摘要
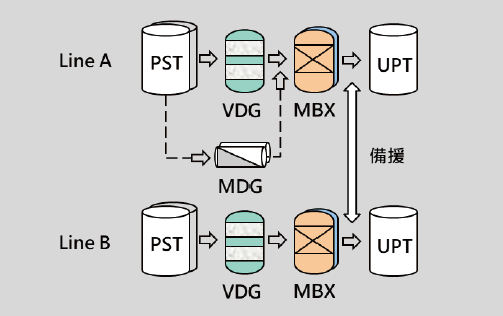
FAB6 純水脫氣系統架構升級-翻新挑戰與經驗分享
Keywords / Vacuum Degasification(VDG),Membrane Degasification(MDG),Refurbishment2
超純水系統在面對「如何達成系統穩定供應」的製程挑戰時,舊廠區首要面對的就是真空脫氣單元的翻新,在評比了早期設計的真空脫氣系統(VDG)以及新設廠區慣用的薄膜脫氣系統(MDG)的優缺點後,我們可以得知在晶圓廠的運轉需求下將VDG翻新為MDG是必須的。
在評估了FAB5的翻新經驗後,我們得知最困難的部分是要在不中斷供應的情況下完成擴充系統的架構、試運轉及上線,也因此我們在進行本次翻新時我們使用了分段潤洗、offline PLC程式試俥等可以加速工進以及降低投入風險的嘗試,而在成功將系統投入上線後新架構的系統也成功能在更低風險下進行不停水保養維護以及極大的降低強供時間。最後我們檢討本次翻新工程的缺失,發現在於電盤散熱以及MD 真空系統排水設計上仍有可改進的空間。綜上經驗分享,希望能對於有規畫進行VDG/MDG翻新的廠區有所助益。
When facing the process challenge of achieving a stable supply in the ultra-pure water(UPW) system, the primary challenge for the 200mm FAB facility system is the renovation of the vacuum degasification unit. After evaluating the advantages and disadvantages of the early design vacuum degasification system(VDG) and the membrane degasification system(MDG), which commonly used in 300mm FAB facility system, we can conclude that renovating VDG to MDG is necessary for the fab operation.
Refer to the renovation experience of FAB5, we learned that the most challenging part was to complete the expansion system construction, test run, and tie-in without interrupting the supply. Therefore, in this refurbishment, we tried segmental flushing, offline PLC program testing, and other methods to accelerate progress and reduce