摘要
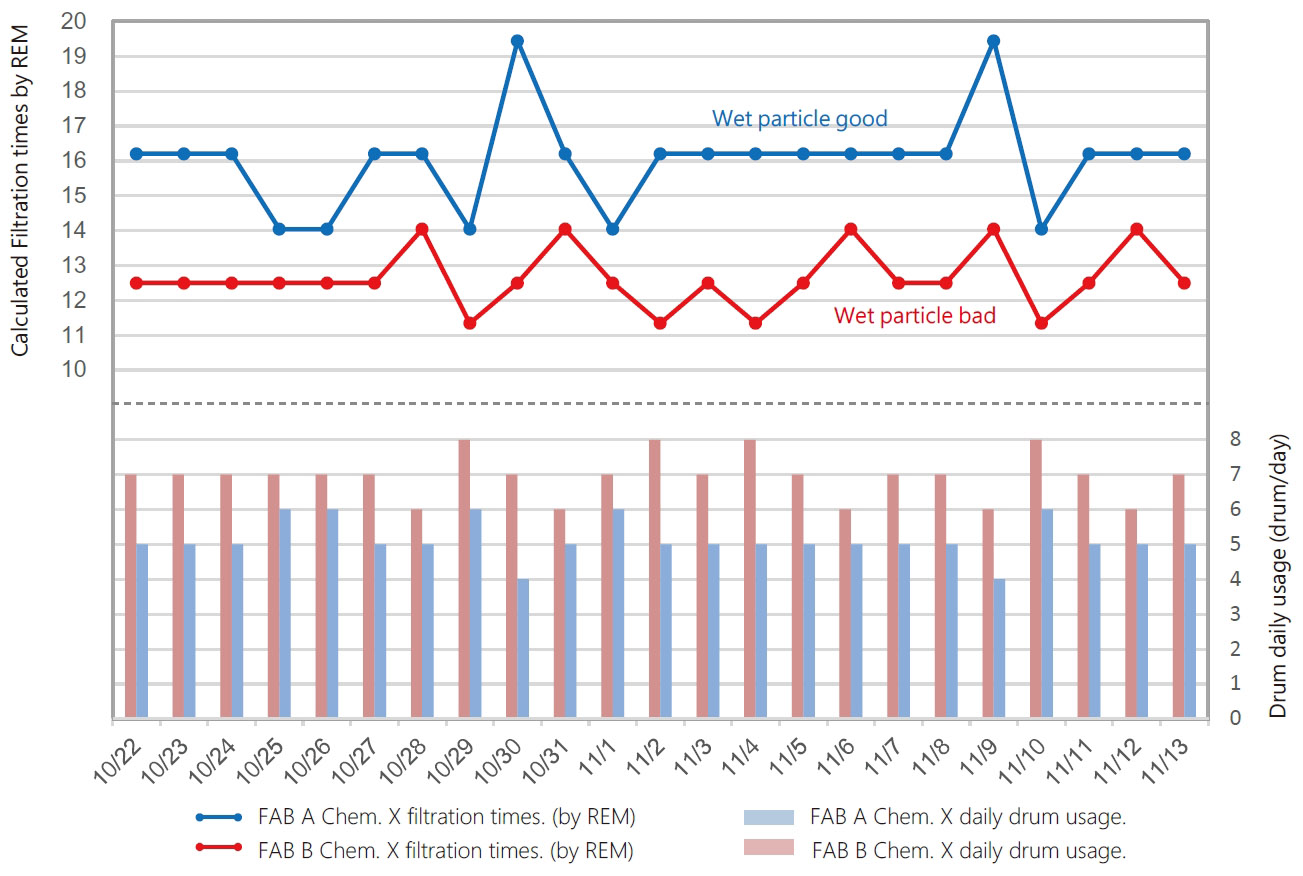
化學品品質管理–循環過濾次數指標之計算模式
Keywords / Chemical Filtration,Circulation Filtration,Index of Filtration Times
前言
過去半導體廠化學品供應大多以〝Clean in & Clean out〞模式為主,也就是供應商提供何種品質的原物料,廠務端就供應相同潔淨等級的原物料給生產機台。在此模式下,原物料品質完全依賴供應商的製程潔淨度,若需藉由提升原物料潔淨度來提升生產良率,也只能透過公司的原物料品質控管部門,從原物料端的品保控管著手[1]。先提高允收標準後,再由原物料檢驗報告(Certification of Analysis, COA)對原物料品質把關。然而隨著製程線寬日漸微縮,先進半導體廠對於原物料品質的要求也日趨嚴格 ,若仍維持舊有的〝Clean in & Clean out〞供應模式,未來恐會有越來越多化學品無法達到先進製程的潔淨度要求。再者,目前國際上半導體廠的先進製程競賽激烈,目前公司雖然暫時居於領先的位置,但若關鍵生產原物料的品質掌握在供應商手上,競爭對手們也能透過供應商獲得相同品質的原物料,並可能因此拉近和我們之間的先進製程差距。
有鑑於此,如何將原物料品質在供應到機台之前加以精進,成為廠務端相當重要的課題,最常見作法為濾材過濾(Filtration)[2]。然而濾材材質以及孔徑控制等相關製造技術,都掌控在濾材供應商手中,要自行開發出過濾效果更佳的濾材並非易事。因此,對於廠務端而言最直接又簡單的做法,即為透過供應管路設計或是濾材串聯等方式,來增加化學品通過濾材的次數(Filtration Times)。而如何合理地計算出過濾次數,提供一個可以比較的數值指標,對於穩定控制供應品質的廠務運轉工作來說,更是不可或缺的一項關鍵。本文將針對過去運轉上曾使用的過濾次數計算方法加以回顧說明,此外也提出了幾種創新的計算模式,並分享其在運轉上實際應用的案例。
