摘要
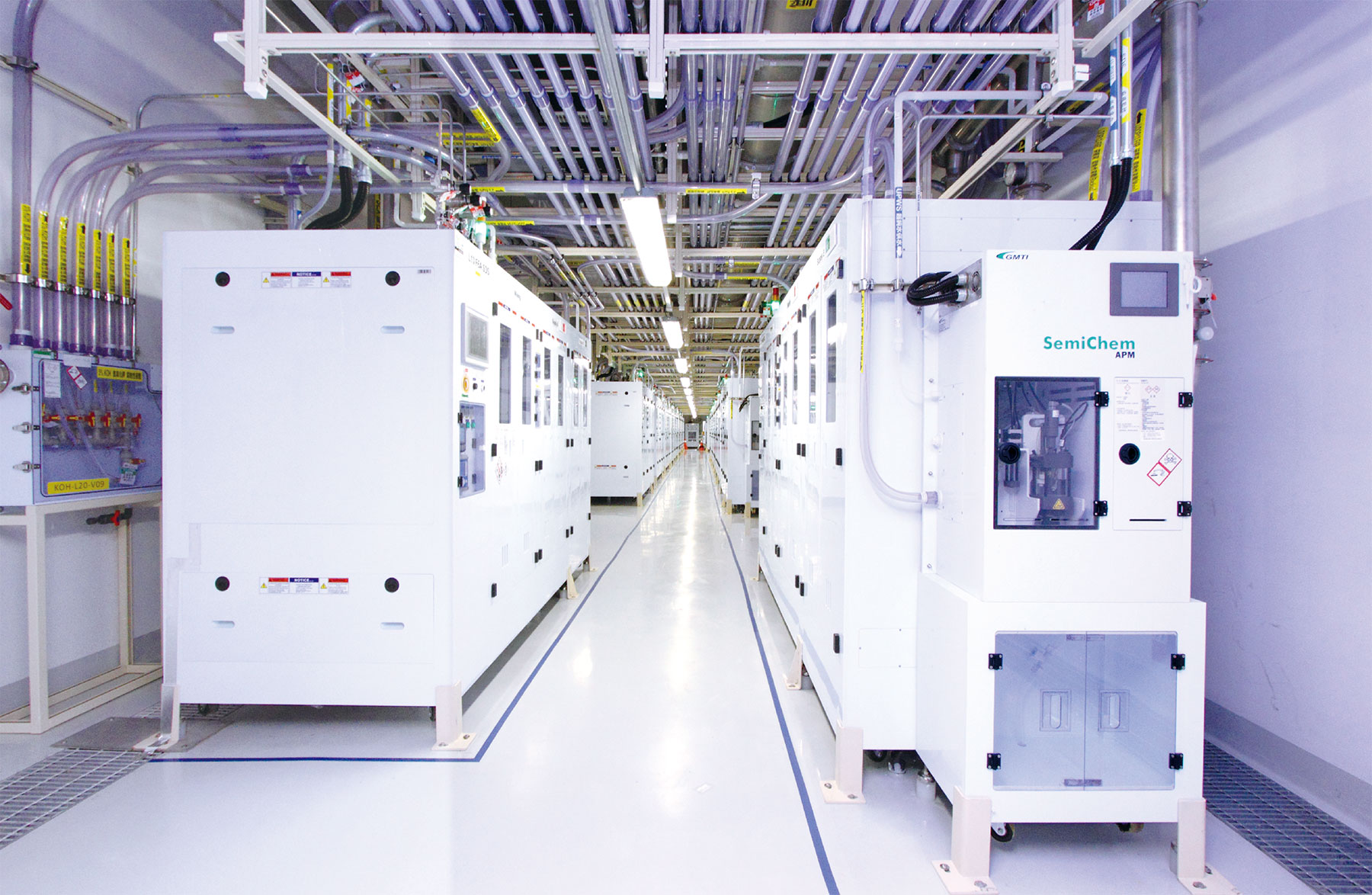
本文主要分析雙氧水滴定儀使用上之問題,針對六向閥和螺桿組進行新概念設計、硬體改造,以及軟體計算進行驗證和優化,包含將滴定儀用作定量的六向閥移除,改由閥件之滯吸力進行定量,並將定量管拉出毛細管,強化管內的附著力,避免閥件開關的瞬間壓力造成回抽,解決因為六向閥存在的所有宿疾問題; 原廠O型環容易因為螺桿推進而擠壓變形,遂利用O型環的體積,於其外定模硬度高、摩擦係數低之「高分子盔甲」,螺桿的取液口則修改成外徑突出而內徑不變的圓柱頭,並在前端做出微縮防止脫落;軟體則優化滴定過程、修正計算功能,設定假想預滴定量,將研磨液定量減量後,因而被放大的修正係數恢復正常,成功解決假性誤差的滴定穩定度變差問題。
前言
即時性的雙氧水(H2O2)滴定儀 (ATRs)於原廠設計,是利用六向閥(6-way valve) 圖1將含有雙氧水的研磨液(slurry)定量後,利用步徑馬達 圖2推動裝有半氟橡膠(Viton)材質O型環(O-ring)的螺桿(piston) 圖3,將固定之微量硫酸鈰(Ce(SO4)2)滴定入反應槽 圖4,和研磨液中的雙氧水進行反應,並利用總共推進的硫酸鈰體積量,回推計算出雙氧水的重量百分比。
圖1、六向閥組
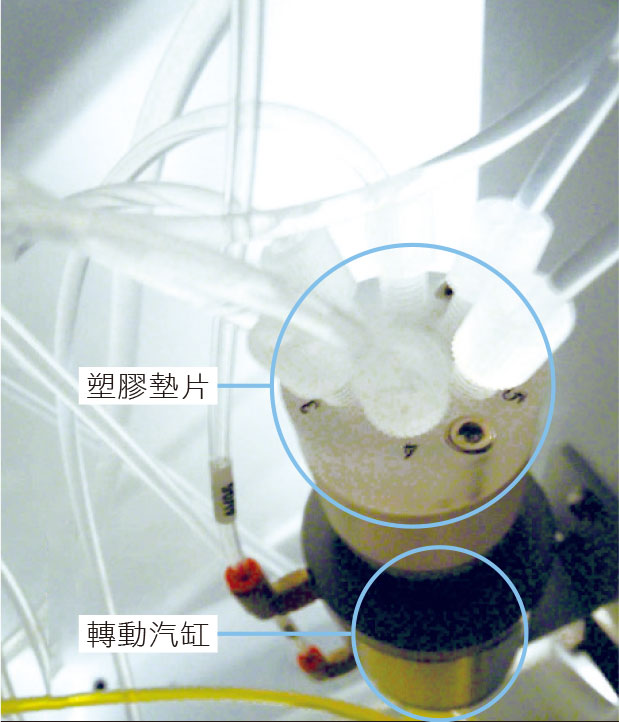
圖2、步徑馬達組
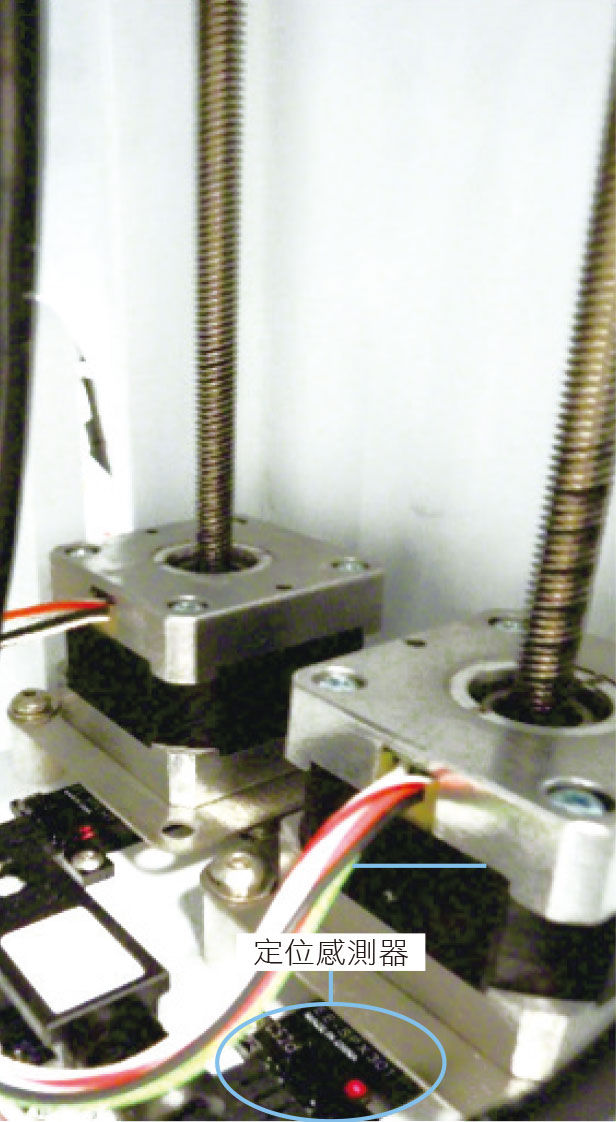
圖3、螺桿組
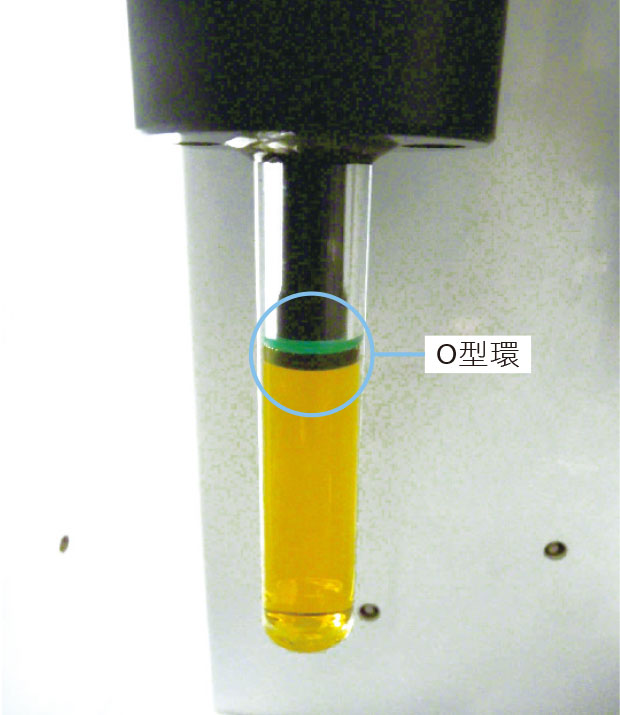
圖4、反應槽組
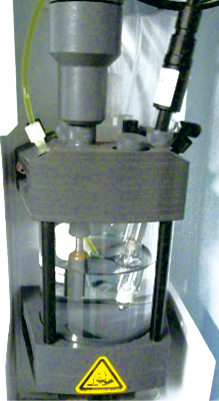
