定量分析
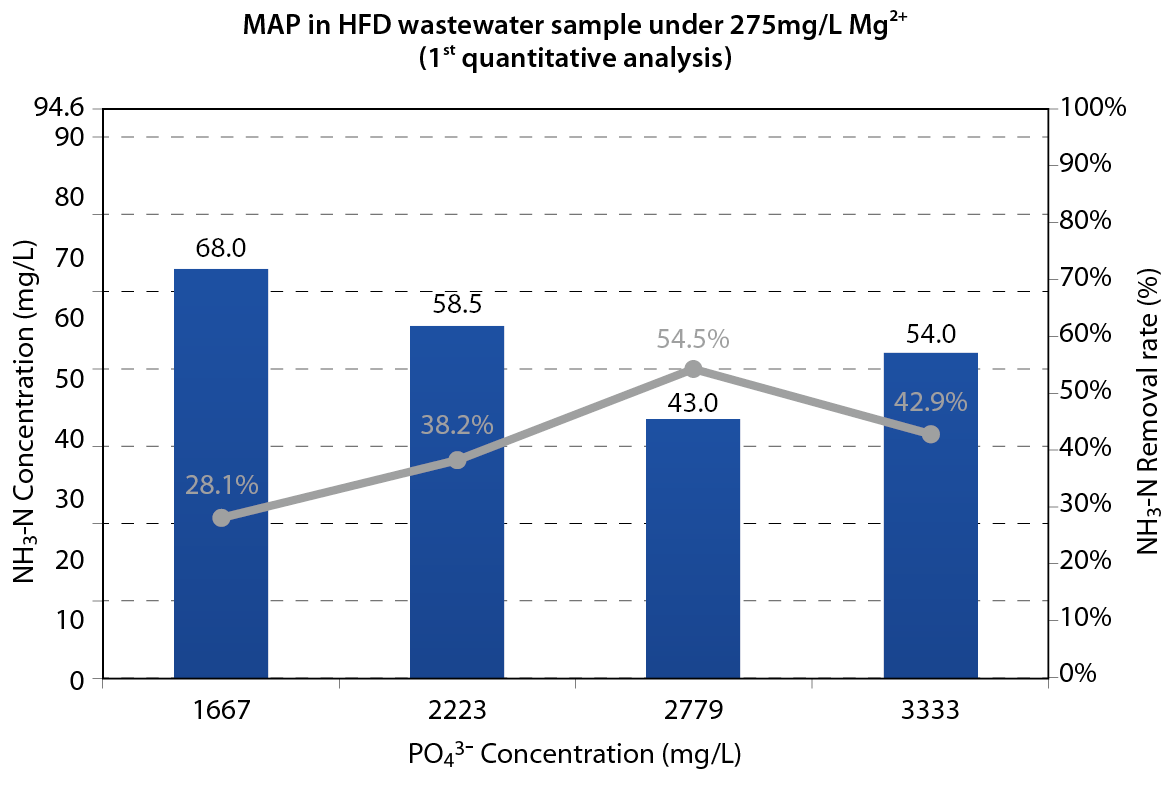
氯化鎂定量分析
以磷酸定量分析結果之氨氮與磷酸根比例,於pH10下進行含有115ppm氨氮之HFD廢水鎂離子加藥量定量分析,以固定體積之86%磷酸做加藥,進行反應時間2小時之瓶杯測試,其中分別以不同體積之10%氯化鎂溶液作為鎂離子添加來源,測試不同鎂濃度下之氨氮去除率,實驗結果如 圖四所示,當[Mg2+]>386ppm時氨氮去除效率開始有顯著上升;[Mg2+]約510ppm時具70%去除率;[Mg2+]約600ppm具80%去除率;[Mg2+]約770ppm具90%去除率。
圖四、鎂離子加藥濃度定量分析
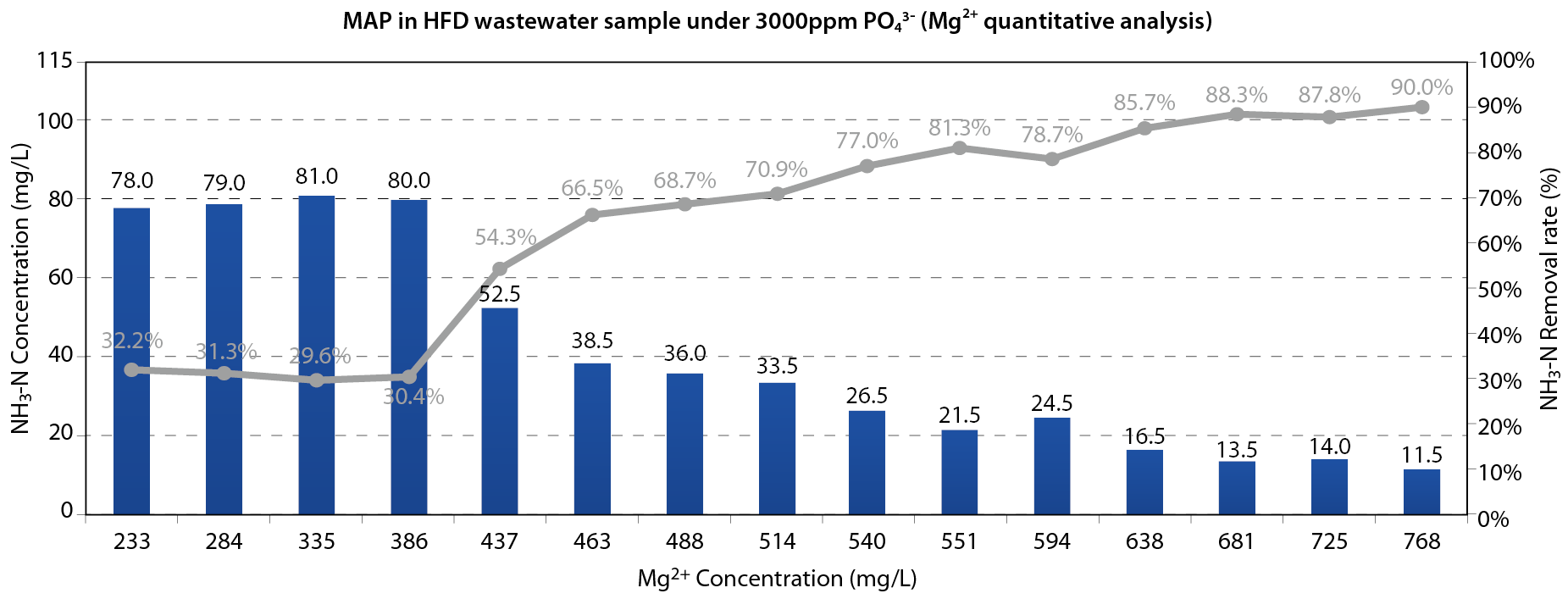
隨氯化鎂濃度增加,氨氮去除率隨之顯著提升,於此濃度平衡下,另進行第二次磷酸定量分析,觀察增高或降低此階段磷酸濃度是否仍顯著影響氨氮去除率。以鎂定量分析85%去除率加藥比率[NH4+]:[Mg2+]=115:638重新於氨氮濃度為135ppm之新HFD水樣做二次磷酸根定量試驗,結果顯示於相同鎂離子濃度下,改變磷酸根濃度對氨氮去除率影響甚低。磷酸根濃度2390~3500ppm內氨氮去除率改變幅度低於±5%。
反應時間分析
為了解MAP法於HFD處理廢水和氯化銨溶液下之反應速率,於預估氨氮去除率60~90%之加藥量區間下進行反應時間分析,以固定之磷酸加藥量,做不同體積之氯化鎂加藥,分別進行109ppm氨氮濃度之HFD斜板上澄液,與配製相似氨氮濃度106ppm之氯化銨溶液分別進行反應速率實驗,取樣每十分鐘之各別氨氮讀值,直至60分鐘視為反應終點。 