摘要
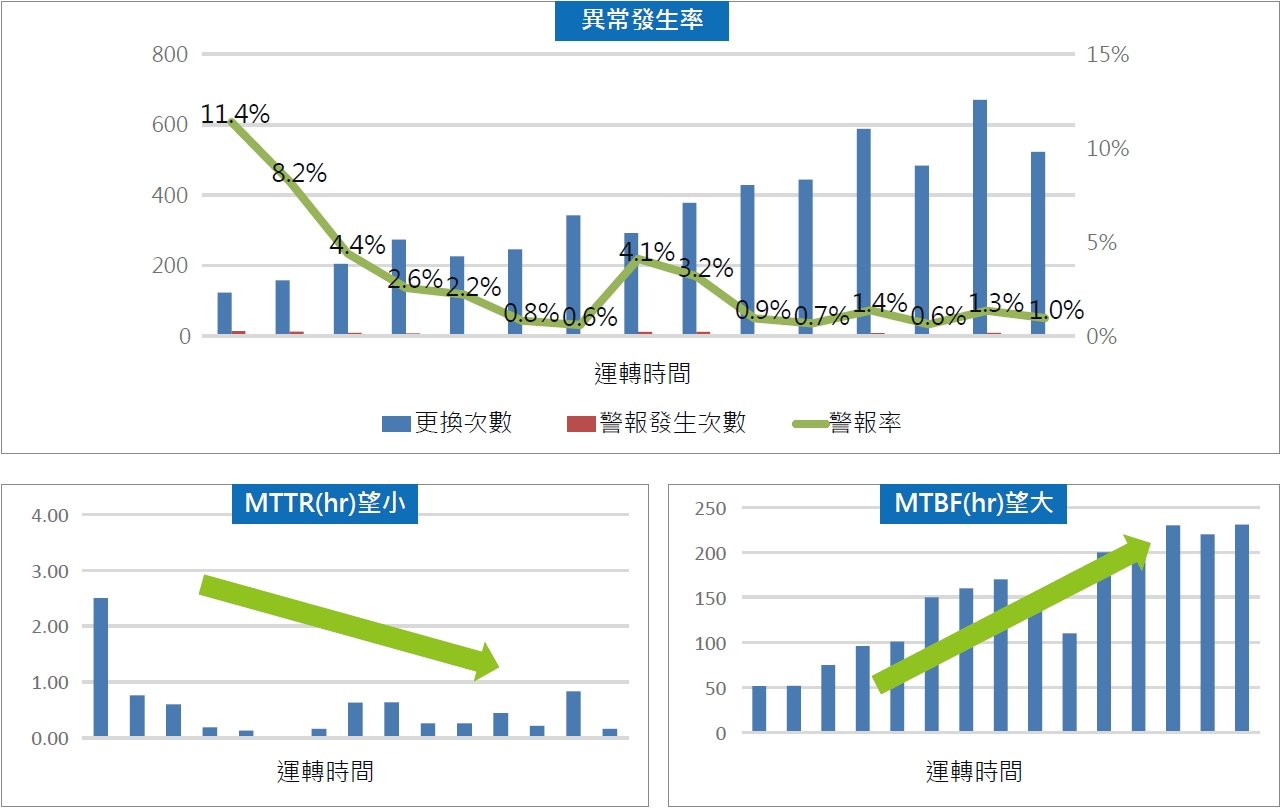
化學品自動化倉儲與高速物流系統建造與運轉實務
目前新廠設計開始採用自動化倉儲(Automated Storage/Retrieval System, ASRS),與桶裝化學品供應單元(Drum Unit, DRU)連結,設計出桶裝化學品高速物流系統(Drum Hyper Logistics, DHL),讓原物料從碼頭下貨到儲區,儲區到上機 ,過程全部用自動化機械取代人力搬運,達到全自動一條龍上機,完成桶裝化學品自動倉儲暨供應系統。此篇將從此系統建造、運轉來分享實務經驗。
前言
德國發起的「工業4.0」(Industry 4.0)概念[1],在全球逐漸發燒。不過,製造相關業者、半導體元件或是系統整合商,即使明瞭工業4.0將為其帶來新的龐大商機,卻礙於入門門檻高,導入工業4.0的想法始終還在原地踏步。
近十年來,倉儲物流發展方向,由人工轉為自動化科技,尤其台灣土地價格昂貴取得不易,建置高效率的倉儲管理系統,減少庫存成本同時提供更快的搬運速度,是企業界爭相投入改善的目標。自動倉儲系統(Automated Storage/Retrieval system, ASRS)在這個時空背景下逐漸往多功能延伸與整合的道路邁進。
自動倉儲是運用存取裝置及周邊設備、電腦和控制器等設備,以達到快速且準確地執行各項倉儲作業,如:儲存、提取、控制和紀錄。自動倉儲系統發展至今已日趨成熟,國內各企業也逐步引進此系統,以減少儲存成本、人工的浪費。自動倉儲可提供及時、便捷的倉儲管理作業,主要的優點是:①改善儲存空間利用率 ②節省直接與間接人工成本 ③精確的控制存貨 ④減少貨品的損壞與失竊 ⑤ 增進操作安全性。
半導體產業導入無塵室晶圓自動傳輸已十餘年,不斷演進至今,已達成真正的無人化自動生產,工作效率大幅提升。然而廠務端供應生產用化學品的庫房,卻還停留在傳統倉儲以人力傳輸。審視目前化學品庫房無法順利轉型成自動倉儲的原因如下:
- 生產機台無法長時間中斷供酸
- 無足夠閒置空間
- 既有運轉廠區無法承受新機運轉不穩定風險 :
- 升級成自動傳輸過程中有傾倒風險。
- 過去無運轉經驗,試車初期可能傳輸異常率太高或所需復原時間太長,造成供應中斷。
- 操作人員不熟悉新系統,更換原物料過程可能造成供應中斷。
面對製程技術的提升,原物料種類與數量都與日攀升,到了N7世代每天需要更換高達200桶之桶裝化學品,傳統倉儲轉型為自動化系統勢在必行。所以,台積廠務設計部團隊在15P7建廠階段就將ASRS加入規劃,並與台積自動化部門和廠務使用端共同開發出新型態,可搭配自動倉儲系統的桶裝化學品高速物流系統(Drum Hyper Logistics, DHL),概念是讓自動倉儲系統內的桶裝化學品直接進入使用端,過程不需人力搬運,達到物流全自動一條龍上機。本文目的就是分享ASRS+DHL建造、安裝、試車、運轉實務經驗。