其中,ATRs部件內,尤以六向閥以及Viton O-ring最常出現問題,目前已經是各研磨系統課有使用此機型的頭痛宿疾,發生過的歷史事件諸如:六向閥的塑膠墊片因為經常性轉向作動而產生磨耗,造成定量失準以及漏液、六向閥汽缸推進異常,沒有完整轉向造成取樣異常、六向閥取樣溝槽結晶造成定量異常、O-ring 因為應力擠壓變形,使得硫酸鈰推進異常……等等,造成機台端每日出現許多品質警報,往往需要耗費大量人力、時間進行部件檢修(PM),以及分析師進行手動滴定量測以進行問題真偽排除。若能想出一勞永逸的方法減少不必要的機台警報,將這些工作負擔減輕,便能增進廠務運轉效率及研磨液廠駐(TSM)人員工作效率。因此本文利用下述三項改善手法以解上述之宿疾:
- 消失的六向閥
- 新式piston & 外穿式O-ring
- ATRs減量滴定,軟體計算優化
十四B廠廠務端一年硫酸鈰的使用量及花費高達兩百五十萬,而硫酸鈰滴定的使用量正比研磨液取樣量或者雙氧水含量,其中雙氧水含量不可變動,而他廠已有進行取樣減量的做法,但伴隨而來的副作用是滴定結果會變得相當不穩定(誤差±0.005%),使得這塊餅看得到卻吃不到。以下便以上述之三項目標進行改良實驗設計。
實驗設計與分析
此章節將分成三個部份,針對六向閥和螺桿組進行新概念設計、硬體改造,以及ATRs 軟體計算進行驗證和優化。
消失的六向閥
以往針對問題的改善做法常常都是利用加法,比如說額外加閥件或者改管等作法,而ATRs宿疾問題大多數都環繞六向閥,因此,反向思考,若能夠直接拿掉六向閥,以其他方式進行定量,並能夠達到一樣的穩定偵測結果,則能達到一勞永逸之成效。
在設計概念上,將原本經過六向閥的取樣路徑 圖5,直接藉由閥件開關的滯吸力進行定量 圖6,並配合將定量管尾端拉出毛細管 圖7,使slurry在管內的附著力被強化,便可進一步避免因為閥件開關的瞬間壓力,可能使得定量管內部分的slurry被回拉,而影響定量準確度。
