摘要
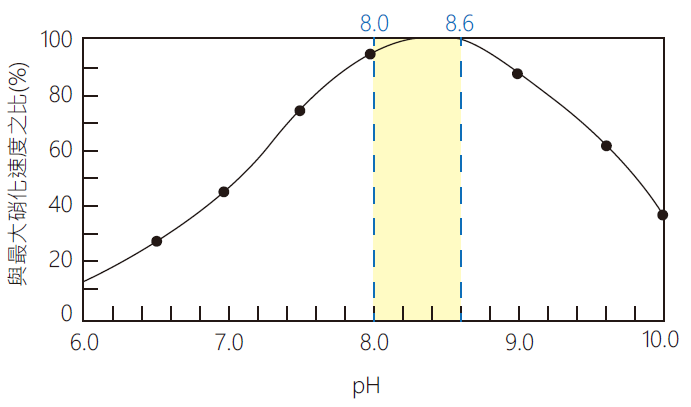
廢水生物處理系統運轉精進與實務
Keywords / Biological Treatment3,Chemical Oxygen Demand2,Membrane Bioreactor2
前言
因應製程廢水性質改變,廠務廢水系統由物理化學原理處理無機廢水,慢慢轉變為利用微生物處理有機污染廢水,如此才能符合園區廢水放流納管標準。本文以先進製程廠區廢水生物處理系統為研究對象,分享試車、運轉等寶貴操作經驗,以期作為其他廠區參考。
文獻探討
2.1廢水生物處理原理
源自自然的處理程序,利用微生物代謝作用去除廢水中溶解性與膠體有機物質,被去除的有機物質轉換為生物體,藉由沉澱分離及排泥而去除[1]。處理方法可大致分為好氧處理、無氧處理及厭氧處理等三種,如 圖1,生物好氧處理可再細分為多種方法,例如活性污泥法、氧化深渠法、生物轉盤等,本文研究對象即採用活性污泥法結合薄膜生物反應器,主要目的為處理化學需氧量問題;生物無氧處理以脫硝脫氮程序為主,本文另一研究對象即採用此程序處理氨氮問題;厭氧處理非本文研究內容,在此不予討論。
圖1、廢水生物處理方法分類
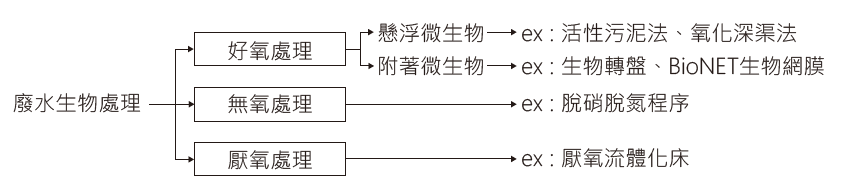
2.1.1 活性污泥法
活性污泥內含細菌、真菌、原生動物、後生動物等微生物,持續攝取水中有機物質,進而生長出許多微生物群 ,並與泥土顆粒結合成膠羽,有機物會與膠羽或微生物接觸,當強制曝氣供給大量氧氣時,有機物會快速被微生物利用,產生二氧化碳與水,達到淨化水質目的。主要處理設施由曝氣槽、曝氣設備、迴流污泥及最終沉澱槽等所組成,如 圖2。
圖2、活性污泥法流程示意
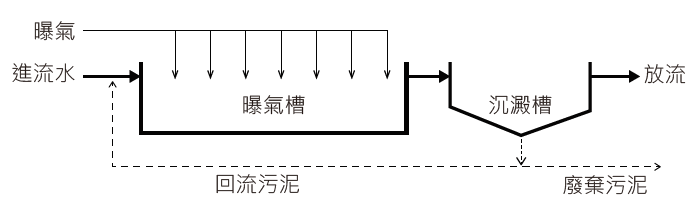
2.1.2 硝化脫硝程序
如 圖3所示,廢水中的氨氮可利用生物處理方式有效去除,主要機制包含兩個步驟,分別為硝化(Nitritation/ Nitratation)與脫硝(Denitrification)。氨氮經硝化菌好氧硝化反應,產生亞硝酸鹽氮與硝酸鹽氮,後續額外添加碳源 ,並由脫硝菌進行無氧脫硝分解後,還原為氮氣。另外, Anammox厭氧氨氧化微生物為一生長緩慢且馴養不易之微生物,必須有嚴謹的控制策略才能馴養成功,此技術目前應用上有一定難度,且非本文研究內容,在此不予討論。