圖五為實驗結果,澄清氯化銨溶液在高加藥量時反應第一時間即可將水中氨氮近乎完全去除,沉澱物迅速沉降且水質清澈﹔於低加藥量時需較長時間達成反應平衡,但水質依舊澄清僅沉澱物變少。HFD斜板上澄液廢水需歷時20至30分鐘才能達成反應終點,反應平衡時間與加藥量多寡相關性不明顯,且過程中亦與鈣離子反應白色懸浮物,反應初始溶液成白濁狀態,沉降效果不彰,約於十分鐘後上澄液開始逐漸分層沉澱。
圖五、不同氨氮去除率下之MAP 反應時間分析
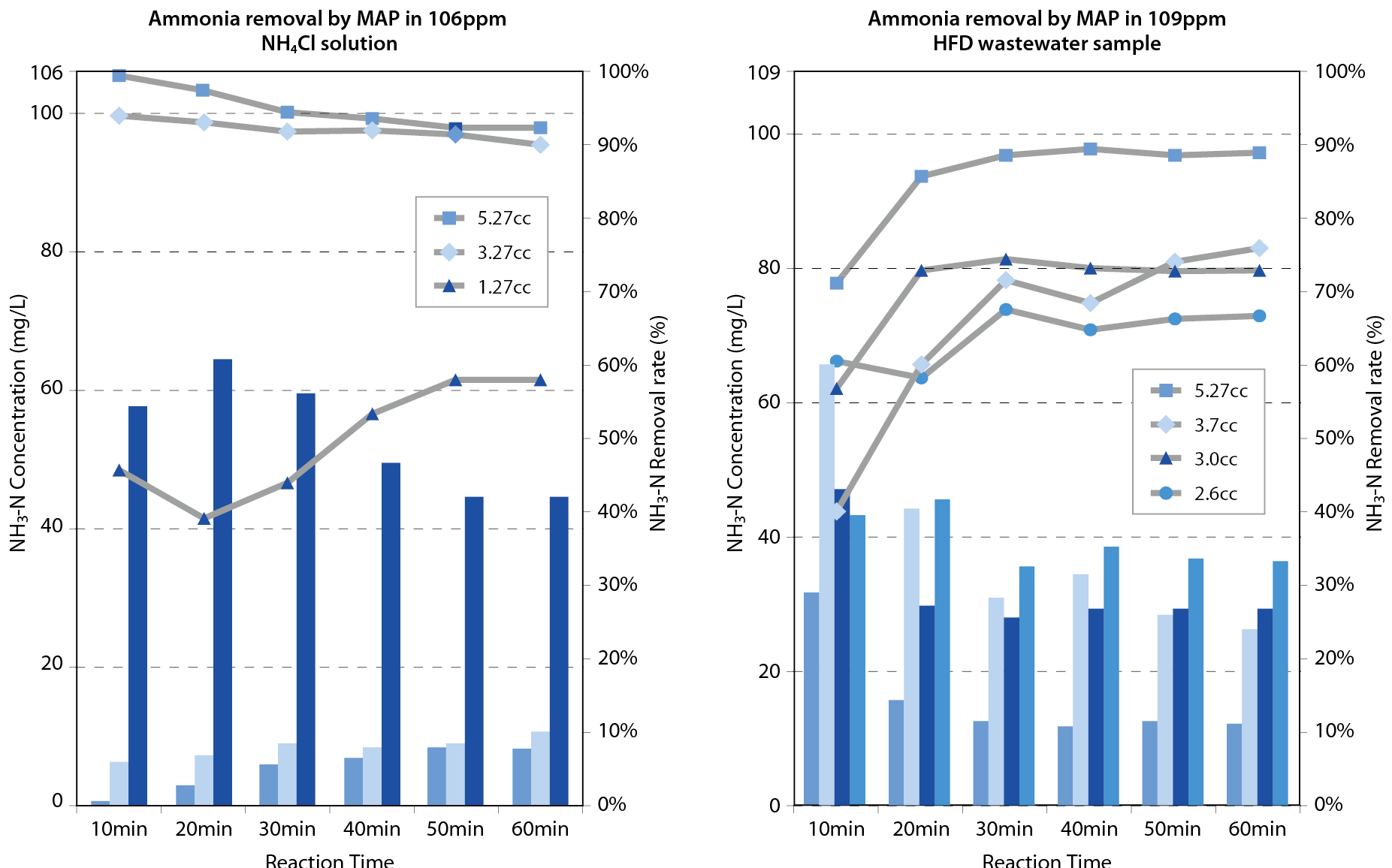
反應曲面分析
以不同H3PO4與MgCl2加藥量組合對HFD斜板上澄液C-240進行氨氮濃度127ppm水樣之氨氮去除率反應曲面圖建構,結果參照 圖六。相同磷酸加藥量下,氯化鎂加藥量越多氨氮去除效率越高,但同氯化鎂加藥量下存在過量與低量之磷酸皆會降低氨氮去除效率,顯示鎂濃度為氨氮去除效率之主要決定因素,而磷酸濃度為次要因素。此實驗中平均氨氮去除率為54.7%,中位數43.3%,標準差為23.4%,雖變動幅度大,但氨氮去除率與加藥量具線性關係,較易利用加藥量掌握和控制。
圖六、不同加藥比例下之氨氮去除效率
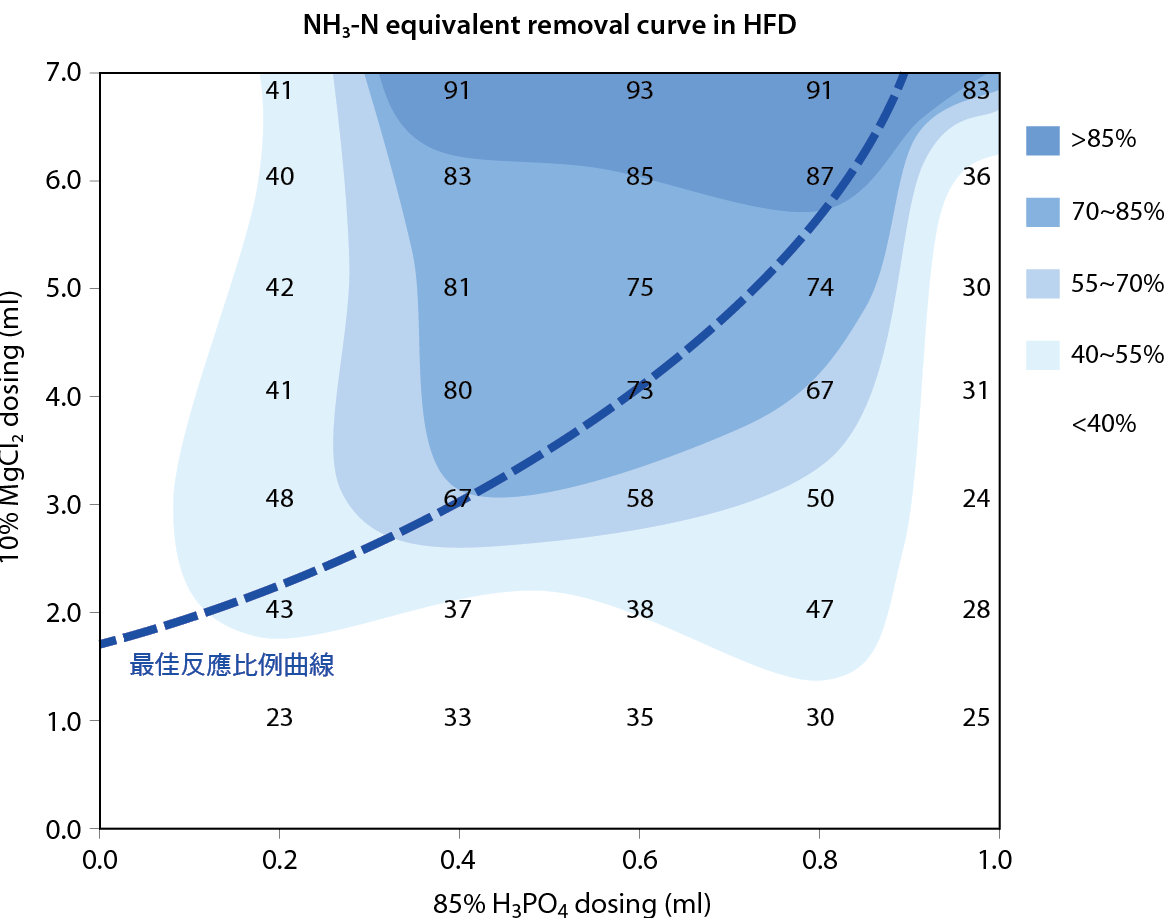