文獻探討
從20世紀80年代末到90年代初,除了製造業以外,農業、批發零售業、倉儲業、銀行、保險和公共機構也開始採用自動倉儲。例如,在農業領域自動倉庫可作為糙米保存庫、水果冷藏設備、裝運前蔬菜預冷設備、蘑菇養殖設備,以及蔬果分選的分類運輸設備。
在20世紀90年代後半期,自動倉庫系統開始投入到更接近終端消費者的物流階段,包括倉儲業和批發零售業,在物流配送中心就可以做到供應鏈管理。這些配送中心除了棧板式自動倉儲之外,還配置了可以處理各種形狀和大小的貨物的箱式自動倉庫,作為出貨以及揀貨作業前的理貨設備。
2.1自動化倉儲的優越性[2]
早期自動倉儲的構想,其基本出發點就是提高空間利用率,充分節約有限且寶貴的土地。在已發達國家,提高空間利用率的觀點已有更廣泛深刻的含義,把節約土地、節約能源、環境保護等方面聯繫起來;有些指標系統甚至把空間的利用率作為系統合理性和先進性考核的重要指標 。一般來說,自動化高架倉儲(ASRS)其空間利用率為普通倉儲的2-5倍,對於形成先進的物流系統,提高企業生產管理水平有相當幫助。
傳統倉儲的唯一功能是保存貨物,屬於「靜態儲存」 。自動化倉儲採用自動化物料搬運設備,不僅能使貨物在倉儲內按需要自動存取,更可以與倉儲以外的生產環節進行連接,通過電腦管理系統和自動化物料搬運設備使倉儲成為企業生產物流中的一個重要環節,從而形成一個自動化的物流系統。這是一種「動態儲存」,也是當今自動化倉儲發展的一個明顯的技術趨勢,如 表1。
對比 | 自動倉儲 | 傳統倉儲 |
---|---|---|
空間利用率 | 充分利用倉庫垂直空間 | 需佔大面積土地,空間利用率低 |
儲存量 | 節約70%土地 | 單層倉庫 |
儲存型態 | 動態儲存 : 貨物在倉庫能 按需求自動存取 | 靜態儲存 : 保存貨物 |
作業效率 | 自動存取,效率高 | 主要靠人力,存取貨物速度慢 |
人工成本 | 可節約80%勞動力成本 | 人工成本高 |
環境要求 | 能適應黑暗低溫特殊環境 | 受環境影響大 |
2.2自動化倉儲系統種類
自動倉儲的種類大致分4類,依照其儲存貨物的類型/數量/需求區分應用的技術大致可分為 : ①Unit Load ASRS ②Mini-load ASRS ③Man-on-board ASRS ④Deep-lane ASRS。
2.2.1 單位負載式Unit Load ASRS