圖3、活性污泥法流程示意[2]
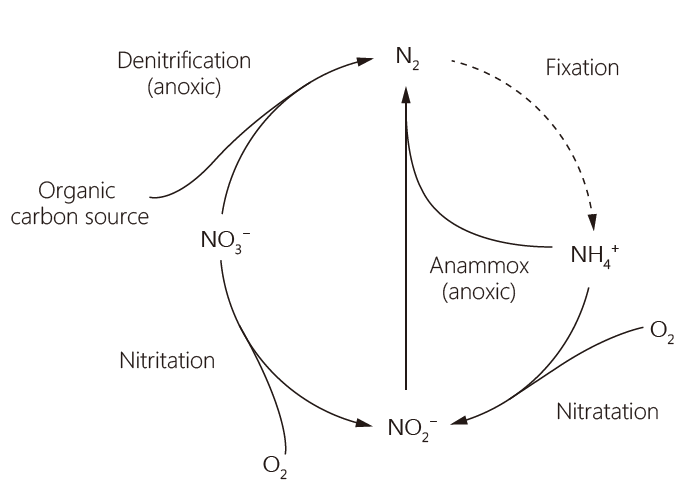
2.2薄膜生物反應器
活性污泥法處理水質易受膠羽沉澱性質影響,污泥常有上浮狀況,且佔地面積大。將薄膜與傳統生物處理結合而成的薄膜生物反應器(Membrane Bioreactor, MBR)可提高過濾及分離效率,取代最終沉澱池,為較新的生物處理技術。與傳統活性污泥程序相比,薄膜生物反應器具有處理水質佳、操作彈性大、佔地面積小等優點[3],同時能承受高污染物負荷與尖峰負荷變動,其優缺點比較如 表1。薄膜生物反應器主要功用為固液分離,依據薄膜放置位置可分為沉浸式與外掛式,依薄膜膜組可區分為四種型式,平板式、管式、螺旋式及中空纖維式。本文研究對象採用沉浸式薄膜生物反應器,膜組選用中空纖維式,實際照片如 圖4。
空間需求 (註1) |
污泥濃度 (註2) |
處理後水質 (註3) |
電力消耗 (註4) |
|
---|---|---|---|---|
傳統活性污泥法 |
大 |
低 |
不穩定 |
低 |
薄膜生物反應器 |
小 |
高 |
穩定 |
高 |
說明 |
註1 薄膜生物反應器不需沈澱單元,可大幅節省空間 註2 污泥濃度高,可承受較大的負荷濃度變化 註3 薄膜生物反應器可完全截留污泥,沒有傳統程序污泥易上浮的問題 註4 薄膜生物反應器需進行曝氣及定時反洗,會有額外的能源消耗 |
圖4、薄膜生物反應器實際照片
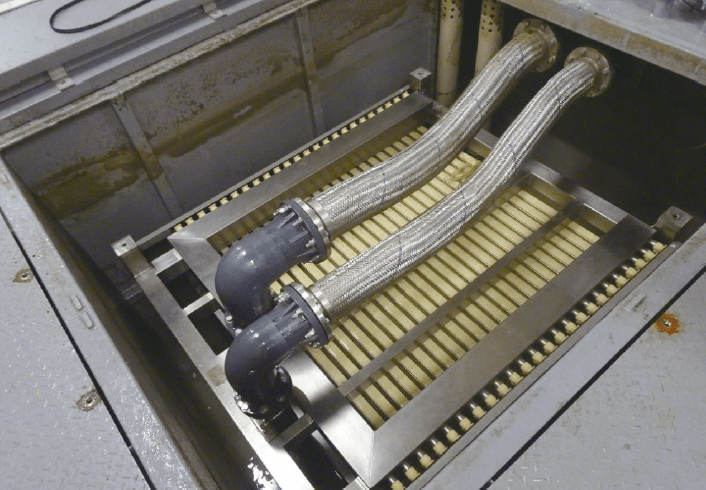
研究方法
3.1系統流程
先進製程廠區廢水生物處理系統分兩個部分,如 圖5 ,高濃度化學需氧量的高階製程有機廢水進入AOR生物處理系統,單元組成包含調勻槽、活性碳、pH調整槽、無氧槽、曝氣槽、薄膜生物反應器及逆滲透膜,經系統處理後供給次級用水回收使用;化學需氧量及氨氮同時存在的廢水,例如低濃度氫氟酸廢水以及濕式廢氣處理設備廢水,則是進入SALIX生物處理系統,其系統單元包含調勻槽、活性碳、pH調整槽、曝氣槽、無氧槽及薄膜生物反應器,經系統處理後外排放流。
圖5、先進製程廠區廢水生物處理系統流程
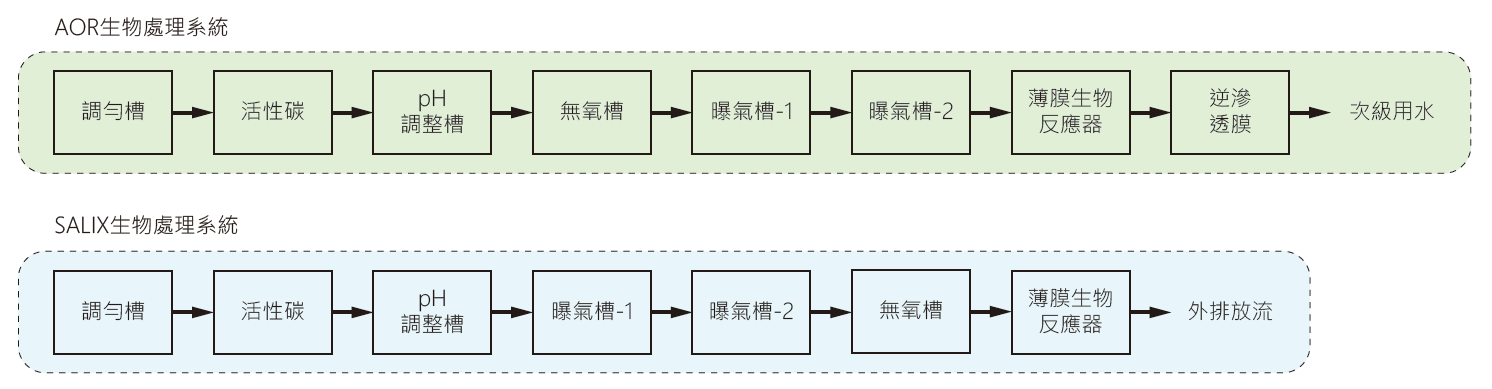
3.2選擇植種來源