在MAP磷酸加藥過程中,廢水中另一重要污染源氟離子,會伴隨磷酸根與水中游離鈣率先沉澱,於此實驗下亦同時量測氟離子在MAP加藥過程中之削減率。在水樣存在8.7ppm氟離子濃度下,相對於氨氮去除率結果,氟離子去除效率較看不出與MAP加藥量多寡之關係,雖其削減率看不出反應傾向,但皆介於30~80%之間,對於HFD廢水氟離子濃度的改善亦具有相當之成效,實驗氟離子削減率平均62%、中位數60%、標準差13.9%,變動範圍皆較氨氮去除效率為小,可視為MAP加藥後之連帶附加效果。
RO二段濃縮搭配磷酸銨鎂沉澱法之新式聯合除氮系統
依據MAP實驗結果,於該廠區條件下,一新式之氨氮處理計畫進行中,運用聯合系統操作模式將可大幅改善HFD&LSR中氨氮濃度過高、水量過大無法處理等諸多問題,創新將其導入既有之MD氨氮系統,進而融合MAP法做最後之除氮聯合操作設計,預期將顯著改善氨氮放流濃度。
此一聯合系統將含有高濃度氨氮HFD製程廢水導入LSR處理系統,經由RO一次濃縮後將濃縮水導入AOR系統做RO二次濃縮,所得廢水則進一步導入TBE/AEX脫氣膜氨氮系統中做除氮處理。此法可囊括前述三大高氨氮廢水系統(HFD、LSR、AOR)進行濃縮,大幅降低氨氮廢水處理量,並提高氨氮濃度增進脫氣膜處理效率。隨後在系統末端設置MAP加藥系統(部分廠區可利用HFD系統替代),作氨氮處理後廢水以及RO二段過剩濃縮水之最終除氮措施,於此同時可充分二次運用廠內回收之廢磷酸做MAP加藥來源。
圖七為此聯合除氮系統流程圖,RO二次濃縮導入氨氮系統段(淺藍段)於某A廠完成實際系統測試,其運行水量與實際檢測出之氨氮濃度亦標示於圖內,第一階段已將51.5ppm之氨氮放流濃度成功降至38ppm,同時額外增加900CMD之次級用水量,第二階段MAP系統(深藍段)評估中,預計接收第一階段MD處理系統之產水做再次處理,並收納超過MD系統負載之過剩水量(方法二分流),總計合併氨氮濃度138ppm,日處理量約370噸之產水。
