摘要
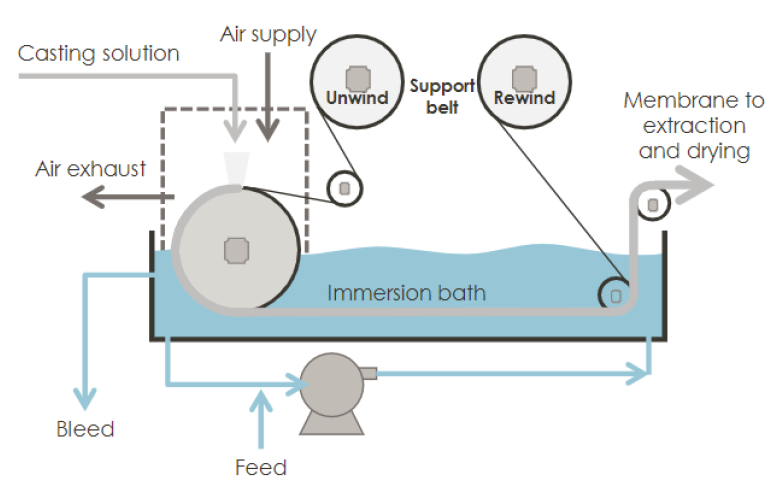
化學系統濾心污染防治
隨先進製程技術不斷推進,化學供應品質也面臨挑戰,偵測品質標準中的金屬含量及含不純物成為製程關鍵。既往影響產線供應品質汙染源,以原物料及耗材供應商製造與包裝品質異常之案例為甚,又以定時保養更換系統耗材或配件影響風險較高。本文以經常性更換之濾心(Filter)借鏡,階段性探討 : ①濾心更換後品質管控(Quality Control)之標準;②新式監控更換濾心品質方法及手法;③評估未來新式高潔淨、低汙染濾心,以提升濾心供應之品質穩定度與可靠度,達到降低濾心更換污染防治之目標。
With the advanced process technology, the quality of chemical supply is also facing challenges. The detection of metal content and impurities in quality standards has become the key to the process.The source of quality pollution in the supply line is the case of abnormal manufacturing and packaging quality of raw material and consumables suppliers, and the impact of regular maintenance and replacement of system consumables or accessories is relatively high.This article takes the filter of the frequently replaced filter as sample, and the first, it discuss the quality control standard after the filter is replaced, and the second, the method and technique of changing the filter by new monitoring system, thirdly, evaluate the new high-clean and low-pollution filter, in order to improve the quality stability and reliability of the filter when it supply.
前言
當製程線徑微縮,要求化學品含不純物奈米顆粒尺寸(Nano Particle Size)和數量(Particle count)日趨嚴格,透過廠務系統或設備機台的多道串聯過濾程序及濾心孔徑微縮來提升純化品質;以5nm製程為例:從上游廠務供應系統濾心20nm~10nm至下游設備機台濾心10~1nm分佈,現況顆粒殘量僅符合運轉基準,若再降低一倍顆粒殘留數量,現行配置已無法克服,故廠務系統評估10~1nm濾心,以成為解決顆粒殘量方案。
安裝於廠務系統新式濾心是否適用於產線,需提證濾心洗淨後品質和化學品殘留顆粒量,及試產供應後,配合設備晶圓電子束檢測缺陷和晶圓表面殘顆粒量,上述前者影響後者,其濾心洗淨流程尤為關鍵。濾心殘金屬量源於包材出貨品質(COA),透過廠務系統使用自動化清洗、浸泡和濾酸後取樣金屬殘量檢驗,可解決殘金屬低量濾心,但殘高含量金屬濾心,可能因浸酸後金屬析出速率不同、清洗量多寡及排酸開閥次序不同,影響洗淨效果,各廠在清洗量與排酸閥件開關時間和次序已有相當研究,本文將著重於浸酸析出金屬實驗做延伸探討和管理洗淨品質。
文獻探討
2.1 濾心材質種類及特性分析
