摘要
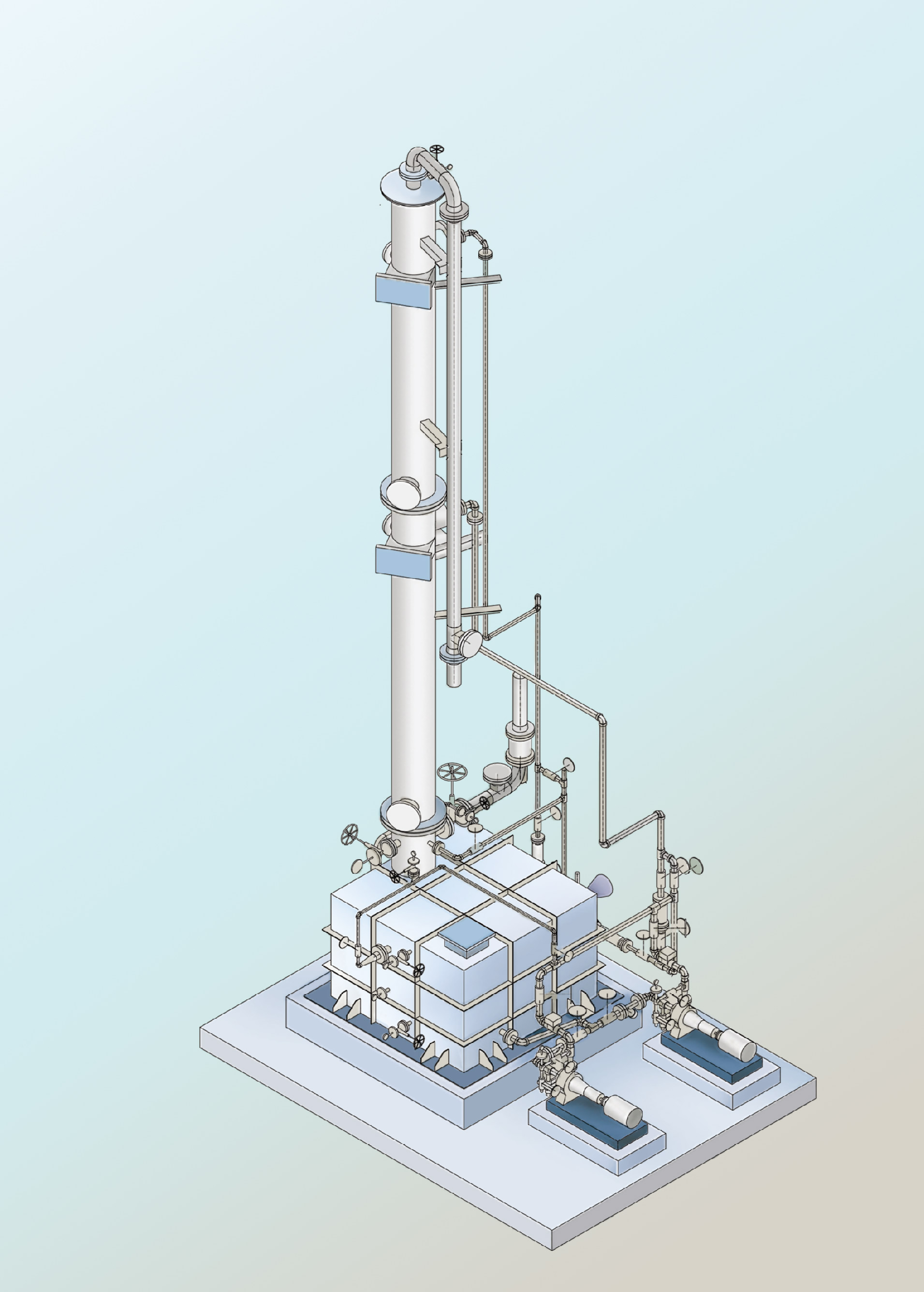
外排廢水化學需氧量減量方法探討與實務
Keywords / Chemical Oxygen Demand(COD),Isopropyl Alcohol (IPA)3,Stripping,Wastewater13
前言
半導體製程越來越先進,使用的化學品種類也越來越多,其中一些酸鹼化學品中亦添加一定比例之有機物,增加廢水處理之困難度;另外大量單片式機台(Single Wafer Type)導入,其存在廢水、化學品混排之問題,造成化學品排入廢水中,上述之問題造成外排廢水之COD 值偏高。且在節水之政策下,廢水製程回收率逐步提高,廢水放流水量變少,導致水中有機污染物被濃縮,使得問題更加惡化。以南科F14B為例,其放流水COD Peak值約偶而會到380ppm左右,離南科納管限值450ppm,僅有70 ppm之差,若廢水廠運轉稍有不慎,可能導致放流水COD超標而受罰。另從廢水廠之運轉操作成本來看,園區污水排放費是採分級費率來收費,若COD值降到250 ppm以下,費率級距可自1.00降至0.90,污水排放費用約可降10~17 %左右,其效益頗大。因此就環保以及操作成本等角度來看,確實有必要進行COD之削減工作。首先我們先進行廠內COD污染源之追查,計畫採源頭減量之措施;另外我們亦針對追查出染物種之特性來評估、找尋一經濟、有效之處理方式。
文獻探討
何謂COD
所謂的COD(化學需氧量): COD化學需氧量是廢水量測重要的指標之一,其表示廢水中可被氧化有機物的含量。當含碳氫之有機物質進入廢水中時,可被微生物、細菌作為食物,最後經代謝作用轉換為二氧化碳及水,此轉化過程需消耗水中水生生物賴以生存之溶氧。因此,任何有機物的存在都能導致水中溶氧量之降低,威脅到水中生物的生態環境。一般廠區的COD來源大多來自於Fab內生產所使用到的有機溶劑,且分子量越大的有機化學品,其COD值越大。