文獻探討–既有計算模式回顧
2.1循環過濾的基本計算模式
化學品過濾的方式可分為一次性過濾(One Pass Filtration)與循環過濾(Circulation Filtration)兩種。一次性過濾為化學品以單向流通過濾材後,即供應給線上生產機台,如 圖1(a)所示,其過濾次數的計算相當單純,完全取決於化學品供應路徑上的濾材數量,為一定值。循環過濾則是貯存於桶槽中的化學品,由幫浦泵抽出流經濾材後再打回桶槽,隨著不斷地反覆循環,過濾次數越多,如 圖1 (b)所示。循環過濾次數的計算相對複雜,也是本文討論的重點,其基本的計算模式可由式(1)表示之:
圖1、化學品(a)一次性過濾及(b)循環過濾式意圖
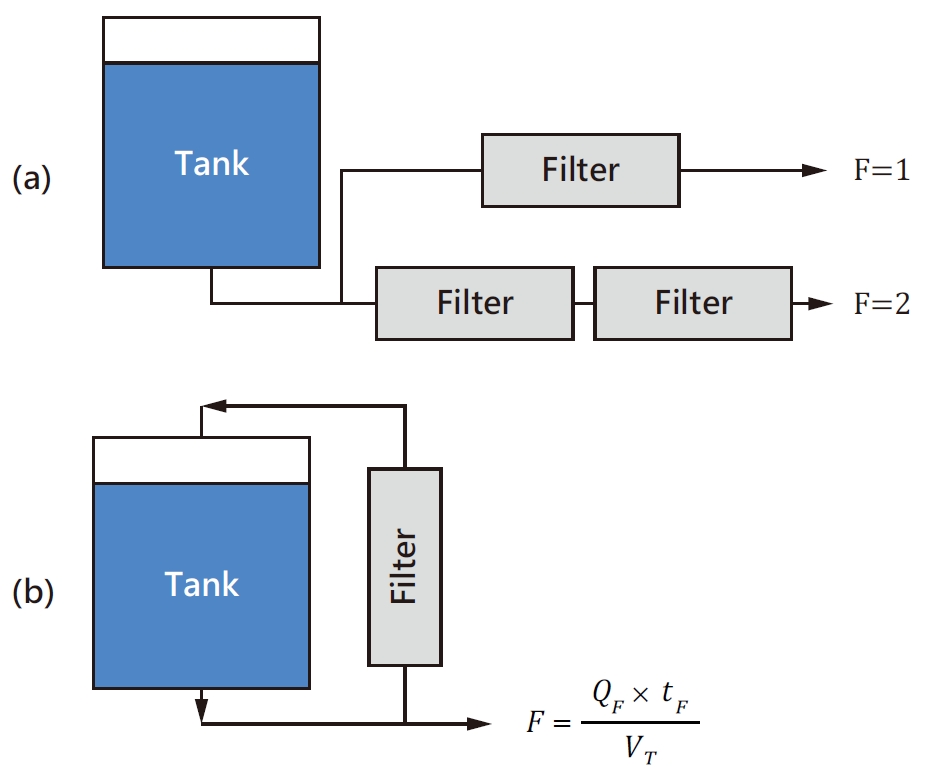
其中F為循環過濾次數、QF為循環過濾流量(L/min)、 tF為循環過濾時間(min)、VT為桶槽內執行循環過濾的化學品體積(L)。
2.2大宗化學品的循環過濾
工廠內用量大較大,需透過槽車供應的化學品,廠務端統稱大宗化學品(Bulk Chemical)。化學槽車首先會將原物料填充至體積較大的槽車桶槽中(Lorry tank,體積約6~ 30噸),Lorry tank數量一般為二顆,主要目的為讓二顆桶槽可作供應及槽車填充的相互切換。接著再透過化學品輸送單元(Chemical Transfer Unit, CTU)將Lorry tank內的化學品輸送至後端體積較小的日用桶槽中(Day Tank,體積約0.5~1.5噸),其數量從1至3顆不等,視化學品的用量與供應模式而定。最後再由化學品供應單元(Chemical Dispense Unit, CDU)將Day tank內的化學品供應給線上機台。