廢水生物處理系統啟用時,會取用相似產業的生物污泥進行植種,經過汰換代謝形成合適污泥。先進製程廠區曾選用北部某面板廠生物污泥作為植種來源,植種後化學需氧量去除率不彰,改為中科園區污水廠後,化學需氧量去除率立即提升至90%。分析差異點在於取泥位置,如 圖6,北部某面板廠於污泥濃縮槽取泥,槽體為缺氧狀態且停留時間過久,污泥已失去活性;中科園區污水廠由污泥沉澱槽取泥,污泥活性較佳。
圖6、植種取泥位置影響示意
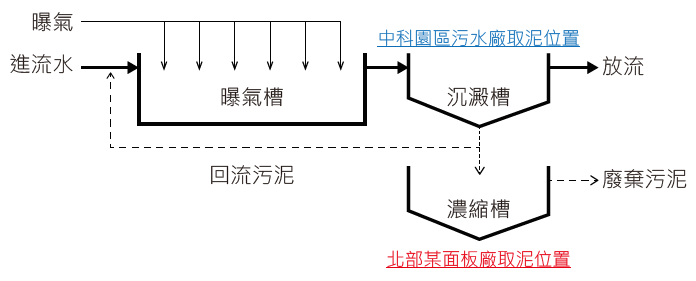
另外,可用實驗驗證污泥是否有去除效果,如 圖7,以廠區廢水與生物污泥混合進行曝氣,量測曝氣前後化學需氧量讀值。由當時實驗結果得知,如 表2,中科與南科園區污水廠污泥皆有化學需氧量去除效果,因此評估就近選擇南科園區污水廠污泥作為植種來源。
圖7、去除效果確認實驗照片
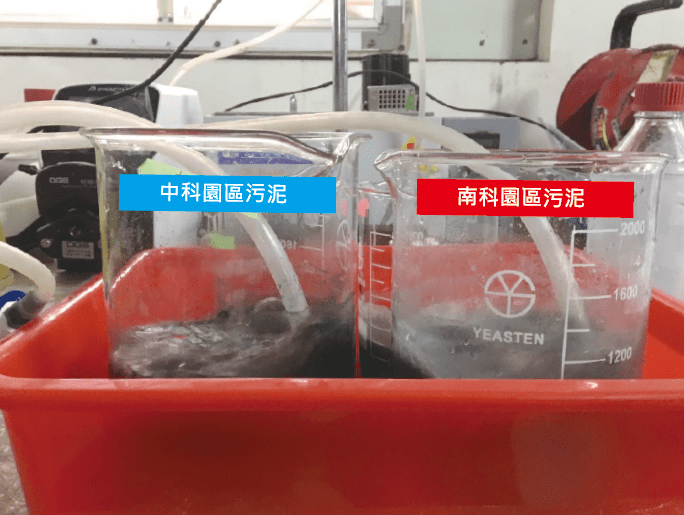
組別 |
項目 |
化學需氧量(mg/L) |
|
---|---|---|---|
Before |
After |
||
第一組 |
0.7L純水+0.3L南科園區污泥 |
62 |
39 |
第二組 |
0.7L原水+0.3L南科園區污泥 |
278 |
45 |
第三組 |
0.7L純水+0.3L中科園區污泥 |
50 |
30 |
第四組 |
0.7L原水+0.3L中科園區污泥 |
281 |
42 |
3.3營造生長環境
良好的生長環境可縮短生物馴養期,使系統運轉效能穩定,以下依文獻建議結合實際運轉經驗,列舉出雙氧水濃度、pH、溶氧、混合液懸浮固體濃度、碳氮比、食微比等六項影響微生物生長的關鍵指標,並整理於表3、表4。
AOR生物處理系統 |
||
---|---|---|
處理單元 |
指標 |
操作範圍 |
調勻槽 |
食微比 |
0.1~0.3 kg COD/kg MLSS*day |
活性碳 |
雙氧水濃度 |
0mg/L |
無氧槽 |
pH |
7~8 |
溶氧 |
0mg/L |
|
混合液懸浮固體濃度 |
6000~8000mg/L |
|
曝氣槽-1 |
pH |
7~8 |
溶氧 |
>1mg/L |
|
混合液懸浮固體濃度 |
6000~8000mg/L |
|
曝氣槽-2 |
pH |
7~8 |