電子級化學品濾心廠牌市售主要分Pall®和Entegris®,其濾心材質種類PTFE(Polytetrafluoroethylene)、HAPAS(High Asymmetric PolyArylSulfone)、HDPE(High-density Polyethylene)、PS(Polysulfone)、Nylon,依可製程產品之耐化性、通透性、耐熱性、金屬離吸附性、親水(Hydrophobic)和疏水性(Hydrophilic)分類,匹配不同種類化學品系統及製程需求,有不同適用性,例如 : PTFE因具有高耐化性且高潔淨度,最廣泛使用於半導體供應系統;HAPAS結構具有高度非對稱性,對於微顆粒阻攔性佳,濾心產品微孔可製作性高,在先進微縮製程中,為具潛力產品;Nylon有較佳的金屬離子吸附性,可列金屬憂選(Metal concern),予化學供應系統串聯使用。使用與否仍須優先考量產品對化學品之適用性(如 表1、圖1)[2][3]。
Product | Rating | DIW | DHF BOE | DHCl SC1 | SPM Phos | Solvents | H2O2 O3-DI | TMAH | BEOL Stripper |
HF 49% HCl 36% NH4OH 29% |
---|---|---|---|---|---|---|---|---|---|---|
PTFE | 30nm~5nm | √ | √ | √ | √ | √ | √ | √ | √ | √ |
HAPAS SPDR | 30nm~5nm | √ | √ | √ | √ | √ | √ |
圖1、濾心薄膜電子顯微鏡表面成像

化學品液相中主要包含硬顆粒(Hard Particle)及軟顆粒(Soft Particle)大小分佈(Particle Size)及微顆粒總量(Particle Count),兩指標影響微縮製程良率穩定性,薄膜平均孔徑大小(Port Size)為顆粒阻攔指標,薄膜結構和材質成形亦影響阻攔顆粒總量,若探討薄膜成形結構對於阻攔效果,可分為對稱(Symmetric)、非對稱(Asymmetric)、多層結構(Duo Composite),對稱結構對於直接補集(Direct Interception)效果較佳,以液相顆粒分布集中大於薄膜孔徑最為顯著,而非對稱結構倚賴慣性補集(Inertial Interception),液相平均顆粒尺寸大於薄膜孔徑和顆粒尺寸分布廣泛者適用,且非對稱結構在奈米孔徑下,低孔徑高較具優勢,根據Pall®提供孔徑10nm濾心,比較低孔隙度(Low porosity)高對稱(Isometric)HDPE結構與高孔隙度(High prpsity)非對稱(Asymmetric)HAPAS之流量(Flow Rate)與壓差(Pressure Drop),同壓差下,非對稱性HAPAS呈現高流通量,因濾膜內,高密度低孔徑分布厚度薄,具有短濾程。多層結構(Duo Composite)可考量濾程,依不同膜厚做孔徑調整,以達到高攔阻、高流量、低壓差之目的(如 圖2 圖3)[3]。
圖2、濾心薄膜結構示意及電子顯微鏡剖面圖
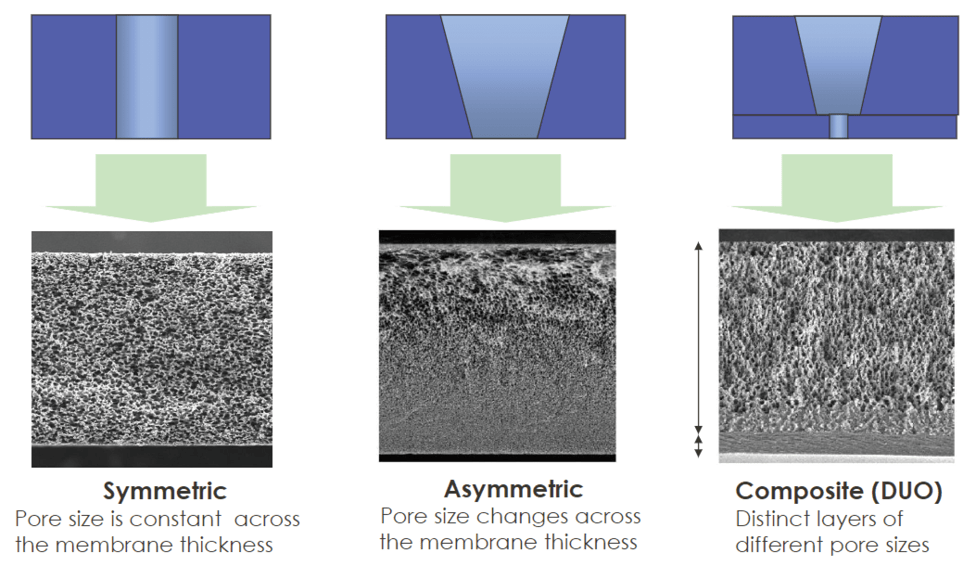
圖3、同濾孔徑下,HDPE與HAPAS濾心流量與壓差比較
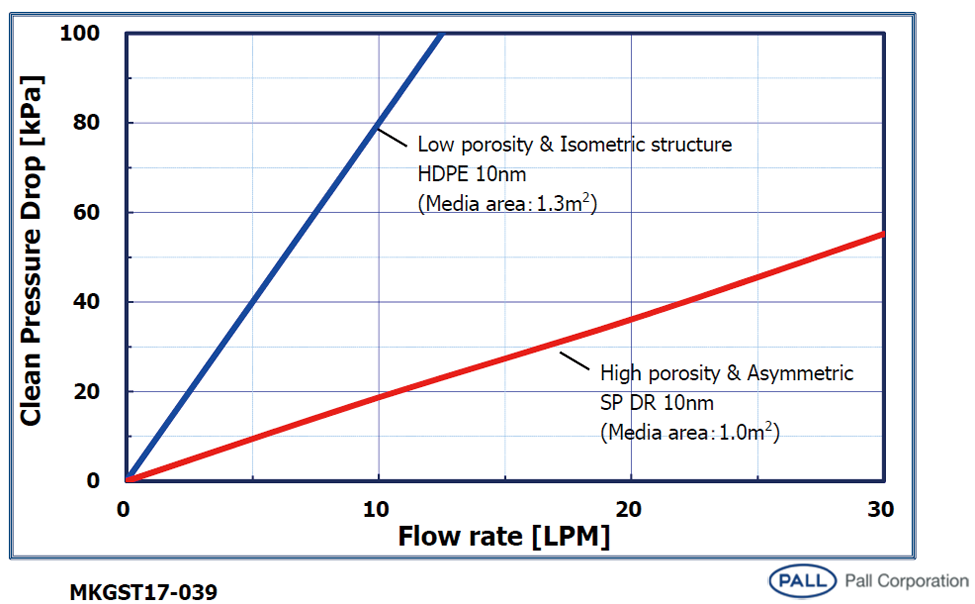
此外,若使用化學品中,部分顆粒具有帶電性,可借由濾材改質,使膜面或濾孔帶電,以達靜電吸附(Electrostatic Adsorption),可提升大顆粒直接補集及微粒慣性補集。
然而軟顆粒課題較硬顆粒阻攔具挑戰性,軟顆粒典型代表為微泡(Micro Bubble),微泡受液體慣性影響,可於濾心孔徑內變形穿越或碰撞破泡,導致微泡透孔;選用濾材具有疏水(Hydrophobic)特性,以增加慣性阻攔效果於薄膜孔徑內,多微泡凝聚形成泡,可減少微泡透孔,或濾材進行表面改質成高表面張力(Critical Surface Energy),增加微泡直接補集,以利於表面微泡凝聚,後者優勢可保留低孔徑濾心產品可製性,和材質選用適用性(如 圖4 圖5)[2][3]。
圖4、微泡在浸潤(Non-dewetting)濾膜下透孔行為和及非浸潤(Wetting)薄膜凝聚形成泡機制
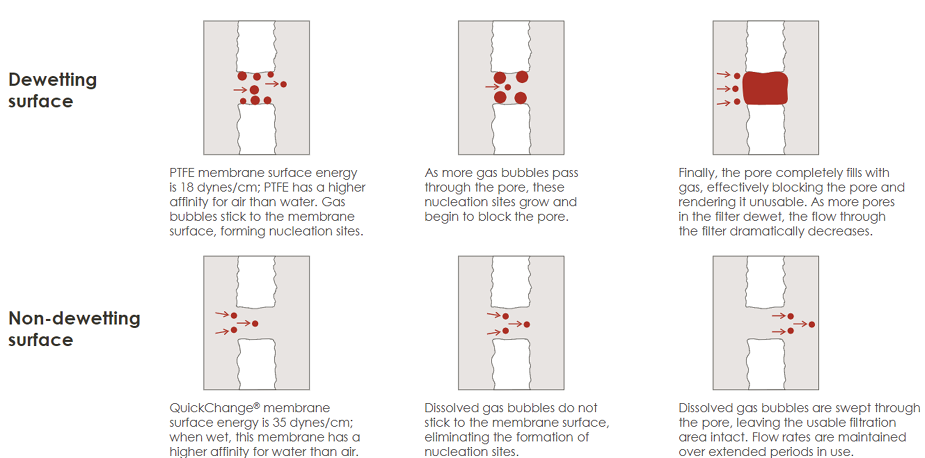
圖5、不同濾心材質表面張力級數比較
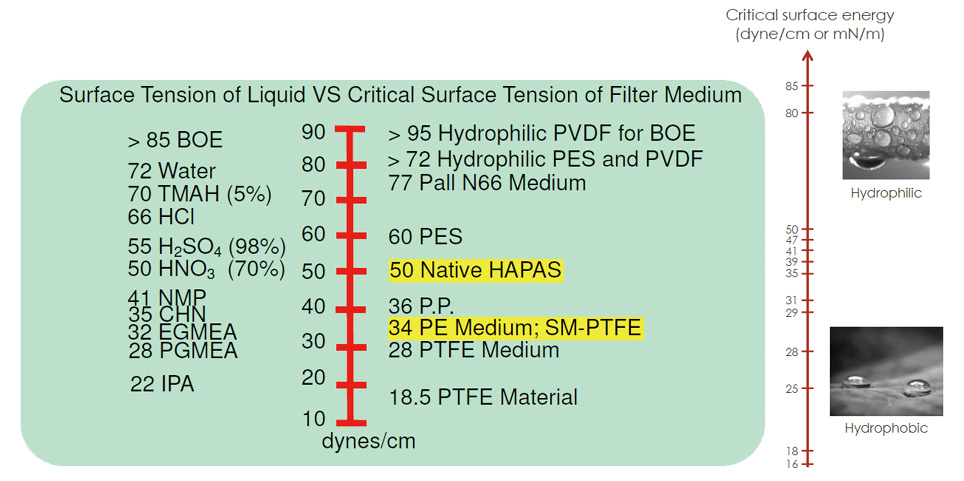