圖5、原始設計之邏輯圖
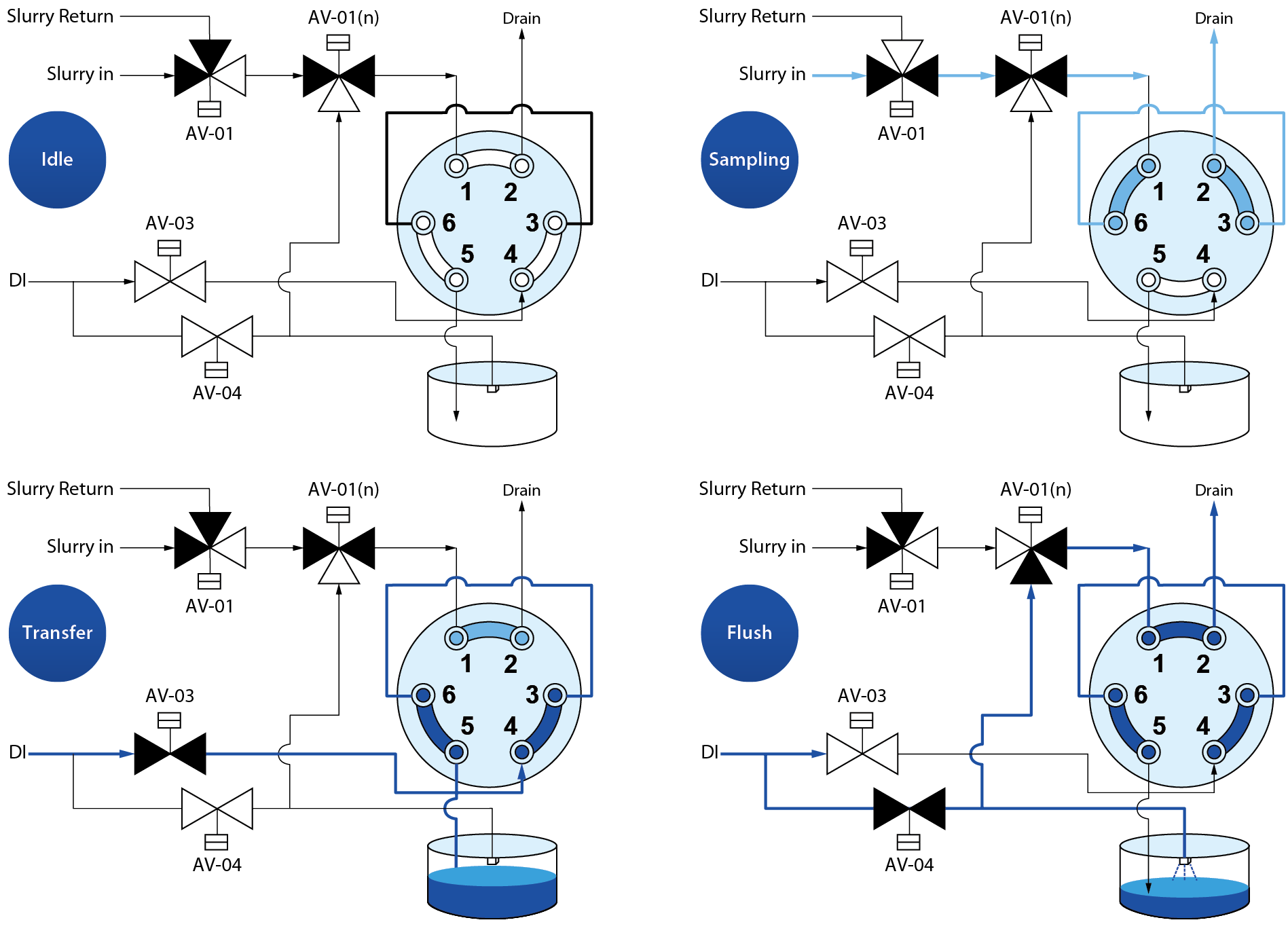
圖6、新設計之邏輯圖
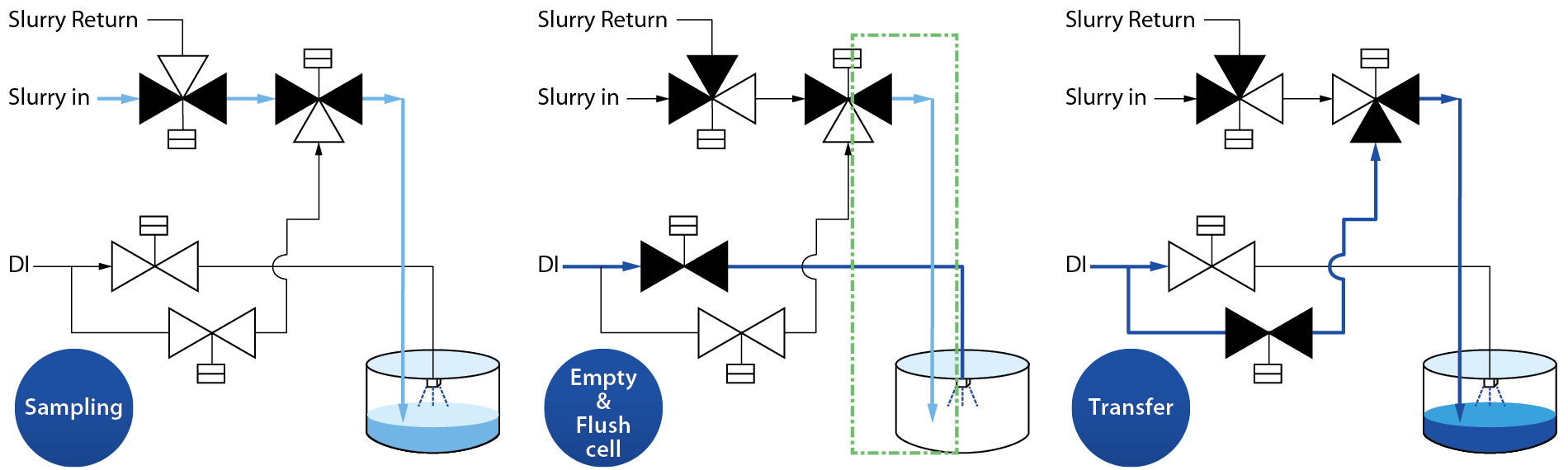
圖7、拉出毛細管之定量管比較圖
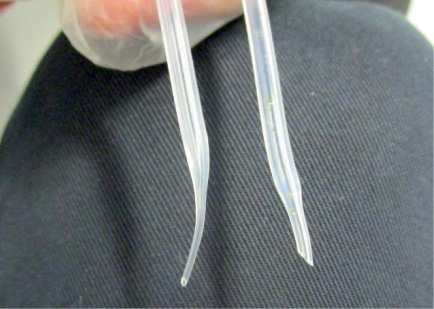
原本系統運作的軟體作業碼(recipe)也必須進行修改 圖8、圖9,將取樣(sampling)步驟提前至第一次洗空(empty cell)之後,並且最後滴定結束後,再加入兩道送水程序(transfer)進行定量管清洗,徹底將定量管以超純水(DI)洗淨,如此才能符合實際運作邏輯。
圖8、程式作動修改後流程圖(上半部)
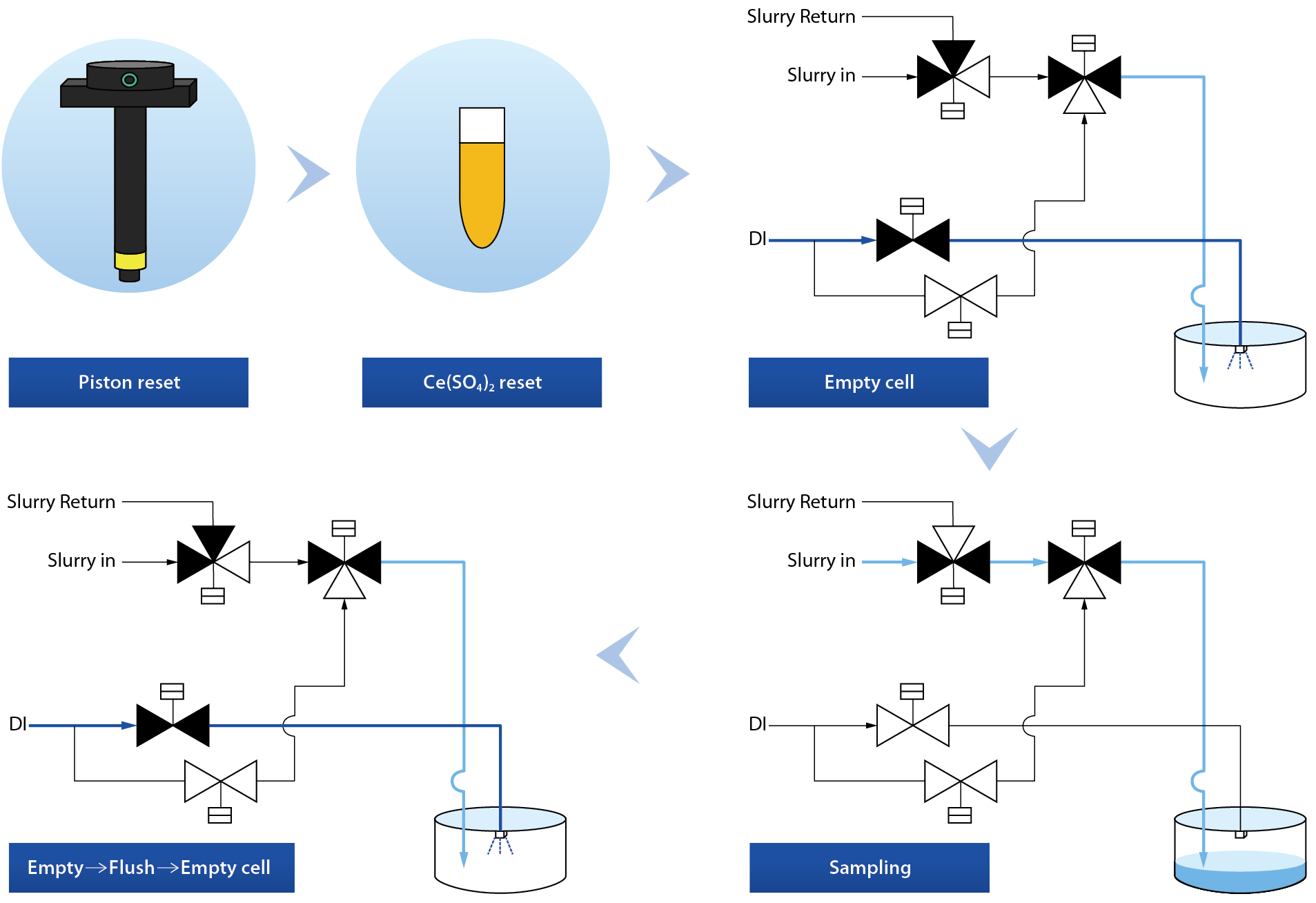
圖9、程式作動修改後流程圖(下半部)
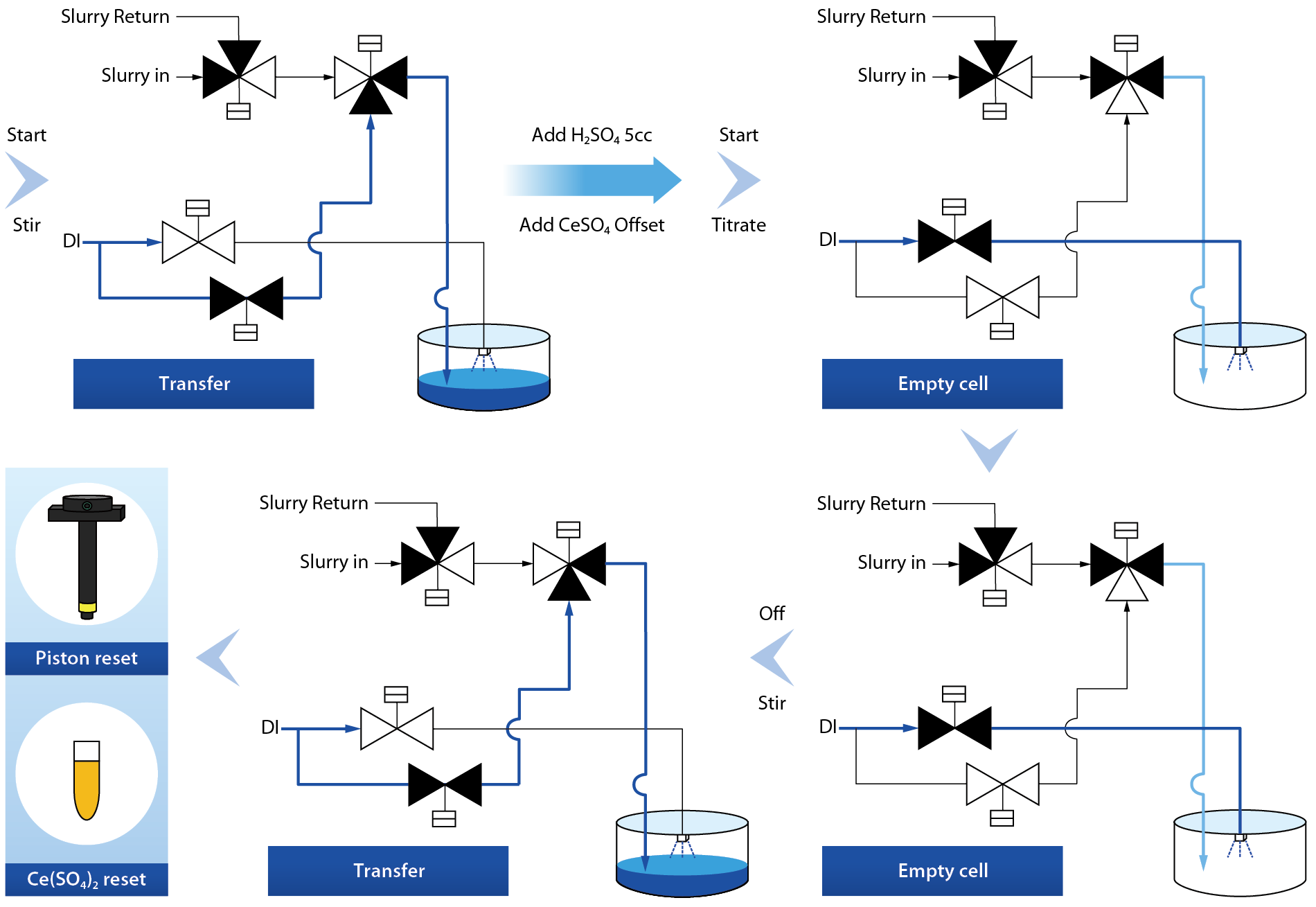
新式Piston及外穿式O-ring設計
一般來說,Viton材質的O-ring會依據其規格,摩擦係數介於0.25~ 0.60,蕭氏硬度(D-type)小於D30,由於硬度偏低、摩擦係數相對較高,其因為日常滴定(每日約20次左右,用量越大次數越多)進行螺桿推進、回拉動作而造成O-ring擠壓變形;針對其他高分子作調查,比較其物理特性後,選了兩項摩擦係數較低且不會使得成本過高的材質進行實驗–聚乙烯(PE)、鐵氟龍(PTFE),如 表1。
特性品名 |
PE 聚乙烯 |
PP 聚丙烯 |
4F 鐵氟龍 |
PEEK 塑膠 |
Viton 半氟橡膠 |
---|---|---|---|---|---|
硬度 |
D68 |
D75 |
D55 |
D86 |
<D30 |
耐熱溫度 |
80°C |
105°C |
260°C |