溶氧 |
>1mg/L |
|
混合液懸浮固體濃度 |
6000~8000mg/L |
|
薄膜生物反應器 |
pH |
7~8 |
混合液懸浮固體濃度 |
8000~10000mg/L |
SALIX生物處理系統 |
||
---|---|---|
處理單元 |
指標 |
操作範圍 |
調勻槽 |
食微比 |
0.1~0.3 kg COD/kg MLSS*day |
活性碳 |
雙氧水濃度 |
0mg/L |
曝氣槽-1 |
pH |
7~8 |
溶氧 |
>1mg/L |
|
混合液懸浮固體濃度 |
6000~8000mg/L |
|
曝氣槽-2 |
pH |
8.0~8.6 |
溶氧 |
>2mg/L |
|
混合液懸浮固體濃度 |
6000~8000mg/L |
|
無氧槽 |
碳氮比 |
<3 |
pH |
7~8 |
|
溶氧 |
0mg/L |
|
混合液懸浮固體濃度 |
6000~8000mg/L |
|
碳氮比 |
>4.5 |
|
薄膜生物反應器 |
pH |
7~8 |
混合液懸浮固體濃度 |
8000~10000mg/L |
3.3.1 雙氧水濃度(Concentration of H2O2)
雙氧水為氧化性物質,高濃度雙氧水進入無氧槽或曝氣槽,將造成微生物大量死亡。高階製程有機廢水中雙氧水濃度約有10~100mg/L,因此在調勻槽及活性碳出口皆須有分析儀器監控雙氧水濃度,並適量添加除氧酵素,確保進入無氧槽或曝氣槽時,雙氧水濃度能維持在0mg/L。
3.3.2 pH
當pH值大於10或小於4時,部分微生物將無法生存,文獻上建議活性污泥法pH宜控制在6.0~8.5間。以運轉操作面來看,有機物被微生物利用時會消耗鹼度,此時pH呈現下降趨勢,需於曝氣槽適量添加氫氧化鈉提升pH,因此實際操作時會建議控制在7~8之間,避免pH落在不適當區間,造成系統處理效能下降。於曝氣槽添加化學藥品有一定風險性,過量添加恐導致微生物大量死亡,建議於pH調整槽將原水調整至偏鹼狀態進入無氧槽與曝氣槽,與回流污泥混合加上鹼度消耗後能剛好在中性狀態,減少在曝氣槽添加化學藥品。
水中含有氨氮時,需仰賴硝化菌在好氧環境下進行硝化作用,將氨氮轉化為亞硝酸鹽氮與硝酸鹽氮,後續再由脫硝菌進行無氧脫硝分解後還原為氮氣,其中硝化菌對於pH極為敏感,最佳pH範圍為8.0~8.6[4],若低於此範圍,硝化反應速率隨著pH下降而降低,當pH值低於6或高於10時,硝化反應幾乎接近停止,pH與硝化速率的關係如 圖8所示。