圖七、新式RO 二次濃縮聯合MAP 法除氮系統流程圖
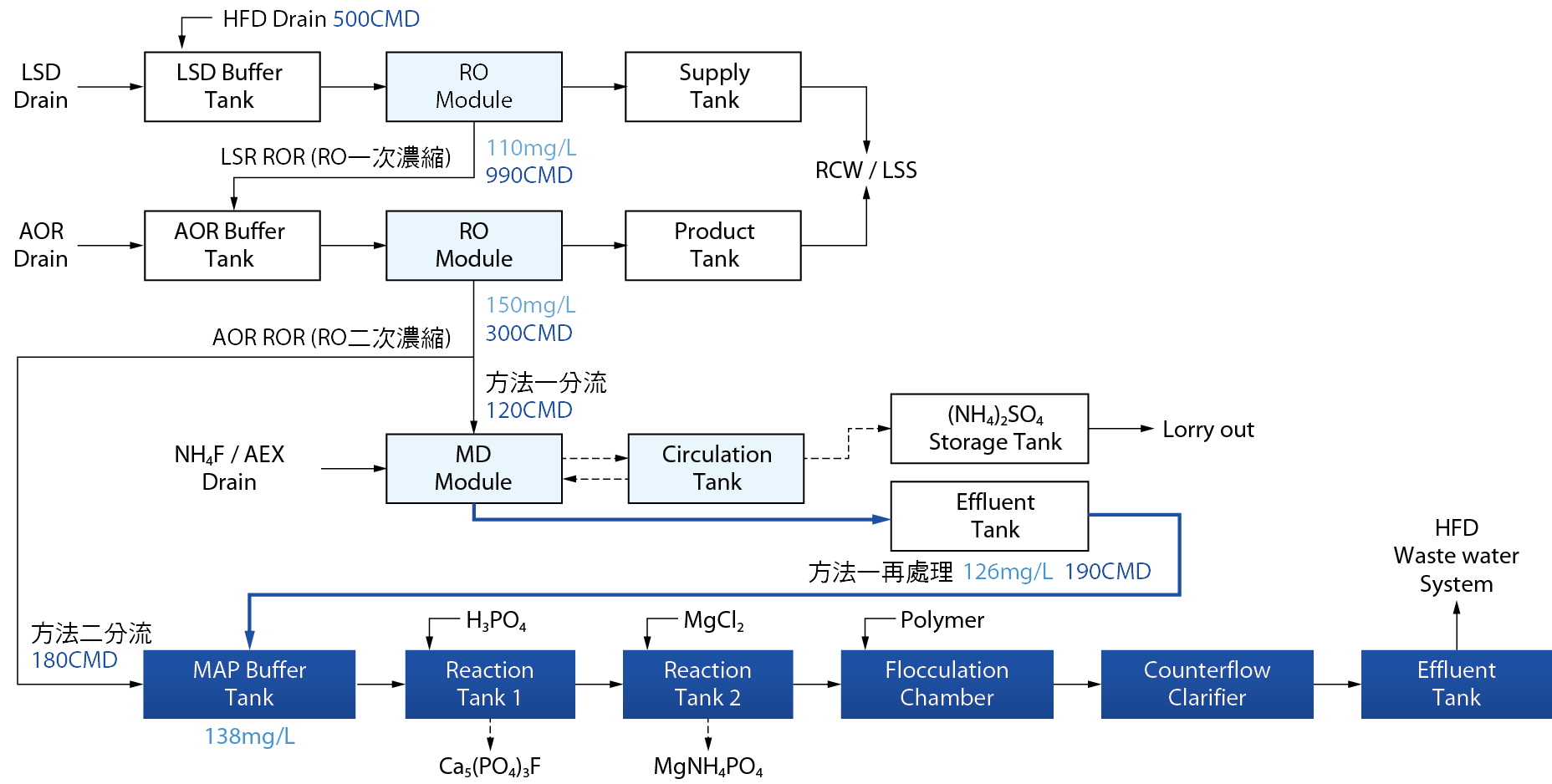
利用MAP實驗數據結果模擬二階段MAP系統運轉,設計60%至90%氨氮去除效率加藥量,做系統運轉評估,數據列於 表三。推估利用二階段MAP系統於90%去除率下,廠A放流廢水氨氮濃度可大幅減少至28ppm,廠B因扣掉AWR貢獻並新增CWRR更可減少至21.5ppm,成功達標民國106年後環保署公定氨氮納管限值,將氨氮去除率降低至60%時也各有31.8 & 25.3ppm之氨氮減量成效,遠低於目前現行狀態。表中淺藍段係估計全時間不間斷加藥量下之加藥成本,若改由回傳放流氨氮數值來作MAP系統端之SP加藥PID控制,應可大幅降低所需MAP加藥量,並可提升操作穩定度與放流氨氮穩定度。更甚者,本加藥量係以HFD系統汙泥斜板上澄液水體實驗結果做推估,實際此聯合系統因尚未進入HFD做氯化鈣加藥處理,水體鈣離子濃度偏低,可大幅降低實際磷酸與氯化鎂消耗量。此外,廠內具備廢磷酸收集槽,日進流約1500公升製程濃廢磷酸,足夠充當MAP磷酸加藥來源,達成資源回收再運用之環保方針。總和而言,MAP實際運行成本落於不間斷加藥推估值之三至四成之間(如 表三末)。
項目 |
數據 |
|||
---|---|---|---|---|
原始MAP進流氨氮濃度(mg/L) |
138 |
|||
目標反應時間(min) |
