摘要
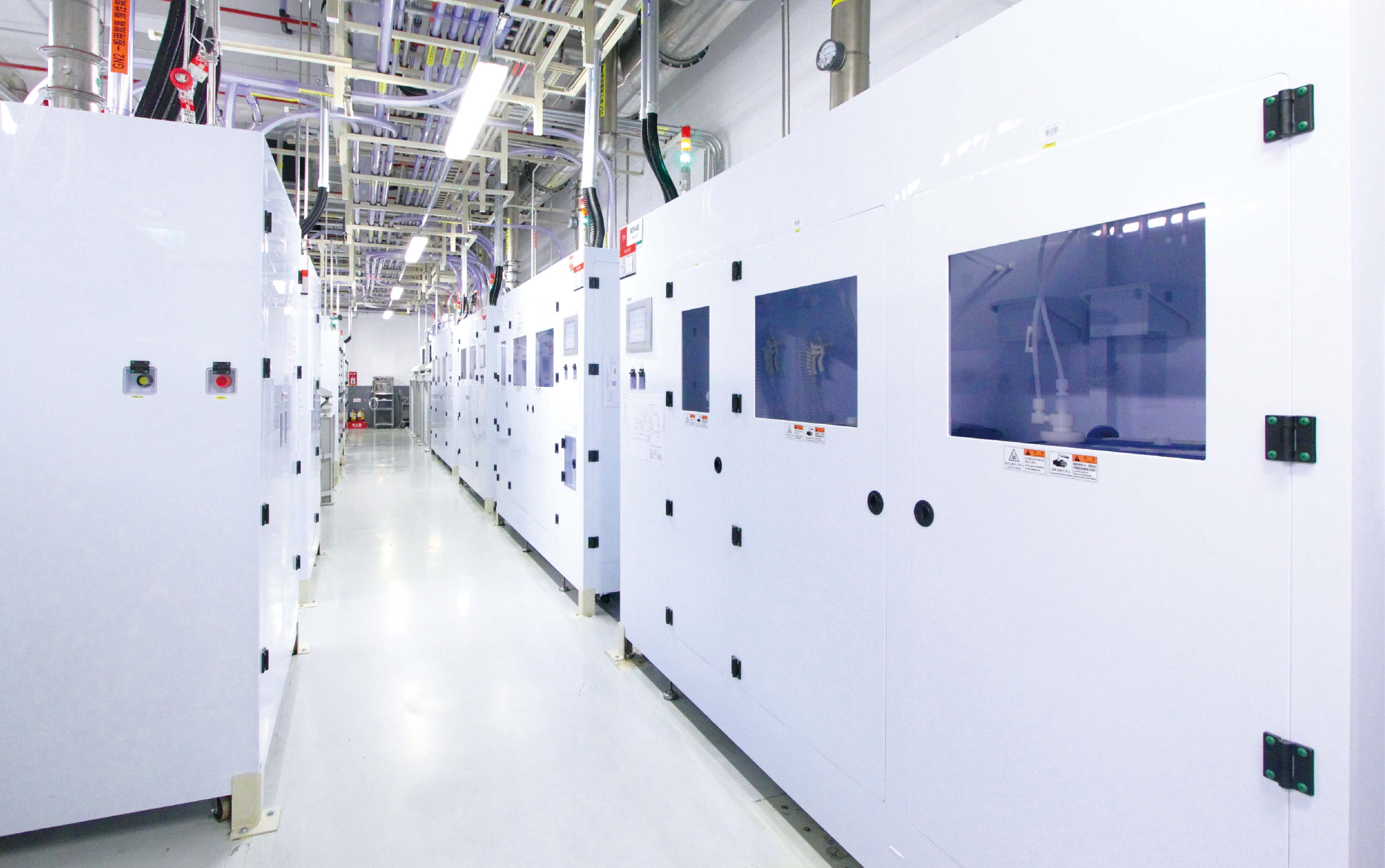
化學品用量異常即時偵測系統
Keywords / Waste Chemical4,Abnormal Consumption,Abnormal Drain,Chemical Consuming Defense System2
半導體製造工廠所使用之化學品,大部分由廠務端中央供應系統自動供應至產線端設備機台。當設備機台發生異常時,容易發生化學品異常大量使用。為了使化學品異常使用防禦系統達到即時且全面性的能力,廠務與自動化整合部門共同開發「化學品用量異常即時偵測資訊科技工具」以達到快速、即時、有效地偵測到異常事件並排除。迄今已實際成功偵測到數次設備機台異常,有效避免化學品錯誤的浪費,節省生產成本與防止環境危害擴大的風險,提升廠區生產運轉穩定性。
前言
中央化學品供應系統(Chemical Dispense System, CDS)依據設備機台提出要酸訊號(Request),系統經由啟動泵浦(Pump)並開啟供應路徑上的閥件(Valve)將儲存槽(Day tank)的化學品供應至機台設備,如 圖1所示,紅色路徑為化學品供應路徑。
圖1、化學品供應路徑圖

廠務端既有化學品異常用量偵測防禦機制有以下兩種方式:Barcode System 、Request Time Out 功能。