COD處理方法評估
目前各廠大多未設置COD之處理單元,無法有效去除有機物。若要進行COD之削減,勢必需評估COD去除設備之設置。一般處理方法可區分為三類:化學處理法、物理處理法、微生物處理法, 表1是各種處理技術評估一覽表。
分類 |
評估技術 |
處理技術說明 |
適用污染物種 |
優點 |
缺點 |
---|---|---|---|---|---|
生物法 |
活性污泥法 |
用懸浮性好氧微生物吸附並分解廢水中有機物。 |
生物可分解之有機物 |
1. 操作成本低 |
1. 佔地面積大 2. 污泥處理問題 |
物理法 |
氣提法 |
利用鼓入之空氣將廢水中內之有機物趕出。 |
低沸點之有機物,如 IPA、EBR |
1. 初設成本 2. 運轉成本低 |
1. 低沸點有機物有效,高沸點效果不佳(NMP、Stripper) |
化學法 |
Fenton 法 |
添加與H2O2件下,產生氫氧自由基,其可將COD分解成CO2。 |
大部分之有機物,對生物難分解之有機物效果佳[2][3] |
1. 初設成本低 2. 技術成熟 |
1. 污泥量大,衍生出污泥處理問題 2. 增加放流水導電度 |
我們針對各種COD處理其適用之污染物種做一研究、評估,確認關鍵污染物種後,找出經濟、有效之處理方法。在晶圓廠最常採用之處理方法為生物處理法,目前新廠之規畫設計亦將生物處理法列入新建廠之標準設施。從文獻研究得知,如余浚薰(2001)[4]與張冠甫(2008)[7]等人,針對晶圓廠之廢水進行COD處理驗證,其去除率效果佳,去除率高達95%以上。