圖8、pH與硝化速率關係圖[4]
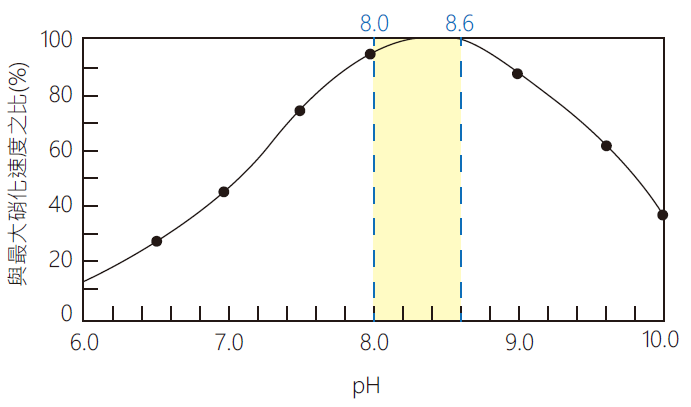
3.3.3 溶氧(Dissolved Oxygen, DO)
好氧微生物利用分子氧作為電子接受者進行代謝,將有機物最終氧化成穩定的無機物質(例如二氧化碳),並產生新的菌體,此時水中溶氧會逐漸下降,需透過強制曝氣維持一定溶氧值,將溶氧控制在大於1mg/L即可避免好氧微生物停止反應。若在無氧槽,通常僅靠攪拌機緩慢攪動避免污泥沉底,此時溶氧值應為0mg/L。
在硝化菌存在的曝氣槽中,溶氧的控制極為重要,通常水中溶氧愈高,則硝化反應速度愈快,一般控制在2 mg/L以上為佳[4],溶氧與氨氮去除率的關係如 圖9所示。
圖9、溶氧與氨氮去除率關係圖[4]
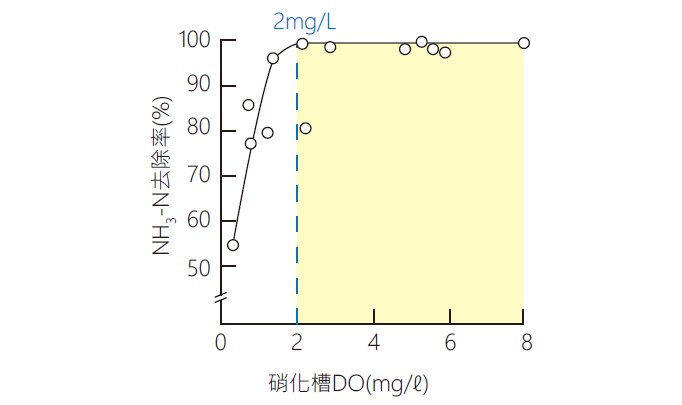
3.3.4 混合液懸浮固體濃度(Mixed Liquor Suspended Solids, MLSS)
混合液懸浮固體濃度為微生物數量指標,當系統單元有薄膜生物反應器時,會將污泥提濃回流至無氧槽及曝氣槽,故混合液懸浮固體濃度會比傳統活性污泥法高出許多 ,一般來說曝氣槽的混合液懸浮固體濃度會控制在6000~ 8000mg/L,若在三倍回流量的情況下,薄膜生物反應器的混合液懸浮固體濃度約會在8000~10000mg/L,其濃度關係式如 圖10所示。
圖10、混合液懸浮固體濃度推估關係式
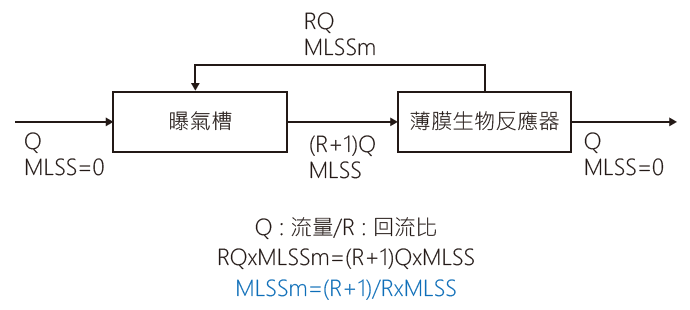
混合液懸浮固體濃度可以透過排泥來控制,去除1.0kg化學需氧量會產生0.3kg污泥,扣除無氧槽及曝氣槽1%污泥內消耗後,即可得知污泥增生量理論值,實務操作上會先以理論值的50%當作排泥量,觀察混合液懸浮固體濃度變化,再決定排泥量增多或減少。
3.3.5 碳氮比(Carbon-Nitrogen ratio, C/N)
碳氮比為化學需氧量與總凱氏氮的比例,是硝化脫硝程序的重要指標,其中總凱氏氮為氨氮與有機氮的總和。當碳氮比大於5,分解有機物的好氧微生物將會是優勢菌種 ,此時硝化菌幾乎不存在,必須等碳氮比小於3,硝化菌所占比例才會上升。在脫硝反應中,需額外添加碳源使碳氮比大於4.5,脫硝反應才會順利進行。
