摘要
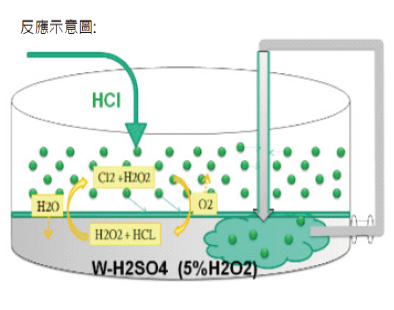
新世代的廢硫酸回收處理系統開發
目前台積電各廠皆以鹽酸法去除廢硫酸中的雙氧水後回用於氨氮廢水處理等系統,本文針對既有鹽酸法所衍生之含氯物質(氯氣、氯離子)之腐蝕、殘留等問題作一探討和研究後,提出新的處理技術-硝酸法,並透過實驗室以及模廠兩種不同等級之測試驗證,證明硝酸法不僅可以將雙氧水去除,且無副產物殘留問題,可完全解決鹽酸法之宿疾。目前FRC Committee已決議改造中科F15P5廠區之既有廢硫酸處理系統(WSR)以進行驗證,未來有機會納入於新廠設計以取代既有鹽酸法,成為新世代的廢硫酸回收處理系統(WSR2.0版)。
Currently, tsmc use hydrochloric acid to remove hydrogen peroxide from waste sulfuric acid recycling. This article explores and studies the existing problems of hydrochloric acid method, such as equipment corrosion from chlorine gas, residual chloride ions in the recycled sulfuric acid, and operational issues. A new treatment technology, nitric acid method, is proposed, and through laboratory and pilot tests, it is proven that nitric acid method can not only remove hydrogen peroxide but also completely solve the residual by-products in the recovered sulfuric acid, and can eliminate the problems of hydrochloric acid method. The FRC Committee has decided to conduct a Pi -Run in the F15P5 site. In the future, it will replace the existing hydrochloric acid method and become the new generation of waste sulfuric acid recycling treatment system(WSR2.0).
1.前言
台積電於2015年開始使用鹽酸法進行廢硫酸之回收再利用,其原理是藉由加入鹽酸作為催化劑,將廢硫酸中雙氧水加以分解去除,但衍生所含氯副產物(氯氣、氯離子)則可能造成後端應用設備之腐蝕、損害以及毒氣警報等疑慮(圖1為廠內硫酸之使用、回收再利用流程圖)。雖然各廠廠務、工安環保等部門花費相當多心力,從操作參數之最佳化以及防禦措施等面向進行改善,但成效有限,顯然僅是治標而不治本。尤其是公司大力推行綠色製造、淨零排之際,實有必要開發一個更安全、更穩定之技術。