risks. After successfully tie-in the system, the new system architecture could take maintenance when keep supplying and greatly reduce the forced supply time at a lower risk. At the end of this article, we reviewed the shortcomings of this refurbishment project and found several improving chances in the electrical cabinet's heat dissipation and the MD vacuum system's drainage design. Based on our experience, we hope that this sharing can be helpful for other FAB which has the requirement to take VDG/MDG refurbishment.
1.前言
晶圓廠所使用的超純水(Ultra Pure Water, UPW)系統中依賴不同的單元設計去目標性的處理水中各種不純物,面對各世代製程之挑戰主要在於「如何達成系統穩定供應」,其中不僅限於基礎的使淨水系統供應不中斷或者產出水質的穩定,更需要考量到各式處理單元設計與系統改善,在摻雜入了日常保養維護、突發性元件故障及人員操作查修訓練等狀況與因素後,依然能滿足工廠端對於廠務系統穩定供應的需求。為追求更穩定的供應品質同時降低突發性元件故障導致的停供風險,200mm晶圓廠在近幾年陸續執行了許多翻新工程,FAB6 超純水系統在考量到未來維護的需求及系統穩定性,也有計畫地擴充薄膜脫氣系統以取代既有的高效率真空脫氣塔。但在成熟運轉廠區要進行如此大的汰換工程首要面對的挑戰是如何在舊系統不停供且不影響運轉下進行新系統擴充設計以及新舊系統電控運轉邏輯差異如何無縫接軌,以及最重要的是在設計及擴充工程完成後要如何在不影響供應水質的情況下無感導入擴充系統及停止運轉舊系統。在200mm晶圓廠廠務設備全面翻新的浪潮中,面臨產線對供應穩定度的挑戰下舊廠區翻新要如何在持續供應純水並維持水質的穩定下進行新建系統的試俥、投入以及達成舊系統的切換及下線便成了多數翻新計畫的首要難題。
FAB6預計進行翻新的系統為純水製程中段的脫氣單元,超純水系統中對於氧氣和二氧化碳等水中溶解性氣體的去除,TSMC的水處理系統目前可見到兩種不同的處理單元: 高效率真空脫氣塔(High efficiency Vacuum degasifier, HE-VDG)以及薄膜脫氣系統(Membrane Degasifier, MDG)。在較早期建置之少數200mm晶圓廠超純水製造工藝中常見採用高效率真空脫氣塔作為除氣手段。但隨著晶圓製造產線對於廠務系統穩定度要求的提升,真空脫氣塔系統由於其脫氣塔維護困難以及單一元件失效便容易導致供應中斷的缺點,導致現今300mm晶圓廠超純水系統中多改採薄膜脫氣系統作為替代。