每次存取一儲存盤(棧板,Pallet)之物料使用範圍最廣 ,建造成本。控制器位於走道末端方便操作人員管理貨物而不需要進入設備內部。高度可達40m以上,儲位量設計可達10萬餘個棧板,適用大型的倉庫,如 圖1。一般使用最普遍的高度以6~15m為主,儲位100~1,000個左右。自動倉儲製造商多以此高度(6~15m),將自動倉儲的料架及存取機(tacker Crane)標準化,並配合各種不同規格的棧板(800~1,500mm)及負載的高度進行設計。由於標準化及規格化,使施工的工期較短,且成本降低。而隨著電控技術的不斷進步,存取時間愈來愈快,以100個棧板存取為例,平均存取時間為70秒/棧板。存取機依控制自動化的程度,可分為手動、半自動及全自動。除控制系統外主要由操控 、走行、捲揚、存取四大裝置組成,此類型也是我們使用的類型ASRS適用於半導體廠運轉模式。特性:
① 物流與資訊流同步,料帳正確。
② 出庫條件可以精確控制。
③ 高架吊車立體運搬,可配合多樓層廠房。
④ 高架貨架儲存,儲存密度高,貨物不受壓傷碰損。
⑤ 庫區無人進入,防火及安全性高。
⑥ 包裝堆棧需尺寸標準化,整齊穩固。
圖1、Unit Load ASR
出處:https://www.cisco-eagle.com/material-handling-systems/asrs-systems/unit_load
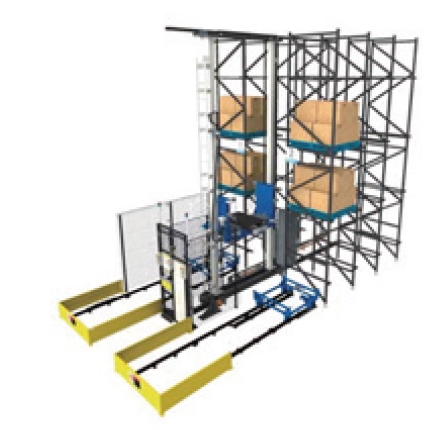
2.2.2 輕負載式自動倉儲Mini-load ASRS
以塑料籃/紙箱為存取單位,重量在50~100kg 。一般以重量輕之小對象的儲存最適合,如電子零件、精密機器零件、汽車零件、藥品及化妝品等輕負載式自動倉儲,高度在5~10m使用最普遍,此類型旨在滿足存儲和處理放置大小不均(從紙箱或塑料盒到托盤)的容器需求,如 圖2。所使用的自動存儲和檢索系統具有高服務速度的特點,旨在確保減少揀選時間和高度動態功能。這類系統會配備取料工具,根據負載單元的特性和搬運要求而自行調整。這種類型的自動倉儲方案特別適用於提升裝配線速度或運輸部門。
圖2、Mini-load ASRS
出處:https://www.ferrettogroup.com/index.cfm/en/solutions/asrs/miniload-asrs/
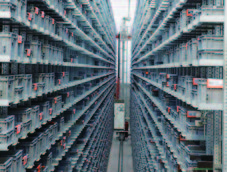
2.2.3 人員登入式Man-on-board ASRS
作業員搭配自動化機具進行庫存優化,自動化程度較低,如 圖3。
圖3、Man-on-board ASRS
出處:https://www.jungheinrich.co.uk/products/new-forklifts/very-narrow-aisle-truck