圖1:廠內硫酸之使用、回收再利用流程圖
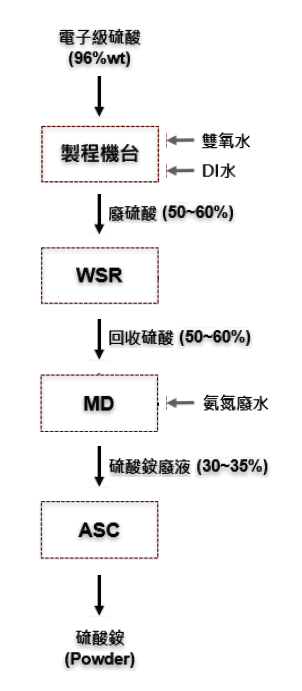
2.文獻探討
2.1 鹽酸在廢硫酸中之反應機制探討
開發新世代回收處理系統之首要任務是針對鹽酸法之反應機制進行研究及探討,了解其問題所在,找出其解決方案及對策。
鹽酸法是由台積電自行開發並通過專利申請,我們透過專利文件(I555702號)所揭露之內容以及公司內部之技術文件,了解其反應機制(圖2)。其反應機制如下所示:
圖2:鹽酸法之反應機制示意圖
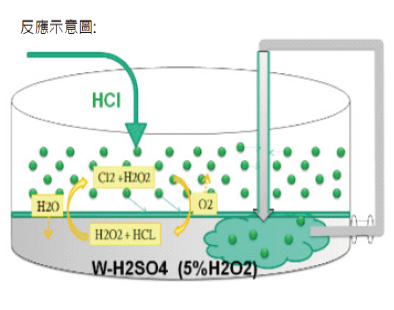
從反應式得知,鹽酸(HCl)擔任為催化劑之角色,式⑴說明其與雙氧水反應生成氯氣(Cl2),式⑵說明氯氣再與雙氧水反應又變回HCl,反覆連鎖反應。不過實際運轉時,氯氣因高溫以及本身在廢硫酸中之溶解度較差,導致氯氣逸散至排氣中,無法再與雙氧水反應,導致連鎖反應中斷,因此需不斷添加鹽酸,也造成氯氣持續逸散。另外一個問題是再生硫酸有氯離子殘留問題,因廢硫酸中含有40~60%的水分,而鹽酸在水中易解離成氯離子(解離常數Ka值高達108),與表1所列常見酸性化學品之解離常數相比,高出許多之數量級。一但HCl解離成氯離子(Cl−)之形式存在,則無法生成氯氣而殘留於再生硫酸內。綜上分析,尋找低解離性且低揮發性的催化劑方可以解決上述問題。
物質名稱 | 化學式 | Ka |
---|---|---|
鹽酸 | HCl | 108 |
硝酸 | HNO3 | 102 |
磷酸 | H3PO4 | 10-2.12 |
氫氟酸 | HF | 10-3.18 |
醋酸 | CH3COOH | 10-4.75 |
次氯酸 | HOCl | 10-7.5 |
2.2 應用雙氧水之催化劑種類探討
在尋找新催化劑前,首先要先了解催化反應機制以及再生硫酸之應用場合,並考慮催化劑對廢硫酸高腐蝕之耐受性等幾個因素,依此歸納出催化劑應具備低揮發、低解離、低析出以及高機械強度等特性。
目前應用於雙氧水之催化劑種類共計有金屬鹽類(氯化亞鐵、亞硫酸氫鈉、CuS、MnO2)、貴重金屬(Pt)、酵素、活性碳以及無機酸(HCl)等幾大類,但可以符合催化劑之要求條件以具低解離性且低揮發性的非金屬催化劑最為接近。我們透過文獻查找以及化學品特性,鎖定硝酸這個化學品,其解離常數Ka為102較鹽酸小很多(108),後續將展開可行性之評估以及反應機制之驗證。
2.3 硝酸在廢硫酸中之反應機制探討
透過文獻查找,雙氧水(H2O2)與硝酸(HNO3)兩者反應後產生NO2(如式⑴所示),而NO2則在有氧的條件下,與H2O2繼續反應後又變為HNO3(如式⑵所示),如此HNO3、NO2相互連鎖反應,實為催化反應機制。不過上述的反應式,HNO3或H2O2都是在水溶液之條件進行反應,而非在含硫酸之環境,因此後續將透過實驗來驗證廠區的含有雙氧水的廢硫酸亦或遵守上述之反應?