純化(Purification)濾心由別於一般攔阻顆粒濾心在於,濾材分子結構具備特殊官能基或陰陽離子,透過離子交換(Ion exchange)、螯合(chelation)或金屬配位反應(Metal ligand bonding),捕捉液相金屬離子(Metal removal)和有機化合物(Organics),此類純化濾心批配於黃光顯影液2.38% TMAH(氫氧化四甲基銨tetramethylazanium hydroxide)有助於改善晶圓缺陷(Scum&Cone defect),主要源於純化濾心對鐵[Fe]、鉻[Cr]、鎳[Ni]和錳[Mn]重金屬和長短碳鏈有機分子移除效果佳(如 圖6 圖7)[2]。
圖6、TMAH(氫氧化四甲基銨)顯影液體殘留金屬與有機化合物對於晶圓(Scum & Cone defect)缺陷

圖7、化學品稀釋倍率和純化濾心與攔阻型濾心移除金屬殘量圖
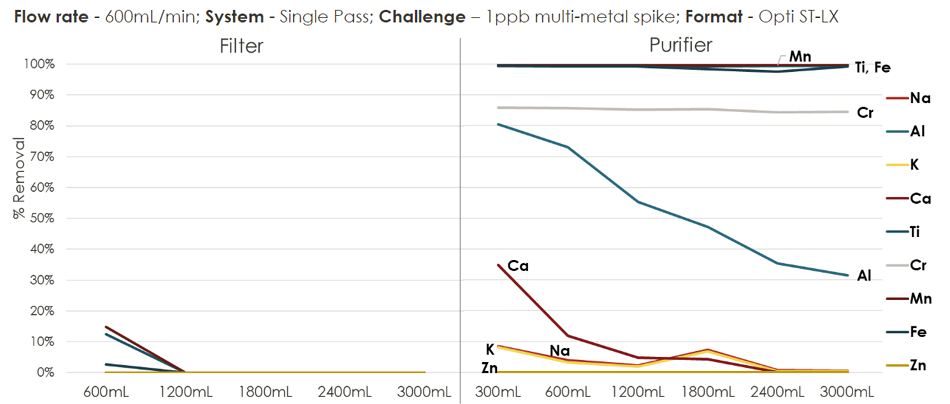
表2依據不同材質濾心比較表,考量低孔徑濾心製品如PTFE、HAPAS和HDPE等的選用上,排除高非對稱性結構的HAPAS的硬顆粒的濾效、濾膜高表張排微泡特性和較佳的流通量(Flow performace)外,HAPAS濾心製品有較高的金屬殘量(Metal cleanliness),此缺陷需透過薄膜製作後洗淨或供應系統更換後的洗淨處理,才得以供應使用,以先進製程的品質要求,化學品的超微量分析金屬殘留量部分金屬元素需約於兆分之一(ppt level)的偵測極限值,以HAPAS濾心製品總金屬殘留量3000ppt為例,供應系統需洗淨稀釋量100~30倍。
Material | PTFE | HAPAS | HDPE | Nylon |
---|---|---|---|---|
Structural formula | ![]() |
![]() |
![]() |
![]() |
Surface treatment | Mdified | Native | Native | Native |
CWST[dynes/cm] | 35 | 50 | 36 | 72 |
Membrance structure | Symmetric | Highly Asymmetric | Symmetric | Asymmetric |
Max temp. | 185 | 70 | 60 | 60 |
Max dP[MPa] | 0.59 | 0.1 | 0.34 | 0.27 |
Flow performace | Good | Excellent | Fair | Fair |
Chemical Compatibility | Excellent | Limited for oxidatives solvents | Limited for oxidatives | Limited for acid oxidatives |
Metal cleanliness(ppt) | <500(10" XP5) | <3000(10" SPDR2-RS1) | <10000(10"-K13C) | NA |
2.2 濾心製造及製造後洗淨處理探討
依據供應系統常見濾心種類Polysulfone、Nylon、Polyethersulfone、Polyacrylonitrile、Polyvinylidene fluoride、Polypropylene製程流程分別以沉浸溼式法(Immersion casting)、噴熔吹塑法(Melt blown)和燒結拉伸法(Sintering Stretching),如 圖8,探討和分析薄膜製程殘餘金屬量。
圖8、不同薄膜材質與成形方式
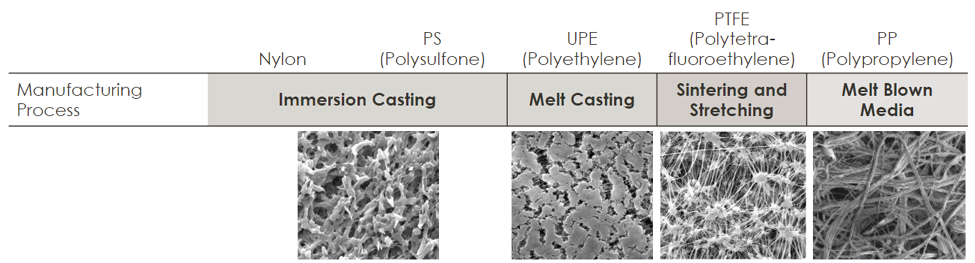
PS(Polysulfone)與Nylon使用沉浸溼式法(Immersion casting)即非溶劑致相分離法(Nonsolvent-Induce Phase Separation, NIPS)成膜(如 圖9)[2],透過高分子鑄膜液浸入凝聚液中固化成膜,溶劑與非溶劑質傳,凝聚液通透量大於溶劑時產生相分離,成膜過程從單相經相分離線(Binodal Curve)形成雙相(Two-Phase Area),膜材透過乾燥固化。由於不同成分配比和質傳過程,影響不同成膜結構,如 圖10 Polysulfone三相圖中,於路徑1為單相直接固化形成緻密膜材,路徑2為高分子貧相(Polymer Lean Phase)成核所形成海綿結構,路徑3成絲狀結構,路徑4則為高分子富相(Polymer Rich Phase)成核形成顆粒堆積結構[1]。