2.文獻探討
2.1 高效率真空脫氣系統
傳統真空脫氣塔工作原理設計是利用當維持負壓環境使密閉系統液面氣體壓力降低時,氣體溶出液體的速率增加達成更低的氣體溶解度(圖1)[1],真空泵將脫氣塔抽氣至真空後,利用水泵泵送水從塔槽槽頂噴淋而下,經過濾料分散後水中之氣體將逸散並被真空泵抽離,脫氣後的水流至塔底再由中繼水泵泵送至下一處理單元,然而此種方式需要耗費極大的能量維持較高的真空度。為提高脫氣效率,高效率真空脫氣塔利用在真空脫氣機中注入微量氮氣等惰性氣體從而可高效去除水中溶解氣體,其會從塔槽底部注入微量氮氣等惰性氣體並由脫氣塔上部經真空泵抽離,此時塔內純水將因亨利定律(圖2) : 常溫下氣體溶解的體積莫耳濃度將和與該溶液上的氣體分壓成正比,從而溶解入氮氣並更為高效的脫除所有其餘諸如氧氣、二氧化碳甚至是高揮發性有機物等溶解氣體。
圖1:低壓時液體具更低氧氣溶解度
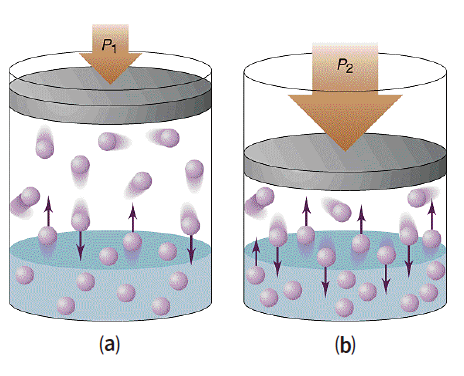
圖2:高含氮環境可使液體具更低氧氣溶解度[2]

高效率真空脫氣塔的結構較為複雜,包含了脫氣塔、真空泵、水泵等。為保證進水分布均勻,脫氣塔通常設計高達十幾米以提供足夠的濾料高度使水氣良好分布,這也導致了其設備佔用空間龐大且難以停機維護,另外脫氣塔需要較為精準的液位控制,如果液位過高容易導致脫氣效率下降,但液位過低卻容易導致水泵空抽跳脫引發停機事故。這樣的複雜構造導致整套系統對控制元件需要有較高度的冗餘設計(redundancy),並且在突發性運轉狀況出現時較仰賴有經驗的操作人員去進行查修及復機。
相較於先進廠區系統,FAB 6在中處理去礦化單元序列採用Christ系統架構(圖3),是由VDG、UV滅菌燈、MGR混床樹酯塔順序所組成,VDG單元包含PST水泵、真空脫氣塔及其脫氣設備、定頻控制之出口增壓水泵,設計處理效能為在供應水量366CMH狀況下可提供平均1ppb以下溶氧值,並且在增壓水泵出口設計有比例式控制回流閥回水至PST,除使其壓力穩定供應在6.5bar外亦可在後段需水量較低時持續循環提升PST供應水質 。在穩定供應二十餘載的背後由於VDG單元脫氣塔為單一設計,運轉至今都尚未進行內部桶槽完整檢測及拉西環更換,導致在近年陸續發現MGR樹酯塔入口散水管遭破碎的拉希環碎片堵塞而令壓差爬升。並由於FAB6 共有兩組相同架構的產水序列: Line A及Line B,為了能互相備援所以在MGR樹酯塔產水出口設計有管路聯通,這使得樹酯塔在壓差爬升時兩個Line的出口產水壓力不均等,過高的背壓也使得供水難以克服往後高約6米的管橋段來回高程差(0.8~1.2bar)進而影響後段供水量的穩定度。
圖3:HE-VDG系統設計
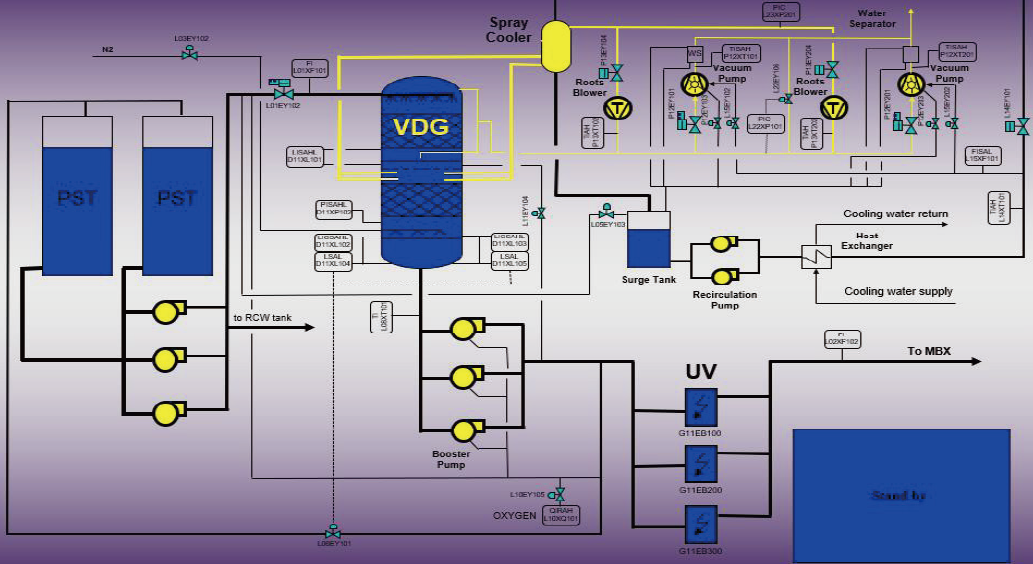
2.2 薄膜脫氣系統
薄膜脫氣系統主要仰賴脫氣膜目標性的移除水中氣體,一般用於水中溶氧去除使用的脫氣膜膜殼內包含了大量疏水性介面的中空纖維半透膜,利用其允許氣體通過但阻攔液體的特性,在半透膜的一側流通液體另一側通入高純度氮氣等惰性氣體便可在兩相互不接觸的情況下遵循亨利定律達成氣體交換(圖4)。與脫氣塔利用拉希環創造水氣分布空間相比,中空纖維膜可利用其更大的交換表面積達成整體系統體積的縮減,此外也可以利用多段的脫氣膜串聯達到更佳的氣體去除效果,這使得薄膜脫氣系統可以在有限的空間下更好的依照可使用空間及方便人員維護的高度進行系統建造。