3.3.6 食微比(Food to Microorganism ratio, F/M)
食微比又稱為有機負荷,為每日流入曝氣槽的有機物量與曝氣槽內污泥量的比值,活性污泥法的食微比會控制在0.1~0.3kg COD/kg MLSS*day,計算公式如下:
F/M=Q*COD/V*MLSS
Q=流入曝氣槽水量(m3/day)
COD=流入曝氣槽廢水化學需氧量濃度(mg/L)
V=曝氣槽體積(m3)
MLSS=曝氣槽中混合懸浮液固體濃度(mg/L)
3.4冒泡因應對策
系統運轉常面臨曝氣槽冒泡問題,如 圖11,大量含污泥的泡沫由桶頂冒出至地面,導致現場環境髒亂,另外泡沫也會從抽氣風管吸入,風管內因此積水,抽氣量下降,造成現場異味逸散。探究原因可分為物化性泡沫及生物性泡沫兩種[5],物化性泡沫主要由油脂或界面活性劑造成,經確認生物處理系統進流水無此問題;生物性泡沫主因為微生物死亡,死亡原因可能為氧化性物質進入、未營造良好生長環境、污泥齡過高老化等。
圖11、曝氣槽冒泡照片
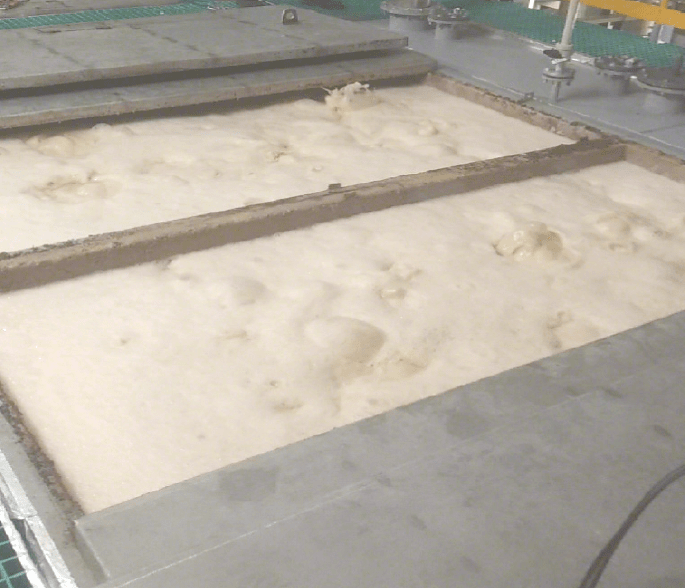
分為兩部分說明改善作法,如 圖12,短期解法包括定量添加消泡劑抑制泡沫產生,以及增設漏液檢知帶,冒泡發生時立即採取應變措施。長期解法部份包括調勻槽定量添加除氧酵素以及活性碳開啟運轉,避免氧化性物質進入生物槽;計算排泥量,每日固定排泥避免污泥老化;定義微生物生長關鍵指標,營造良好環境避免生物死亡。執行上述改善措施後,目前曝氣槽冒泡次數由每月4到6次下降至每月0到2次。
圖12、冒泡因應對策
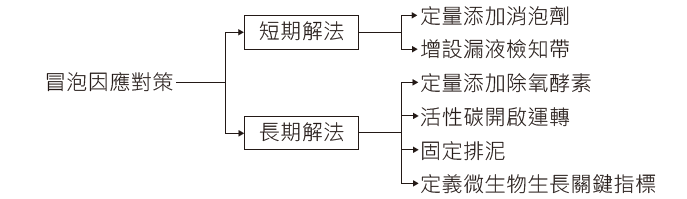
3.5進流水化學需氧量過高因應對策
先進製程廠區AOR生物處理系統設計水量為800CMD ,進流化學需氧量設計值為1,800mg/L,設計碳負荷為1,440kg,因製程機台使用有機化學品用量大增,運轉後發現高階製程有機廢水的化學需氧量濃度約在2,000~4,000 mg/L之間,為避免碳負荷超過設計值,必須降低系統進流水量來因應,部份高階製程有機廢水將無法處理,放流外排化學需氧量恐有超標風險(南部科學工業園區廢水化學需氧量納管標準為450mg/L)。