圖9、沉浸溼式法(Immersion casting)
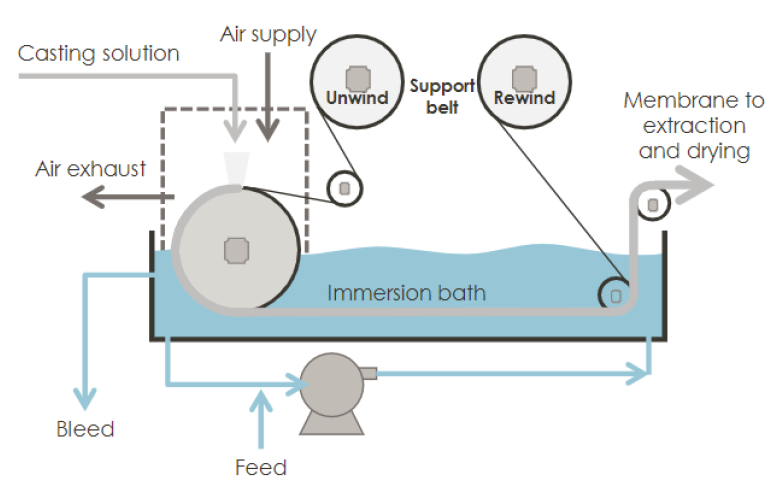
圖10、Polysulfone三相圖與分離路徑圖
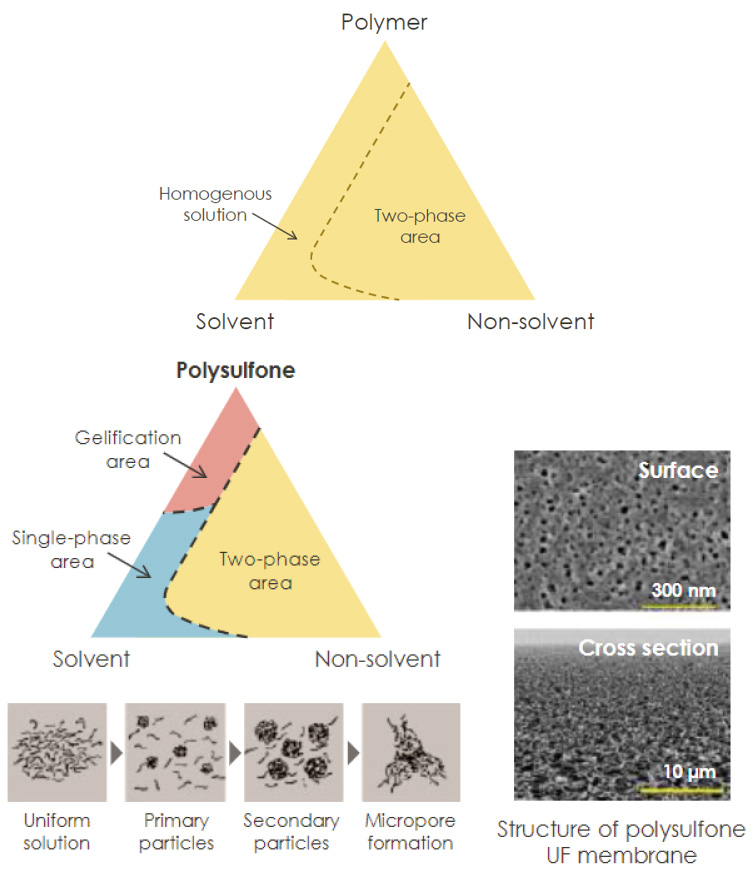
UPE(Ultra High Molecular Polyethylene)和PP(Polypropylene)薄膜採熔噴吹塑(Melt Blown)技術,如 圖11所示[2],熔融高分子聚合物透過高速吹塑氣體噴嘴擠出,均勻噴吹於冷卻滾筒上,固化成形後經適度拉伸和熱處理即可得到欲製薄膜,其過程不涉及媒介溶劑操作,可避免濾心再未洗淨完全,有機物殘留膜內之風險。其製程需選擇具有較佳流變和表面特性的高分子聚合物,吹塑出直徑較小的熔噴纖維,以達到低孔徑和高孔隙度之薄膜。
圖11、噴熔吹塑法(Melt blown)
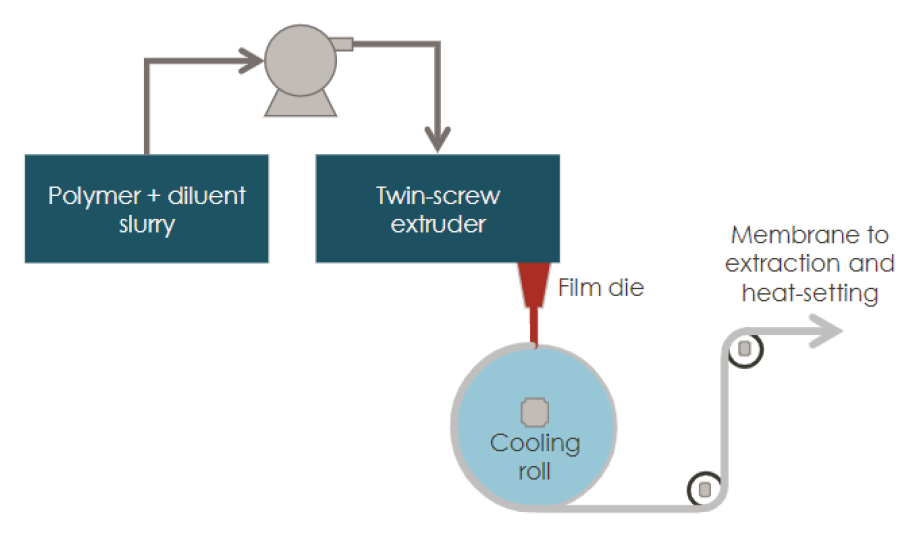
由於PTFE(Polytetrafluroethylene)粉末屬高溶點聚合物,混拌潤滑劑形成膏狀粉末,擠壓成形排除空氣後,經熱處理(Heat Treatment)和初步拉伸提高基膜強度,基膜進入非對稱燒結(Sintering)溫度和薄膜拉伸壓延(Extrusion)成膜,如 圖12[3],其設定適當的燒結溫度和時間,以及控制拉伸壓延速度和次數,可增加交聯(Fibril)密度和空隙度,並有效降低膜內孔徑。因PTFE膜材質疏水性且結構具有交錯曲折及層狀立體堆疊,濾心製品加工洗淨後,需增加一道預溼處理(pre-wet)程序浸泡,避免濾孔殘留微泡。
圖12、燒結拉伸法(Sintering Stretching)
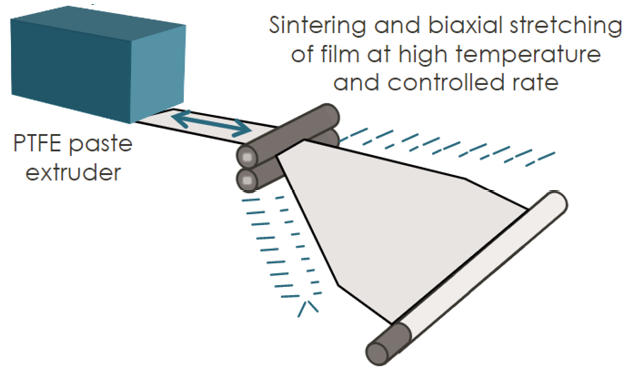
濾膜完成後需經膜黏著(Resin)、濾膜打折(Pleating)、折膜安裝(Put membrane in the housing)、預潤(Pre-wetting)、超純水洗淨(DIW Flushing)、乾燥(Drying)、濾罐封裝(Capsule welding)、清洗(Cleaning)和外包裝(Packaging),部分濾膜因受限製程條件及設備,成品濾膜殘留有機物和錯合微量金屬元素,無法單由酸劑洗淨,需經由有機溶劑互溶和酸洗析出,減少金屬元素殘留,而洗淨酸劑和有機溶劑劑量影響成品金屬殘留量,但隨著洗淨劑量次數增加,會導致成品有機殘留和供應商洗淨成本,如 圖13[2]。
圖13、供應商濾心洗淨流程
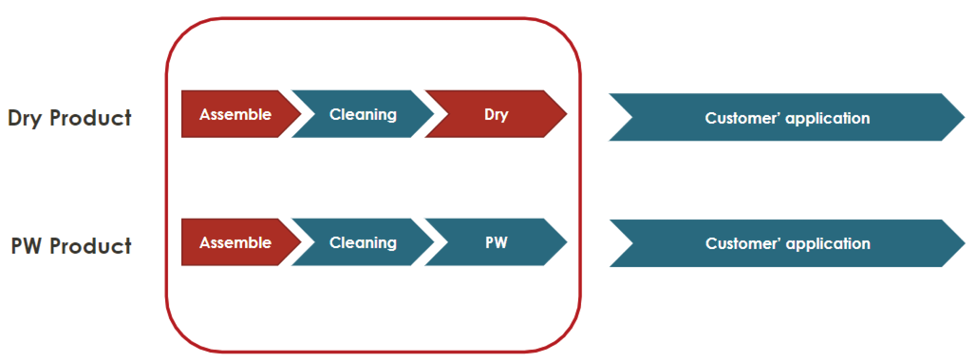
2.3 濾心洗淨程序探討
廠務供應系統完成濾心安裝後,傳統自動清洗程序,濾心外充填排放(Pre-fill)及排泡(Vent),接續濾心內充填排放(Drain),完成規範洗靜量後,經浸泡(Soaking),再取樣確認(Quality check)。於台積電RD廠評估發現,受不同化學品流體黏滯性,以及硬體設備濾心前後管路出入口和排泡管路配置非對稱,造成流體短流,排泡不完全,濾心未浸泡清洗區域,有金屬殘留及降低濾效疑慮,因此提倡使用擾流洗淨解決方案。
- 預先充填排放和擾流排泡(Pre-Fill& Vent) : 開啟排泡閥充填排放,使濾心外充滿化學液,當溢流排放後,同步執行短間格開關排液閥,擾動滲透有助於濾心內氣體排空。
- 擾流排液(Flush) : 排液程序過程,追加短間格開關閥排泡,增加濾心外盲區溢流,目的增加濾膜潤洗,減少濾心開始使用後帶出微泡。
- 浸泡(Soaking) : 當化學液充滿濾心內外後,需經長時間靜置浸泡,使濾心內微泡和不純物擴散,達平衡狀態後,再執行排放置換或排空化學液程序,以達洗淨效果。
此方案應用於大尺寸(20")濾心、多並聯濾心、小孔徑濾心及高黏度流體,可克服洗淨不完全區域和短流盲區效應,如 圖14。
圖14、擾流洗淨程序流程示意
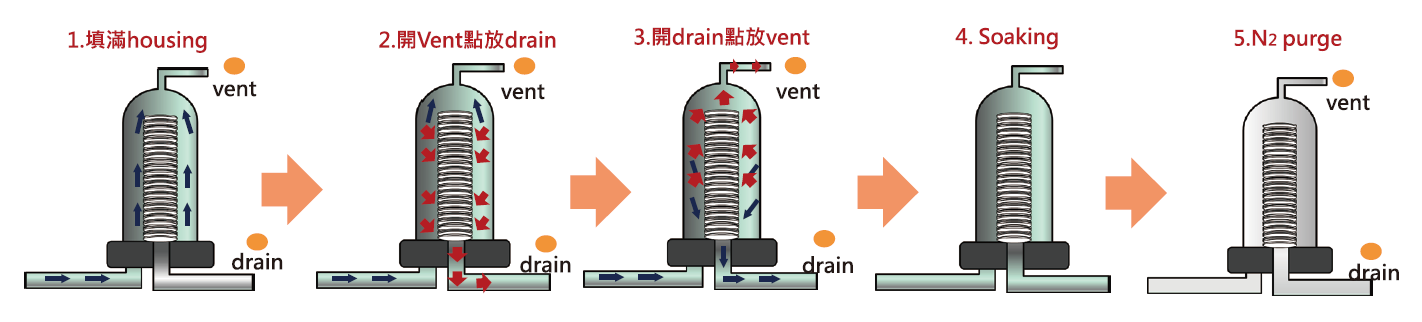
由於系統拆卸濾心前,執行氮氣充吹濾心後,管路呈現空管下更換,在安裝鎖固後的第一次預充填時,沖洗於濾心內的金屬析出液易殘留於管末呆酸處(Dead Zone),此處僅能透過排放置換舊酸時,由質傳擴散至新酸中,降低金屬殘留,且受濾心濾阻影響,濾心出口管路流速較低,流場擾動效果差,容易在取樣時,無法確認此處殘留狀況,往往在濾心瞬間上線時,影響下游設備供應品質,因此開啟濾心末端閥件置換管末呆酸處的逆洗程序,必含括於洗淨流程中,此程序需於完成預先排放滿管後執行,預防出口閥開啟後,造成供應邊出口壓降。