圖4:脫氣膜作用原理示意[3]
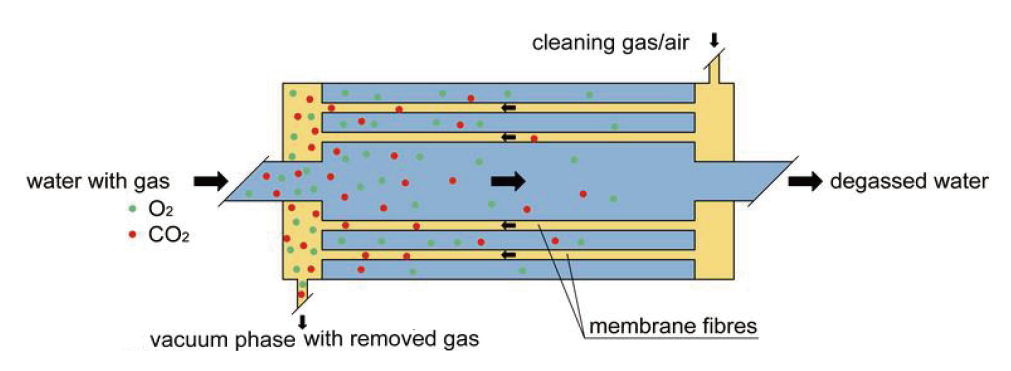
薄膜脫氣系統架構一般僅由供水泵、真空泵及脫氣膜組成,其簡單的架構及較小的系統體積使突發異常狀況時操作人員較容易進行查修及復機,此外在冗餘度的設計上因為脫氣系統是由多段的脫氣膜串並聯組成,這使得系統可以允許在不停止供應的情況下逐套進行保養及更換耗材。兩者差異比較整理可見表1,同真空脫氣塔相比,薄膜脫氣系統雖然在對水中有機物去除效能較差及耗材價格上較貴,但考量其操作體積較小、系統操作靈活度高及對操作人員的經驗要求較低,目前TSMC廠區純水系統脫氣單元設計多捨棄脫氣塔而採用脫氣膜。
VDG | MDG | |
---|---|---|
初設成本 | 高 | 低 |
運轉成本 | 低(無耗材) | 高(半透膜汰換成本約2.3M/年) |
佔用空間 | 大。為達成足夠接觸面積需較大真空容器 | 小。真空纖維膜體積小接觸面積大 |
擴充性 | 難以擴充 | 模組化易擴充 |
去除有機氣體能力 | 較好。可廣泛適用潔淨度較低水源 | 較差。脫氧膜具選別性,需就處理水源特性選擇合適MD |
啟動時間 | 較久(>1小時)需預先建立真空環境才可產水 |
快速 (30min內 in SPEC.) 接觸面積大,無預抽真空需求 |
操作難易度 | 較困難(須兼顧上下層真空度) | 簡單(僅須注意啟動水錘) |
適用環境 | 來源水質不穩定、追求低運轉成本ex.油氣產業、回收水 |
對24小時生產不中斷需求高的產業 ex. 晶圓廠、電廠 |
2.3 FAB 5 翻新經驗借鑑
科學家牛頓曾說過,「如果說我看得比別人遠,那是因為我站在巨人的肩上。」,本次MDG的擴充工作可以順利進展也多所仰賴其他廠的翻修心得,FAB5在MDG擴充上的先行經驗給了我們許多良好的參考。舉要點論述如下:
❶ 以外掛方式擴充新建系統
在FAB5進行MDG擴充時,為達成產線供應不中斷是先將新建系統以併聯外掛方式運轉及投入,如此便可避免與原系統的干涉過多影響控制及操作參數的調整。
❷ 採用Christ系統架構成功運行
原先以目前300mm新廠區流程來說,純水中處理流程主要採用先過混床樹脂後再進脫氣單元(MDG),但FAB5亦分享其沿用Christ系統架構: 先進脫氣單元(VDG)後再到混床樹脂的方式,水質狀態也可良好運轉。
❸ 快速上線經驗之工法學習
另外FAB 5 在完成MDG系統設置完成尚未投入前,預先進行低流量flush 幫助清洗模組並同時確認水質狀況,在APM完成管路修改直接投入系統運轉,完全無影響水質狀況,綜上經驗,FAB6藉由這些分享有效縮短評估流程及實際施工期程。並在系統建置試運轉時,能夠有更大的決心及靈活度可在原有系統不停水狀況下投入MDG供應。
3.研究方法
3.1 FAB 6架構及翻新設計