260°C |
200°C |
酸鹼程度 |
弱酸鹼 |
強酸弱鹼 |
強酸鹼 |
強酸鹼 |
強酸弱鹼 |
摩擦係數 |
0.18 |
0.37 |
0.04 |
0.02 |
0.25~0.60 |
此部分設計的理念,目的要盡可能地延長PM週期、降低人力成本,因為現實不存在不損壞之素材,而若要製作全高分子的O-ring,又會使得製作成本大幅上升,人力成本降低的效益便會大打折扣,因此運用市面包覆式O-ring的概念,此處材料不需要到精細包覆的程度,直接利用原本Viton O-ring的體積,再其外穿上一層硬度較高,摩擦係數較低之定模「高分子盔甲」 圖10。
圖10、外穿式橡膠O 型環實際照片
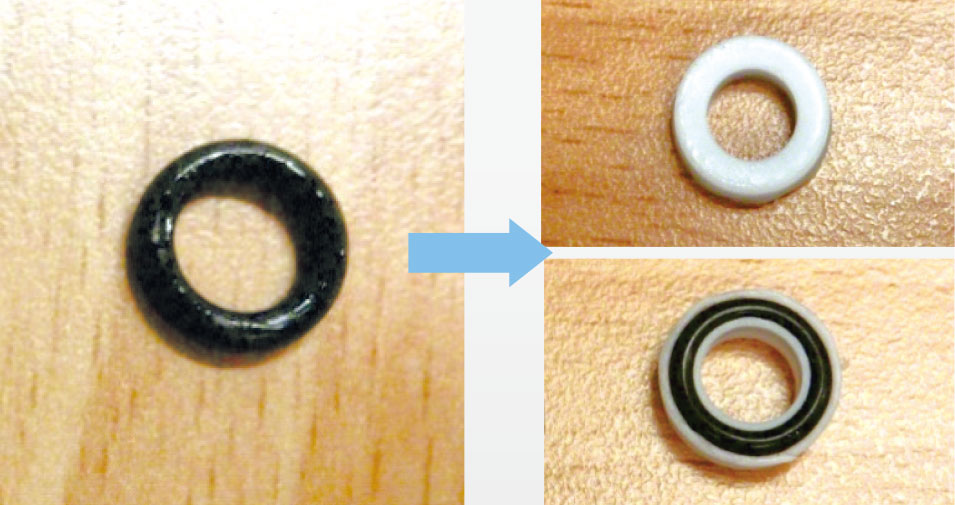
而此新設計之外穿式O-ring,由於無法利用原本的Piston進行安裝,並且原廠的Piston取液口,其設計是面口向內的圓錐型,所以取液口實際是高於O-ring安裝處,若當O-ring密合度發生異常時,便會明顯造成步徑馬達計算的推進量和實際滴定量不符合的狀況,就會有數值異常問題;因此,針對此問題,將Piston的取液口修改成向外突出而內徑不變的圓柱頭(suction head),並且在前端做出微縮,避免外穿式O-ring裝上後,會因為步徑馬達回拉而脫落,如 圖11,實際安裝結果,如 圖12。
圖11、Piston 改良前後圖
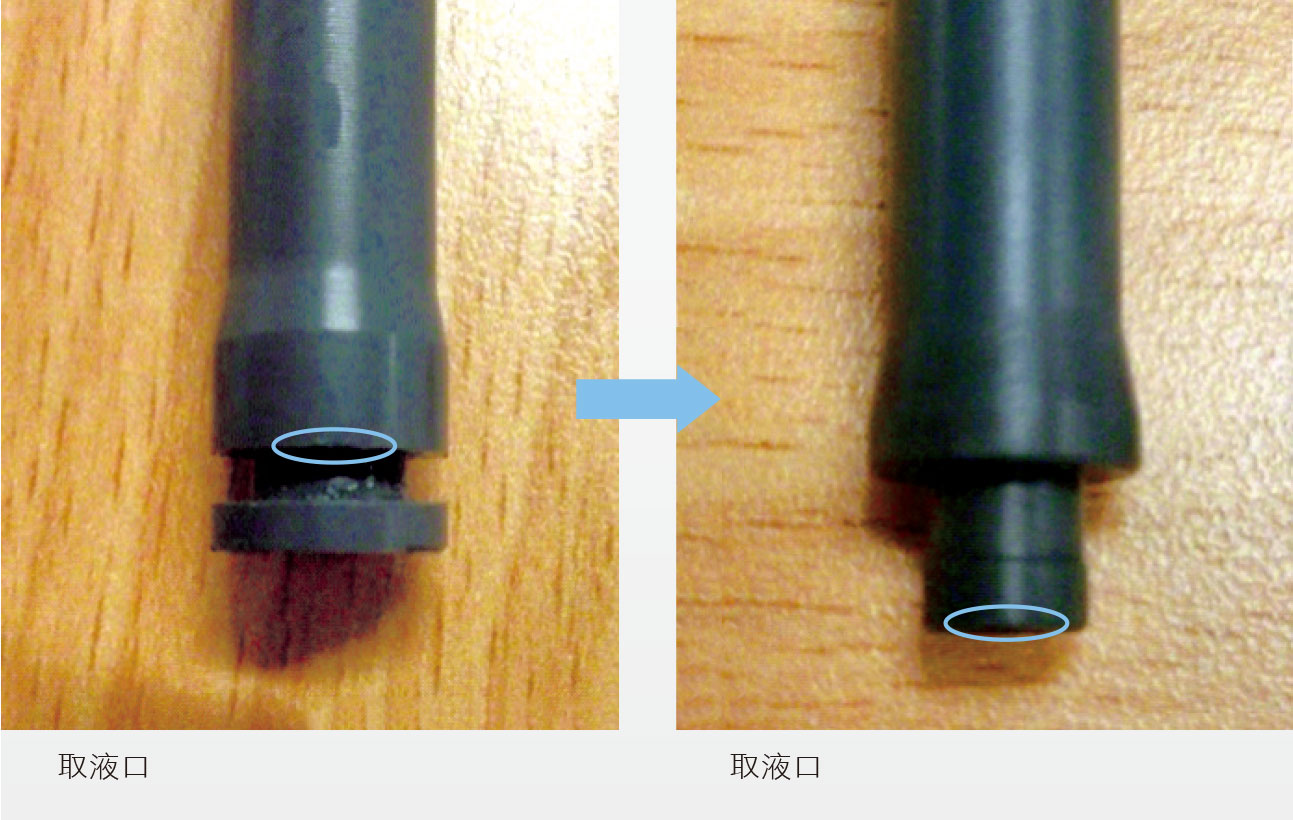
圖12、實際完整安裝圖
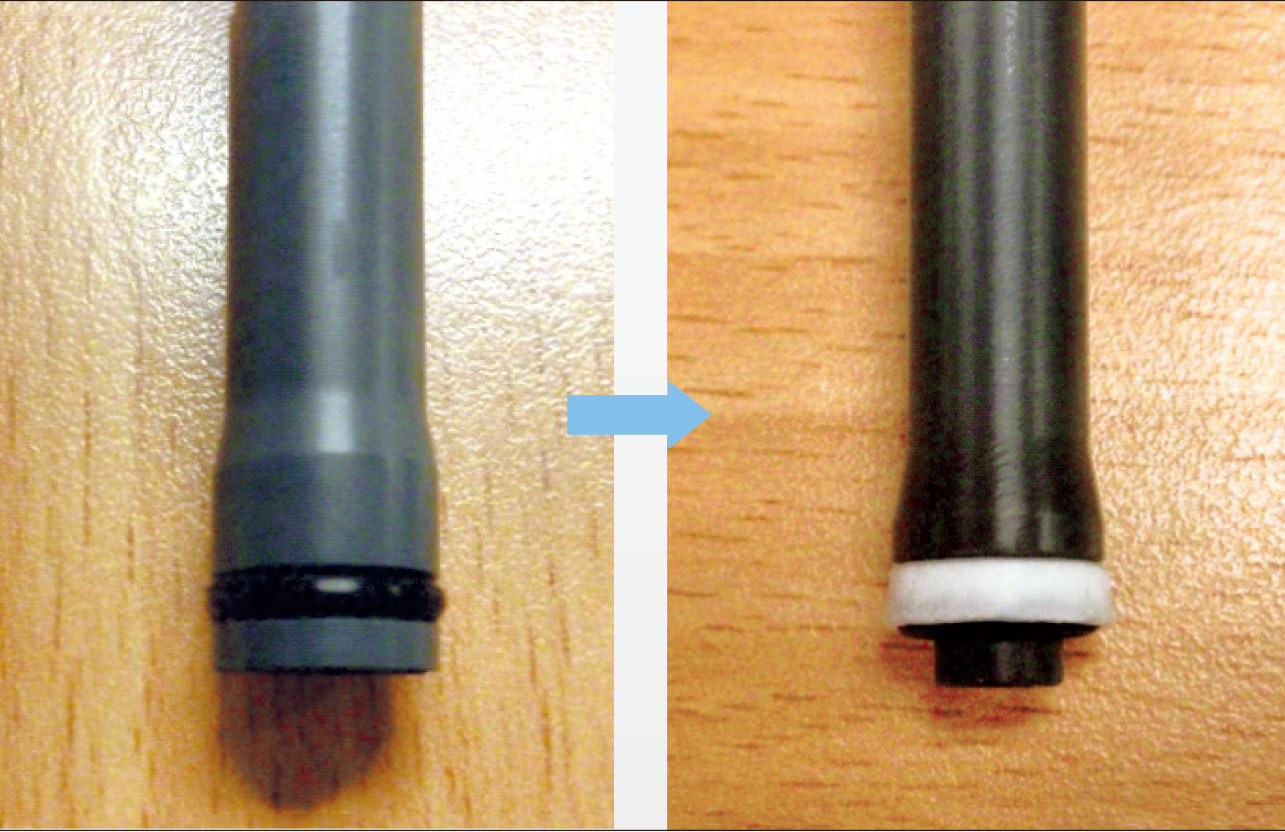
ATRs減量滴定,軟體計算優化