研究方法
3.1 原物料、濾心搭配於供應系統條件
HF25%為僑力化工,物料COA總金屬(Total Metal)殘留約為65ppt,總計13種金屬,0.03um particle count<45ea (Range : 15~40ea)。
HF49%為僑力化工,物料COA總金屬(Total Metal)殘留約為65ppt,總計13種金屬,0.03um particle count<45ea (Range : 5~30ea)。
IPA為李長榮化工,物料COA總金屬(Total Metal)殘留約為0.002ppb總計13種金屬,0.03um particle count 25ea (Range : 20~40ea)。
HAPAS 2nm濾心為廠牌Pall®,分別10吋及20吋。(圖15)
圖15、Pall® HAPAS 2nm濾心型錄
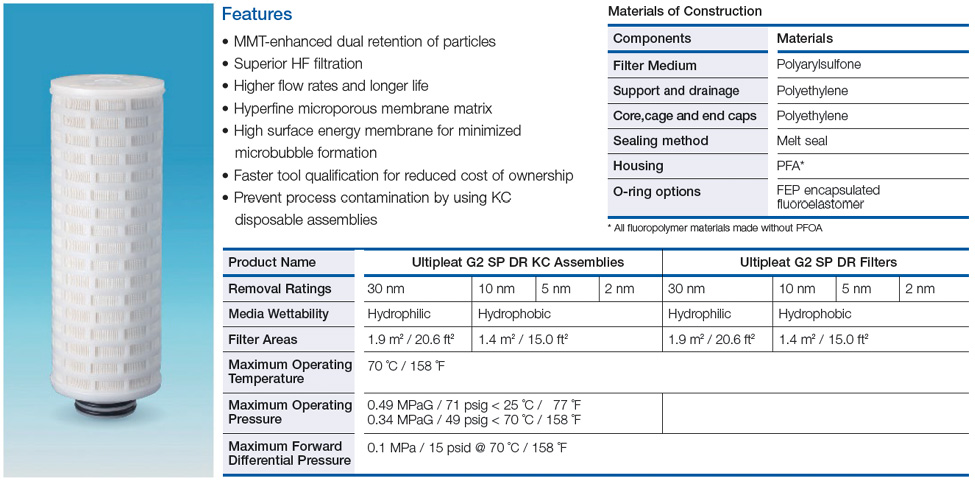
PTFE 2nm和10nm濾心為廠牌Entegris®,分別10吋及20吋。(圖16)
圖16、Entegris® PTFE 2nm濾心型錄
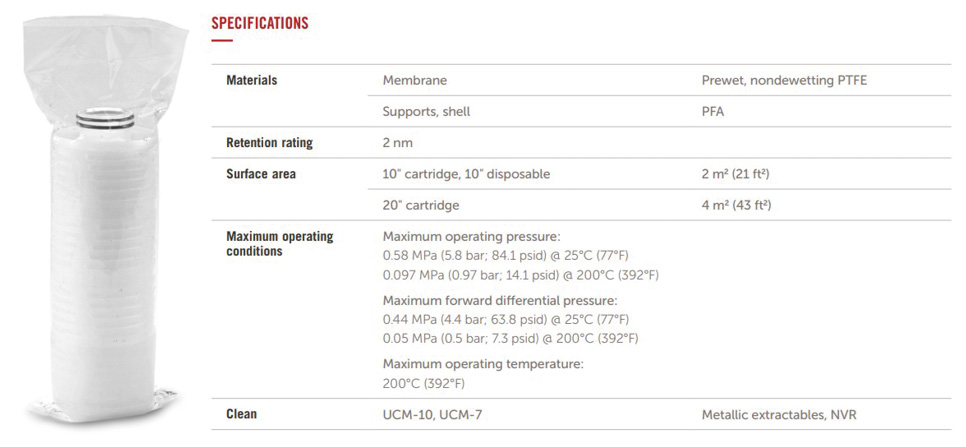
PS 1nm濾心為廠牌Entegris®,分別10吋及20吋。(圖17)
圖17、Entegris® PS 1nm濾心型錄
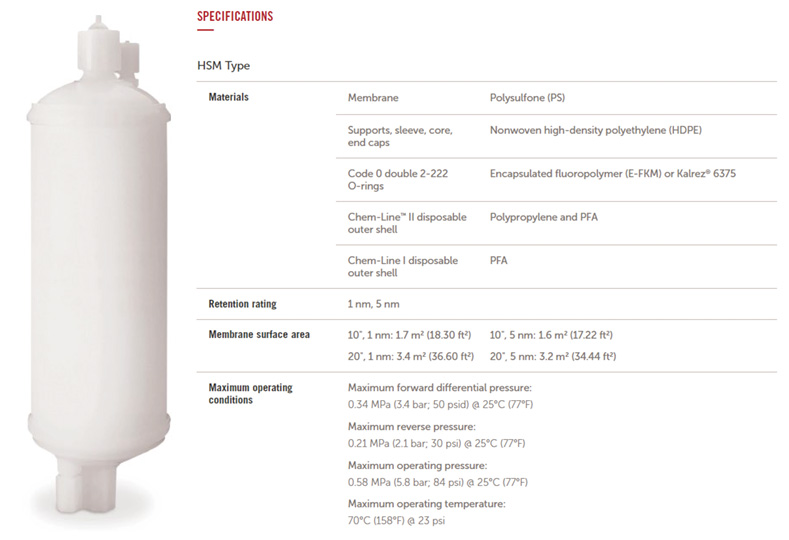
3.2 濾心包裝水金屬殘留量
於上文文獻回顧提及供應商濾心洗淨不足,新品濾心安裝於供應系統,恐需長時間洗淨,以去除金屬殘留,因此取樣於濾心包材內超純水,以驗證此論點;3nm UPE(Entegris®)濾心,將不同批號進行包裝水取樣,委樣至台積實驗室檢測。
3.3 不同種類濾膜金屬析出分析
此實驗著重5nm製程量產廠和RD廠,配合WET Clean進行化學品殘留顆粒量減量評估,導入2nm孔徑PTFE(Entegris®)、HAPAS(Pall®)及同級1nm PS(Entegris®)濾心,安裝於含氟類HF1%、HF25%化學供應系統後,依PM O.I.規範洗淨量 : 逆洗量 : 浸泡量2 : 1 : 1程序(Flush Volume)60L/ea(size : 10吋)和120L/ea(size : 20吋),參數設定洗淨以預先充填的排泡(Vent)、排放(Drain)和逆洗,由系統磅秤重量(Load Cell)或旁通管(Side tube)液位高度,紀錄執行上述狀態,於上述程序前需執行手動取樣,避免未浸泡下和直接洗淨後取樣,僅取得新酸樣品,由台積電實驗室CHAD以Agilent ICP-MS 8900(Inductively Coupled Plasma, ion source-Mass Spectrometer, ion analysis)分析濾心13種金屬元素殘留量,每日執行一次上述動作一次,收集數據至可上線供應單位。
3.4 濾心使用傳統與新式擾流洗淨程序金屬析出分析
安裝2nm HAPAS(Pall®)濾心於HF1% CMDU,分別使用傳統與擾流程序參數設定方式,如 表3,每次洗淨開始及結束後,需紀錄磅秤重量差,確認是否達洗淨量條件正洗360L、逆洗180L和浸泡,次日執行取樣及委樣至台積實驗室檢測,並同前日洗淨條件動作操作,觀察金屬殘留至範圍內。
Step | Step1(sec) | Step2(sec) | Step3(sec) | Step4(sec) | Step5(sec) | Step6(sec) |
---|---|---|---|---|---|---|
擾流洗淨 | Vent | Vent+ Pipe Drain(點放) | Pipe Drain+ Vent(點放) | Vent+ Pipe Drain | Drain+ Pipe Drain(點放) | Pipe Drain+ Drain(點放) |
60sec | 60sec | 60sec | 60sec | 60sec | 60sec | |
傳統洗淨 | Vent | Drain | Pipe Drain | - | - | - |