Barcode System可記錄原物料使用狀況,並統一彙整於廠務中央監控與數據收集系統(Supervisory Control and Data Acquisition System, SCADA System),SCADA收集廠務系統相關資訊(機況警報、要酸訊號、換酸資訊),於每天人工統計換酸數量,確認是否有異常大量換酸狀況,若有異常尚需與廢液系統排放量進行比對。此資訊的查詢皆必須至廠務值班室電腦進行,需要人員進行資料彙整,且無法反應設備要酸模式是否有改變趨勢,只能透過廢液系統的變化量進行判斷,若該化學品屬於排放至廢水系統的種類就更加難以掌握。
要酸訊號逾時(Request Time Out)的設定:要酸開始與結束時間皆會被廠務系統紀錄,機台要酸時間已有逾時的警報機制;當設備機台提出要酸訊號時間超過警報設定即為要酸時間逾時(Request Time Out),此時系統主動強制關閉供應閥件,如 圖2所示。但此作法無法偵測到高頻率短時間的異常要酸模式,且此警報會實際關斷供應閥件,停止供應化學品至設備機台,若為錯誤判斷時將有導致生產中斷的風險。
圖2、要酸訊號逾時停止供應示意圖
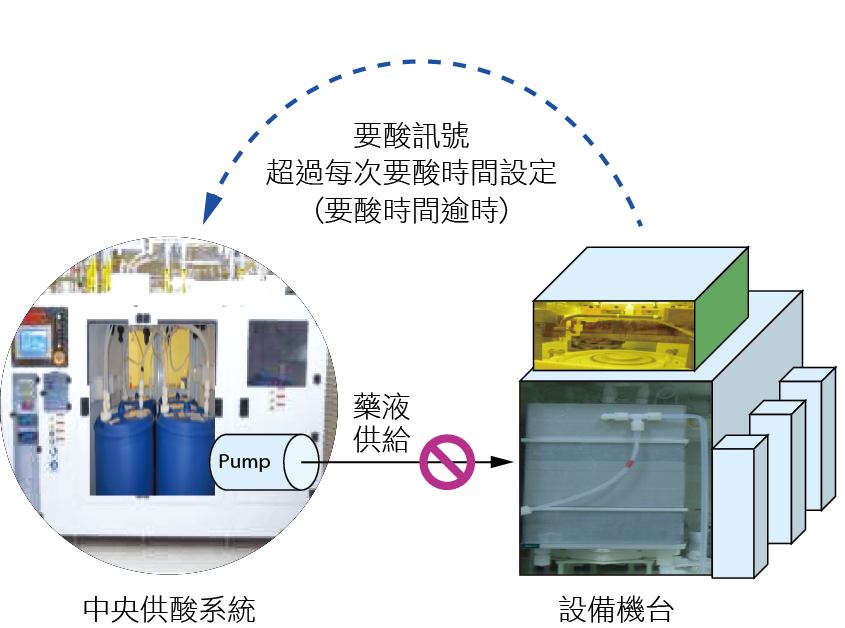
因此我們思考,針對現行化學品異常用量偵測機制(如 表1)是否有新方法改善,既然SCADA系統已有設備機台要酸時間的資料庫,藉由此資料搭配程式自動判斷,套用統計學標準差觀念,以找出機台合理要酸時間,並達到能即時偵測化學品異常用量的自動化系統。
廠務系統 |
防禦機制 |
手法 |
是否能偵測線上機台異常 |
自動警報功能 |
影響線上機台 |
反應時間(hr) |