為提升原物料供應品質,廠務端針對Lorry tank額外設置了循環單元(Circulation Unit, CU),讓桶槽內的化學品透過不斷的循環過濾,達到提升原物料潔淨度的目的。過去廠務端針對Lorry tank循環過濾次數(FLT)的計算模式如下
其中tF, i及tF, i-1分別為該顆桶槽此次及前一次,從灌充後到切換為供應側之前的有效循環時間(min)、tS, i則為該顆桶槽從此次灌充後到切換為供應側之前的實際循環時間(min),VE與VF分別為該顆桶槽於此次灌充前桶槽內的原物料剩餘體積(L)與灌充後的原物料總體積(L)。
2.3桶裝化學品的循環過濾
除大宗化學品之外,部分的桶裝化學品供應系統(Drum Unit, DU),也會透過供應桶槽循環過濾的方式來增加其供應品質。當桶裝化學品裝上DU之後,會先透過補液幫浦將化學品輸送至Day tank,再由供應幫浦將Day tank內之化學品供應給線上機台,或是先輸送至壓力容器(Pressure Vessel)再透過其供應給線上機台。於此同時, DU內的補液幫浦也會不斷地將Day tank內的化學品抽出,經過濾材過濾之後再重新補回桶槽,藉此達到循環過濾的目的。Day tank和Lorry tank的循環過濾最大的差異在於, Day tank的數量一般僅配置1顆,桶槽內隨時都有完全未經過濾的新化學品補入,或是經循環過的舊化學品輸出,使其循環過濾次數較難估算,以致於目前尚未有一個合理的算法可供廠務端使用。有鑑於此,本文將提出兩種新型的計算模式,針對Day tank的循環過濾次數進行合理的估算。
本研究提出之計算模式
3.1概略型估算模式(Rough Estimation Mode, REM)