20 |
|||
目標去除率 |
90% |
80% |
70% |
60% |
目標MAP產水氨氮濃度(mg/L) |
13.8 |
27.6 |
41.4 |
55.2 |
NH4+ : PO43- : Mg2+濃度比 |
135:2390:902 |
135:2390:642 |
135:2390:596 |
135:2390:528 |
NH4+ : H3PO4 : MgCl2質量比 |
1 : 18.3 : 26.2 |
1 : 18.3 : 18.8 |
1: 18.3 : 17.3 |
1 : 18.3 : 15.3 |
NH4+ : PO43- : Mg2+莫爾數比 |
1 : 3.4 : 5.0 |
1 : 3.4 : 3.6 |
1 : 3.4 : 3.3 |
1 : 3.4 : 2.9 |
HFD System其他氨氮來源貢獻濃度(mg/L) |
51.7 |
|||
預估HFD System產水氨氮濃度(mg/L) |
55.5 |
59.5 |
63.4 |
67.3 |
預估廠A放流氨氮濃度(mg/L) |
28.0 |
29.2 |
30.5 |
31.8 |
預估廠B放流氨氮濃度(mg/L) |
21.5 |
22.7 |
24.0 |
25.3 |
預估85%磷酸日加藥量(CMD) |
1.06 |
1.06 |
1.06 |
1.06 |
廢磷酸GC日增量(CMD) |
1.2 ~ 1.5 |
|||
預估10%氯化鎂日加藥量(CMD) |
13.1 |
9.3 |
8.6 |
7.6 |