2.4 硝酸、鹽酸對於不銹鋼之損害機制研究
不鏽鋼之所以不生鏽,主要是表面會形成一層厚度1-3nm鉻-氧-氫氧根結合的鈍化膜。但氯離子與鈍化膜成分中氧或氫氧根發生置換反應,生成氯化鹽類,而硝酸則為鈍化膜之生成有促進之效果。目前硫酸銨結晶系統大多為不銹鋼,我們詢問原廠。其建議硝酸耐受濃度小於2,000ppm,而鹽酸則為40ppm,兩者相差50倍之多。
3.研究方法
3.1 硝酸法之可行性研究
為驗證文獻中之反應機制是否適用於廢硫酸中雙氧水之去除,我們在實驗室中組了一套實驗設備以進行驗證,並驗證最佳之操作參數。(如圖3所示)。
圖3:實驗設備示意圖
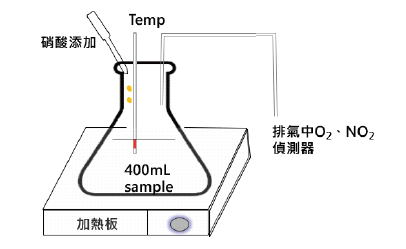
實驗樣品則取自廠區之廢硫酸(60%硫酸、3%雙氧水),實驗之控制因子為反應初始溫度、硝酸添加量;分析項目則為反應前後之雙氧水&硝酸之濃度、反應後之排氣中物種濃度以及反應中之溫度,表2為分析項目、方法以及所需儀器之一覽表。
分析項目 | 分析方法 | 分析儀器 | |
---|---|---|---|
反應溫度監測 | 溫度計監測 | 溫度計 | ![]() |
NO3−濃度 | 酚二磺酸比色法 | 分光光度計 | ![]() |
H2O2濃度 | 滴定法 | Titrator | ![]() |
排氣NO2、O2濃度分析 | NDIR法 | 氣體分析儀 | ![]() |
3.2 模廠測試驗證
在完成上述實驗室等級之測試後,為了進一步優化測試數據以及作為成廠設計之參考等目的,我們組裝一套模廠設備,並以廠區內之廢硫酸樣品進行測試。圖4分別為模廠設備示意圖以及現場照片,包含一內建攪拌器且保溫效果佳之反應器(容積:30Liter)、精準控溫之加熱系統、硝酸添加系統、硫酸傳輸系統、排氣處理系統等設備單元。
圖4:模廠設備示意圖
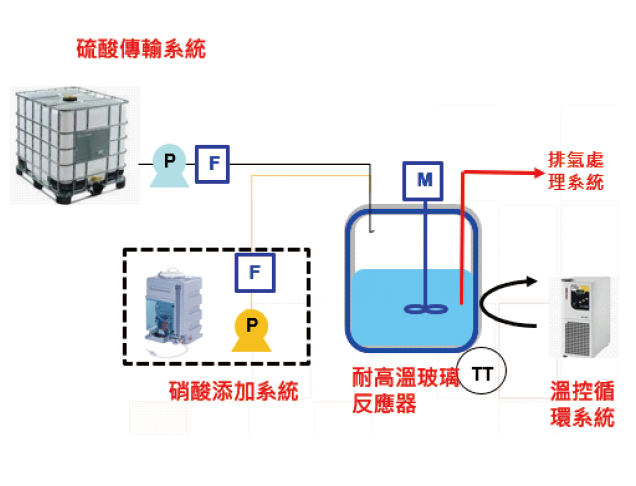
4.結果與分析
4.1 硝酸法之可行性驗證結果
4.1.1 反應初始溫度及實驗設計
我們在廢硫酸樣品中加入硝酸後,發現無反應現象,故使用加熱板來加熱廢硫酸樣品,加熱至90℃時,方觀察到開始有氣泡產生,顯示雙氧水分解反應啟動,此實驗結果可用圖5(催化劑vs活化能關係圖)來解釋,在硝酸(催化劑)存在條件下,活化能能階變低,只要溫度大於90℃時,即可突破H2O2分解之能量障礙,此溫度90℃即為硝酸催化反應之初始溫度。後續將以90℃溫度為基準設計幾個操作溫度,並搭配硝酸添加量,共設計6個實驗組以驗證出最佳的操作參數,其測試結果如表3所示。
圖5:催化劑與活化能之關係圖

組別 | 實驗因子 | 實驗結果 | ||||
---|---|---|---|---|---|---|
初始溫度 (℃ ) | 硝酸添加量 (uL) | 反應中最高溫度 (℃ ) | 硝酸根含量 (ppm) | 雙氧水含量 (ppm) | 雙氧水去除率 (%) | |