人力需求(manhour) |
Remark |
|
---|---|---|---|---|---|---|---|---|---|
單次大量要酸 |
多次小量要酸 |
||||||||
中央供酸系統 |
機台要酸訊號監控 |
限定單筆要酸訊號時間(Request Time Out) |
V |
|
V |
V |
<1 |
0 |
不適用高頻率短 秒數異常狀況 |
每日要酸桶數統計 |
人工統計 |
V |
V |
|
|
24 |
1 |
反應時間長,難以 追蹤異常機台 |
計畫方法
要達成化學品自動偵測警報功能,必須克服資料可自動上傳,並讓系統能具備自動比對功能,以下將說明功能建立流程與分析邏輯。
IT資料自動上傳
線上設備機台要酸訊號會記錄SCADA系統,我們利用VBA語言建立要酸訊號自拋程式(採用Excel格式),此程式建立於SCADA電腦,可自動抓取資料庫內欄位數值(Raw data),並將其資料儲存於中繼站電腦,接下來利用Windows內建排程工具,每小時(可依需求者自行定義)執行要酸訊號自拋程式,即可達成將資料自動匯出至IT資料庫指定路徑,程式邏輯流程如 圖3所示所示,以便CIM (自動化整合部門)由指定路徑讀取資料進IT資料庫進行分析,使資訊公開透明化。
圖3、自拋程式資料自動上傳邏輯判斷流程圖
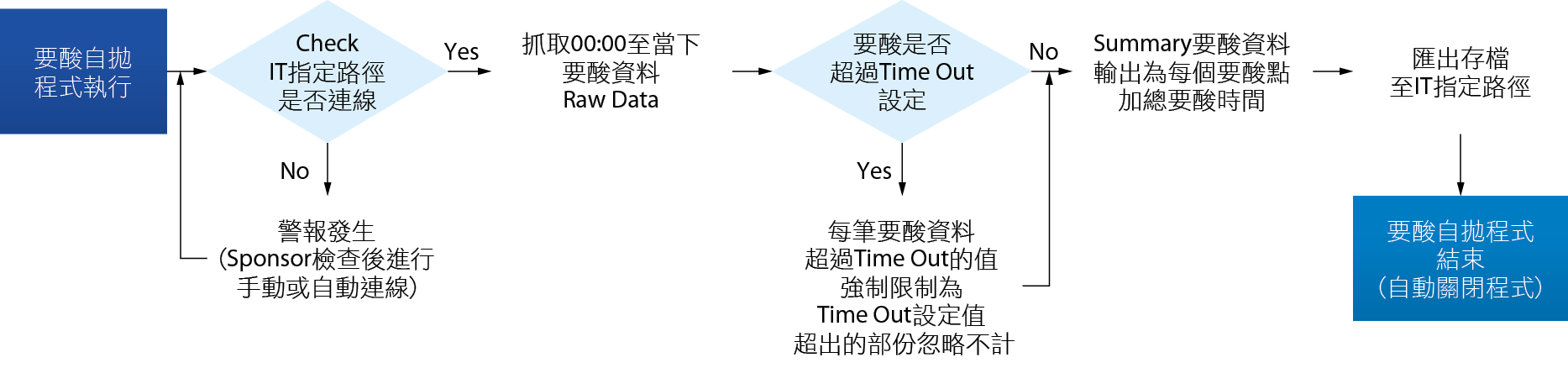
IT資料自動比對