120sec | 120sec | 120sec | - | - | - |
圖18、擾流洗淨程序
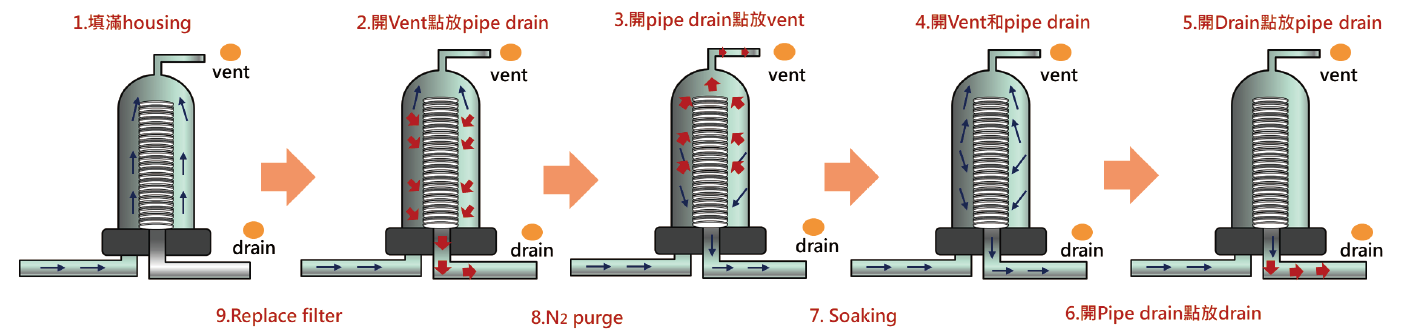
圖19、傳統洗淨程序
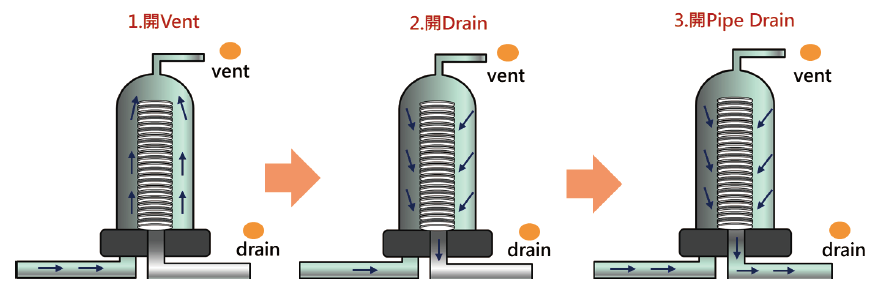
3.5 HAPAS、PTFE和PS濾心供應試車於晶圓測試方法
濾心洗淨後,需在供應前進行試車(Pre-Qual),以限時上線供應方式,測試使用於晶圓後,晶圓透過電子束檢測缺陷和表面殘顆粒量(Inline KLA)確認供應品質,亦或使用粒徑分析收集(Offline Paticle)酸源殘留顆粒量,此兩道驗證程序可作為濾心是否可上線供應之依據。
3.6 濾心預洗、pre-qualilty及活體移植方法
活體移植一詞出自醫學,將捐贈者器官轉移至具相容性之受捐者體內,亦同於供應系統中濾心,轉移安裝於相同供應系統中;考量5nm先進製程大宗和關鍵化學品(Critical Chemical)供應品質,廠房於建置初期,主系統予與附屬測試供應系統(Pre-quality CDU),系統管表圖如 圖20,上游CCBTU配管於此系統,系統內搭配250L桶槽、幫浦(Pump)、雙通道濾心,系統下游至測試供應盤(Pre-quality VMB)和切換盤(Switch Box),最後連接於設備機台;測試供應系統目的為灌充原物料前試吃,並量測設備機台單一酸源殘留顆粒量,因系統雙通道配置,發展出將單邊或雙邊試車(pilot run)成功之濾心,轉移其他相同濾心數量和尺寸之供應系統使用,其一減少主供應系統在供應前進行試車、限時上線供應方式,仍有全面影響產線其他機台設備之可能性,其次減少主供應系統更換後,洗淨和取送樣次數,單邊供應壓降之風險。
圖20、Pre-quality CDU架構
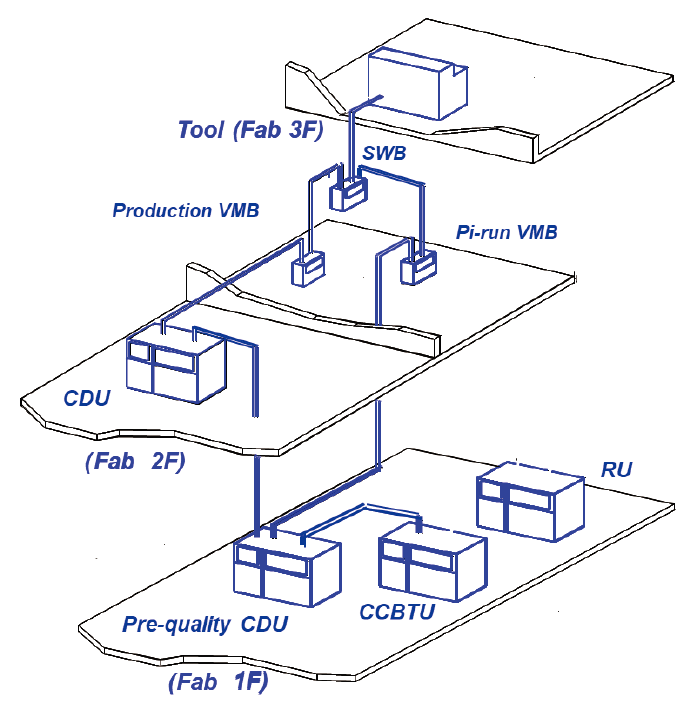
活體移植流程分成移植前,如 圖21所示,需更換附屬測試供應系統濾心進行預洗(Pre-clean),經洗淨、浸泡、取樣分析和試車(pre-quality);活體移植前,測試供應系統濾心需執行微氮氣吹淨,確認濾心內無殘酸後,再執行外蓋(Housing)拆除,過程需避免高壓和長時間氮吹,預防濾心破孔或孔徑殘氣;拆卸後,需連同濾心和外蓋(Housing)一同放置於夾鏈袋內,並轉移至欲更換之供應系統安裝,完成洗淨、浸泡、取樣分析。運用上述流程,實驗安裝4支10吋濾心5nm孔徑PTFE(Entegris®)濾心於IPA Pre-quality CDU預洗,完成金屬殘留確認(Quality Check)和試車(Pre-quality)後,活體移植至IPA RU,再清洗和取送樣,觀察金屬殘留變化,並與一般更換IPA RU流程作為對照組。
圖21、活體移植流程示意
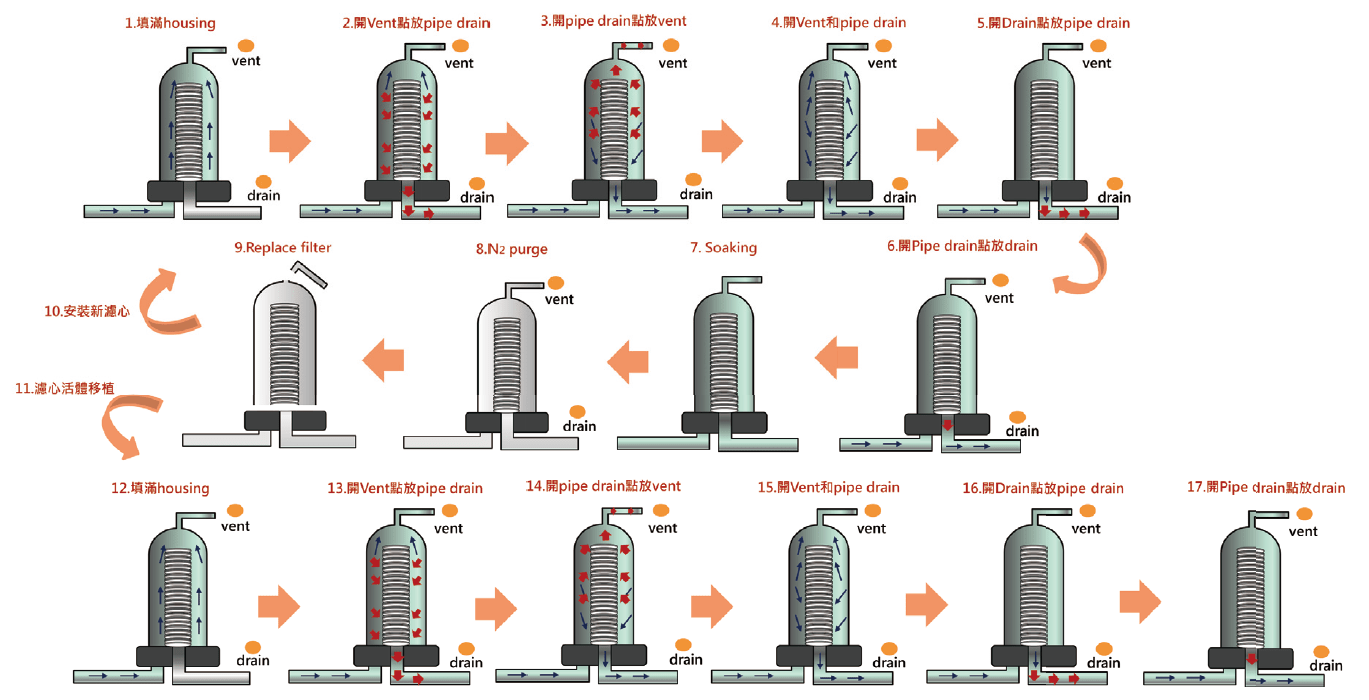
結果與分析
4.1 濾心包裝水金屬殘留量分析
將不同生產批號之3nm孔徑UPE(Entegris®)濾心包裝水送樣檢驗如 圖22,發現大量金屬元素鈉和鋁約5~20ppb,且鉀、鈣和鋅約1~15ppb,依照生產批號比對,批號第三碼依英文字母代表為月份,於1、2和3月生產批號相較5和7月生產批號的金屬殘留量少,如 圖23結果與供應商提供COA資料比對有正相關,顯示不同月份生產濾膜和濾心清洗流程中,有殘餘未完全洗淨之金屬殘留。
圖22、3nm UPE不同生產批號包裝水之金屬殘留比較
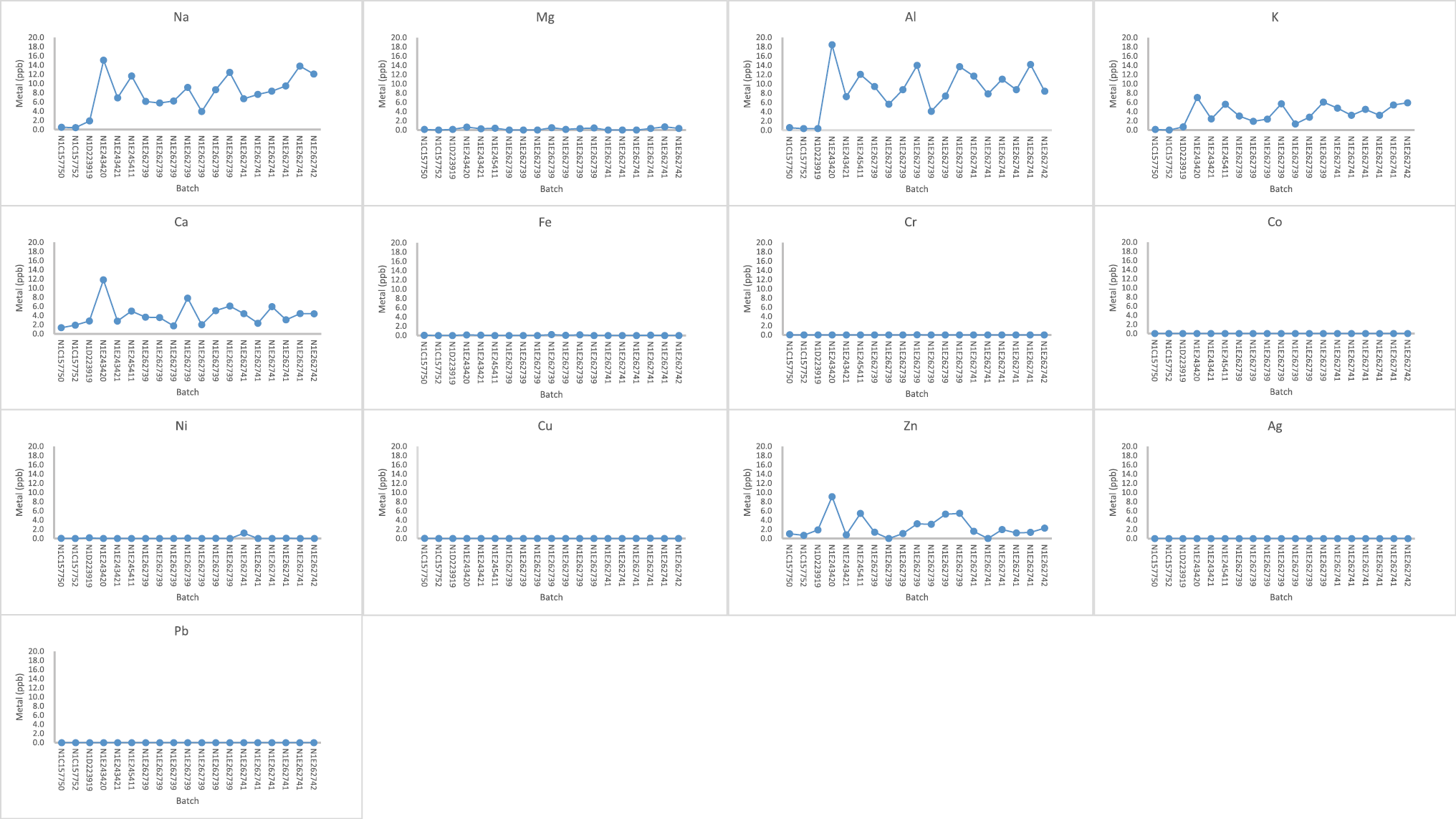
圖23、Entegris® 3nm UPE不同生產批號之金屬殘留分析
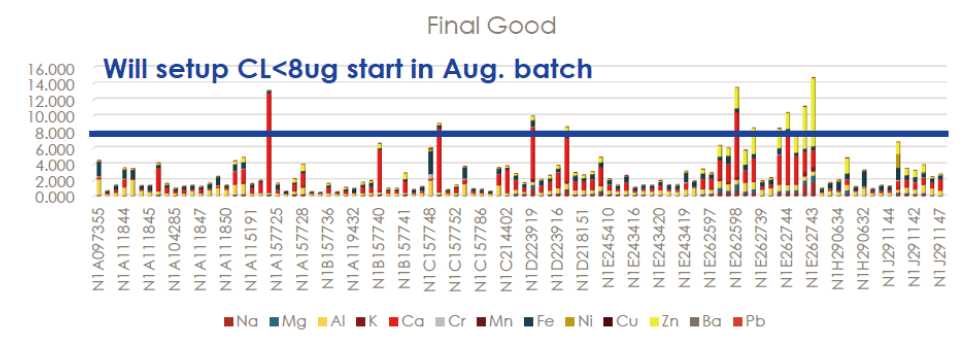
4.2 HF1%供應系統使用HAPAS、PTFE和PS濾心洗淨後金屬殘留分析