但從魏憶琳(2006)[6]之文獻中提到在生物處理法在曝氣過程中,廢水中低沸點有機物質易從水中逸散至大氣中而衍生VOC廢氣污染問題,因此已設置生物處理系統之廠區均將曝氣槽加蓋並配置風管將排氣導至VO處理系統進行處理。由此由此發想,針對廠內一些含低沸點有機物質(ex : IPA..) 之廢水或許可以使用氣提法(Stripping)來處理。
計畫方法
COD之減量,首先需找出關鍵之污染源,我們採取的方法是以「面→線→點」之收斂手法來進行調查分析以找出主要污染源。待確認污染物之種類、特性以及水量後,可依先前所評估之處理技術找出相對應之削減措施。
面
我們先盤查廠內含有機物的化學品, 表2為含有有機溶劑之化學品列表。再來我們透過SIPOC手法,依供應端、原物料種類,使用端、收集系統、最終處理系統等項目進行調查分析,以釐清找出廢水中之COD可能來源。
分類 |
化學品名稱 |
有機物組成 |
---|---|---|
Acid |
研磨後清洗劑 (CX-100) |
檸檬酸、羥基亞乙基二膦酸 |
複晶矽蝕刻液 (M1) |
醋酸 |
|
鋁蝕刻液 (M2) |
醋酸 |
|
Caustic |
研磨後清洗劑 (CR168) |
1-丁磺醯胺、氟化磺醯胺醇 |
顯影液 (TMAH) |
氫氧化四甲基胺 |
|
研磨後清洗劑 (TC-10) |
N-(2-氨乙基)乙醇胺、乙醇酸、三-(2-羥乙基)甲基氫氧化銨、酒石酸 |
|
研磨後清洗劑 (ATMI-PC) |
正丁醇、1,4-丁二醇 |
|
Solvent |
IPA |
異丙醇 |
去光阻劑 (CLK88) |
專密溶劑、TAMH |
|
去光阻劑 (AX30) |