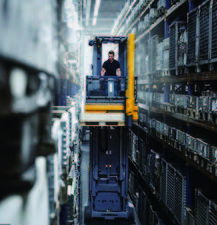
2.2.4 深道式Deep-lane ASRS
深道式自動倉儲是所有自動倉儲系統中空間儲存密度最高者,貨品的儲存流動是設定鋼架的傾斜高度差,靠儲存貨品本身的重量自動流送,並在高密度鋼架的前後端設置自動存取機。此類型的自動倉儲適合種類少數量多的貨品儲存,尤其適合先進先出的作業,惟不容易從流道中段取出貨品,如 圖4。
圖4、Deep-lane ASRS
出處:https://www.abelwomack.com/deep-lane-high-density-pallet-storage/
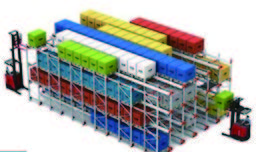
2.3智慧倉儲[3]
智慧倉儲是指在自動倉儲管理基礎上,利用RFID射頻識別、網路通信、信息系統應用等信息化技術及先進的管理方法,實現入庫、出庫、盤庫、移庫管理的信息自動抓取、自動識別、自動預警及智能管理功能,以降低倉儲成本、提高倉儲效率、提升倉儲智慧管理能力。
其中,倉儲信息自動抓取功能是指對貼有電子標簽(例如條碼或RFID) 的貨物、庫位、庫架信息自動抓取,包括貨物屬性、庫位及庫架分類等,無須通過人工一一辨認。倉儲信息自動識別功能是通過與後臺伺服器的聯接,在自動抓取信息基礎上,實現信息自動識別,快速驗證出入庫貨物信息、庫內貨物正確堆放信息等。自動預警功能是通過信息系統程式設定,對問題貨物進行判斷發出告警,讓管理者提前應對。智能管理功能則能將資料庫內的大數據自動合成各類單據,輔助管理供應鏈決策。
計畫方法
在前言與文獻中,吾人構思最適合半導體化學倉儲的系統是單位負載式Unit Load ASRS,加上設計專用的銜接桶裝化學品供應單元DRU,形成了桶裝化學品高速物流系統DHL的全新物流架構,本章節將詳細說明ASRS+DHL建造與運轉的過程。
3.1建造
ASRS建造分成安裝和測試,敘述對未來運轉影響的幾個重點。
3.1.1 安裝
① RGV與DHL馬達傳輸速率需匹配 : RGA功能為載運貨物至目的地,其移動精度可達+/-5mm,負責ASRS←→DRU傳輸,安裝時需特別注意RGV&DHL馬達傳輸速率, RGV滾輪傳送速度初版設計為12m/min,而DRU滾輪傳送速度設計為5m/min,在試車階段發現傳輸速度差會產生打滑現象,長期不均勻施力也可能造成DRU馬達受損,為免傳送過程速度差導致貨物傾倒,決議更換RGV馬達,將其滾輪傳送速度為降為5m/min與DHL傳輸速率匹配避免未來運轉異常。