第一種為概略型估算模式(Rough Estimation Mode, REM),此模式可針對DU的循環過濾次數進行初步估算,主要用於跨廠區相同系統的循環次數概略性比對。圖2為REM的計算示意圖。
圖2、REM計算模式的說明示意圖
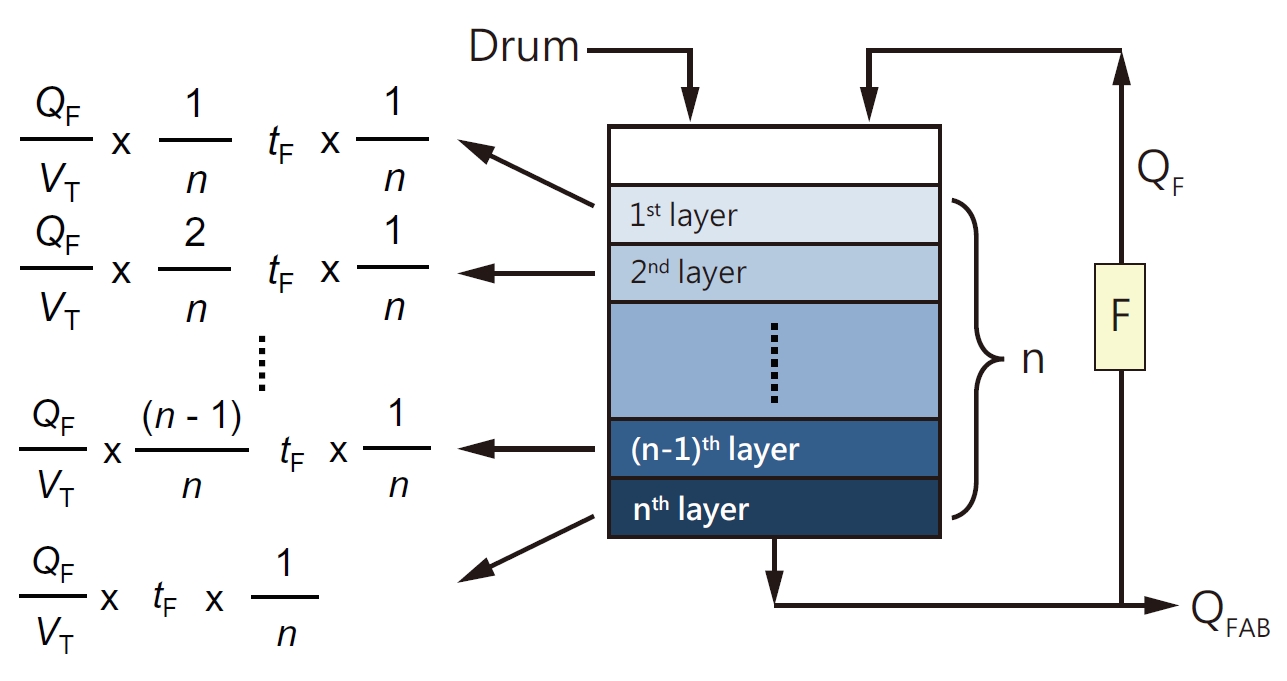
如前文所述,由於Day tank的供應模式為補液及供應動作同時進行,為了計算方便,本文假設一顆Day tank內的化學品可分為n層,最上層為最新補入Day tank的化學品 ,循環次數最少,而最下層則是在Day tank內循環最久的化學品,過濾次數最多。而每一層的循環過濾次數(FDT, i)可由下式所示之:
Day tank化學品的總過濾次數(FDT),則是每層化學品過濾次數的加總,如下:
當n趨近於無窮大時,式(4)可寫為:
經計算後,式(5)可整理為:
假設Day tank循環過濾不間斷,過濾期間所發生的Vessel補液等其他可能造成循環過濾程序短暫中斷的時間忽略不計,則Day tank的循環過濾時間(tF)可視為:
其中QFAB為設備端的使用流量,將式(7)代入式(6),FDT則可改寫為:
式(8)即為概略估算模式的計算式,其中循環過濾流量QF,視供應Pump壓力設定而定,為一固定值,QFAB則可透過每日桶裝化學品平均更換數量加以概略估算之。
3.2動態型精算模式(Dynamic Calculation Mode, DCM)
本研究提出第二種計算模式為動態型精算模式(Dynamic Calculation Mode, DCM),顧名思義此模式可對循環過濾次數作較精細的計算,計算結果也會隨時間呈現動態變化,可用於時序密度需求較高的線上產品缺陷(Defect)比對。DCM的計算方式為每經過∆t的時間,即計算一次過濾次數,由於Day tank補充新化學品的時間間隔為一定值,所以當∆t時間內從Day tank供應出去的化學品量越小,Day tank補進未經過任何過濾(F=0)的新化學品就越少,使得Day tank中的整體化學品過濾次數較高。