二甲亞碸、二乙二醇單丁醚 |
|
去光阻劑 (CLC32) |
乙二醇醚 |
|
稀釋劑 (Thinner2) |
醋酸丙二醇甲醚酯 |
|
稀釋劑 (Thinner3) |
醋酸丙二醇甲醚酯 |
|
潤濕劑 (NMP) |
NMP |
|
稀釋劑 (PGMEA) |
丙二醇單甲醚乙酸酯 |
|
去光阻劑 (ACT690) |
乙醇胺、二甲基硫醇、鄰苯二酚 |
|
去光阻劑(ST-250) |
三乙醇胺、亞氨二乙酸、N-(2-(二甲氨基)乙基)-N,N',N'-三甲基-1,2-乙二胺 |
|
顯影劑DEV-2 (A515) |
環戊酮 |
|
稀釋劑 (EBR) |
PGME、PGMEA |
|
稀釋劑 (OKG thinner) |
γ-丁內酯、丙二醇甲醚、丙二醇單甲醚乙酸酯 |
線
接著依據SIPOC手法所層別出可能之污染源後,於現場進行進行採樣分析後建立起COD污染質量平衡圖 圖1。現場採樣分析的方式,我們先從排入廢水廠之各種廢水管排主管路先著手,確認出哪一股廢水之COD最高。接著再進入Fab針對每一個Bay位所配置次主管(Sub-Main)之採樣箱進行採樣、分析,如此可將污染源追查限縮到「線」的層面。
圖1、製程機台之廢水排放架構示意圖
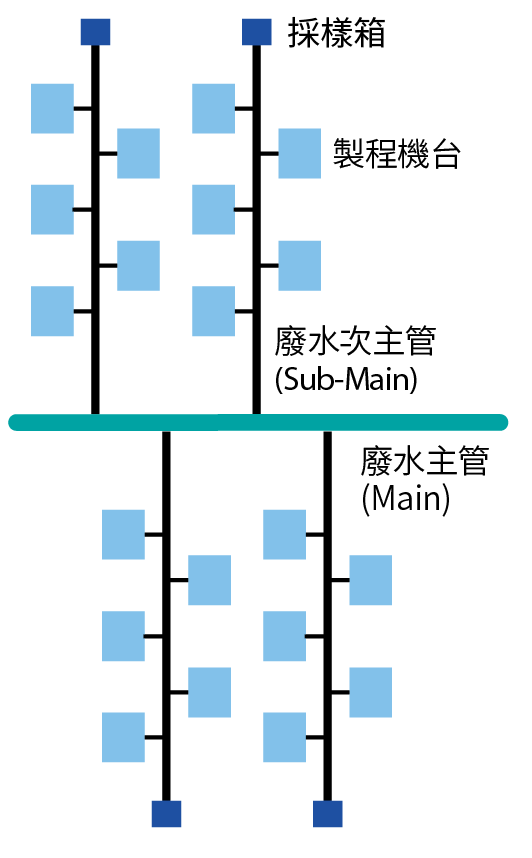
點
最後再比對該區域各機台的化學品使用以及廢水管排之Blue Book資料,即可找出關鍵污染源之機台以及化學品。最後再依此結果找出最佳之改善措施。
結果與分析
廠內含有機物之化學品調查結果
透過SIPOC 圖2法全面的調查得知大多有機溶劑均排至廢液收集系統後再清運至廠外處理,因此不會排放至廢水廠,但有些仍排入酸性廢水(AWD)、TMAH廢水、鹼性廢水(CWD)、AOR (高階有機廢水)等廢水管排中,因此我們針對這幾股廢水進行現場採樣驗證。