廠內使用之硫酸铈為相當高價的化學品。此藥劑於ATRs之使用量正比於slurry的定量,目前使用的是原廠1毫升定量管搭配六向閥使用。其他廠區曾提出將定量管縮減便能達到減量之成效,但此減量實際應用時,對滴定結果會產生雙氧水量測穩定性不佳之問題,造成品質圖(trend chart)被監控單位挑出檢討,反而增加廠務人員工作負擔 圖13。
圖13、取樣減半後,雙氧水量測品質圖
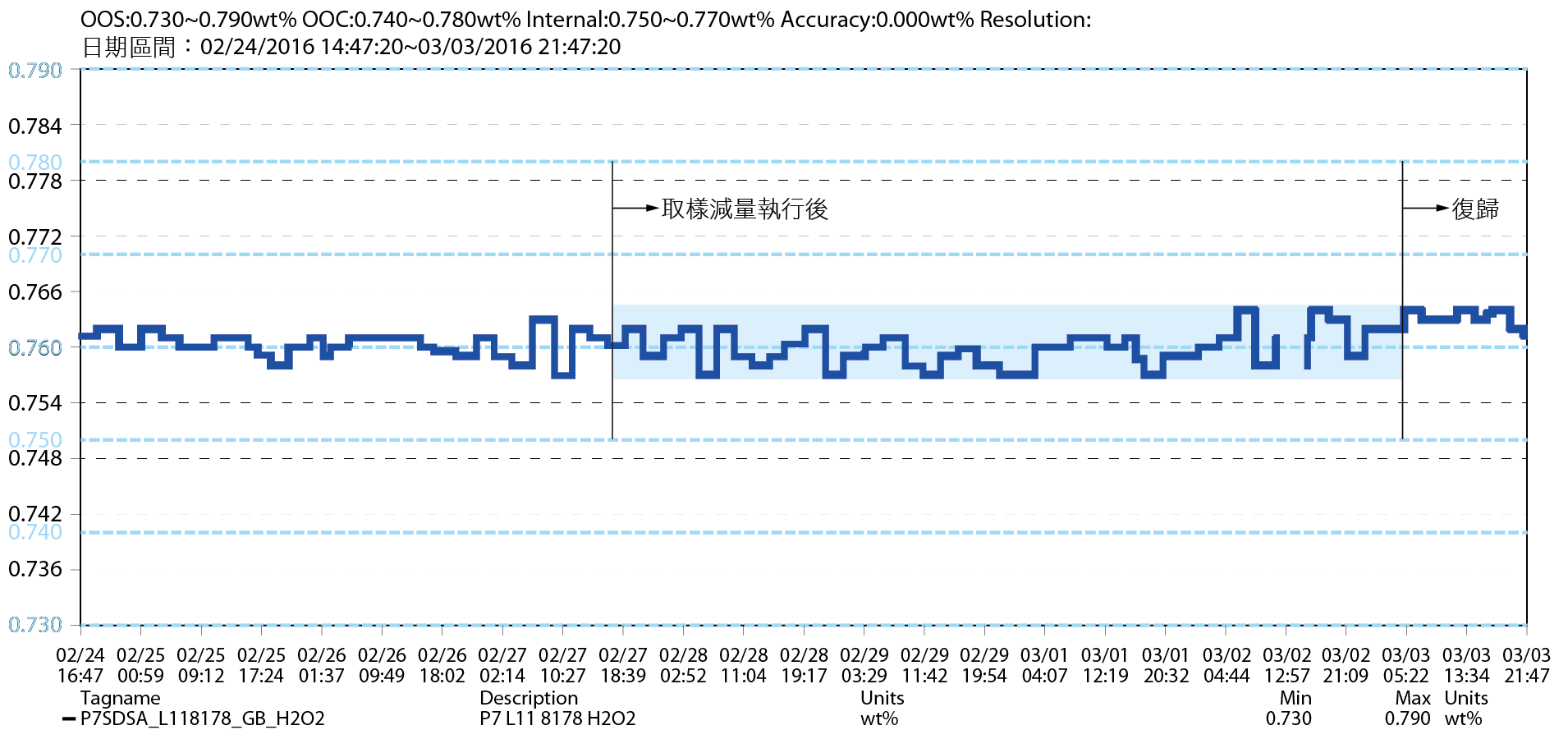
基於懷疑立場,直接檢驗ATRs的歷史資料,取21筆資料出來,將每一筆當量點,扣掉上一筆當量點作出折線圖可發現,平均每筆滴定,硫酸鈰的使用差異量是落在0.0003~0.0005毫升之間 圖14,小數點下四位,這意味著每次的滴定誤差是非常微量的,但為何卻造成同一鍋研磨液之雙氧水 trend chart有0.005,小數點下三位以上的誤差產生?表示軟體計算方式,必須深入檢視。
圖14、硫酸鈰铈使用差量圖
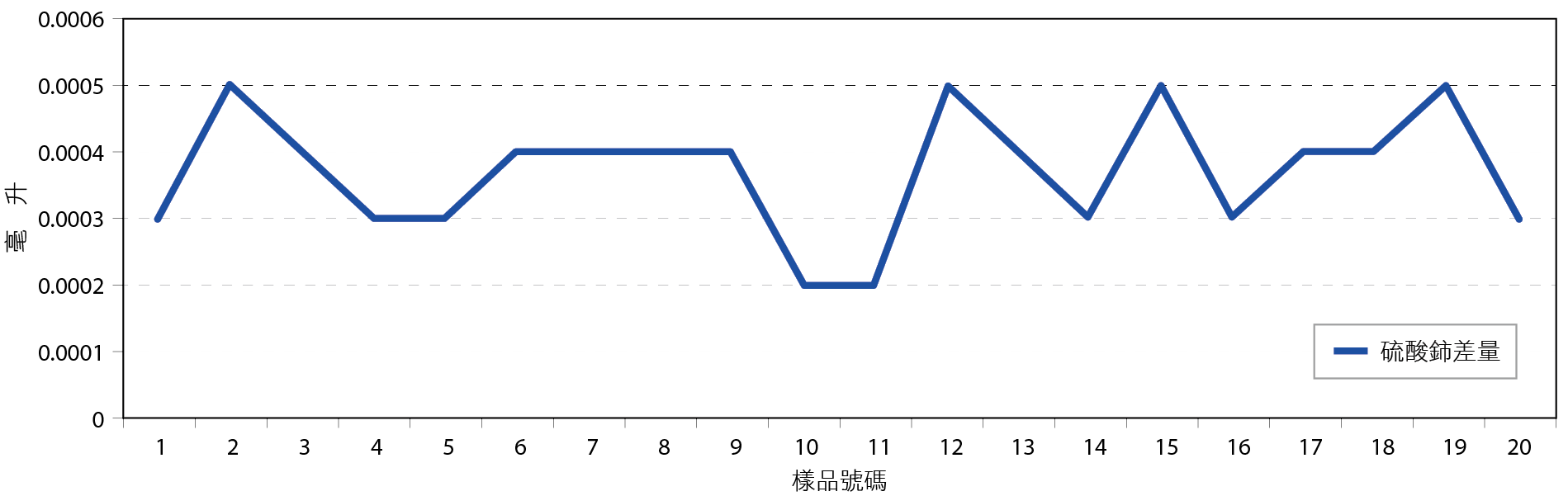
因此,檢視ATRs軟體計算結果,可以發現其H2O2數值公式為:
(參與反應硫酸鈰量+硫酸鈰預加量)×Factor= H2O2數值(%) ........... 式一
由上式我們可知,無論是何種雙氧水濃度的slurry,滴定結果都一樣需要乘上修正常數(Factor)才會變成測定的雙氧水濃度值。此因原廠自動滴定儀是設計給多種化學物品使用,但每種化學藥品的減量線並不相同,換言之,若取樣濃度不同,便會需要利用factor去修正滴定結果。從上述之公式,表示前一筆和後一筆滴定的變化值會等於:
(硫酸鈰滴定差異量)×Factor=每筆滴定雙氧水變化量 ........... 式二
而當取樣量減半,對同一種研磨液而言,雙氧水的含量是固定的,若軟體計算要得到一樣的濃度值,則必須將factor放大兩倍,然而,從 圖14便已知,硫酸鈰的滴定差異量是固定的區間,因此,就公式二可知,當factor被放大,變化值也就會跟著放大,此證明為原廠系統的計算方式造成此誤差結果。