純磷酸不間斷加藥日成本(NTD) |
$119,855 |
$119,855 |
$119,855 |
$119,855 |
氯化鎂不間斷加藥日成本(NTD) |
$95,435 |
$67,885 |
$63,023 |
$55,821 |
廢磷酸運用&PID加藥控制總日成本推估(NTD) |
$48,676 |
$40,234 |
$39,871 |
$39,349 |
結論
因應日漸備受重視之氨氮廢水問題,MAP磷酸銨鎂沉澱法在廠區實驗中,證實為一確實有效之除氮策略,搭配設計之RO二次濃縮聯合系統操作可同時濃縮HFD、LSR與AOR前三大高氨氮廢水,集中納管原有系統中無法處理之氨氮,將其正確導入脫氣膜氨氮系統進行除氮,現行某廠區實驗證實此法運作時合乎RO回收系統負載量,在適當之流量調整下無不良情形發生或系統傷害,且可順利濃縮氨氮進入MD膜中處理,已穩定運轉中。於聯合除氮系統第二階段MAP法評估中,降尺度實驗證實在適當且合理之加藥量下,反應20分鐘內即可得有效率之氨氮去除效果,並伴隨著氟離子濃度降低之副改善作用,成效顯著,若聯合廠區廢磷酸貯存系統做MAP磷酸加藥供應來源,更可達到資源回收再利用之環保功效,搭配控制放流氨氮臨界濃度控制值(SP)做加藥控制,更將節省可觀加藥成本。
本RO二段濃縮聯合MAP除氮系統,可確實控管半導體製程所產生之大量高濃度氨氮廢水,大幅增加現行廠區氨氮處理能力,以及遇到瞬間濃度鋒值時之危機應變能力,其改善成果值得為現行廠區氨氮減量改善之參考依據。
參考文獻