圖2、廠內COD可能來源 SIPOC圖
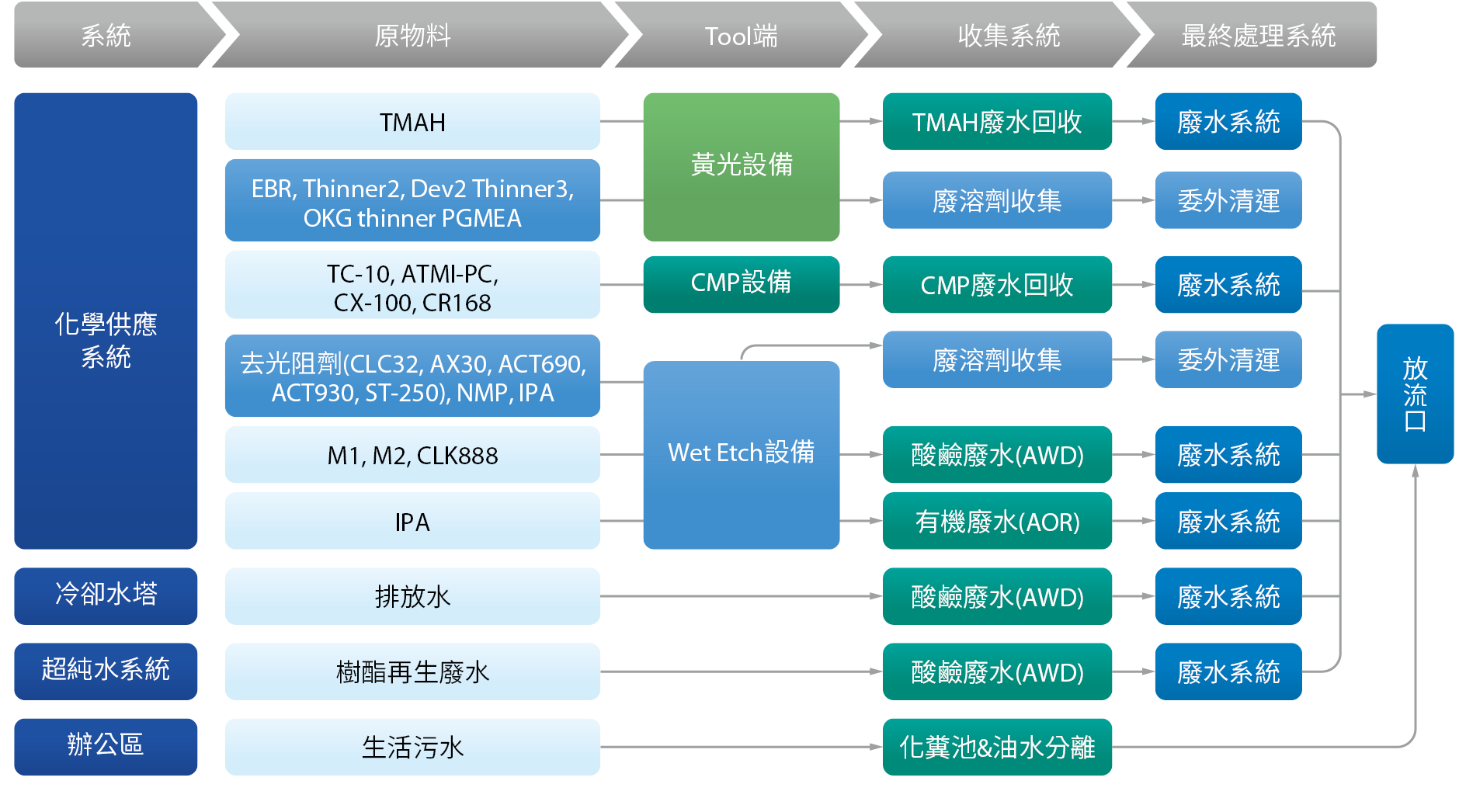
廠內COD來源查找之結果分析
我們透過廢水源頭分析及查找,發現B/E區域AOR廢水管排之COD值4,200ppm,佔整廠COD總量之53%,佔比最大。接著往下追查,發現EEB-B-1 Bay位Sub-main管路COD測值值高達60,300ppm。最後再進一步比對該區域機台之化學品使用&廢水管排的Bluebook資料後,確認出PR Strip製程機台(廠牌:Lam Research、型號:DV-Prime)為關鍵污染源。
COD削減措施執行說明
基於上述之調查結果,我們與設備單位合作,參考機台之製程步序以及到現場實地勘察後,有以下之結論 表3:
PR strip / Spin off |
DI Rinse |
IPA Dry |
Spin off |
|
---|---|---|---|---|
Tool Process Flow |
![]() |
|||
Chamber噴灑時間軸 |
![]() |
|||
Drain三向閥時間軸 |
![]() |
|||
Drain廢水收集秒數 |
![]() |
|||
現場觀察Finding |
去光阻劑經過此spin off甩乾步驟,仍有薄薄一層殘留在wafer表面上。 |
前一個步驟殘留在wafer之去光阻劑在此步驟被洗出 上一cycle殘留在Chamber 的IPA在此步驟被帶出 |
DI、IPA分流不易,導致部分IPA與DI水相混合而排入廢水中 |
IPA殘留在Chamber溝槽內 |
改善作法 |
無 |