因此若取樣量減半,並要維持原本的量測的雙氧水變化量,則factor數值必須要和減量前一樣。本文改變滴定儀「計算程式」中的硫酸鈰預加量(offset),而不改變「作動程式」 螺桿步徑馬達的實際推進量 圖15,所以不會影響實際滴定的真實性,便可維持取樣減半後的factor數值和減半前一樣。
圖15、量測機台主機板司職示意圖

圖16人員實際改機流程說明,根據結果可知,變化值會因此放大。
圖16、人員實際改機流程說明
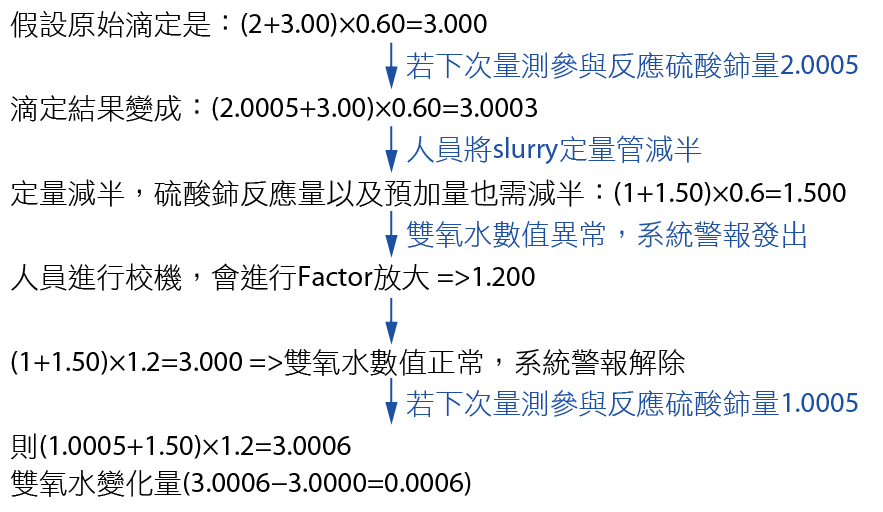
在軟體設定中,放大ATRs硫酸鈰預加量的「計算值」,將假想數值設定,使得Factor等於執行定量減半前,但實際動作設定,螺桿預加硫酸鈰設定量不去做改變;依 圖16例子,將計算程式中,硫酸鈰添加量改成4.00,如 圖17說明,則取樣減半後,修正常數便會和減半前一致。
圖17

結果與討論
將六向閥移除的理念,已成功安裝並實踐;而新式piston以及外穿式O-ring安裝了九台;ATRs軟體優化的方式則已驗證。
ATRs 消失的六向閥之成果
實際機台測試點數已超過八個月,此期間除了因為電極電壓值異常進行更換、以及槽車雙氧水濃度變化造成的trend chart起伏以外,平常雙氧水滴定之結果,是改造前、後不變。除了O-ring PM外,未曾有過任何相關H2O2警報,相較於2015年同一廠區因為六向閥而造成之警報共四百餘次,若此法能全面施行,相信可大幅減輕廠務運轉壓力。
另外,H2O2 trend chart曾被質疑是否有太過穩定而呆機之狀況,因此有故意進行機台的惡化實驗:混酸異常操作。實際利用非供應端的桶槽,故意做出水比例偏多的研磨液,結果系統確實能逮到雙氧水濃度偏低的異常狀況並發出警報 圖18,證明不會因為太過穩定而呆掉,由以上之成果已證明將六向閥移除之概念已具有實戰之可能性。