資料自動上傳至IT資料庫後,需有自動判斷與警報能力,可藉由資料庫中要酸秒數(Request Time)與要酸次數(Request Count)兩項資料做程式計算判斷方式。
要酸秒數自動比對
要酸秒數程式計算邏輯:將一天內機台的要酸秒數自動加總,則得知當天總要酸時間,連續取30筆資料(可依使用者需求改變;本次舉例為30天=1個月資料當計算),利用統計手法(自動計算)得算數平均值 (X)與標準差(sigma),並取3倍標準差(X+3‧sigma)視為警戒(Alert)設定值,當每小時資料自動上傳至IT資料庫後,若超過該設定值則判斷為異常要酸,計算是如下所述:
Xi=數據個別值,i=1~n;即為第1~n個數據值 (舉例:30天;n=30)
Xi=X1,X2,....,Xn
X=算數平均值;一組數據將其加總再除上數據的總量可得算數平均值
sigma=標準差;該組數據各別與其平均值之差的平方的平均數再開平方根
Alert limit=警報線;算數平均值加3倍sigma
Alert limit=X+3‧sigma
判斷流程圖如 圖4所示。
圖4、要酸秒數自動比對邏輯判斷流程圖

要酸次數自動比對
要酸次數程式計算邏輯:程式自動累加一天內機台的要酸次數,連續取90筆資料(可依使用者需求改變;本次舉例為90天=3個月資料當計算),將其總合後平均值乘安全係數1.2 (可依使用者需求改變;本次舉例為1.2當安全系數)當警戒(Alert)設定值,接下來繪製比較線,目的做為當比較線低於Alert設定值,則判斷為異常,為了避免過度警報或警報誤判,因此比較線計算採兩種時間:月比較線與周比較線,計算出30天(月)與7天(週)的算數平均值,當兩者同時高過Alert設定值時,則判斷為異常要酸,判斷流程圖如 圖5所示。