將Drain to W-IPA之秒數延長(5→10 sec) |
將Drain to W-IPA之秒數延長(23→43→48 sec) |
- 此機型為單片式機台(Single wafer type),在同一個Chamber ring內使用液態IPA以及DI water進行Wafer 清洗。
- 排液機制:使用後之IPA以及DI water之排放管均是同一管路,分流僅靠三向閥切換,分別是DI drain、低濃度IPA廢液(IPA-L)、高濃度IPA廢液(IPA-H)。其中DI、IPA-L兩股Drain排入廠務端AOR廢水管排內,而IPA-H則排入W-IPA廢液收集系統。
- 化學品殘留問題:在清洗過程中,IPA、去光阻劑等化學品無法全部排入廢水管排,而會有少許殘留在Chamber溝槽內,在下一次cycle的DI water rinse步驟被帶出而排入廢水。
依據上述之結論,我們決定採取Drain三向閥之切換秒數調整之作法,讓Chamber內IPA多排一點至IPA廢液收集系統,如此排入廢水廠的IPA則會減少,但又不至於造成IPA廢液收集系統負擔過重,在IPA廢液以及廢水之排放取一平衡點。
完成機台調整後,針對該廢水取樣進行COD分析以驗證成效。在參數調整前,COD值高達35,000~ 43,000 ppm,且水樣中有很濃IPA味道,但參數調整後,COD值降至4,000~ 9,000ppm,削減率達90%以上,削減效果相當顯著。而我們進一步確認廢水放流水COD值之變化 圖3,並以盒鬚圖方式進行分析,其均值自275→241ppm,降幅達12%,而Peak值則從380→289ppm,降幅高達23%,且調整後之盒鬚圖Box Range較調整前的來的窄,表示我們將此高濃度IPA之廢水儘量切換至廢液收集系統之措施,使得每天放流水COD值波動變小,使廢水系統之操作相對穩定。另外,觀察IPA廢液之增加量,每天僅增加約0.7噸,增幅約8%,對收集系統無太大之負荷。