圖18、混酸異常實驗結果
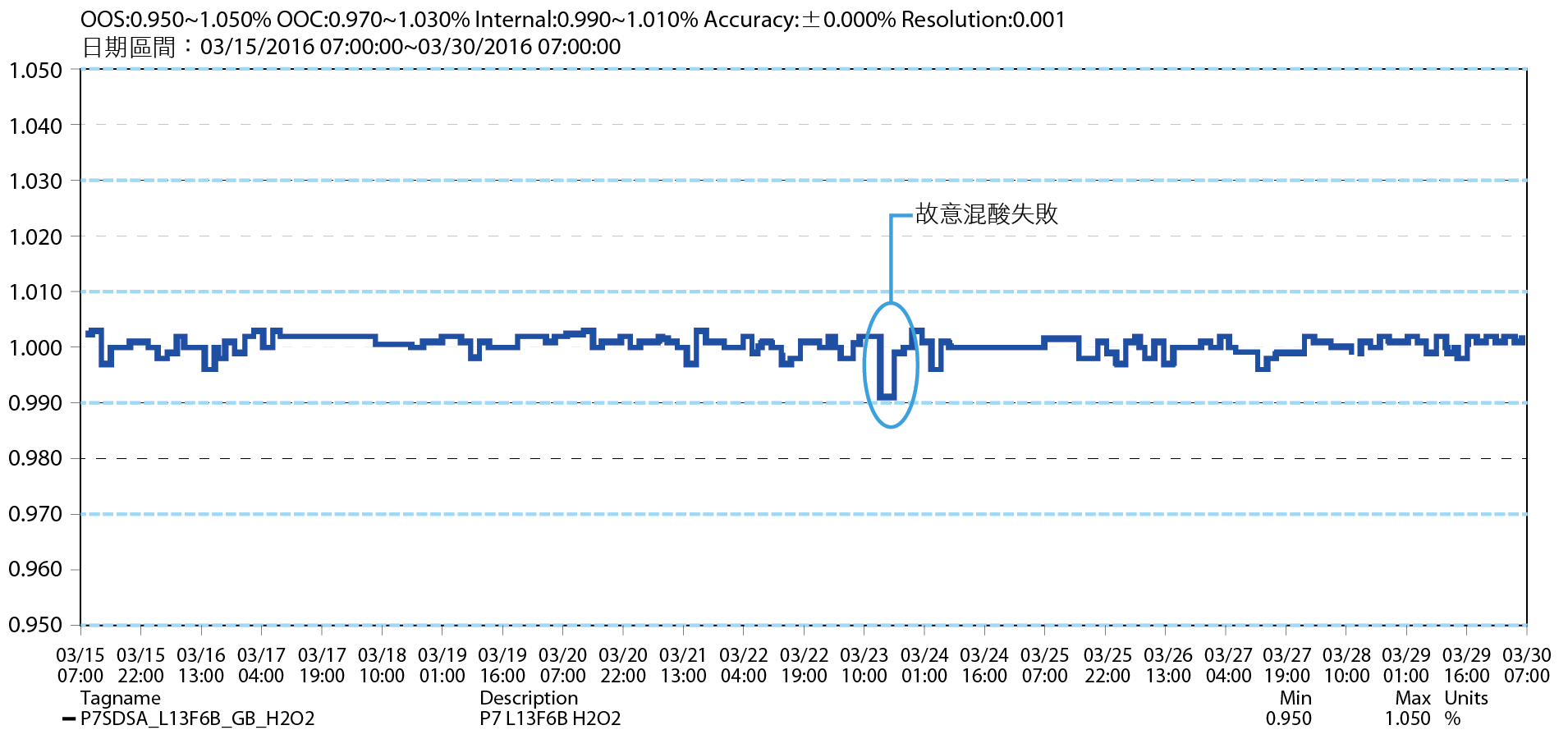
新式Piston及外穿式O-ring之成果討論
過往因為O-ring之磨耗使得密合度異常,影響了硫酸鈰的滴定,最終使機台觸發ATRs的假警報(手動檢測正常),並且會和線上用量相關,用量越大、檢測越頻繁,便越容易造成問題,幾乎是每台一個月都會異常一次。計算2015年O-ring造成之相關警報高達576次 圖19,狀況排除之人力負擔龐大,亟需解決此問題。
圖19、Alarm Estimate
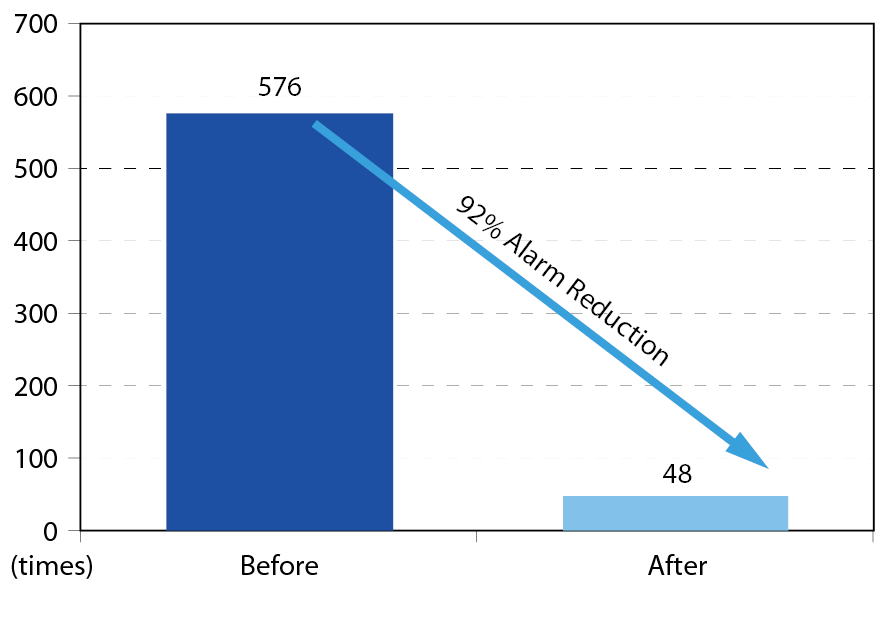
此計畫之成果,總共已實驗十台,至目前為止,最長超過一年並無造成任何相關警報發生。本章節將以此超過一年之機台其雙氧水量測結果作主要討論。
安裝上新設計之Piston及O-ring組,此處使用的是「鐵弗龍材質」(PTFE)聚乙烯(PE)材質的測試結果,由於其蕭氏硬度較大(D68),內層的Viton O-ring無法有效將其撐開,於推進或者回拉過程中,外層盔甲容易向內縮而造成密合度異常問題。此組合由H2O2的即時量測結果,可發現實驗前後的結果不變,並且安裝後至今最長已經一年又三個月未執行ATRs O-ring PM(包含上油或者更換橡膠環),並且雙氧水的量測結果皆因為此料件測試造成之異常狀況,預計全面更新之後,TSM和廠務人員工作負擔絕對可大幅下降 圖20。
圖20、O-ring Life-time Comparison
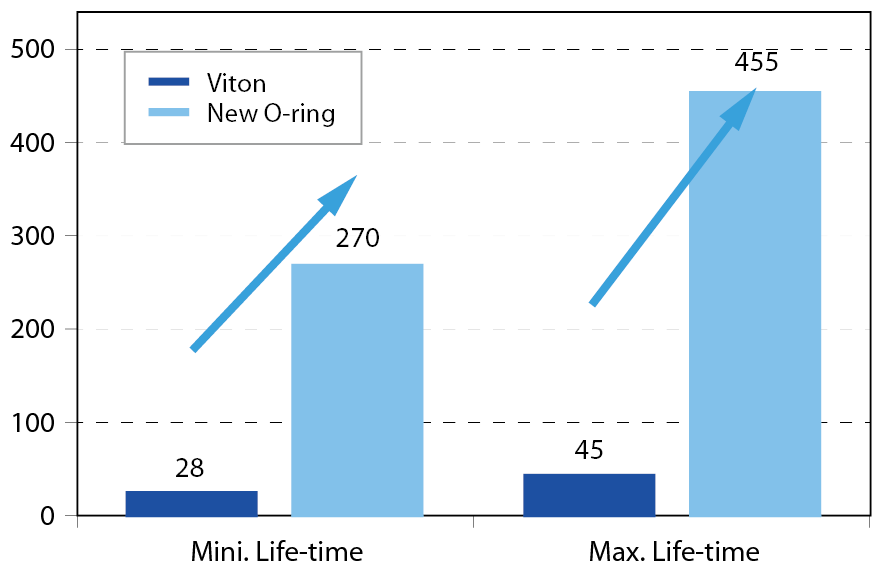
ATRs減量滴定,軟體計算優化