圖5、要酸次數自動比對邏輯判斷流程圖

結果與分析
系統介面與管理
藉由化學品資料自動匯出至CIM IT系統,使用NT帳號密碼登錄化學品用量防禦系統,如 圖6所示。系統分析整理化學品資訊後,將各機台化學品用量資訊以圖表格式呈現,程式畫面主要分三介面:搜尋介面/清單介面/SPC介面,以下將逐一說明操作。
圖6、化學品用量異常即時偵測系統介面
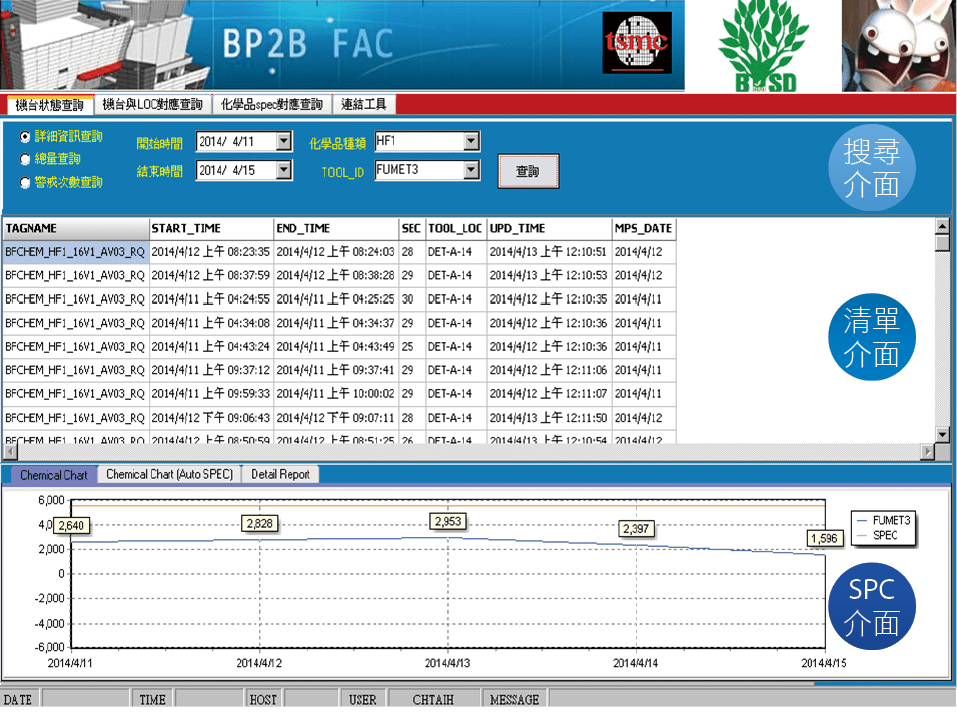
搜尋介面
進入介面後,共3種搜尋模式選擇:詳細資料查詢(預設模式)、總量查詢、警戒次數查詢,使用者可選擇開始與結束時間,並可依不同化學品種類與機台編號等相關資訊,明確找出特定機台於某時間內要酸狀況,如 圖7所示。
圖7、搜尋介面選擇查詢條件
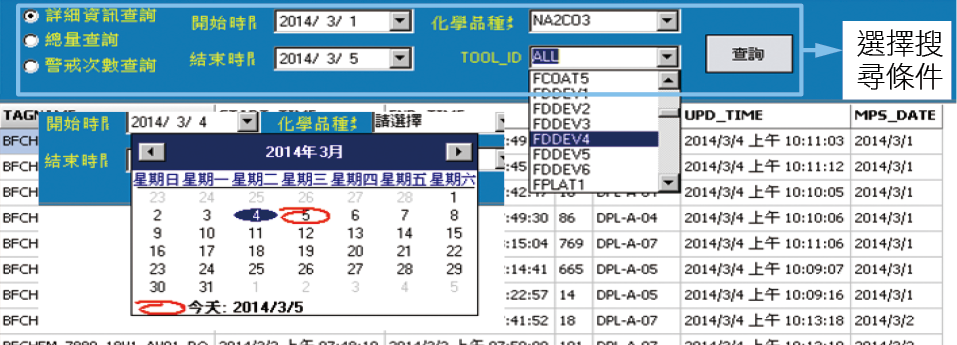
清單介面
清單介面主要顯示查詢後資料明細結果,可逐一顯示每筆要酸紀錄或其他資訊提供給使用者作參考,依搜尋模式不同則顯示不同描述,當查詢為[詳細資料查詢]則顯示該時間內每次要酸訊號資訊。若為[總量查詢]則顯示該時間內,特定機台或特定時間,該化學品總要酸時間與次數,如 圖8。若為[警戒次數]則顯示該時間內,機台發生過觸發警戒條件的次數,以便使用者快速了解機台狀況,如 圖9顯示。
圖8、清單介面顯示- 總量查詢模式