圖3、放流水COD檢測數據
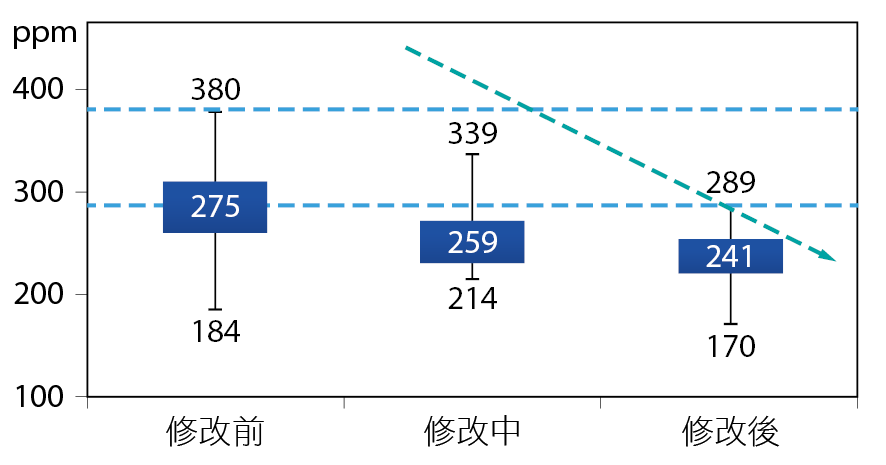
在完成機台Drain秒數調整後,COD大多低於預設目標值<250ppm,但偶而會仍會有幾筆測值高過250ppm。為保險起見,因此我們仍需採取下一階段之改善措施。
氣提法(Stripping)去除IPA之評估試驗
從上述之調查結果,在確認廢水之COD貢獻物質主要為IPA,我們依據之前所評估,決定使用氣提法(Stripping)將IPA自水中趕出以達到去除之目的。為驗證廢水中IPA是否可透過氣提方式加以去除,我們構一小型模廠設備,進一步測試相關操作參數。
模廠設備主要為6吋直徑之氣提塔 圖4,內部充填1m高之拉西環,並配置一20L循環水槽,水樣經由Pump打至塔頂透過灑水器均勻分布在拉西環,而吹脫用之空氣自鼓風機自塔底鼓入後在拉西環表面與水樣進行氣液交換。測試水樣則取用該區機台所排放之AOR廢水進行測試,分別以常溫以及40℃溫度進行氣提測試3hr,期間每隔1hr取樣一次,分析水中IPA濃度值以驗證其去除效果。
圖4、氣提法 Pilot Test現場照片
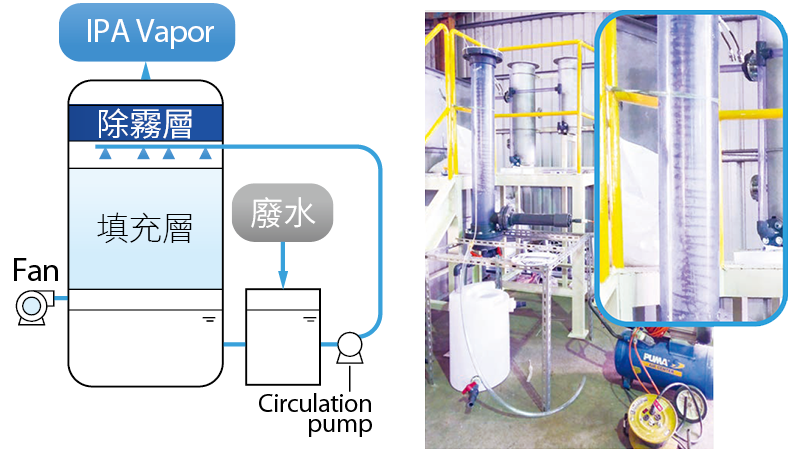
評估試驗結果
實驗結果 圖5在常溫下吹脫3hr後,IPA去除率約六成左右,但水中殘留IPA仍約700ppm其值仍偏高,因此我們進一步將操作溫度提高為40度,而IPA去除率則高達95%~98%,水中殘留IPA大幅下降至41~211 ppm,其對外排之COD值可再降30~70ppm,如此將可達成管制值<250ppm之目標。至於氣提出之含有IPA之廢氣則直接導入VOC處理系統 圖6,不需設置廢棄處理設備,且可提高VOC處理系統進氣之熱值,以降低天然氣之使用等效益。