反之 ,則會讓Day tank中的整體化學品過濾次數被拉低。圖3為DCM的計算示意圖。其中FDT, t和FDT, t+∆t分別為Day tank在 t和t+∆t的時間下的循環過濾次數。
圖3、DCM計算模式的說明示意圖
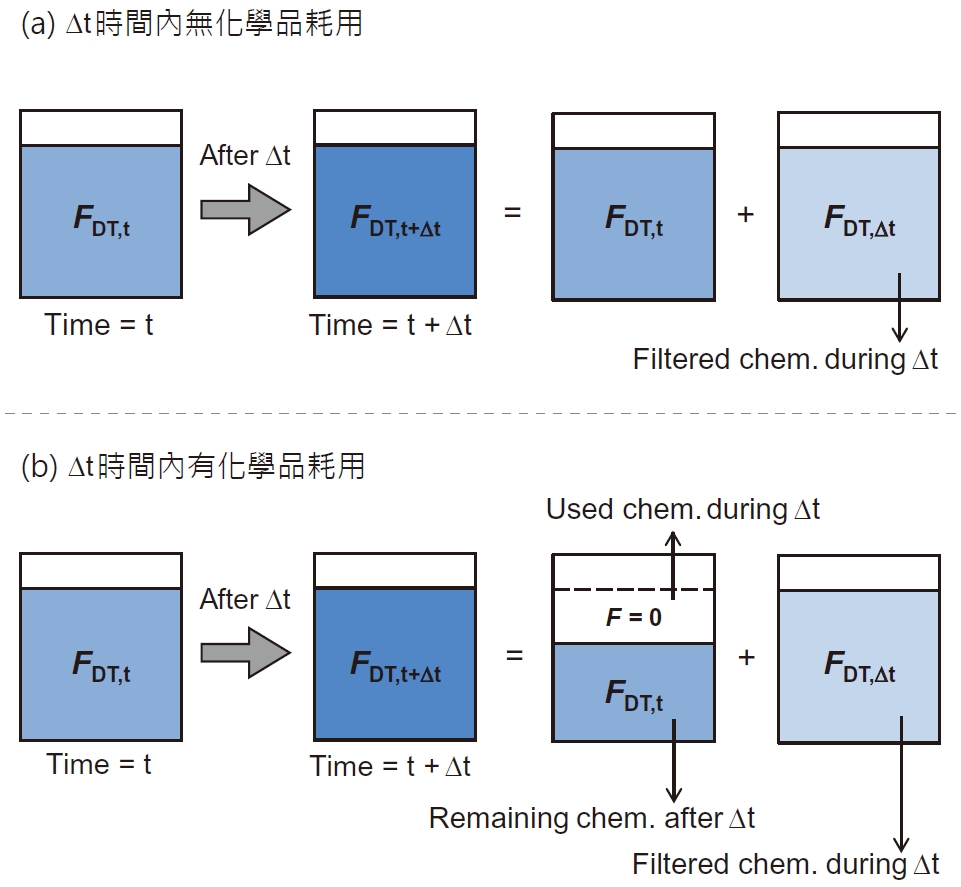
首先,先假設一個較簡單的狀況,如 圖3(a)所示,當∆t時間區間內,Day tank未供應出任何化學品,此時經過 ∆t之後的Day tank循環次數可很直觀的以下式表示之:
其中FDT, ∆t為在固定的∆t時間內Day tank可增加的循環次數,由式(1)可知,當循環流量不變的情況下,FDT, ∆t是為一定值。接著討論在∆t的時間區間內,Day tank有供應出化學品的狀況,如 圖3(b)所示。在討論此情況的計算方式之前,需先建立Day tank每次的補液時間間隔遠小於∆t的限制。在此前提之下,Day tank可視為均在滿桶液位的狀況下執行循環過濾,故每小時增加的循環過濾次數FDT, ∆t仍可視為一定值。由於在∆t內,Day tank已被消耗掉了一部份的化學品,並同時補入了F=0的新化學品,因此在這當中僅有未被消耗掉之舊有化學品的循環次數可繼續往下累加,新補入化學品的部分,其循環過濾次數需從0開始計算 。故經過∆t之後Day tank循環次數,需先將桶槽內的化學品體積,乘上一舊有化學品比例(R),再加上每小時新增的循環次數,如式(10)所示:
其中R可用下示計算之:
tREQ則為Δt時間間隔內Day tank供應出化學品的總時間。
結果與討論
4.1REM應用實例