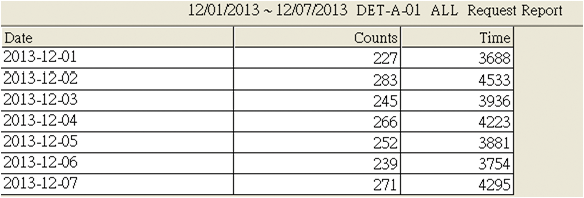
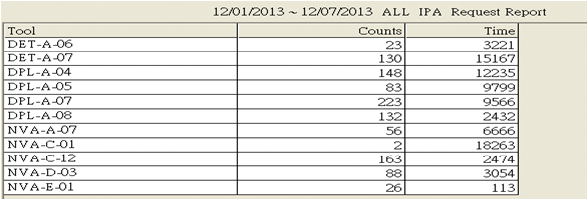
圖9、清單介面顯示- 警戒次數查詢模式
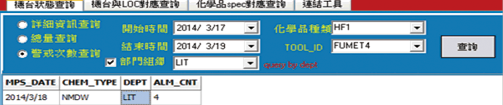
SPC介面
IT工具下方欄位顯示SPC Chart,代表該機台每天要酸總秒數(紅線),並顯示該化學品設定之警戒值(藍線),鑒於警戒線數值非固定值(取往前30天資料並依X̄+3Sigma計算),因此每天警戒值皆會改變,如 圖10。
圖10、清單介面顯示- 警戒次數查詢模式
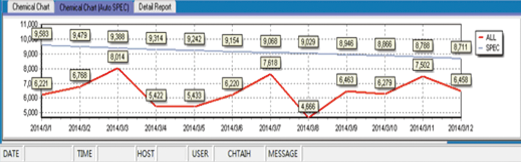
系統實績驗證
化學品用量異常即時偵測系統利用機台要酸次數和要酸秒數作統計分析,於2016年第一季上線使用迄今,過程中成功實際偵測到數次機台異常,以下舉例說明兩種較常發生的實際案例狀況。
實際案例一
顯影設備機台保養(Preventive Maintenance, PM)後因人為疏失,造成機台端Na2CO3化學品Fliter排泡閥件未關閉,導致異常高頻率用酸。由於每次要酸時間未超過Request time out設定,同時該化學品屬於排放至廢水系統種類,因此也無法藉由廢液系統發現問題。在往常此問題可能僅能透過每天交接統計換酸桶數才知道有異常,且也無法明確知道是哪台設備有問題,因此異常處理需花大量人力與時間,本次則於當日即發現異常機台的要酸次數與要酸總秒數增加,如 圖11,立即通報設備CCJO4JO檢查異常機台,發現運轉中機台化學品Fliter排泡閥件未關閉,快速有效找出問題並改善。