圖5、氣提法 Pilot Test 實驗結果
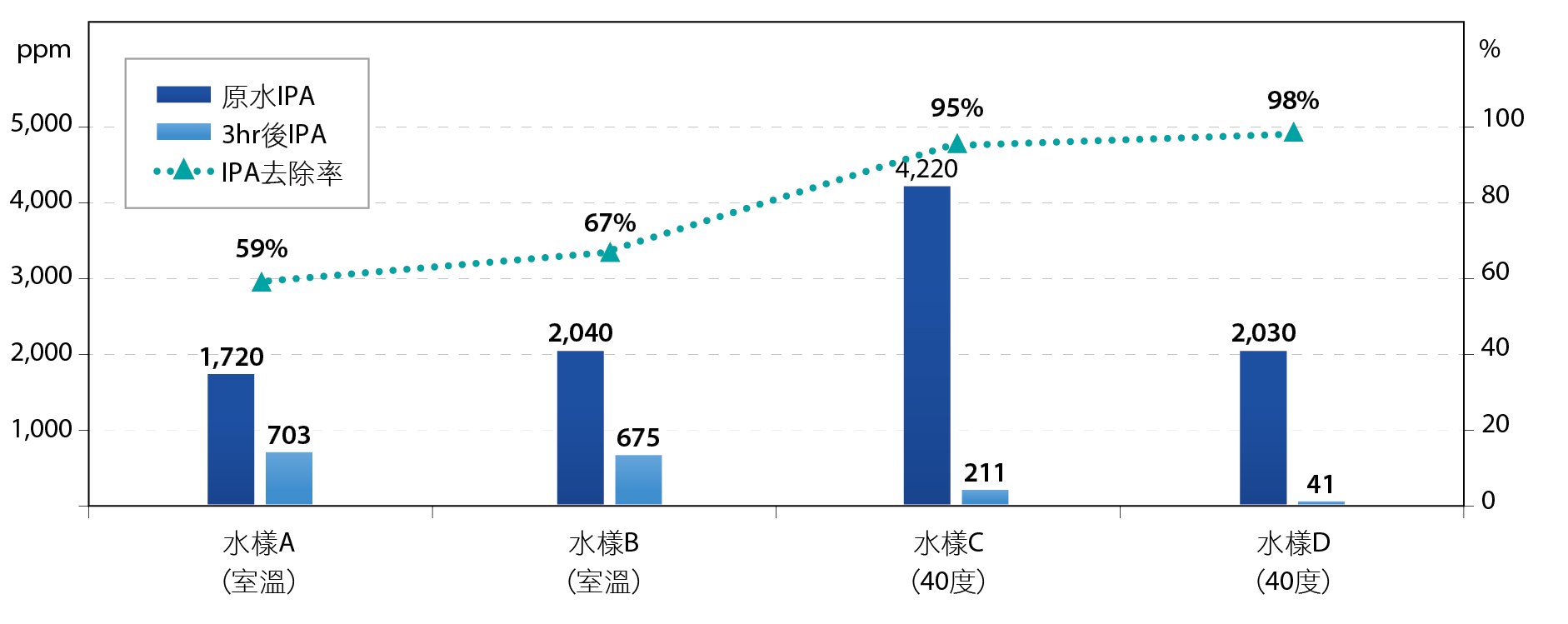
圖6、以氣提法處理含IPA廢水之流程示意圖
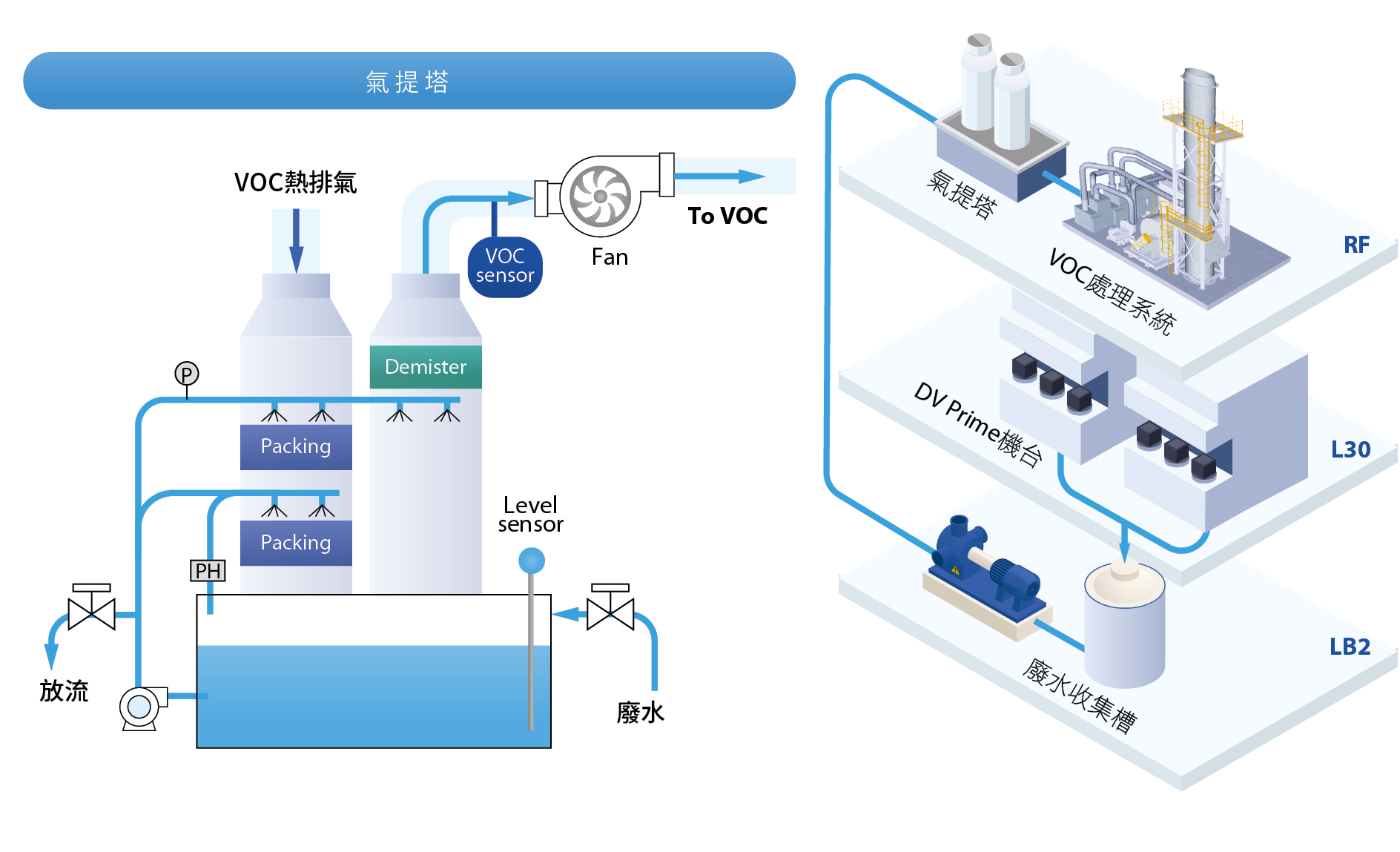
結論
本文針對廢水中COD濃度削減提出兩個快速、有效做法:源頭減量以及源頭處理。這一次與設備部門合作,直接從機台端進行Drain秒數參數調整,即可達到廢水COD之削減目的;接著我們再將機台所排放之高濃度IPA廢水,在未其他股廢水混合前(未被稀釋前),使用氣提法進行前處理,不僅去除率高且可降低後續處理設備之負荷。以上作法我們透過測試驗證確實有效且成效卓著,在此分享供各廠區COD削減改善之參考依據。
參考文獻
- 王春盛,「半導體高濃度廢水之高級氧化處理與有機廢液之異丙醇回收」,元智大學,民國91年。
- 司洪濤等,氧化技術在高濃度COD廢水處理之應用,經濟部工業局產業製程清潔生產與綠色技術資訊網。
- 高級氧化程序在廢水處理上之應用,工業汙染防治技術手冊,經濟工業局,民84年。
- 余浚薰,半導體廠綜合性廢水節水實例-生物薄膜系統,2011年科學工業園區廠務技術研討會,2011年。
- 朱昱學,廢水好氧性生物理方法與操作維護技術簡介、中技社綠色發展中心。
- 魏憶琳,廢水處理場揮發性有機物防制、中技社通訊第58期,2006年,
- 張冠甫,IPA廢水處理技術介紹,永續水資源管理專輯,2008年。
留言(0)