② RGV與DHL需增加free roller降低滾輪距離<30cm : DRU與RGV距離35cm,經實驗證實,當棧板上化學桶兩滿兩空的極限狀態,如 圖5,此重量不平均必定發生旋轉傾倒現象,於是在DRU與RGV中間增設無動力滾輪free roller ,將距離減少至距離23cm,小於單桶質量中心30cm。
圖5、Free roller安裝位置&棧板重心
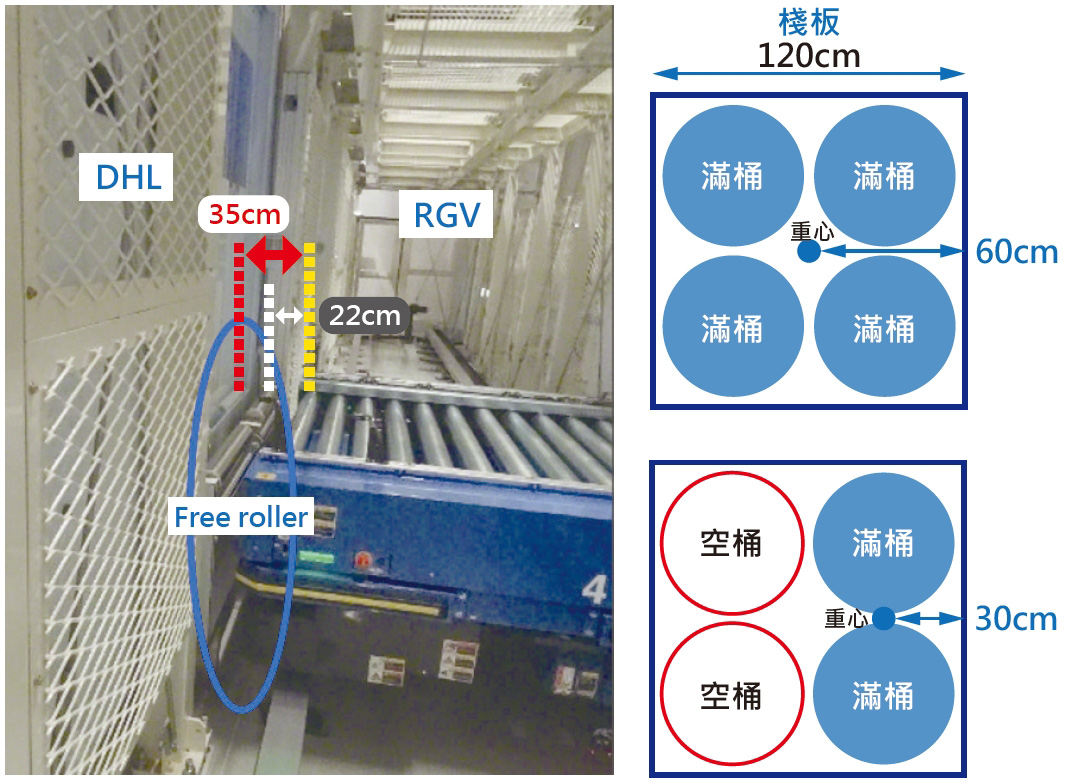
③ 安裝對照式sensor避免異物侵入問題 : ASRS原設計透過圍籬作區隔,非實體牆無法完全杜絕人員進入或是物品掉落在機台行走路徑的可能性,審視安全性後在所有輸送機(RGV/Crane)路徑加裝對照式sensor,如 圖6,一旦感應到物體即刻停下輸送機動力源。
圖6、對照式sensor安裝位置剖面圖
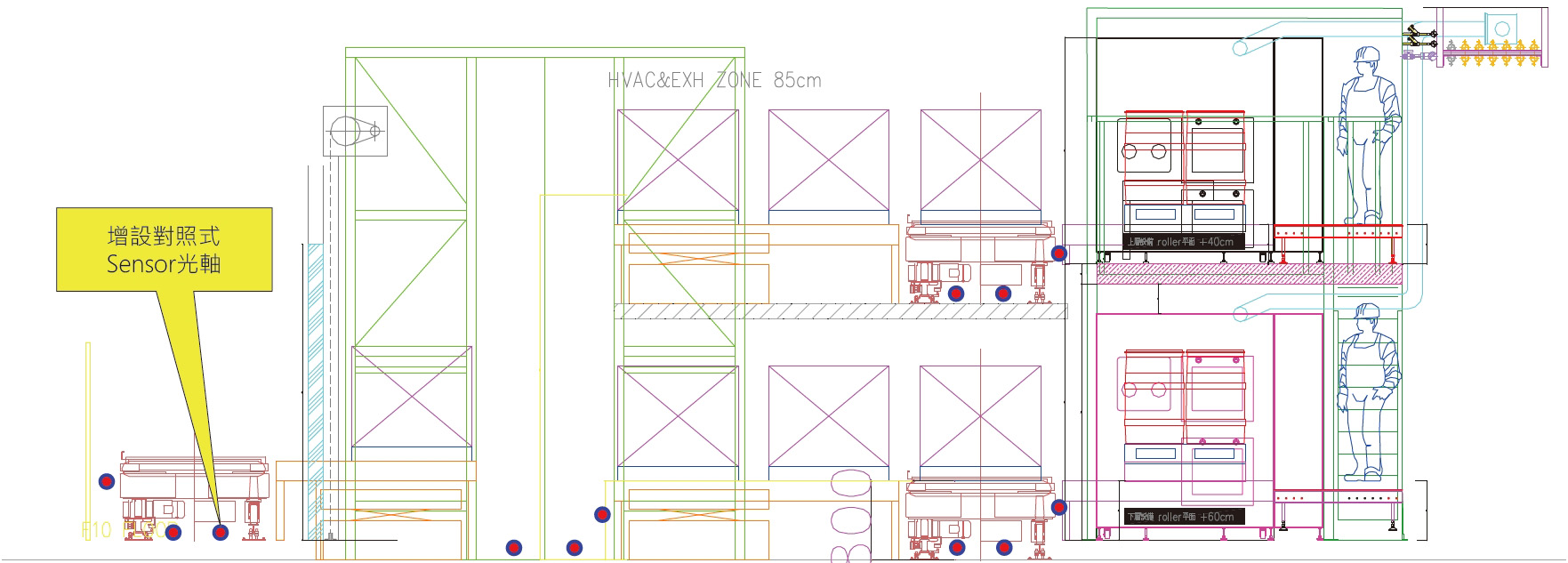
④ 漏液檢知功能 : ASRS初始並無設計漏液檢知機能,但不同於傳統倉儲系統,內部平日並無人員進入巡檢,若發生化學品洩漏將無法第一時間感知,故將ASRS所有區域以帶狀式漏液檢知器圈圍,作為極早期偵測手段,如 圖7為其分布範圍。
圖7、帶狀式漏液檢知器分布圖
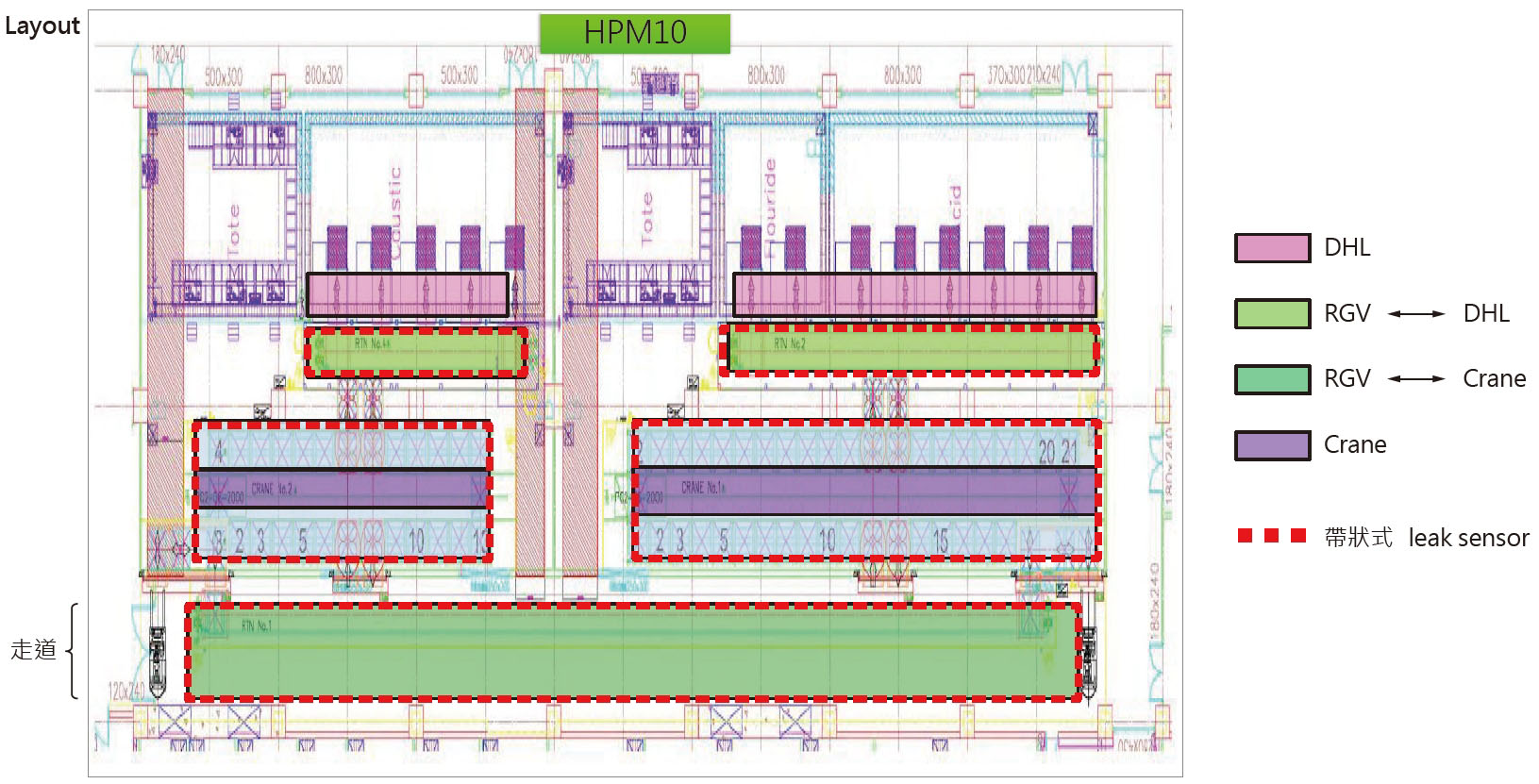
⑤ 入料口(manual port)安裝自動門 : 貨品入料口(manual port) 原設計為求便利性採取開放式,未設置防堵人員或異物侵入的圍籬,為避免人員受機具捲入的危害,檢討後新增自動門,如 圖8與ASRS傳送指令連動,並新增以下警報偵測系統異常。
- 門開啟/關閉命令→tsmc門禁系統刷卡
- 門開啟中→Manual port無法執行入出庫
- 門開啟過久→idle>10min系統發出異常警報
圖8、manual port自動門現場照
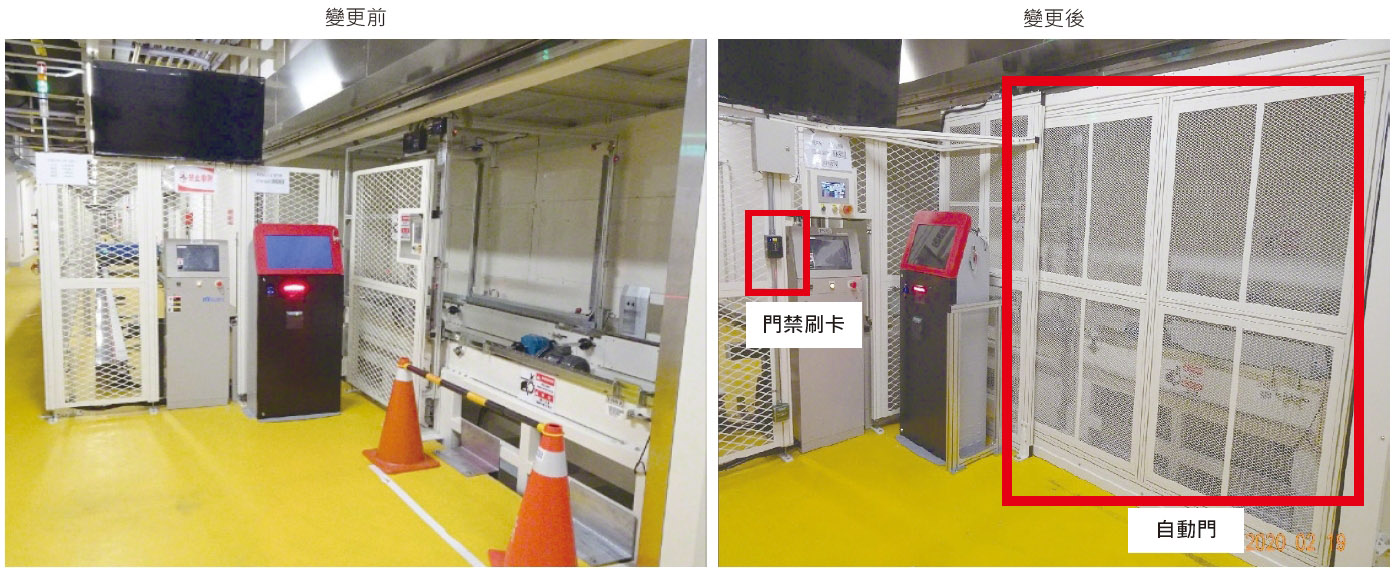
3.1.2 試車
ASRS+DHL各單元安裝完成後,最終還需進行72hrs連續運轉測試(俗稱燒機測試),測試須包含所有ASRS運送路徑,共5條如 圖9,其目的為確保各單元距離感測誤差皆已調整精確,測試過程需同時考慮真實性及安全性,實桶內注滿純水取代化學品,避免測試過程異常洩漏導致系統損壞。測試結果共計完成了1,422次傳送,在檢視所有紀錄後確認沒有重大異常,才算完成運轉前試車,72hrs連續運轉測試其重點如下 :
- 棧板種類越多越好,避免運轉後sensor些微誤差造成系統停止
- 過程中需連續運轉中間若有任何異常需重新開始
- 測試時所有運轉路徑
圖9、72小時運轉測試路徑模擬圖
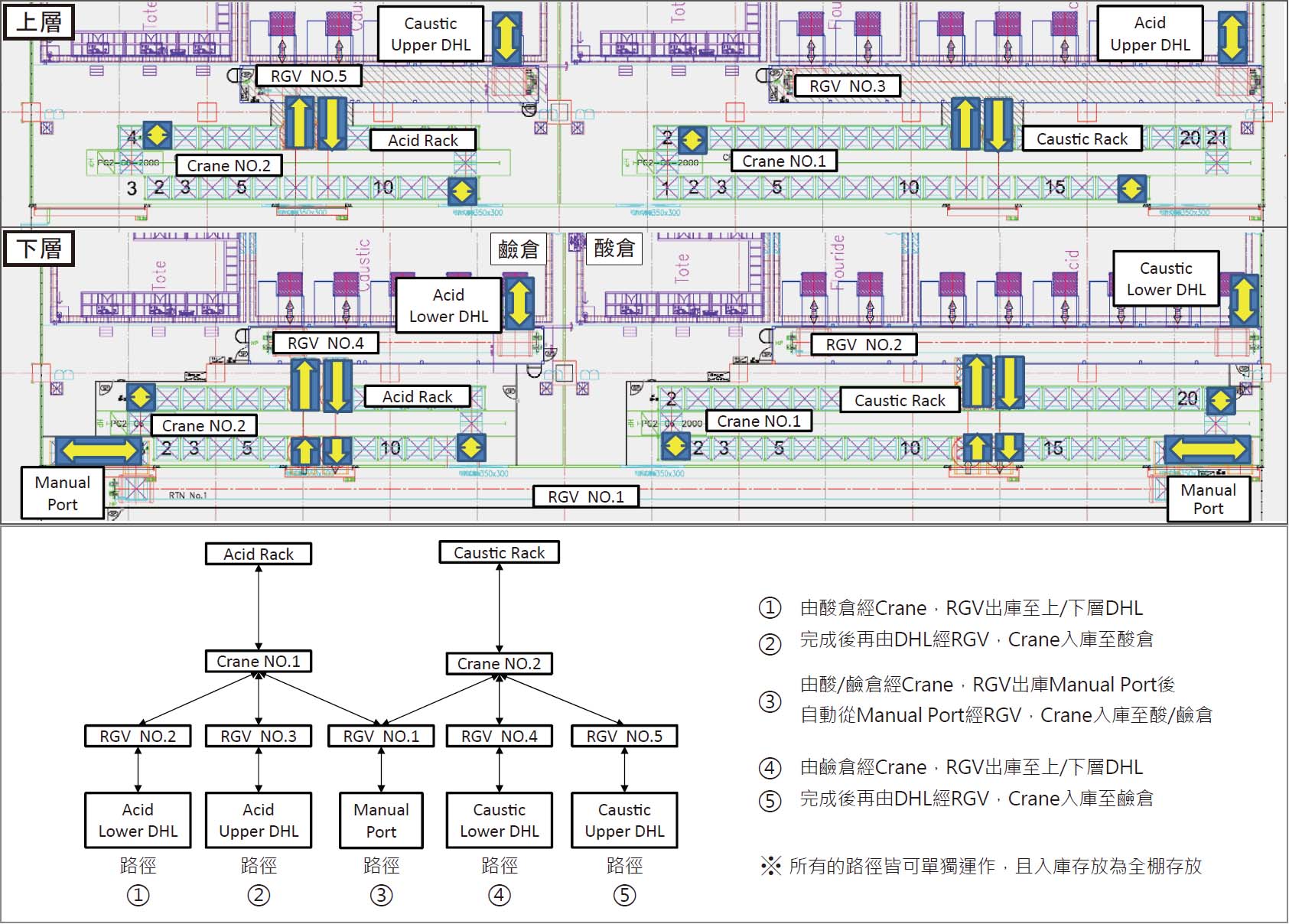
3.2運轉
系統正式開始投入化學品裝載運轉,陸續發現6大問題,與設計部及承商共同完成改善。