在MDG系統的硬體設計上,我們採納FAB5經驗計畫建立可獨立運轉並聯於既有VDG系統的外掛型設計(圖5),並且在產水單元序列部分由於同屬Christ系統,我們也採用相同設計於PST桶槽出口預留點增設水泵送水進擴充之MDG系統,在產水側則設計有追載MGR樹酯塔出口壓的變頻增壓水泵在一定壓力控制範圍下將水送進UV滅菌燈、混床樹酯塔,如此便可使整個去礦化處理單元能維持穩定克服高程差的供水壓力。此外在3M Liqui-CelTM脫氧膜的規劃上我們採用了3組一串共10串互為並聯,設計產水量達380CMH的N+1設計,加大設計水量及並聯分串架構使得人員可以在不需停水下隨時切離部分膜組進行保養及查修(圖6),同時也參考FAB 5經驗讓我們可以在一邊配管安裝時一邊分段低壓潤洗各串MD模組,大幅節省後續試運轉工期。
圖5:FAB6 UPW中處理去礦化單元架構示意圖
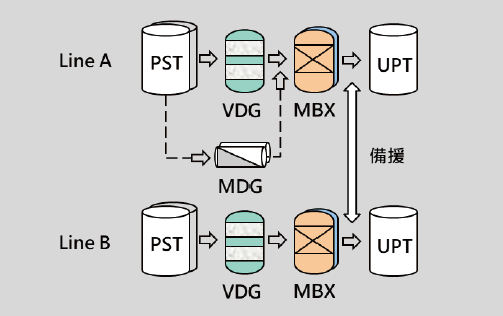
圖6:MDG系統脫氧膜並聯設計P&ID圖
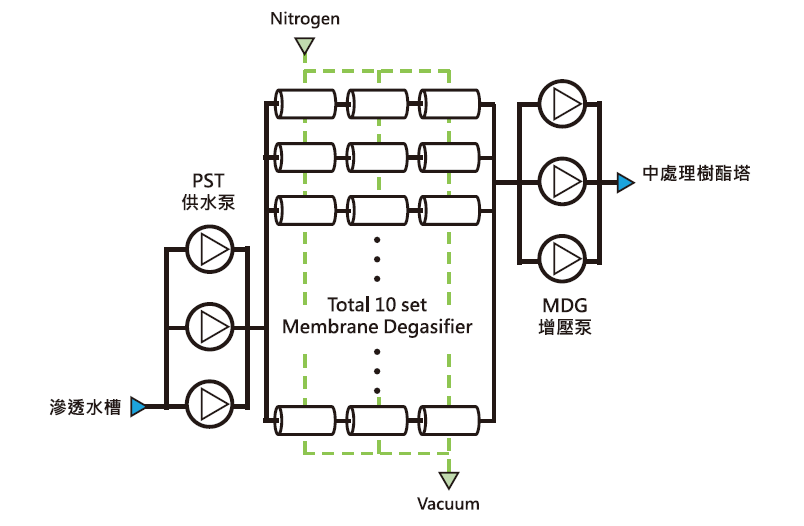
在軟軔體的設計上,為避免再對既有系統複雜的PLC邏輯進行修改而產生極高的投入風險,我們採用獨立PLC的架構以新擴充的PLC控制MDG運轉,並考量後段只需要MBX樹酯塔重要閥件有開啟使MDG產水時管路不蓄壓即可,在新舊系統的橋接上便設計使新PLC透過乙太網路讀取舊系統的開閥訊號,並建立閥沒開啟或異常關閉時設定為MDG啟動條件,如此便可避免蓄壓爆管的風險,並且在舊系統需先啟動完成才能啟動MDG新系統的架構下,在後續進行舊系統邏輯變更及試俥時也較為簡單,只需要關閉不再需要運轉單元的邏輯及互鎖條件確保舊系統可正常啟動,不需考量要新系統運轉邏輯加入到既有程式中是否會影響運轉。
3.2 困難點與解決方案
就如同老屋翻新遠比新屋裝潢來得複雜,既存的UPW系統要在一邊運轉的情況下一邊進行系統的擴充及拆除勢必會遇到許多困難點,在這次以外掛併聯方式新建系統並投入上線的過程中,我們主要遇到的困難點羅列如下:
❶ 需要在舊系統持續供應下不影響水質的進行新系統試俥及上線
由於產線端對於穩定供應的壓力,既設廠區在導入新系統時最大的困難就是在不停止舊系統運轉下讓新系統同步試俥上線完成取代,因此新系統如果是計畫採用外掛方式建立者通常都會離線運轉循環至水質正常後才投入上線。有鑑於純水系統對於水中溶氧及氣體不純物的敏感度,脫氣單元的試俥及投入更是不容有失,我們在試俥計畫中主要將系統切分成兩大部分: 硬體功能試車以及軟體控制試俥,硬體功能試俥部分最主要是計畫藉由將產水管段連接到臨時循環回水管路或水溝,以手閥限流下手動啟動動力系統進行低壓產水試俥,確認水質可達標準後再逐步開啟產水總閥投入至線上。軟體部分試俥則是透過現今新PLC支援透過乙太網路撈取資料的功能,讓我們可以在新PLC聯入相同網域後撈取既有PLC狀態點建立模擬試俥環境去off-line比對修改的邏輯有無問題,這使得在實際導入時出現邏輯錯誤的風險可以有效降低,也讓自動控制導入試俥時間可以大幅縮短至非歲修時段便可完成。
❷ 需要將舊系統PLC邏輯在持續運轉下部分停機卻不影響供應