比較同2nm孔徑HAPAS(Pall®)與PTFE(Entegris®)濾心,安裝於HF1% CMDU(Chemical Mixing Dispense Unit)單通道並聯3支20吋濾心,實驗結果,如 圖24;當日更換後執行正洗360L和逆洗180L新酸置換量後,2nm HAPAS濾心的鉀、鈉、鎂、鋁、鉻、鐵、鎳等金屬元素皆大於供應使用規範100~200倍,需經4天的4倍洗淨和浸泡量後,才得以降低至約5~10%殘留量,觀察約5~10日洗淨後,鐵、鉻、鎳等過渡金屬元素以降至規範內,而鉀、鈉、鎂、鋁的鹼金和鹼土元素仍持續達20~100ppt範圍內析出殘留。說明低濃度氫氟酸,特性不易解離成氟離子與金屬元素反應析出外,即便高流通量的HAPAS也不易透過沖出方式,將膜內金屬殘留排至濾心外,僅能由置換新酸後,由浸泡擴散析出殘留金屬,洗至17日後,仍有鉀、鈉、鎂、鋁金屬殘留約莫100ppt。而同級2nm PTFE濾心,洗淨5日後,即可洗淨至上線規範內。當日洗淨前取樣,兩者總金屬殘留差異約100倍,推斷HAPAS濾心的原廠金屬殘留量較PTFE高。
圖24、HAPAS、PTFE和PS於HF1%洗淨天數與金屬殘留比較
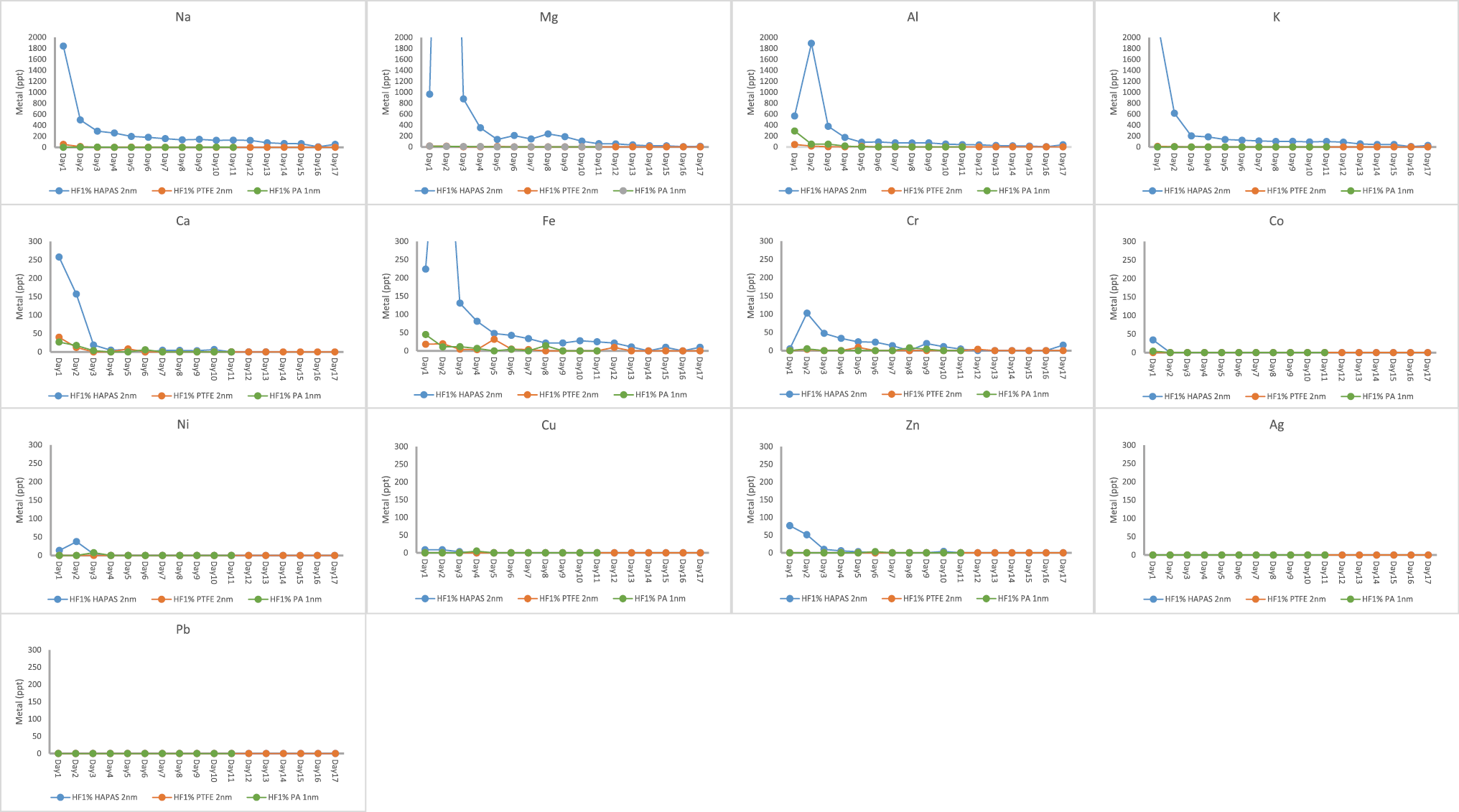
2nm PTFE(Entegris®)濾心與1nm孔徑PS(Entegris®)濾心洗淨後,總金屬殘留量兩者皆比HAPAS佳,而PTFE又略比PS佳,觀察PS洗淨5日後,僅約10ppt/unit微量析出元素。
4.3 HF25%供應系統使用HAPAS、PTFE和PS濾心洗淨後金屬殘留分析
比較與上述4.2中同濾心條件下,搭配使用不同濃度氫氟酸HF25%供應系統中,CDU(Chemical Dispense Unit)單通道並聯2支10吋濾心,如 圖25;當日更換後滿酸浸泡取樣後,PTFE和PS金屬殘留量較HAPAS少,且執行第一次正洗120L和逆洗60L浸泡後取樣,PTFE金屬殘留即達規範,PS需洗至5日後,鋁金屬殘留可達規範內,兩者皆可於短時間內,洗淨符合供應需求。
圖25、HAPAS、PTFE和PS於HF25%洗淨天數與金屬殘留比較
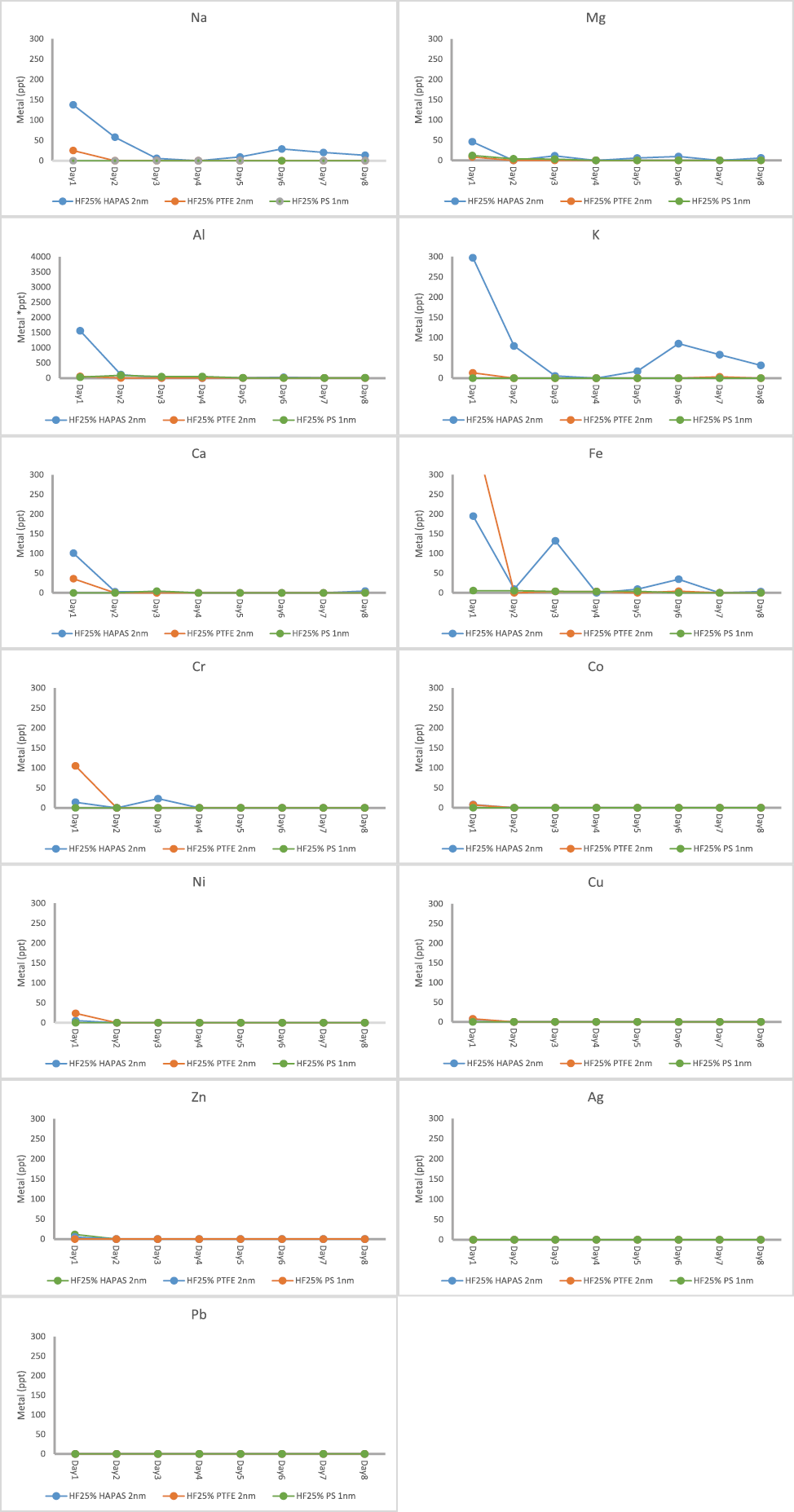
此次HAPAS濾心更換於HF25%供應系統,此實驗組相較於HF1%,雖洗淨速度較快,仍未能在短時間洗進使用品質內,幾日洗淨浸泡後取樣,仍有鈉、鎂、鐵和鉀金屬析出。
HAPAS濾心無論投入於HF1%或HF25%洗淨實驗中,鋁金屬殘留於原包材較為顯著,原廠Pall®HAPAS濾心進行HF1%浸泡實驗,並間格3日取樣觀察,隨浸泡時間越長鋁析出量呈現線性增長,第13天浸泡析出結果,鋁金屬佔總金屬析出量約90%,如 圖26;其次觀察析出金屬為鉀、鈉、鐵和鈣元素,析出元素同本次洗淨實驗觀察結果。
圖26、Pall® 2nm HAPAS於HF1%浸泡取樣實驗
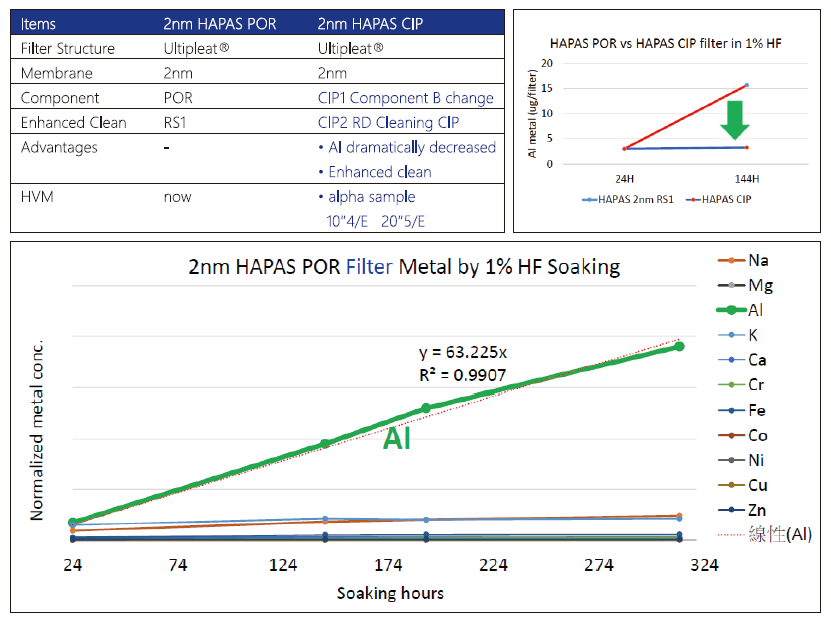
4.4 傳統與擾流洗淨金屬殘留分析
傳統洗淨(POR)比較擾流洗淨(CIT)天數和金屬殘留比較如 圖27,以鈉、鎂、鋁和鉀析出殘留量觀察,傳統洗淨至範圍需花15天左右,而使用擾流洗淨僅需花5天,效率提升3倍,且洗淨2天即有大幅度減少金屬殘留;HAPAS濾心在多日洗淨和浸泡後,仍偶有金屬析出現象發生。
圖27、擾流洗淨CIT與傳統洗淨POR金屬殘留與洗淨天數比較
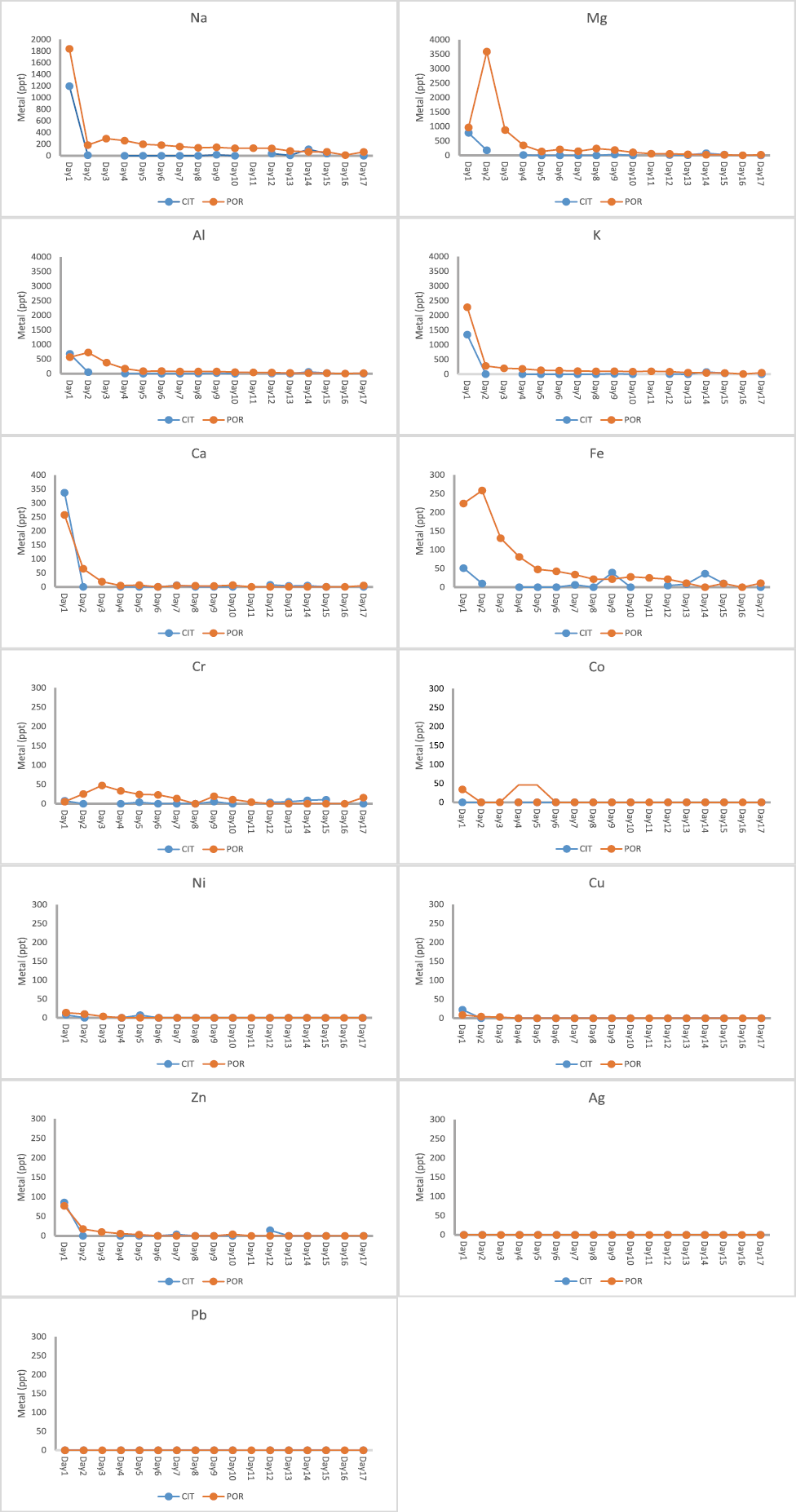
4.5 HAPAS、PTFE和PS濾心供應試車於晶圓測試
HAPAS、PTFE、PS於洗淨後,使用HF1%供應系統進行濾心試車(pre-qual),分別得到 表4 inline KLA和 表5 offline particle結果;兩者數據主要供應下游關鍵製程(Critical Process)WET Clean設備,於濾心上線供應後4小時後,由晶圓電子束檢測缺陷(Inline KLA),HAPAS和PS皆無累計特殊缺陷、明顯大量計數或特殊分布,粒徑檢測(offline particle)19nm顆粒尺寸(particle size)計量皆在範圍內。使用HF25%供應系統進行濾心試車(pre-qual),得 表6 inline KLA和 表7 offline particle結果,無論Inline KLA和offline particle結果皆符合規範。
Function | SPC chart/KLA Map | Results | |
---|---|---|---|
WET Clean | HAPAS | ![]() |
Comparable |
PTFE | - | - | |
PS | ![]() |
Comparable |