3.2.1 運轉資訊不足
運轉初期即發現運轉資訊不足,只有紀錄crane的傳輸資訊如 圖10,諸如RGV、Load cell、到站時間等等紀錄不足,也無法從報表得知運轉表現。為此我們將ASRS資料彙整上傳至台積內部資料處理系統,再將資料轉換成ASRS+DHL operation index,如 圖11,利用以下3個KPI指標來了解運轉健康狀況。
- 異常警報率 : 異常次數/傳送次數,來了解系統健康度
- MTTR(Mean Time To Repair平均修復時間) : 從出現故障到恢復中間的這段時間,MTTR越短表示嚴重失效行為越少
- MTBF(Mean Time Between Failure平均失效間隔) : 規定的工作環境條件下,開始工作到出現第一個故障的時間的平均值。MTBF越長,表示可靠性越高
圖10、ASRS初版KPI
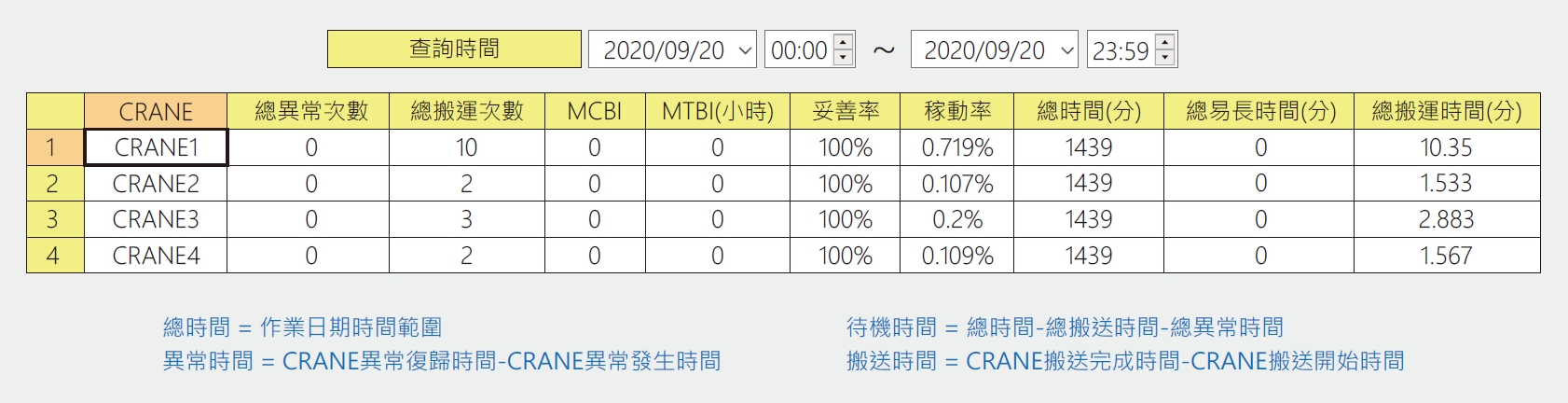
圖11、ASRS+DHL operation index
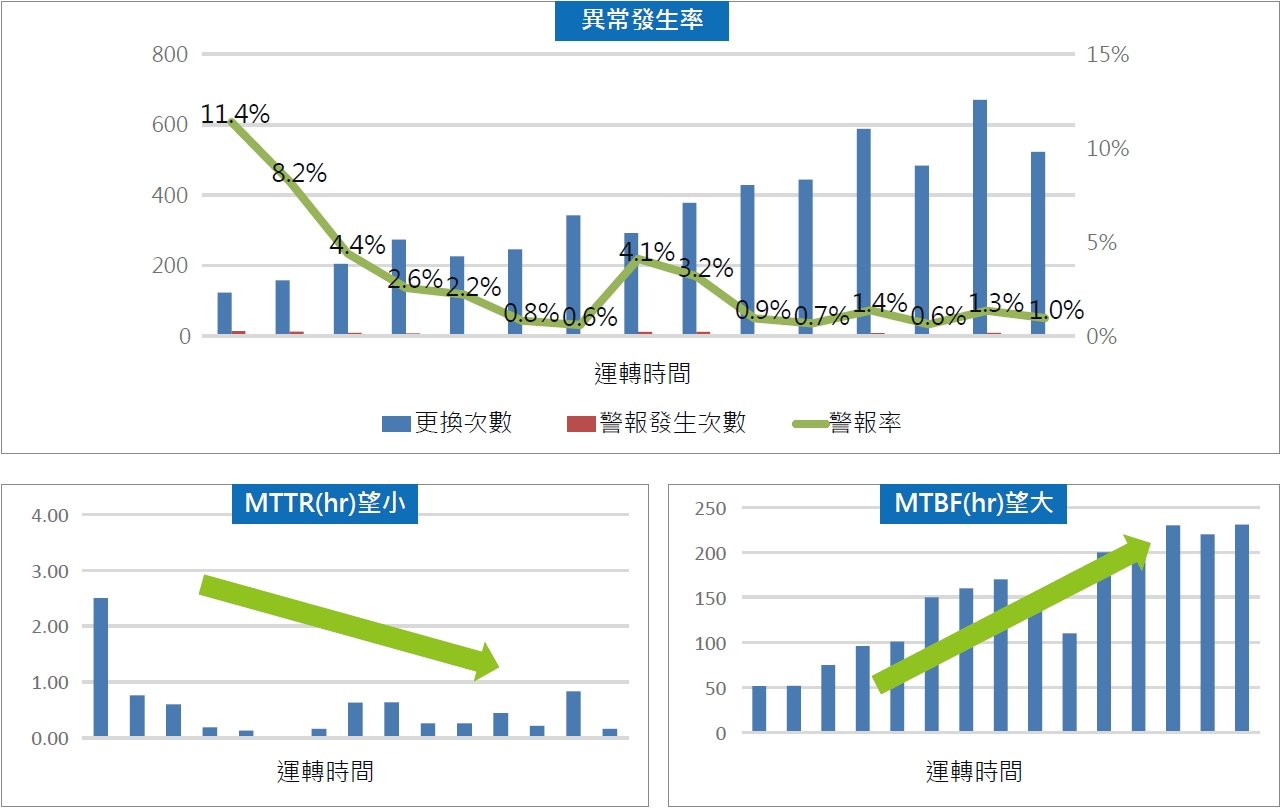
3.2.2 定位sensor調整
運轉初期由於各廠商棧板&drum桶雖已制定統一規格 ,但仍有些微差距,時常因sensor位置不佳而使ASRS系統停止,如 圖12,經過各家廠商棧板測試調整後才找出最佳位置。未來新廠建置時,可提前在72hrs測試時增加不同類型棧板組數,加速完成最佳化調整。
圖12、ASRS異常 : 定位sensor位置不佳
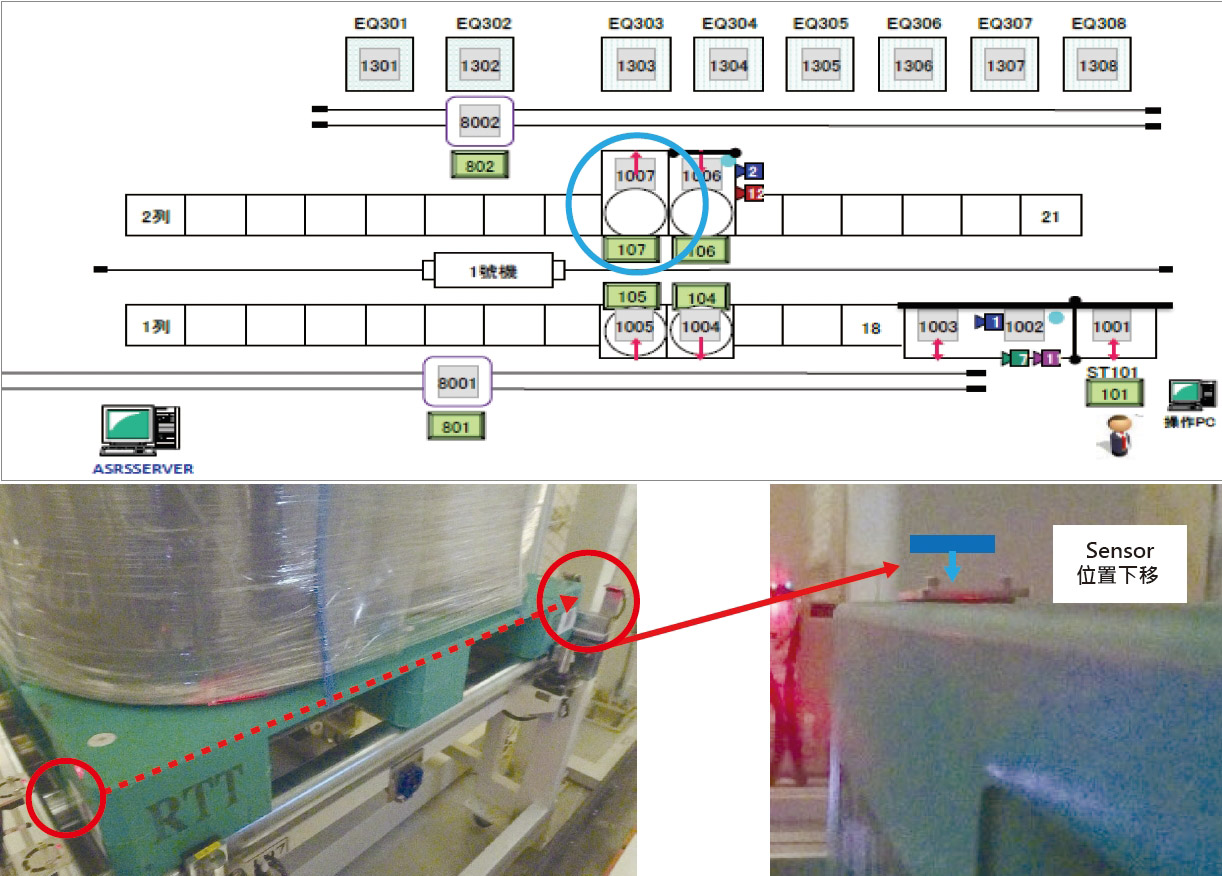
3.2.3 定位sensor誤作動
桶裝化學品為避免在運送過程中或放置太久導致灰塵積在桶身,在桶身會在包覆膠膜保護,但膠膜在ASRS傳輸過程中容易造成定位sensor紅外光散射,致使sensor接收錯誤導致系統停機。解決方法是在定位sensor上增加集光罩如 圖13避免光線散射,集中效果佳,裝設後未再發生。後續已將集光罩定為建廠標準,避免未來新廠區再發。
圖13、ASRS異常:定位sensor誤作動造成
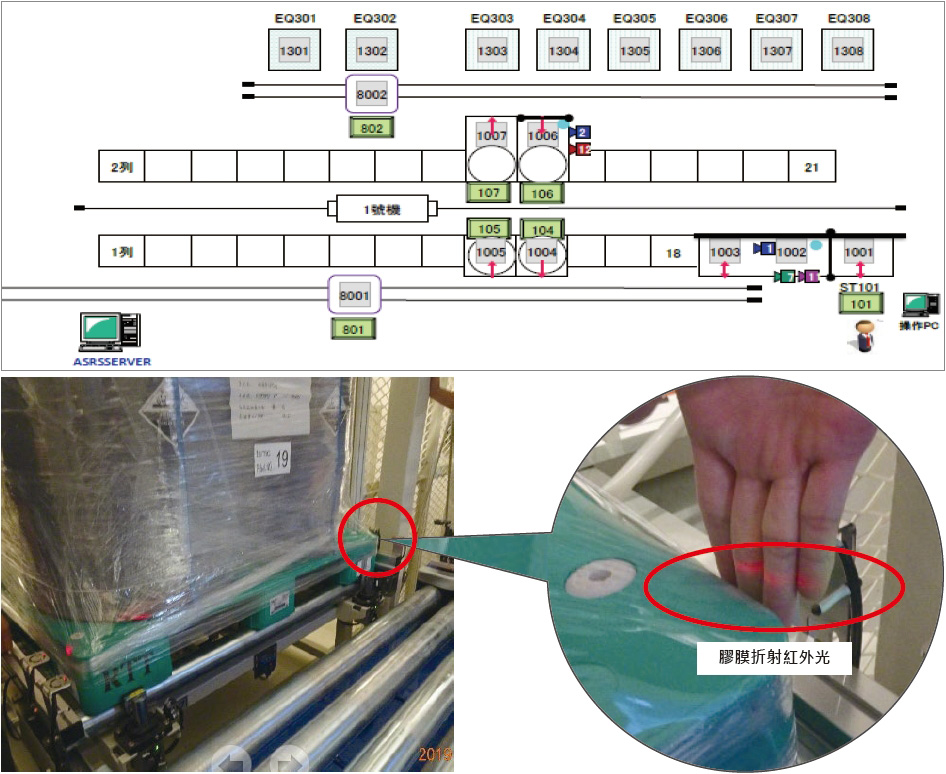
3.2.4 DRU棧板傳送卡板
DRU傳送滾輪有左右兩側,但只有單邊有動力傳送(power roller),另一側是無動力滾輪(free roller),棧板傳送過程若因棧板老舊底部不平,很容易使傳送時力矩偏移 ,導致棧板旋轉卡板停機,如 圖14。為此我們將滾輪由單邊動力改成雙邊動力,兩邊同步運行大幅減少棧板旋轉問題。此雙動力滾輪設計也已定義為新廠標準規格。
圖14、DHL動力滾輪