新舊控制邏輯的橋接在整個翻新案中可說是最令人頭疼的問題,舊有的控制邏輯編寫之初為了保護系統不要出現硬體損傷及難以短時間復歸的狀況,便加入了許多的互鎖條件(interlock active)使得整個中處理系統會在VDG單元跳脫時也全部停機。新擴充的MDG單元為避免在已經夠複雜的舊程式中加磚添瓦的新增控制邏輯所以採用獨立PLC硬體、邏輯,而為了整合新舊PLC程式,除了將後端MBX未開閥的互鎖訊號傳回MDG PLC使其在舊系統完全啟動後才會接續啟動避免擴充系統影響既有系統運轉外,也需要對需要停機的舊系統相關PLC互鎖邏輯進行剔除。為避免在程式更新時造成系統意外停機,過往擴充經驗多是仔細逐條省視階梯圖以正面表列挑選出所有相關的互鎖條件,但在此案中我們也參考了過往各廠翻新PLC的換頭案: 使用灌有新程式的測試用PLC抓取現場正在運轉的PLC I/O讀值進行運算以比對新舊程式差異(圖7),我們在每次的更新上線前先透過網路抓取現場實際數值交由灌有新邏輯程式的測試機PLC運轉進行除錯,此舉除了能有效避免因人工省閱階梯圖邏輯時的疏漏造成意外停機的風險以及節省大量點對點測試時間,也可以透過直觀的新、舊PLC運轉結果比對,在完整的移除相關VDG interlock條件並避免其餘部分程式於VDG停機後運轉異常。
圖7:通過乙太網路建立測試環境可進行即時測試及比對
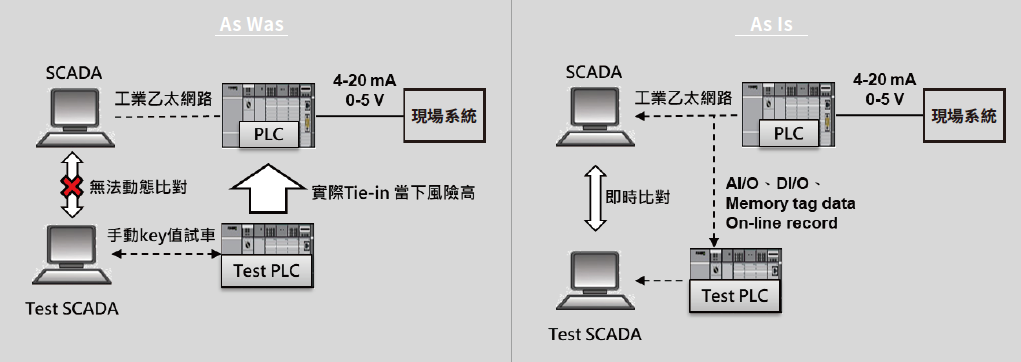
❸ 極短的工期及切換自動運轉上線的風險控制
從MDG系統擴充發包到正式上線耗時16個月(2021/03~2022/07)期間跨越了一次停水歲修及一次不停水歲修,但扣除其中許多的長交期料件待料時間實際施工時間被壓縮至不到8個月,其系統上線的施工進度可謂是相當緊湊,除必要在停水歲修時才可裝設的入水主管三通外,為了達成工進目標其餘系統試俥、產水上線都安排在不影響後端供應水質的情況下線上投入。為了確保工程進度能跟上,我們在這次翻新中於各主管段高點開闢排氣點,每完成一組管段便開始分段潤洗使得配管完成時也近乎完成潤洗以最大縮短清洗時間,此外由於不停水歲修時間遠早於自動控制試車完成期限,參考風險分級後我們為把握該次歲修機會也調整工序加快完成硬體配置並於當天進行較高風險的手動強供送水,並在後續藉由詳細分解各投入步序及風險,在不影響供應穩定的情況下於平日時按表操課指揮人力,如預期地轉換手動強供為自動控制順利完成整體系統線上投入。
4.結果分析
4.1 翻新成果
在全課同仁的通力合作下,FAB6 Line A UPW系統脫氣單元成功在2022/07完成翻新投入並在2023/03 APM時完成舊有VDG系統停止運轉,期間產線供水水質皆維持穩定供應未造成影響,也沒有因為工程造成系統停機的事故,得以證明前述對應三大風險的解決方案有效的發揮其作用。
而在完成翻新後我們主要獲得的效益是能將「維修風險化整為零」,如圖8比較所示,既有的真空脫氣塔由於體積龐大導致只能放置戶外也難以有冗餘設計,其上元件也受影響不僅在戶外失效機率高維護檢修也非常不容易造成了穩定供應的挑戰,在成功翻新為MDG後整體系統大多放置室內環境較好也容易進行維護操作,且最重要的是N+1的脫氣模組設計使得整個脫氣單元不像以前無法部分停機而可以進行不停水維護,讓整個系統的保養可以常態化、平日化。