圖11、實際案例一,設備PM 後閥件未復歸
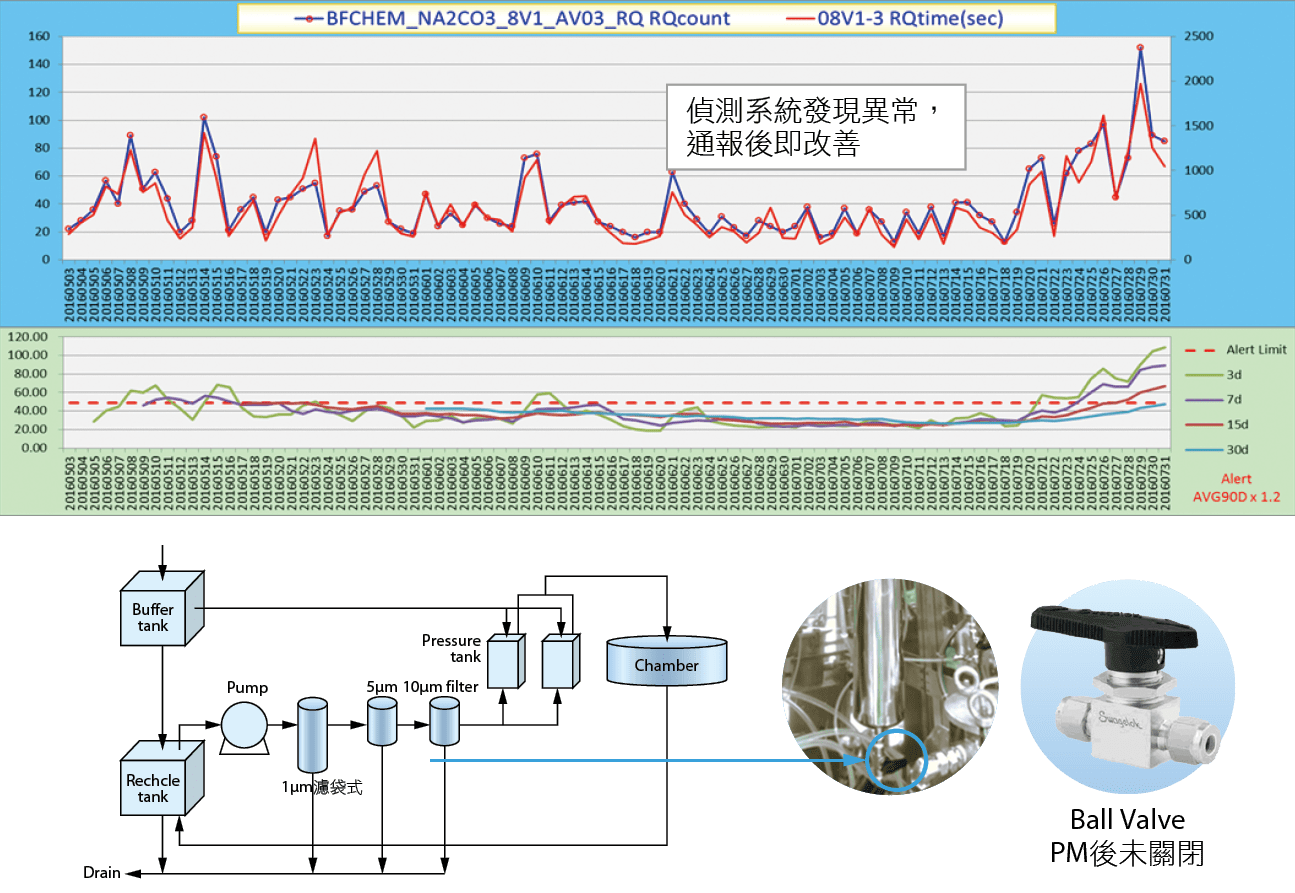
實際案例二
Stripper設備機台使用化學品IPA,控制IPA要酸訊號電磁閥異常,造成高頻率短暫要酸現象,如 圖12,此現象會導致廠務系統閥件開關次數增加,進而影響閥件壽命。若以往一般的Request Time Out功能也無法抓到此異常,甚至到廠務機台閥件也異常時才發現問題,透過此系統要酸次數自動比對功能快速發現異常,立即要求設備更換零件改善,避免問題的擴大。
圖12、實際案例二,設備電磁閥異常導致高頻率要酸
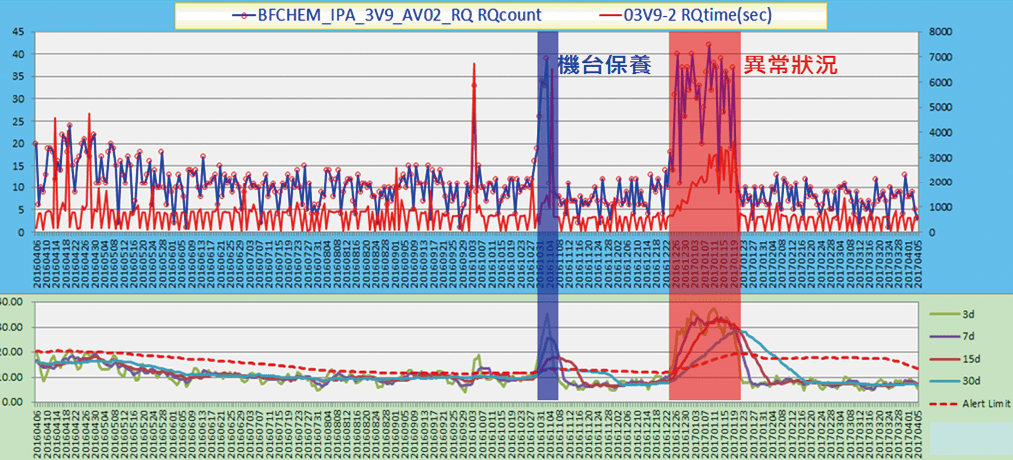
如以上所述,化學品用量異常即時偵測系統可以實際發現異常狀況,鑒於該系統具備自動化分析能力,降低人員操作工作量與讓Module人員可更加方便查詢操作,如 圖13,以往需一天後經人工匯出資料計算後才能發現的問題,改善為每天每小時自動分析比對,不僅更完善防禦偵測異常用量,同時也大幅降低發現問題時間。
圖13、異常用量應變時間比較圖
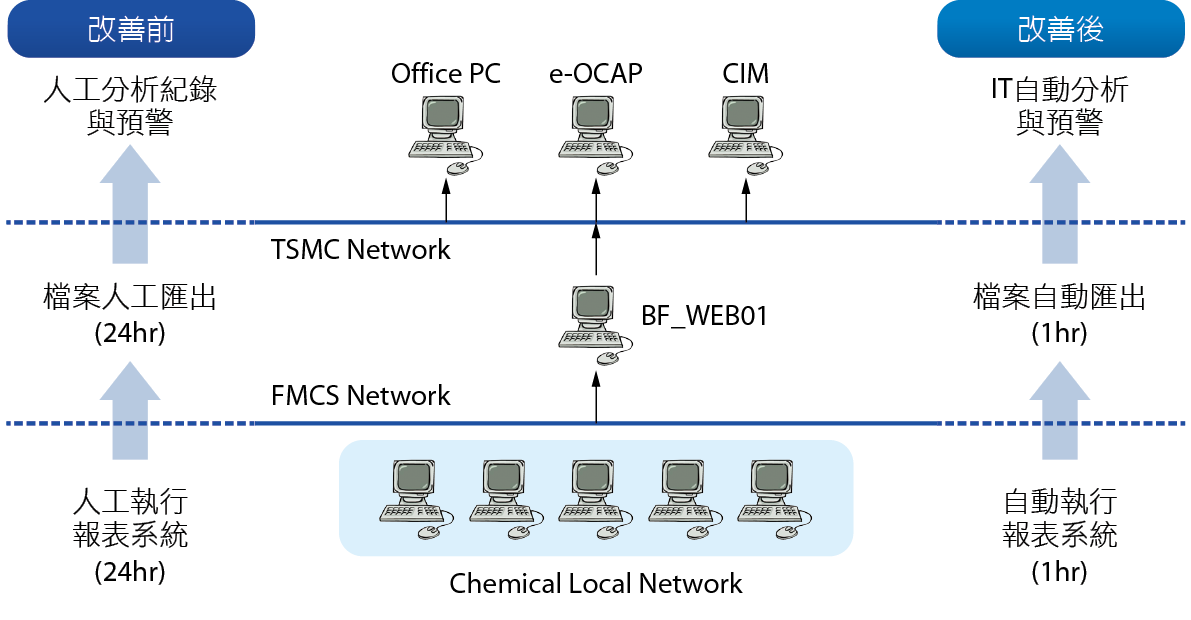
結論
