摘要
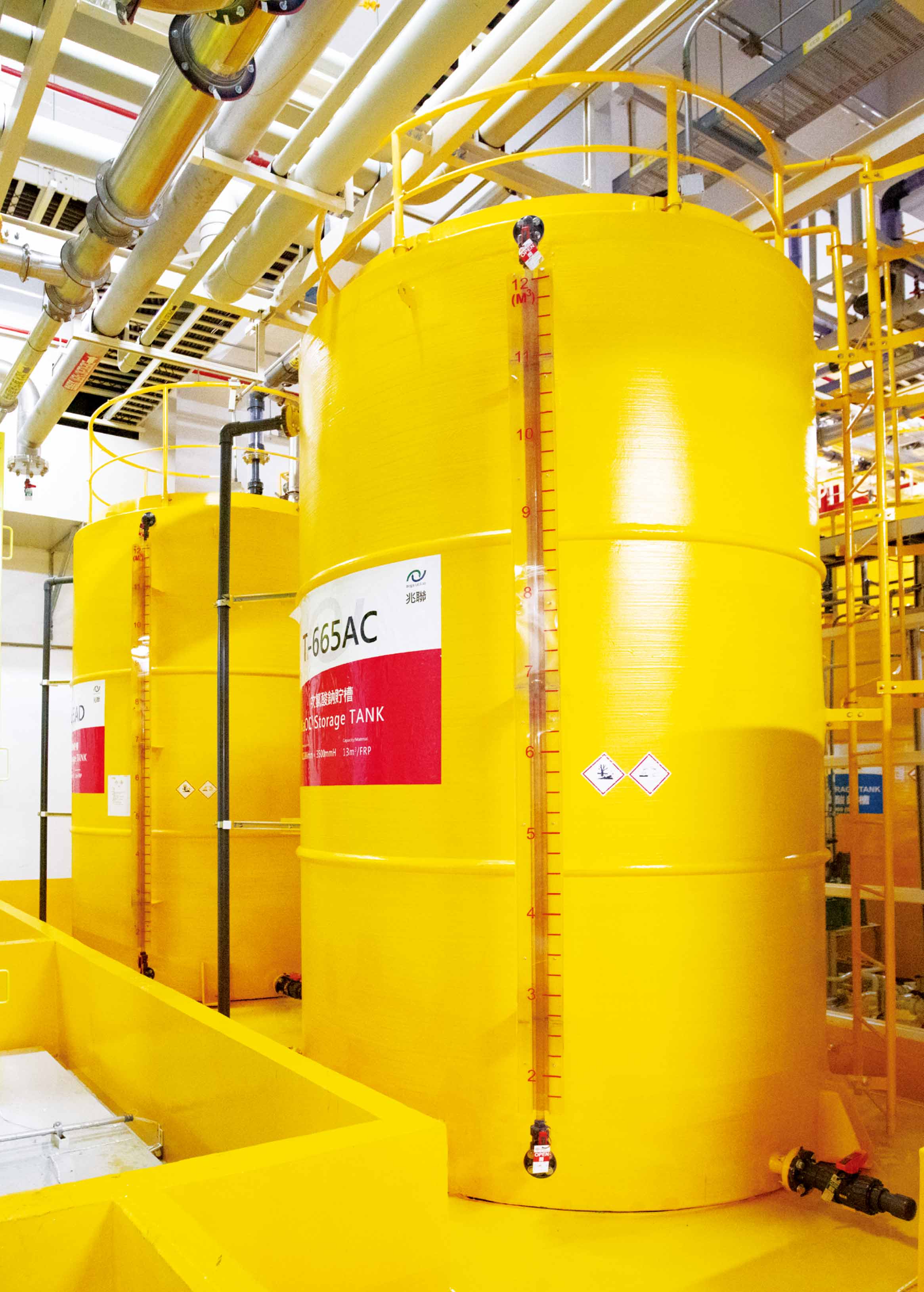
先進封裝廠含高濃度雙氧水廢液處理技術與實務探討
前言
高濃度雙氧水銅蝕刻液(LDPP)為先進封裝廠蝕刻產出之特有酸性/重金屬化學品,主要使用於先進封裝二廠(AP2)與先進封裝三廠(AP3)蝕刻製程,該製程廢液中含1~8%雙氧水(H2O2)與3%磷酸(H3PO4)。AP2與AP3廠區廢液量佔全公司廢液總量9%,其中W-LDPP為先進封裝廠獨有廢液,每月總排放量約840噸,佔先進封裝廠區廢液總量近50%,如 圖1所示。根據郭亮等人(2014)研究[1],廢液中雙氧水濃度與化學需氧量(COD)成正相關,實際量測W-LDPP COD高達25,000ppm,依管理局規定放流水COD標準需小於450ppm,且雙氧水會自我分解產生氧氣,於廢水處理系統造成金屬沉降效率變差,雙氧水濃度高於50ppm時不建議排入廢水系統處理,故未處理前W-LDPP廢液需委外廠商清運處理,依廢液槽車每次清運量12噸計算,平均每月需清運70次,一天清運次數達2至3次,如此頻繁清運導致高運轉風險與高額委外處理費用。
圖1、廢液量百分比
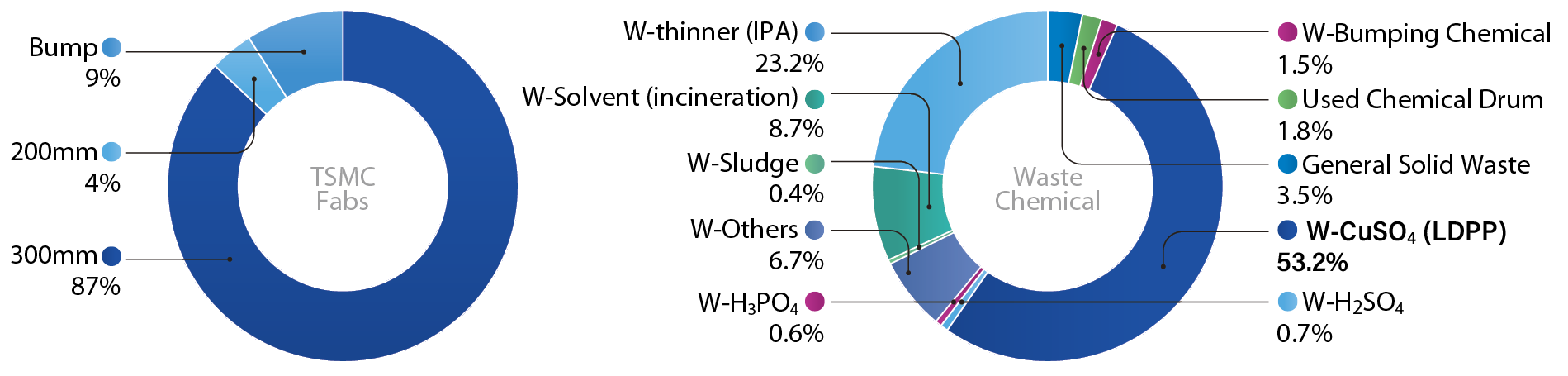
因此我們設計將含高濃度雙氧水廢液經由前處理變為符合外排規範的廢水。因應廠區空間有限,無法新增全新的處理系統與桶槽,因此規劃修改既有廢液桶槽並增設雙氧水處理功能,將W-LDPP廢液將由含銅廢液變成含銅廢水,再利用廢水金屬沉降系統去除銅金屬,達到含高濃度雙氧水廢液自行處理目標。
文獻探討
高濃度雙氧水處理技術
晶圓廠區許多去除雙氧水的方式與技術,目前常見應用於濃度3%內的雙氧水處理,尚無實際針對高濃度雙氧水廢液進行處理,晶圓廠常見處理雙氧水方法有活性碳法、酵素法、HCL法、UV法等,藉由前人文獻指出選用適合的處理方式需考量效率與運轉風險,如邱品嘉(2005)[2]研究指出UV法因紫外光限制,無法穿透水中無機鹽,導致去除雙氧水效率較差,陳建達(2015)[3]與蔣崴(2010)等人[4]提出活性碳處理雙氧水有堵塞等風險,考量先進封裝廠區空間有限,已無閒置空間新增桶槽,因此考慮雙氧水去除效率、系統運轉成本、空間需求、反應溫度、操作安全風險與環保等相關考量,藉由矩陣圖配比權重後分析,選出酵素法為本廠區最適合的高濃度雙氧水處理方法 表1。