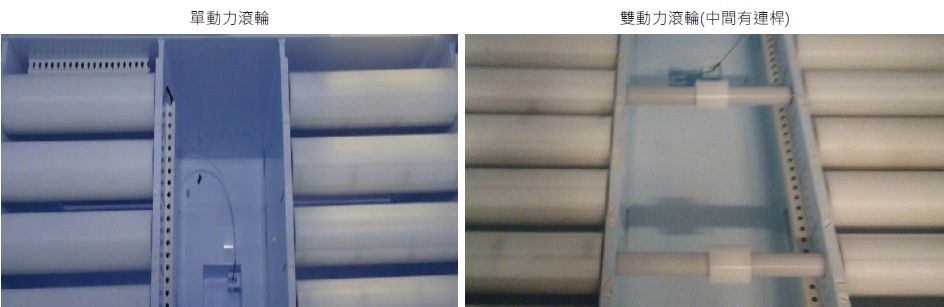
3.2.5 DRU棧板傳送卡板
棧板膠膜在傳輸過程中,偶有膠膜絮會因為移動飄起 ,若飄起時機剛好經過sensor,會造成誤作動,如 圖15。後續即使膠膜絮已經離開遮蔽點,但系統仍需要操作人員至現場確認並復歸才能繼續運轉。為避免此問題,吾人檢討了合適的sensor判斷延時,以杜絕干擾現象。
圖15、ASRS異常 : 膠膜絮造成sensor誤作動
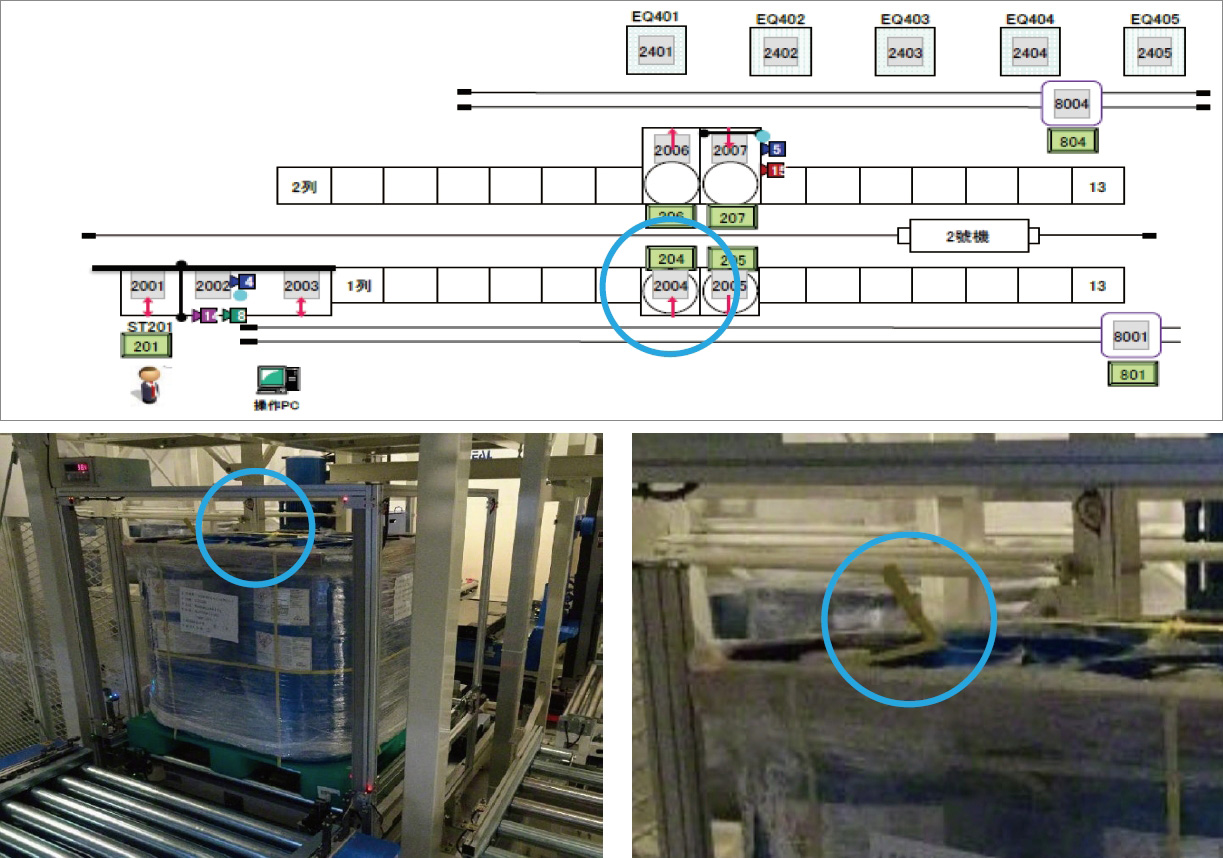
3.2.6 ASRS系統online狀態下異常無警報
ASRS系統狀態可分3種:①手動→由人員手動操作 ② 自動→系統全自動 ③online→人員介入處理中,需人為下指令,無法全自動運轉。初期人員維護系統時復歸時皆未切至正確之自動狀態,故與廠商討論將online狀態改成異常狀態,並發出警報,以提醒管理者系統已進入異常處理模式。
結果與分析
ASRS+DHL系統運轉啟用至今。透過分析DHL運轉 KPI,找出關鍵警報,如 表2,並逐一克服改善前6大問題 ,有效的將異常發生率從運轉初期的11.4%降至1%,MTTR 從2.5降至0.21hrs/次,MTBF也從51提升至224hrs,有效提升了系統可靠度。
項目 | 異常 | 原因 | 改善 | 異常數量 | 異常分類 |
---|---|---|---|---|---|
1 | crane無法運轉 | 棧板超出定位sensor | ASRS調整sensor位置 | 11 | 硬體 : ASRS |
2 | 旋轉台無法運轉 | 膠膜散射紅外光造成sensor誤偵測 | 加裝集光罩避免sensor干擾 | 9 | |
3 | DHL無法傳輸 | 棧板旋轉卡板 | DHL傳輸改雙動力滾輪 | 15 | 硬體 : DHL |
4 | RGV緊急停止 | 膠膜未包裝完全觸發sensor | sensor判斷增加delay time | 3 | 軟體 |
5 | ASRS無法運轉 | 運轉單元未切回自動 | 增加系統未切回自動提醒警報 | 3 | |
6 | RTN無法運轉 | 傳輸訊號延遲 | 訊號傳送邏輯de bug | 7 |
此外,透過大數據分析,也能看出自動倉儲對於桶裝化學品進料到退桶所節省的工時,如 表3,自動倉儲不僅大幅節省了庫房操作員入庫/出庫/領料的動作,從ASRS直接將桶裝化學品傳輸進入DRU的工作,也讓棧板工作時間從原本60分鐘大幅降低至只需要花費20分鐘,整體傳輸時間節省了67%。
傳統倉儲傳輸時間(分鐘) | 自動倉儲傳輸時間(分鐘) | ||||
---|---|---|---|---|---|
實桶入庫 | 10 | 5 | ASRS 實桶入庫 | ||