先前章節曾提到,脫硝程序需在無氧環境下額外添加碳源,一般業界大多額外購買甲醇、葡萄糖或異丙醇等化學品作為碳源添加,沒有加碳源時,進入無氧槽的硝酸鹽氮無法脫硝成氮氣,廢水放流的硝酸鹽氮有超標風險(南部科學工業園區廢水硝酸鹽氮納管標準為30mg/L),而廠區內的高階製程有機廢水含異丙醇,可視為現成碳源。因此以AOR生物處理系統設計碳負荷1,440kg為依據,將多餘無法處理的高階製程有機廢水泵送至SALIX生物處理系統無氧槽作為碳源,如 圖13,避免未經處理的高階製程有機廢水直接外排放流。
圖13、以高階有機製程廢水作為脫硝碳源
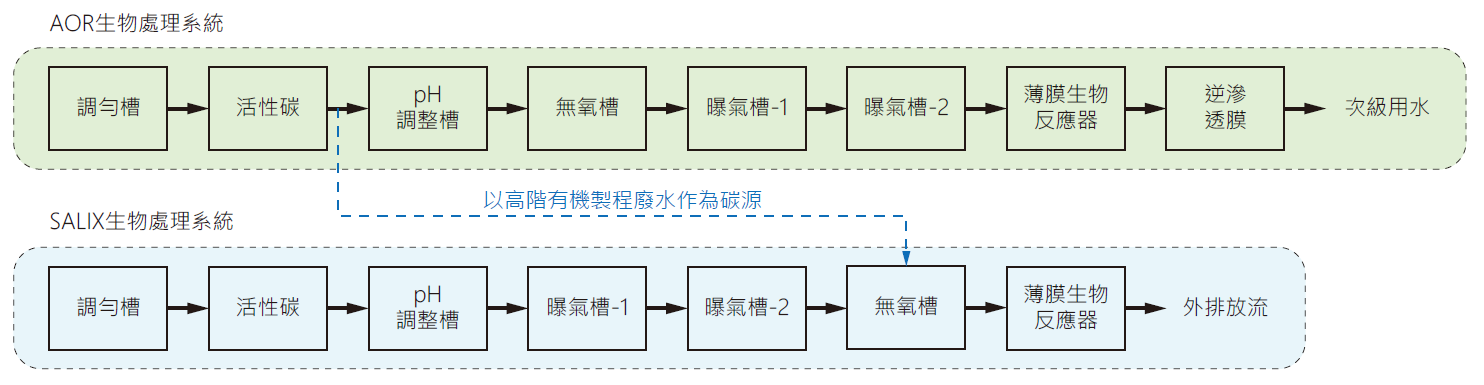
3.6薄膜生物反應器膜壓過高因應對策
先進製程廠區生物處理系統採用的沉浸式薄膜生物反應器,如 圖14所示,其產水屬於負吸揚程動作,負吸力驅動源來自泵浦,反洗與產水共用管路但路徑相反,屬正揚程動作,因此產水時透膜壓力為負值,反洗時透膜壓力為正值,薄膜生物反應器產水最大可承受透膜壓力為-60kPa,正常運轉時產水透膜壓力會小於-20kPa,反洗透膜壓力也會小於20kPa。
圖14、沉浸式薄膜生物反應器
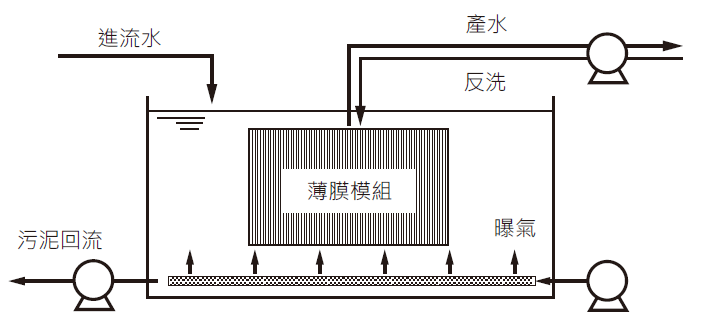
運轉時偶爾會發生膜壓過高問題,將產水時間縮短或下修產水流量可暫時降低膜壓,但仍需探究真因才能一勞永逸。圖15整理出三種情境,說明如何判斷薄膜或生物污泥是否正常,並列出對應解決方法。當產水初期與末期透膜壓力皆未超過-20kPa、反洗透膜壓力亦低於20kPa時,代表薄膜與生物污泥皆在正常狀態;當產水初期透膜壓力即超過-20kPa、反洗透膜壓力亦大於20kPa時,代表薄膜已阻塞,需加強線上藥洗頻率以及提高曝氣量因應;當產水初期透膜壓力正常,產水末期透膜壓力快速惡化,透過反洗可以使透膜壓力恢復正常時,代表生物污泥過於黏稠,但薄膜尚未完全阻塞,此時可藉由增加污泥回流量降低污泥濃度,並提高曝氣量加強膜絲擺動來因應。
圖15、薄膜生物反應器膜壓過高情境模擬
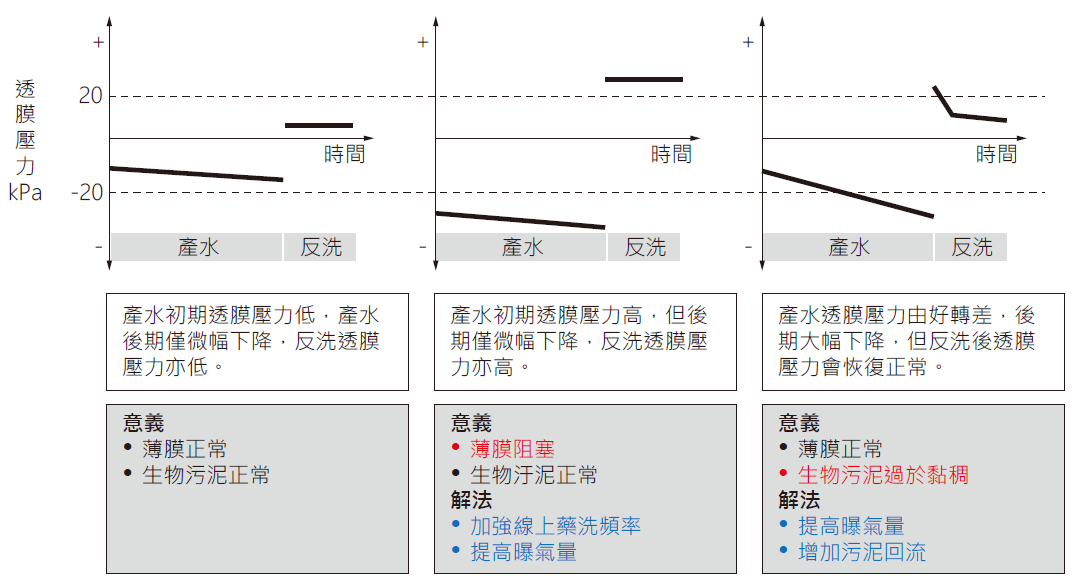
結果與分析
圖16、圖17、圖18為先進製程廠區AOR及SALIX生物處理系統啟用後的去除率趨勢,目前AOR生物處理系統化學需氧量去除率能達到90%;SALIX生物處理系統較晚啟用,學習AOR生物處理系統的經驗後,化學需氧量去除率在短時間內即大於90%,氨氮去除率則是提升至50%。