化學品X為廠區A及B均有使用的化學品。在2019年10月中下旬,廠務收到工廠反應,相較於廠區A,廠區B在使用化學品X時,有濕微粒(Wet Particle)較多的狀況。廠務端比對兩廠區廠務端的供應系統、化學品濾材更換日期與原物料批號等,均未發現任何差異。進一步以REM計算兩廠區化學品供應之前的過濾次數,結果如 圖4所示,才發現廠區B的每日桶裝化學品使用量略高於廠區A,導致其循環過濾次數較低,並推測此為造成兩廠區化學品X供應品質差異之主因。我們也透過此數據,建議製程端分散機台生產負荷,讓廠區A部分的產能移至運轉負荷較低的廠區C ,藉此增進廠區A的化學品循環過濾次數。
圖4、廠區A及B使用之化學品X,每日Drum桶用量與REM計算之過濾次數關係圖
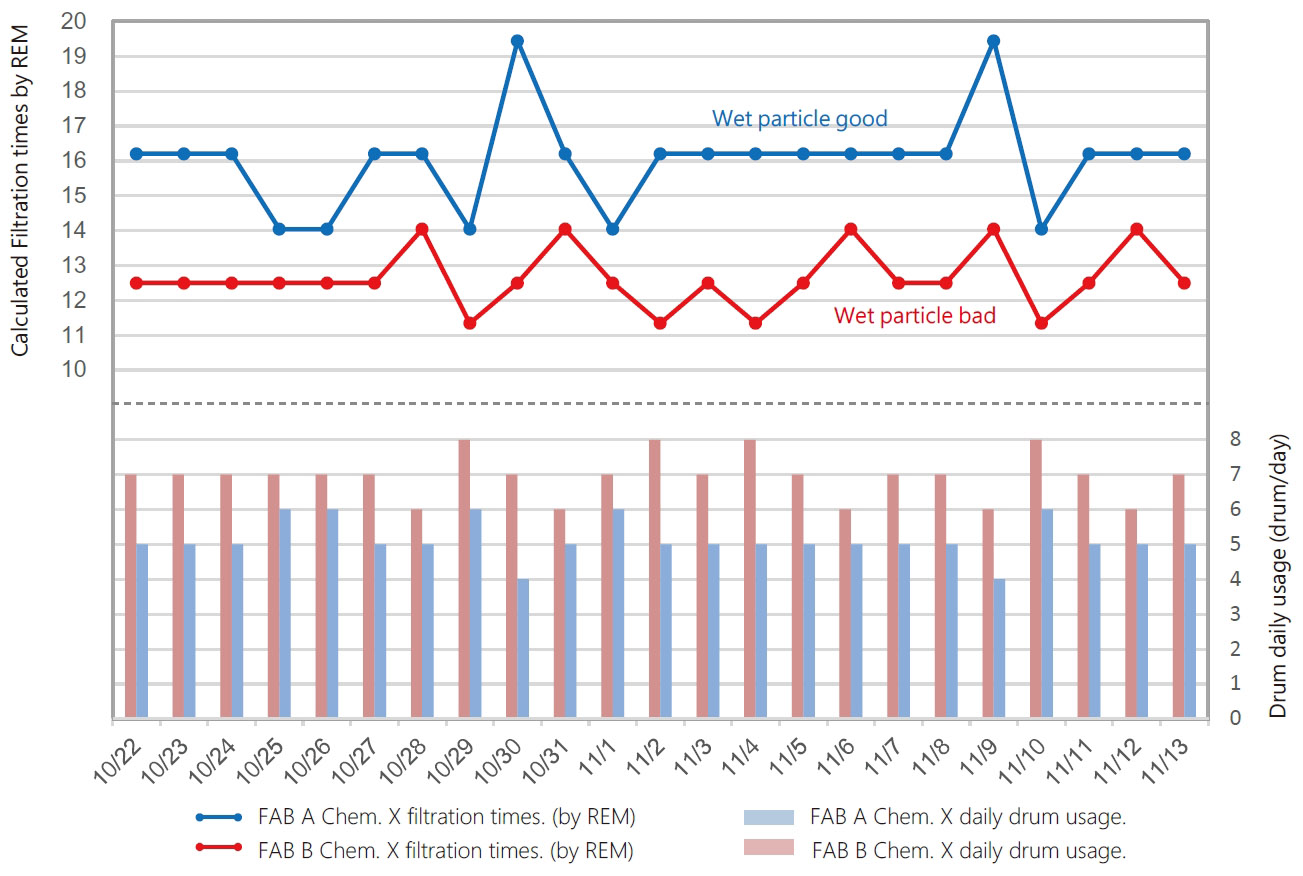
2020年初,另一劑化學品Y也發生類似案例,這次該化學品的供應品質則是在廠區A於1/2之後有較差的表現。然而,在此次案例中,卻無法利用REM的計算結果來完整地解釋供應品質差異。圖5為A與B廠區所使用之化學品Y,每日桶裝化學品使用數以及REM計算之過濾次數關係圖。由 圖6可看出,化學品Y於廠區A的用量平常在3桶/日以下 ,但在1/2當天,因設備執行機台維護保養、異常查修與機台桶槽清洗等作業,使得當天的用量突增至6桶/日,進而使當天的過濾次數由原本的20次以上,降至10次左右。這部分可用以說明廠區A於1/2之後供應品質表現較差的現象 。然而,此結果卻無法說明為何廠區B整體的用量大於廠區A,且在1/7、1/9與1/10也有使用量大於6桶/日的狀況,但廠區B的化學品Y供應品質卻仍維持在相當不錯的水準。
圖5、廠區A及B使用之化學品Y,每日Drum桶用量與REM計算之過濾次數關係圖
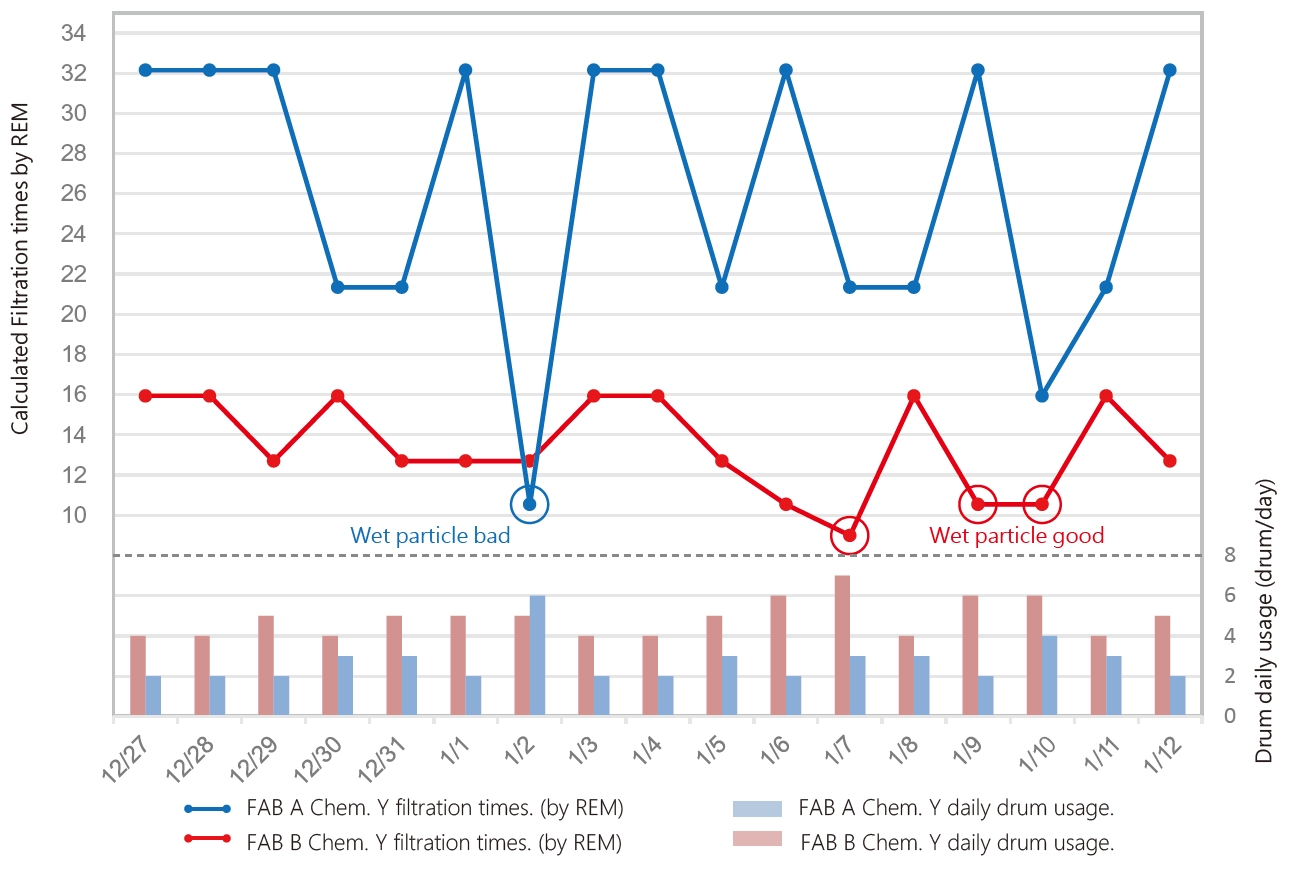
圖6、廠區A與B使用之化學品Y,每小時總要酸秒數與DCM計算之過濾次數關係圖