- Chang. F.J., Tsai, Y.H., Chen, P.A., Alexandra C., Georges V., 2015. Modeling water quality in an urban river using hydrological factors – Data driven approaches. Journal of Environmental Management 151, 87-96.
- 林后志、林舜宏、陳睿斌、黃俊欽、呂理安,2014,以磷酸銨鎂法搭配中央合成及反應曲面法實驗設計探討科學園區聯合污水廠廢水中氨氮去除之研究,中華民國環境工程學會2014廢水處理技術研討會。
- 李玫、傅正貴、王俊元,2014,創新氨氮廢水資源化,台積電第十四期新工季刊,13-19。
- 吳珊蔚、陳國輝、廖英儒等,2013,MAP沉澱法處理高濃度氨氮廢水工藝應用,中國化工貿易,第七期。
- 劉俊、王雷、李雪鬆等,2013,磷酸銨鎂沉澱法處理高濃度氨氮廢水實驗研究,油氣田環境保護,Vol.23,No.6。
- 張琴、楊彬彬、潘水秀等,2010,MAP法處理高濃度氨氮廢水技術研究發展,四川環境,Vol.29,No.5。
- 吳立,孫立平,李志偉等,2009,化學沉澱法處理高濃度氨氮廢水的試驗研究,四川環境,Vol.28,No.1。
- 鄒安華,孫體昌,宋存義等,2007,化學沉澱法從氨氮廢水中回收磷酸銨鎂,北京科技大學學報,Vol.29,No.6。
- 晏波,胡成生,朱凡等,2005,磷酸銨鎂沉澱法去除NH3-N的影響因素及應用研究,環境化學,Vol.24,No.6。
留言(0)