實桶出庫使用 | 庫房出庫 | 5 | NA | ASRS庫房自動出庫 | ASRS實桶出庫使用 |
廠務領料 | 5 | NA | ASRS 自動領料 | ||
廠務上機 | 20 | 5 | ASRS 自動上機到DHL | ||
空桶入庫待退 | 廠務出庫 | 5 | NA | 廠務出庫 | ASRS自動退空桶入庫 |
庫房入庫 | 5 | 5 | 庫房入庫 | ||
空桶繳出 | 10 | 5 | 空桶繳出 | ||
總計花費時間 | 60 | 20 | 總計花費時間 |
結論
經過一年多的努力,廠務終於建構出ASRS+DHL化學品物流新標準。廠務在最先進的N5/N7新廠區藉由收集安裝/試車/運轉,各個階段的使用者經驗,得出許多寶貴的智慧結晶。整理如下:
① 系統安裝:
- 與DHL傳輸的RGV馬達傳送速度改為5m/min
- DHL與RGV距離增加free roller使距離小於30cm
- 對照式sensor安裝
- 帶狀式leak sensor
- manual port自動門安裝
② 試車階段 : 增加測試棧板種類與數量,及早發現運轉問題,及早調整。
③ 運轉階段 : 共有6項改善,皆已列入標準設計。
- 運轉資訊不足 : 建立運轉KPI
- 定位sensor調整→提早於試車階段驗證
- 定位sensor誤作動→增加集光罩
- DRU棧板傳送卡板→DRU改雙動力滾輪
- 棧板膠膜干擾→增設異常警報延時
- ASRS系統online狀態下異常無警報→增設異常警報 ,提醒管理者已進入半自動操作
15P7成功導入了ASRS+DHL模式,改變了半導體廠化學品物流運作邏輯,大幅減少了人力輸送所需的時間。目前各式酸、鹼類化學品已經完全導入此系統,惟有機化學品(solvent) 礙於系統防爆設計規畫及法規檢討尚未完成,仍需人力搬運上機。未來展望繼續開發防爆型ASRS,期望有朝一日有機化學品也能達成全自動化倉儲。本專案歸功於廠區的即時回饋和設計部的快速反應,讓問題迎刃而解 ,也讓新廠區來得及站在巨人的肩膀上,避免重蹈覆轍。期許這些經驗傳承,能讓既有廠區降低轉型所需面對的未知風險,建立信心開始發展新世代的桶裝化學品高速物流系統。
參考文獻
- 呂明山(2018)。工業4.0時代來臨∶機械工業4.0。科技大觀園 。2018年10月1日,取自https://scitechvista.nat.gov.tw/c/sgTm.htm
- 自動化立體倉儲的優越性-MBA智库百科,http://wiki.mbalib.com/zh-tw/自動化立體倉儲的優越性。
- 智慧物流與倉儲專輯-RFID讓倉儲系統全面透明化,DIGITIMES企劃2013。
留言(0)