圖8:FAB6 UPW Line A 脫氣單元翻新前後差異
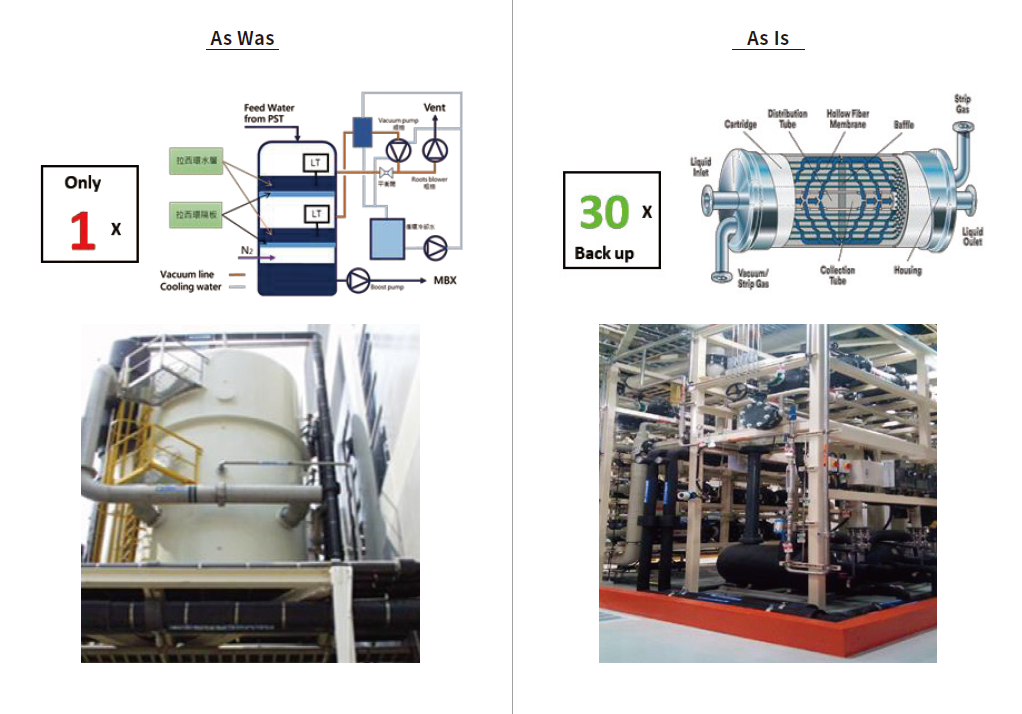
此外由於強供應變流程的優化,過去使用VDG系統時強供復機需要同時關注閥件、塔內液位、真空系統、轉動設備等多種條件,使得需要有豐富經驗的人員才有辦法在約20~30分鐘左右執行完成。而在MDG控制邏輯方面,改為MDG系統後不僅在程式控制就納入了停機條件復歸自動復機的功能,強供也僅需要關注在閥件是否正確開啟從而大幅縮減了強供時間至10分鐘內可完成,這主要拜其元件組成簡單且有經過豐富的offline PLC邏輯模擬試俥除錯所賜,除了EMO按鈕外其餘包含避免爆管後端閥件未開啟自動停機機制以及泵浦低壓保護等互鎖訊號都可以設計為訊號復歸後會自動進行復機步序,並為了方便值班人員可以快速進行異常狀況停復機,除了一鍵起停機按鈕外也加上可以轉手動強供的設計,這些改善使得我們在面對製程對穩定供應需求的挑戰時能夠有更大的把握。
4.2 設計巧思
在本次翻新中,筆者認為最能提供給其餘廠區作為翻新參考的巧思便是前段所描述的分段潤洗規劃,在原本系統商提出的管路計畫為整體管路完工後再執行潤洗一周,但在考量時間壓力下經過討論後決定: 一邊配管的同時一邊在主管段分段高點增設多個排氣閥,使每天配管收工後便可立即開始潤洗當天配置的管路段,這是一個極低成本的工法,除了可以爭取到許多時間外亦可在未來有停水進行管路維修時提供方便的洩壓潤洗路徑。
同時在PLC試俥方面也有值得借鑒用於往後翻新工程的嘗試,那便是利用新PLC支援透過乙太網路撈取資料的功能建立模擬試車環境off-line進行邏輯程式運行試車,這樣的工法未來不論是應用於系統擴建、新建PLC站點或舊系統汰換翻新PLC都可以用得上,在測試用PLC運行測試邏輯並設定相關點位去抓取舊有正在運轉的PLC DI/O、AI/O資料後觀測其off-line輸出指令是否如同預期變化,此舉除了能夠直觀比對新舊兩套邏輯運轉的差異比較外,也可以在模擬環境將可能的運轉風險狀態參數輸入去模擬緊急應變時的系統狀態,能夠大幅降低PLC切換投入風險。
5.未來展望及結論
在完工的喜悅後,我們也是發現了一些可以再改進的部分可供未來Line B MDG 擴充或者它場借鑑,其中最難以處理的部分是電盤設計的缺陷,本次採用的電盤架構為節省占地便將MCC動力盤與控制盤整併為一盤並以電木板分隔,然而這樣緊湊的設計架構也使盤內溫度常居高不下,這也導致有電控元件加速衰退的風險在,為此後來我們變更電盤的散熱設計,由原先的盤面風扇機械送風降溫改為是外掛冷氣降溫,此舉也成功使電盤溫度有7~10度左右的降溫成效(圖9)。
圖9:改善後電盤溫度由35~48度降至28~42度
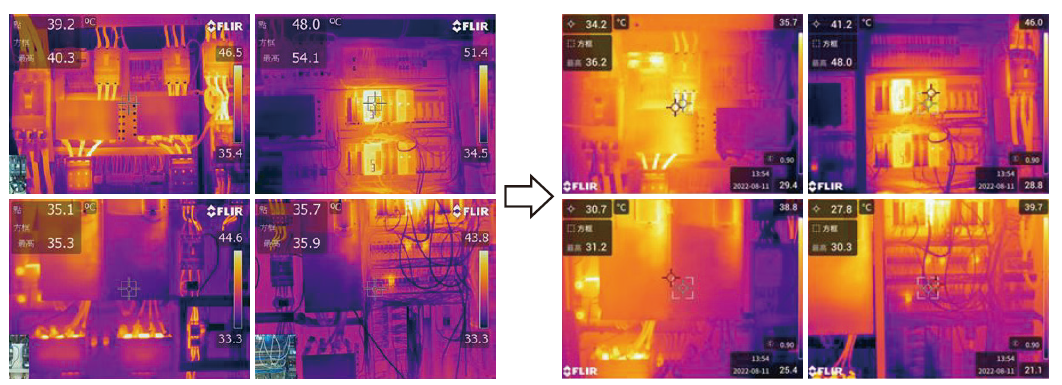
此外還有一點重要的設計檢討便是我們由於空間侷限性為了盡可提升坪效便將部分MD膜組及真空管路置於低過真空泵浦入口高度,這使得我們會需要設計一個定期於管路低點排水的自動閥組,然而若是閥件動作失效導致管內積水干擾真空度將會影響產水品質。因此我們除了在閥件安裝極限開關監視開啟狀態訊號回傳外,也建議未來如有類似的翻新需求最好是將MD模組及真空管路高度盡量抬高過真空泵浦,使其在建立真空時可一併移除多餘水分避免類似風險存在。