化學品用量自動防禦系統與供應用量報表已於2016年第一季上線使用,經實例證實可有效反應產線端化學品用量異常現象,符合達到能即時偵測化學品異常用量的自動化系統目標。比較修改前後化學品偵測異常系統功能,如 表2所示,可改善以往無法藉由換酸桶數與要酸秒數(Request Time)偵測到的異常,並大幅降低應變時間與人力。
廠務系統 |
防禦機制 |
手法 |
是否能偵測線上機台異常 |
自動警報功能 |
影響線上機台 |
反應時間(hr) |
人力需求(manhour) |
Remark |
|
---|---|---|---|---|---|---|---|---|---|
單次大量要酸 |
多次小量要酸 |
||||||||
中央供酸系統 |
機台要酸訊號監控 |
限定單筆要酸訊號時間(Request Time Out) |
V |
|
V |
V |
<1 |
0 |
既有功能 |
每日要酸桶數統計 |
人工統計 |
V |
V |
|
|
24 |
1 |
||
總時間偵測 |
統計總要酸秒數平均值取3倍Sigma |
V |
V |
V |
|
1 |
0 |
新增功能 |
|
總次數偵測 |
統計總要酸次數平均值×安全係數 |
V |
V |
V |
|
1 |
0 |
新增功能 |
該系統迄今於封裝廠區(BP2)使用,未來期望能廣泛應用於各廠區,即使各廠區供應系統廠牌與訊號控制方式不盡相同,但依此化學品用量自動防禦系統判斷邏輯觀念,也可達成相同之功效,讓所有運轉單位每日更清楚掌握廠區即時供應狀況,避免異常排放造成原物料成本增加,達到更為快速、有效地發現異常用量,進一步提升本公司對於化學品用量防護機制。
留言(0)