1 | 100 | 400 | 132 | 138.8 | 22 | 99.93 |
2 | 110 | 400 | 136 | 72.6 | 2 | 99.99 |
3 | 110 | 300 | 136 | 41.9 | 2 | 99.99 |
4 | 120 | 300 | 140 | 6.8 | 0 | 100 |
5 | 120 | 250 | 139 | 0 | 0 | 100 |
6 | 120 | 200 | 138 | 3.2 | 4 | 100 |
4.1.2 實驗結果分析
分析6組實驗之數據,雙氧水去除率均可達99.9%以上,而硝酸根之殘留值則隨著初始溫度的上升逐漸下降。其中第5組實驗中,初始溫度為120℃、硝酸添加量為250uL,雙氧水&硝酸根之殘留值均為 0ppm。由此我們研判硝酸與雙氧水反應分解放熱,樣品之溫度自原先120℃提高至140℃,將樣品中殘留之硝酸蒸發而逸散至排氣中。為驗證此推論,我們調配含有500ppm硝酸根之硫酸樣品(不含雙氧水)進行加熱,發現樣品中之硝酸濃度可自原先500ppm 降至40ppm(如圖6所示),確認硝酸可透過加熱方式進行去除。
圖6:硝酸殘留量vs.溫度之實驗曲線圖
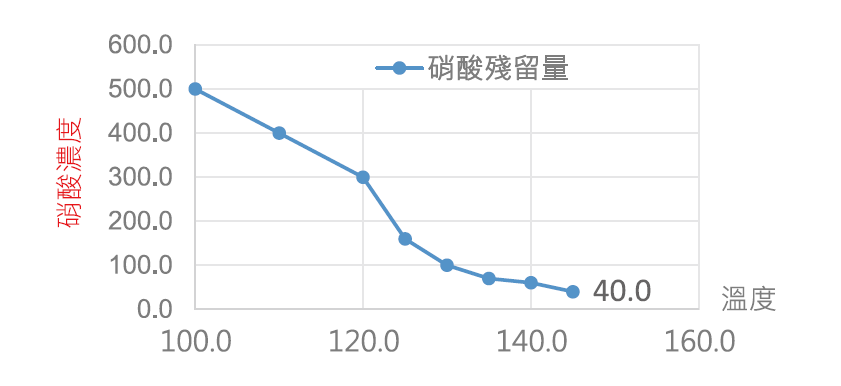
綜上實驗結果,我們歸納以下之結論:適量的硝酸添加量以及初始溫度等操作參數,確實可將雙氧水完全分解且無殘留物,且溫度更是關鍵因子,其不僅提升反應速率,減少藥劑添加以及反應時間、並可將未反應之硝酸加以揮發,使硝酸之殘留降至最低。
❶硝酸催化反應:
❷硝酸去除機制:
4.2 模廠測試結果討論
4.2.1 最佳操作參數之放大實驗
我們將實驗室所測得之最佳操作參數(初始溫度:120℃、硝酸添加量250uL),廢硫酸樣品量自400mL放大到25L(放大62.5倍),硝酸添加量僅Lab test 的1/3量時(硝酸量:硫酸樣品量=5mL:25,000mL,約200ppmV)即觀察到大量氣泡產出,因此停止硝酸添加。待反應結束後測得雙氧水及硝酸根兩者數據皆可為0,完全複製Lab test之測試結果。究其可能原因有是模廠反應器之保溫效果良好,其不僅有保溫夾套外且有上頂蓋之設計可以減少熱量散失以及減少NO2之逸散,可持續與雙氧水進行連鎖反應,另一原因是反應器內建攪拌器,混和效果更佳,提高反應速率。(如圖7所示)
圖7:反應器之實體照片圖
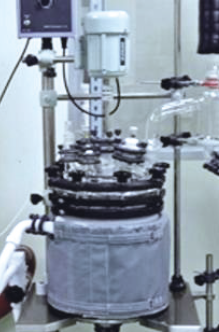
4.2.2 降溫實驗初始溫度
另外我們也進行一組最低初始溫度90℃之模廠測試,以驗證其硝酸根殘留濃度,實驗後硝酸測值為40.5ppm,遠低於硫酸銨結晶設備原廠建議值2,000ppm。
由上述實驗,我們可以透過初始溫度之調整來決定回收硫酸之產出品質。往後可以依據回收硫酸之應用場合來調整操作參數。
在完成模廠測試後,我們對於硝酸法之操作參數更加清楚,也與既有鹽酸法做一比較。(表4)