圖16、AOR生物處理系統化學需氧量去除率
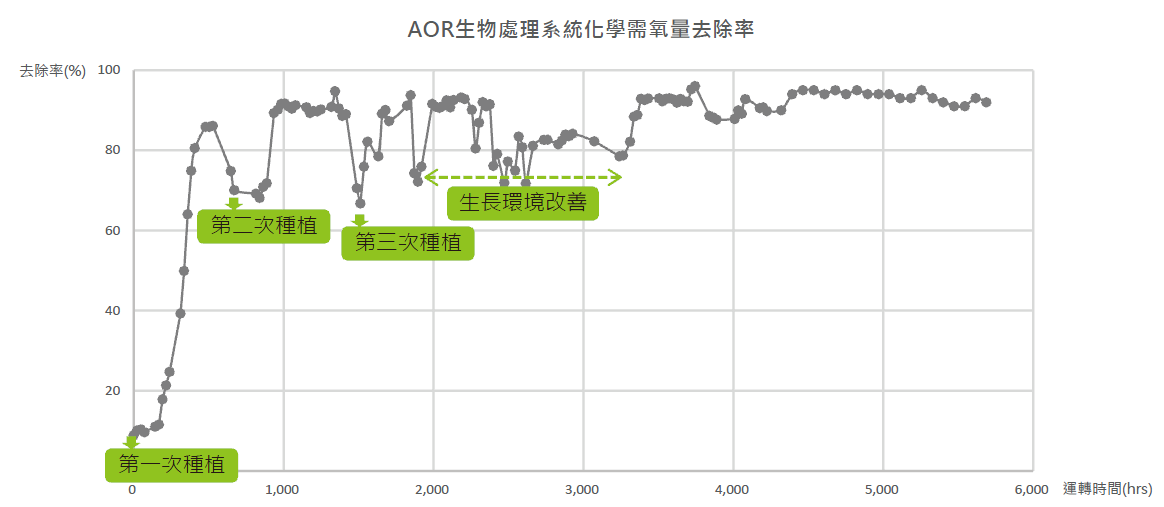
圖17、SALIX生物處理系統化學需氧量去除率
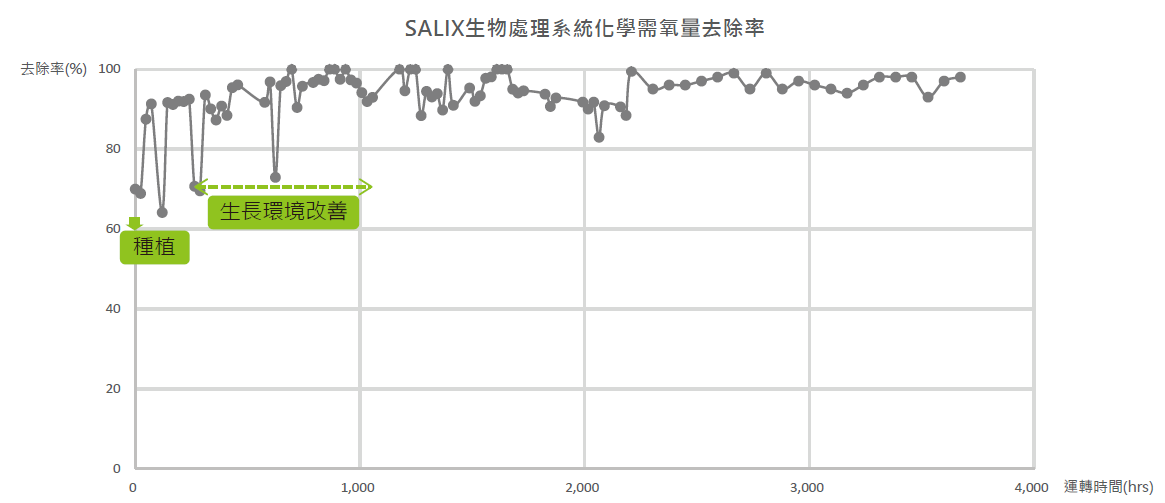
圖18、SALIX生物處理系統氨氮去除率
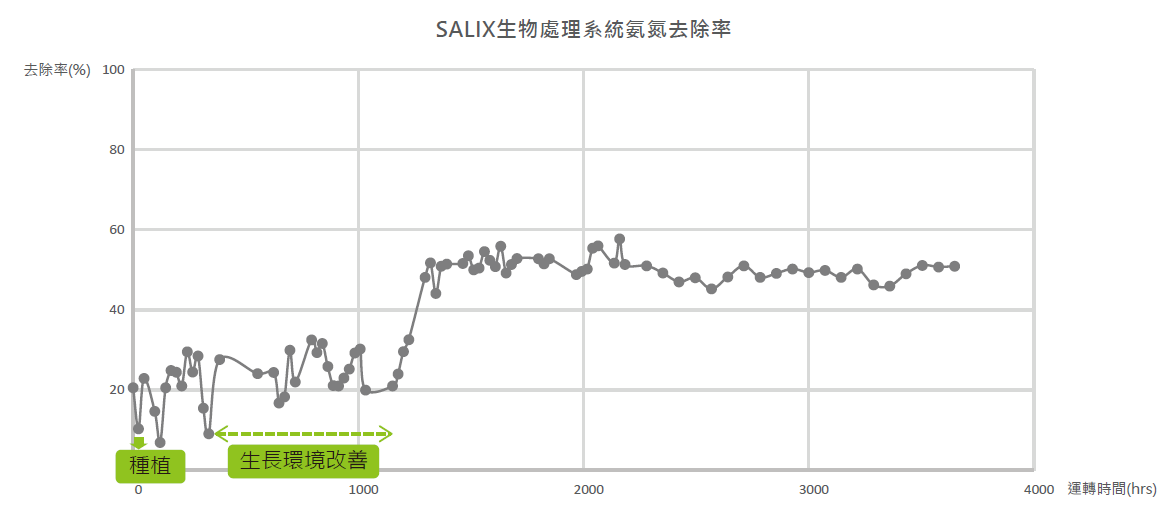
結論
總結上述改善心得,並分成「生物馴養」、「系統運轉」、「宿疾改善」三方面說明。在生物馴養部分,植種取泥位置要以活性較佳的污泥沉澱槽為主,可先以廠區廢水與植種污泥進行去除率實驗,確保植種污泥有處理效果 。在系統運轉部分,依據文獻建議及實際操作經驗,定義出雙氧水濃度、pH、溶氧、混合液懸浮固體濃度、碳氮比 、食微比等六項生長關鍵指標,營造合適環境可縮短馴養期,讓系統更加穩定,此外可就地取材利用高階製程有機廢水作為脫硝反應碳源,取代外購甲醇、葡萄糖或異丙醇等化學品。在宿疾改善部分,依運轉經驗提出冒泡因應對策,短期解法能避免災害擴大,長期解法則是改善系統體質,降低冒泡頻率,另外,薄膜生物反應器膜壓過高需先判別問題後再對症下藥,薄膜阻塞可加強線上藥洗及提高曝氣量因應,生物污泥過於黏稠應先提高污泥回流量,並適時加大曝氣,方能解決問題。
先進製程廠區廢水生物處理系統運轉至今克服許多挑戰,正朝向穩定運轉的目標前進,本文分享試車、運轉操作等相關經驗,以期提供其他廠區運轉參考,惟氨氮去除率尚有改善精進空間,後續仍待與各方專家們集思廣益,提出更有效的改善方案。
參考文獻
- 翁煥廷,生物處理程序常見問題,工業區環保中心處理單元最適化操作參數建立講習班,2015。
- 廖南維、劉偉裕、林志高,新穎厭氧氨氧化生物除氮技術動態,中華技術,109期,頁134-143,2016。
- 范姜仁茂、莊連春、曾迪華、廖述良、游勝傑、梁德明,薄膜生物反應器(MBR)於廢水處理之技術評析,工業污染防治,109期,頁49-96,2009。
- 歐陽嶠暉,下水道工程學,長松文化公司,頁538-539,2001。
- 張聖雄、陳見財、陳良棟,廢水生物處理程序常見問題實務探討 ,工業污染防治,97期,頁69-87,2006。
留言(0)