在製程品質需求迭代提升的挑戰下,由於VDG較差的可維護性及較高的因單一元件失效造成純水系統停機風險,其逐漸讓MDG此一脫氣單元的設計所取代。而在評估MDG系統擴充時除參考300mm 設計架構外,本次FAB6在翻新時所使用到的各種巧思、檢討與工程思維希望可以成為各廠進行翻新評估時的參考,相關整理比較表格請參閱表2,尤其在於產能趨緊下維修保養時間越來越寶貴,如何在爭分奪秒的歲修時間達成最大的翻新效益,以及如何評估風險分級在不影響產線的情況下進行擴充系統的工程、試俥、投入等規劃,是既設廠區也逐漸需要面臨的問題。屆時希望此期介紹FAB6在MDG翻新所做得分享經驗可以作為借鑑幫助各廠突破翻新規劃時所遇到的各種困難。
本次翻新設計 | 300mm 設計 | |
---|---|---|
單元架構 | 沿用Christ架構系統,MD→UV→MBX→UPT | UV→SBP→MD→UPT |
MD 膜架構 | 臥式擺放,較節省空間 | 立式擺放,便於人員維護 |
泵浦架構 | MD入出口各有一組泵浦,MBX舊系統完全啟動後跟隨啟動,適用Christ架構系統 | 僅MD 入口一組泵浦,隨後段SBP |
PLC架構 | 中處理單元/MDG獨立PLC,便於進行部分系統擴充或汰換 | UPW 系統統一一組redundancy CUP PLC控制,便於維護成本較低 |
電盤架構設計 | 控制/動力受空間限制組於同一盤面,有訊號干擾風險及散熱問題 | 控制/動力分盤 |
電盤冷卻設計 | 開放式環境受限無環境降溫,電盤外掛空調進行盤內降溫 | 隔出電盤隔間,環境由MAU/AHU統一降溫 |
試俥前潤洗 | 通過多個預留排氣閥進行分段潤洗,時間較節省適合成熟廠區翻新使用 | 統一於配管完成後送水潤洗 |
試俥上線模式 | 低壓潤洗至水質通過後,逐漸建壓及開關閥於不影響既有系統水質下線上投入 | 循環至水質通過後直接上線 |
排水設計 | 受空間高度限制導致部分U型管路需由氣動閥排水,具設備失效風險 | 全MD膜架高由真空泵抽除 |
參考文獻
- http://ch302.cm.utexas.edu/physEQ/solutions/selector.php?name=henrys-law
- https://www.google.com/url?sa=i&url=https%3A %2F%2Fwww.youtube.com%2Fwatch%3Fv%3DZ_CU9b89w_w&psig=AOvVaw3TYNe_hYk8K1qekNOXn8XC&ust=1674093115976000&source=images&cd=vfe&ved=0CBEQjhxqFwoTCKDjz_2A0PwCFQAAAAAdAAAAABAk
- https://www.hydrogroup.biz/products/process-water-treatment/membrane-degassing.html
留言(0)