鹽酸法(既有方法) | 硝酸法(新評估) | |
---|---|---|
催化藥劑 | 32%鹽酸 (bp:84℃) | 60%硝酸(bp:121℃) |
反應溫度 | 80~100℃ | <120℃ |
雙氧水分解所需時間 | 6~20hr | 10~20min |
反應速率(每批次) | 8~24hr | <4hr |
藥劑添加量 | 1~1.5%(v/v) | 0.020%(v/v) |
雙氧水殘留 | <50ppm | <20ppm |
4.3 實廠設備規劃
完成硝酸法之可行性驗證後,我們也同時著手硬體系統之設計。硝酸法與鹽酸法比較,相對高溫且耗能,因此我們評估導入兩個全新設備:
❶耐高溫之搪玻璃反應器:因硝酸法初始溫度約>90℃,添加硝酸反應後之溫度隨之提高15~20℃,已超過既有PFA Ling Tank之適用範圍(<90℃),因此評估導入耐高溫之搪玻璃反應器(可耐溫至200℃)。搪玻璃反應器製作工藝不同於PFA Lining Tank是將膠水貼附方式,而是以除耐高溫、耐腐蝕等優點外,其內建攪拌器之設計,與既有Pump循環方式相較,混和效果更佳,提高反應速率。圖8為搪玻璃反應器之特點說明。
圖8:搪玻璃反應器之特點說明
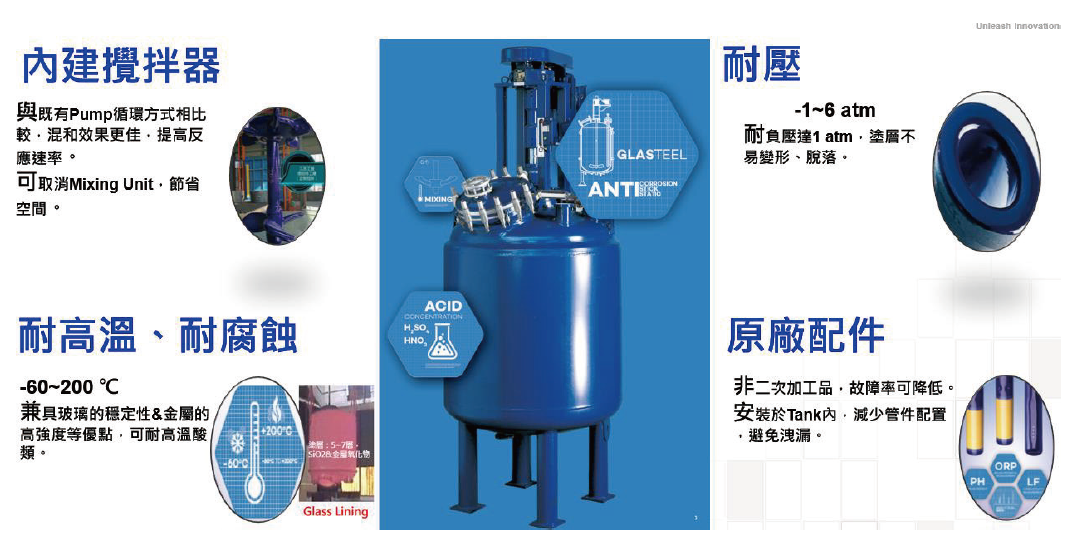
❷熱回收設備:導入耐高溫、耐腐蝕以及高熱傳導率的碳化矽熱交換器,將硫酸成品之餘熱來預熱下一批之待處理廢硫酸,以減少能耗。
5.結論
透過實驗室及模廠兩種不同等級之測試,驗證,硝酸法可透過適量的硝酸添加量以及溫度控制等操作手法,確實可把廢硫酸中雙氧水完全去除,且無殘留物之存在。其中溫度之控制更是為關鍵因子,不僅可減少藥劑添加量、縮短反應時間,並降低硝酸之殘留量。與既有鹽酸法做一比較,硝酸法藥劑添加量少,並且不純物之殘留值也可降至最低
目前FRC Committee已決議改造中科F15P5廠區之既有廢硫酸處理系統(WSR)以進行驗證,未來有機會納入於新廠設計以取代既有鹽酸法,成為新世代的廢硫酸回收處理系統(WSR2.0)。
參考文獻
- David Gray,The Reaction of Hydrogen Peroxide with Nitrogen Dioxide,1972,The Journal of Physical Chemistry Volume 76.
- 李崑池,以活性碳進行半導體廠含雙氧水清洗製程廢液回收處理之研究,2011,崑山科技大學環境工程系。
- 陳鴻賓,不鏽鋼的耐腐蝕性,防蝕工程第六卷第一期p44~60,1992。
- 維基百科。https://zh.m.wikipedia.org/wiki/酸度系數
- 呂欣、劉明翰,廢硫酸去除雙氧水系統 安全防護提升,廠務季刊Vol.32。
- 曾治寰、郭中閔,廢硫酸去除雙氧水系統最佳化探討,廠務季刊Vol.44。
- 林力雋,無憂無氯_低濃度廢硫酸回收效率提升及品質優化,廠務季刊Vol.48。
- 中華民國專利I555702號(回收廢硫酸溶液的方法與裝置),2016。
留言(0)