Function | SPC chart/Offline PA | Results | |
---|---|---|---|
WET Clean | HAPAS | ![]() |
Comparable |
PTFE | ![]() |
Comparable | |
PS | ![]() |
Comparable |
Function | SPC chart/KLA Map | Results | |
---|---|---|---|
WET Clean | HAPAS | ![]() |
Comparable |
PTFE | - | - | |
PS | ![]() |
Comparable |
Function | SPC chart/Offline PA | Results | |
---|---|---|---|
WET Clean | HAPAS | ![]() |
Comparable |
PTFE | ![]() |
Comparable | |
PS | ![]() |
Comparable |
4.6 濾心預洗、pre-qualilty及活體移植於異丙醇供應系統
一般濾心更換流程(POR)於異丙醇循環系統(IPA RU),需逐日洗淨、淨泡和取樣,於 圖28所示,更換後第1天即浸泡出鈣、鐵、銅、鎂金屬殘留,雖經5天浸泡和洗淨有大幅度減少,其過程異丙醇循環系統仍處於桶槽未循環狀態,即便過程暫不將此異丙醇桶槽供應,處在單桶供應對於供應量較大廠房來說,供應中斷風險極高;若採用活體移植流程(CIT),經異丙醇附屬測試供應系統(Pre-quality CDU)安裝後經短暫預洗和取樣後,近乎無金屬殘留,濾心經轉移至異丙醇循環系統後,再經過洗淨、淨泡和取樣,同樣得到和移植前結果。從兩者更換後洗淨浸泡結果,即得到單日取樣結果差異,這說明擁有單邊2支10吋串聯濾心且有獨立濾心排放路徑的附屬測試供應系統,比起單邊4支10吋串並聯濾心的循環系統,附屬測試供應系統有較高的洗淨效率;另外,活體移植後,也未出現金屬殘留,以 圖28結果為例,可於活體移植後2日,將循環濾心上線供應,相較一般濾心更換流程(POR),可縮短上線時程。
圖28、活體移植CIT與一般更換POR金屬殘留與洗淨天數比較
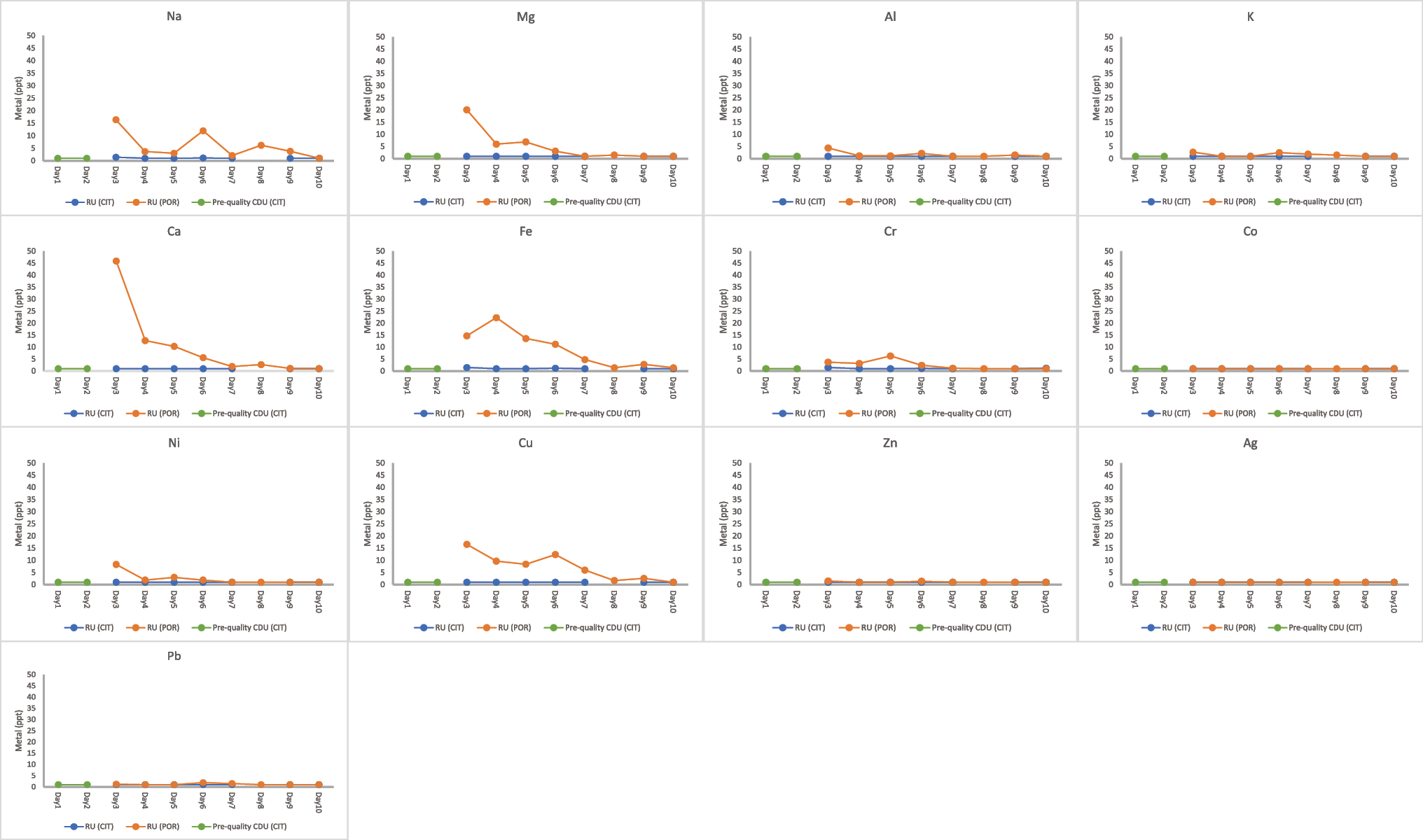
結論
評估新式濾心於供應系統需先根據產品型錄,確認適用性,選擇適當的洗淨方式,以上述實驗對象中HAPAS濾心,並不適用於HF化學供應系統中,除濾心耐壓(Pressure drop)性不足外,即使透過較佳的擾流洗淨方式,在長時間浸泡下,仍有大量金屬析出,最終需加長時間持續洗淨至無析出物,才得以使用,雖然HAPAS濾心有較低的成本費用,但過程需耗上大量化學品和時間,整體未必符合成本效益。
活體移植為新式濾心更換濾心之方法,適合用於長時間清洗或需透過浸泡析出不純物或金屬,過程可減少單邊濾心供應或循環濾心更換過程無循環,濾心經活體移植後,可短時間內上線供應;即使無附屬測試機台,延伸至同概念系統即可運用,例如 : 欲更換CR168混酸或供應系統之濾心,可拆卸氨水75ppm混酸系統(NH4OH 75ppm CMU)單邊濾心,此舉有助於對原本較差包材出貨品質(COA) UPE濾心,經預洗(Pre-clean)和活體移植安裝於CR168混酸或供應系統,有較快速洗淨且消耗較少混酸化學品清洗之成本。唯更換作業安全和二次汙染風險考量,微氮氣吹淨不足,未排空濾心內殘液,使拆卸過程漏液;轉移濾心之環境或包裝袋沾汙,恐在安裝於供應系統時,造成供應汙染。鑒於上述風險,可調整系統設計,比照 圖20進行修改如 圖29,將可更換濾心之系統,追加管路路徑於附屬測試供應系統(Pre-quality CDU),對已更換洗淨之濾心,進行附屬測試供應系統補液和試車。
圖29、改良Pre-quality CDU架構
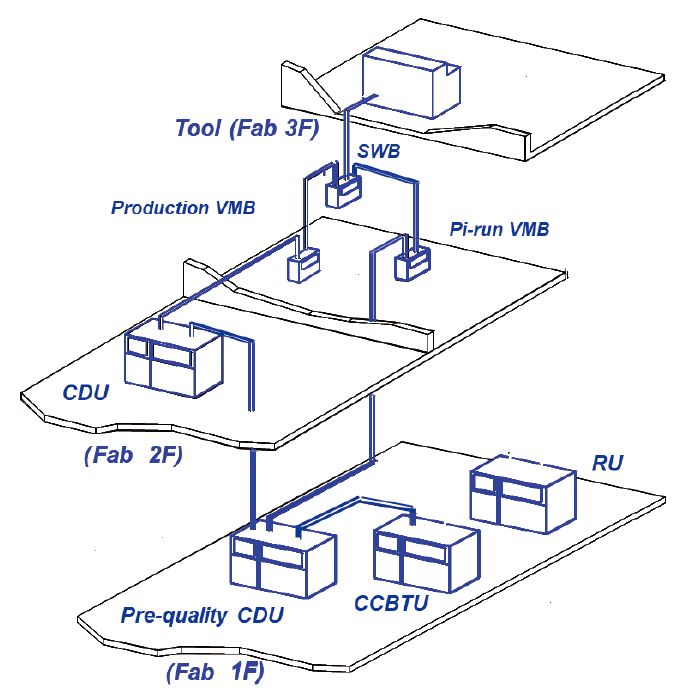
參考文獻
- 2017/12/25膜材於能源與水處理領域之應用發展現況(下)李旋維、張書噥、林俊男、朱文彬、蔡麗端/工研院材化所。
- 2020/11/11 FD GC Workshop Entegris Filter解密與新世代產品介紹陳柏嘉。
- 2020/11/11 FD GC Workshop Pall Filter解密與新世代產品介紹楊立凡。
留言(0)