此處作法,故意利用雙氧水含量較低之研磨液作測試,來加強驗證此計算優化的方法(雙氧水含量越低,若取樣減半更容易造成滴定不穩),機台原始的滴定數據,當量點硫酸鈰消耗約4.52毫升,預滴定量為零,雙氧水含量為0.760%;利用式一求出factor為0.1681,因此當取樣量減半後,factor會放大成0.3364,此時候的H2O2 trend chart出現許多異常突波,因此被監控單位挑出進行檢討 圖21。
圖21、機台取樣減半後之雙氧水量測結果
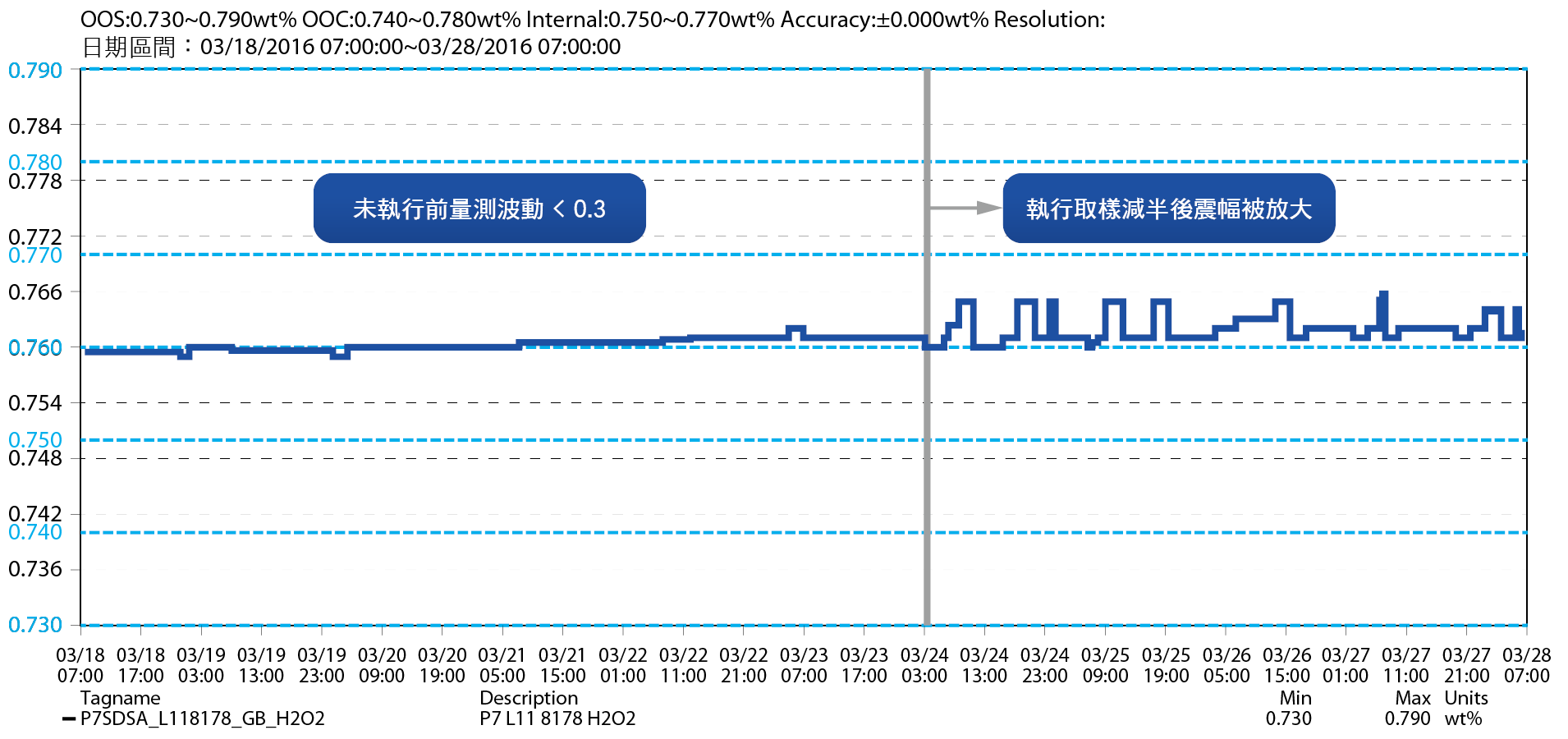
於是進行軟體數據優化,將假想預滴定量設定於計算程式內,取樣減半後的當量點消耗量為2.26毫升,設定預滴定量為2.26,兩者相加後,系統便會判定當量點消耗量為4.52毫升,則factor恢復為0.1681,此時H2O2偵測穩定度便會恢復正常;另外,為證明不會因此修改而H2O2量測變成呆掉,故意進行雙氧水/slurry混酸比例異常實驗(雙氧水多加一些),結果一樣可逮到異常量測值 圖22,如此便可使取樣減半達到實戰性之使用,預計一年該廠區硫酸鈰的使用,可節省約250萬。若各廠能使用此法進行雙氧水量測取樣減半,每年節省下來的物料成本便會相當可觀。
圖22、執行計算優化後之雙氧水量測結果
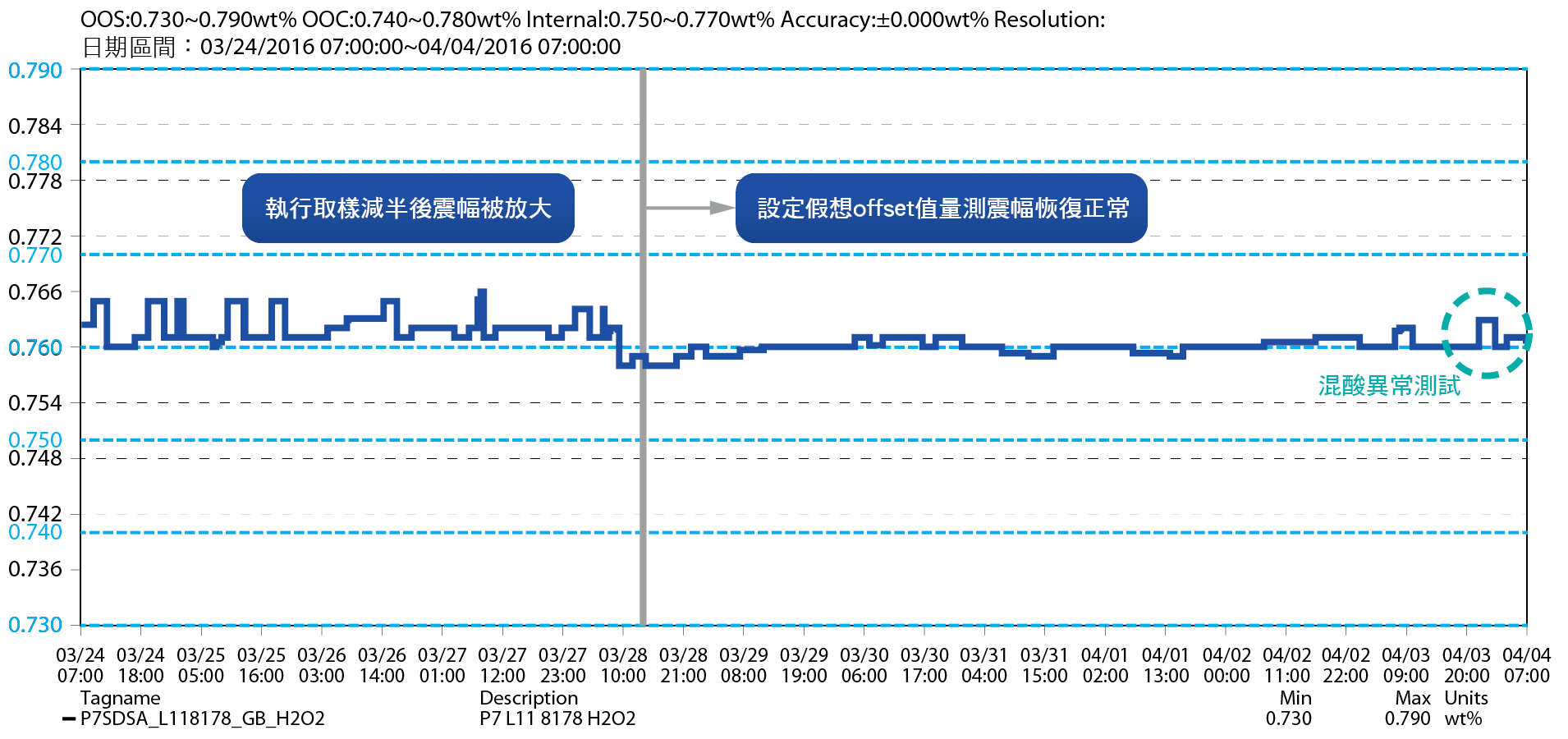
結論
以上各項已成功實踐之作法,利用2015年的狀況計算,預計十四B廠一年人力可節省三千多小時、一年機台警報減量九百餘次、物料一年可節省五百多萬。此外並提升廠務運轉效率,不必花費大量時間處理假警報。廠駐人員不必一直取樣送測實驗室,以及進行ATRs的各項異常狀況排除,甚至原本ATRs的月/季/年保養,都可以不必執行,廠駐人員將可實現只要保養機台外觀之理想願景,相信對本公司有使用到ATRs的各廠人員,其工作效率會有顯著之幫助。
留言(0)