4.2DCM 應用實例
為了能合理解釋化學品Y供應品質在廠區A與B的差異,本研究導入了DCM計算模式,針對用量同樣均為每日6桶的兩天,分別為1/2的廠區A以及1/9的廠區B,進行每小時過濾次數的計算,結果如 圖6所示。由結果可看出,1/2的廠區A,機台化學品需求時間間隔較不平均,密集集中於1/2中午過後,使得化學品的循環過濾次數逐漸被拉低,並於21:00過後低於10次以下,也因此影響了其供應品質。反觀廠區B於1/9的狀況,雖然化學品的過濾次數偶有因單一小時機台化學品需求秒數較長,導致過濾次數偏低,但因為需求間隔較為平均,所以整體過濾次數還是可以慢慢拉回恢復到15次以上。此結果也可看出機台端化學品需求時間間隔長短對於循環過濾次數的重要性。
本研究進一步利用DCM的模擬結果,給予機台對於化學品Y需求時間間隔建議,以提升整體的供應品質。正常生產模式之下,機台內部的桶槽約每20小時會有一次的化學品置換需求,置換化學品時的補充流量約為12L/min。以廠區A為例,該廠區共有2台使用化學品Y的機台,每個機台有2顆桶槽,故共有4顆桶槽有定期的化學品置換需求。要讓每個桶槽的化學品置換時間平均,最直接的算法為化學品置換週期除上桶槽數量,算出之時間為300分鐘。將已知最佳化的時間間隔,以及置換流量代入DCM計算,結果如 圖7(a)所示,可看出化學品的過濾次數會介於27.7至33.3次之間,平均為30.6次。
圖7、(a) 以DCM計算出Tool在最佳的化學品需求時間間隔下的循環過濾次數
(b) 以DCM模擬出Tool在密集換酸PM後,過濾次數的變化情形
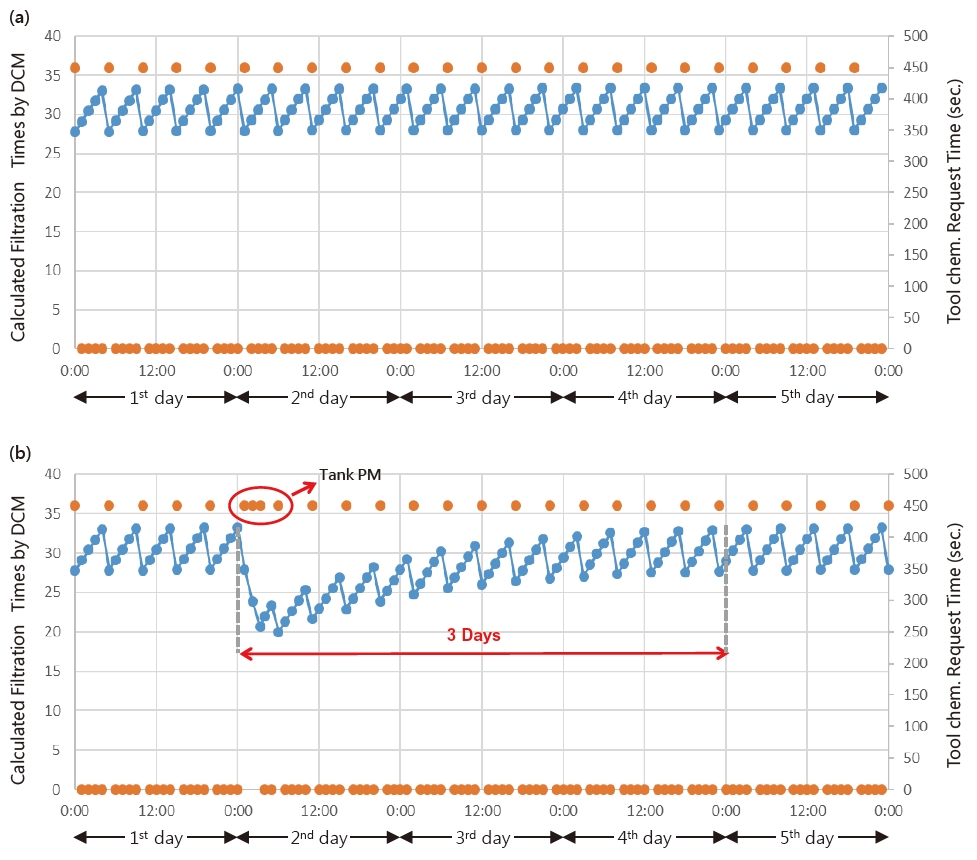
另外,機台的桶槽也有執行定期保養的需求,保養期間桶槽會連續且密集地執行3次化學品置換,每次間隔約70分鐘。本研究也將此行為模式代入DCM進行模擬計算,結果如 圖7(b)所示。結果顯示,在如此密集的化學品置換行為之下,過濾次數會由原本的33次被拉低至20次,之後機台在正常的300分鐘置換頻率之下,大約要經過3天之後 ,過濾次數才會緩慢的恢復至原本的水準。本研究也根據此結果,建議機台的桶槽定期保養時間間隔至少要大於3天 ,才可避免化學品整體的過濾次數在尚未回到正常水位之前,又持續被拉至的更低水位。
結論
本研究提出了概略型估算模式(Rough Estimation Mode, REM)及動態型精算模式(Dynamic Calculation Mode, DCM)兩種新型的計算模式,針對桶裝化學品供應系統(Drum Unit, DU)的循環過濾次數進行計算。REM以每日桶裝化學品的使用量作為計算基礎,可用於跨廠區相同系統的循環過濾次數概略性比對 ; 而DCM則是使用固定時間內化學品總需求秒數作為計算基礎,因計算頻率高,適用於時序密度需求較高的線上Defect比對。實際應用的結果顯示,REM確實可用於某些化學品在跨廠區大方向上概略的比對,但若需評估短時間內化學品需求頻率對於供應品質的影響,還是需透過DCM的計算結果,才可提供較為合理的說明。此外,本研究也透過DCM的模擬,提供線上機台一個建議定期保養週期,確保化學品循環過濾次數能恢復至正常水位後再執行下一次的保養。
目前DCM的計算,係建立於設備端的化學品需求流量為一固定值的假設,故目前僅適用於設備端需求流量較為穩定的化學品。未來若將廠務端供應機台的出口流量計即時數據,導入DCM的計算程式中,相信可更廣泛地適用在各種DU化學品的循環過濾次數計算。
參考文獻
- 曾恒毅,2019,因應研發先進製程轉量產之氣體與化學供應系統運轉策略。廠務季刊,Vol: 33。
- 徐銘宗、江宜臻、謝欣容,2013,先進半導體廠化學品供應系統及微粒子控制。廠務季刊,Vol: 10。
留言(0)