去除方法/item |
活性碳法 |
HCL法 |
酵素法 |
UV法 |
權重標準 |
|
---|---|---|---|---|---|---|
H2O2 |
去除率 |
5 |
3 |
5 |
1 |
5分>99% |
成本 |
運轉成本 |
5 |
3 |
5 |
1 |
5分<0.1MNTD/Y |
風險 |
空間需求 |
3 |
5 |
3 |
3 |
5分_可用既有設施/桶槽修改 |
操作溫度℃ |
5 |
1 |
3 |
5 |
5分_<40C |
|
操作風險 |
3 |
3 |
5 |
5 |
5分_無毒氣/無堵塞風險 |
|
廢棄物產出 |
1 |
5 |
5 |
3 |
5分_無產出 |
|
分數 |
22 |
20 |
26 |
18 |
|
酵素添加實驗規劃
依吳旻學(2013)[5]與研究指出,酵素具有活性,隨pH值和溫度的改變,其活力隨之變化,當酵素與含有雙氧水廢液反應時,如遇到極端pH有可能造成失活現象,故酵素在pH介於中性活性最佳。本次實驗取樣分析W-LDPP原始廢液pH為1,屬於強酸性,應注意避免酵素與未調整原廢液直接接觸,需將pH提升至中性後,再添加酵素去除雙氧水,因此本文實驗計畫先將W-LDPP調整pH至7後再添加酵素,本文共三種不同酵素進行評估,規劃三組實驗組 表2固定添加50ppm酵素,觀察其處理效率。
酵素實驗組別 |
廢液 (pH) |
廢液H2O2濃度 |
反應時間 (min) |
轉化率 |
|||
---|---|---|---|---|---|---|---|
0 |
10 |
20 |
30 |
||||
對照組 |
7 |
53,000 |
添加酵素反應 |
效率 比較 |
|||
實驗組 1 |
|||||||
實驗組 2 |
|||||||
實驗組 3 |
雙氧水去除槽安全設計
因應廠區空間限制,封裝廠將既有閒置廢液桶槽進行資源活化,將其修改為雙氧水去除槽(Reaction tank),趙怡欽(2005)[6]等人提及高濃度雙氧水因自解後產生大量的熱源與氧氣,具高度風險,AP2含雙氧水廢液桶槽曾因排氣不及導致破裂,可知雙氧水去除槽內H2O2經分解後若氧氣無適當排出累積於反應桶槽內,或反應熱能導致W-LDPP廢液溫度遽烈提升,將對安全性危害極大,因此槽體安全設計必須考量槽內氧氣釋放量與冷卻需求,王聖文(2015)[7]研究指出可藉由理論公式推導出合理設計,由式(1)~(3)計算出氧氣釋放量與廢液升溫程度:
質量不滅定律:
..............(1)
理想氣體方程式:
...........................(2)
熱力學定壓比熱公式:
.........................(3)
其中,式(1)的符號說明n為物質的莫耳數(單位:mol),m為物質的質量(單位:g),M為物質的分子量(單位:g·mol-1),V為物質的體積(單位: ml),d為物質的密度(單位:g·ml-1),Vm為理想氣體的莫耳體積(單位:L·mol-1);式(2)的符號說明P為理想氣體的壓力(單位:atm),V為理想氣體的體積(單位:L),n為理想氣體的莫耳數(單位:mol),R為理想氣體常數(0.082atm·L·mol-1·K-1),T為理想氣體的絕對溫度(單位:K);式(3)的符號說明ΔH為反應吸收或釋放的熱量(單位:J),m為物質的質量(單位:g),S為物質的比熱容(單位:J·g-1K-1),ΔT為反應的溫度變化(單位:K)。
雙氧水去除槽冷卻系統建置目的在於控制反應槽內廢液溫度,依不同廠區廢液濃度狀況不盡相同,陳昭義(2004)[8]與李崑池(2005)[9]等人研究發現雙氧水溫度達40℃將開始自我加速提升反速率,60℃則達失控反應,此時若無外力介入將持續快速升溫,安全風險大幅增加,因此建議反應溫度高於40℃需建立冷卻系統。反之若分解後反應熱能於桶槽內升溫不高於40℃,則可評估不建置冷卻系統達降低建置成本。
廢水沈降處理
利用廢水金屬處理將已去除雙氧水後W-LDPP廢液去除含銅金屬(反應流程如 圖2所示),依張玉霞(2004)[10]報告指出含銅金屬適當沉降pH值為8~10 圖3,為避免影響放流水質,廠區規劃廢水金屬反應槽pH調整至8~9, 此條件下大部分金屬離子轉變成難溶於水的氫氧化物鹽類,再於慢混槽添加Polymer混凝劑與重金屬捕捉劑,形成膠羽汙泥沉澱後去除metal-ion,反應式:Cun++OH-→Cu(OH)n。即可將含金屬廢水轉成適合放流的一般廢水。
圖2、廢水金屬處理系統
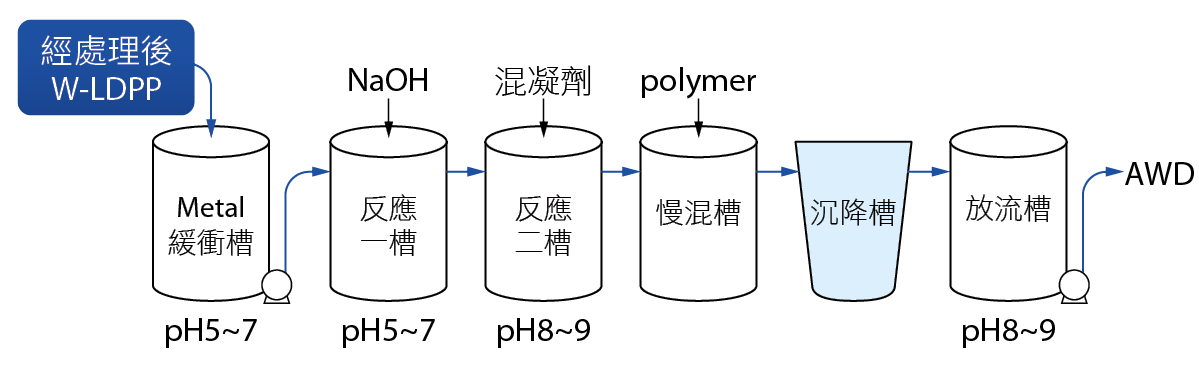
圖3、各金屬氫氧化物沈降pH值
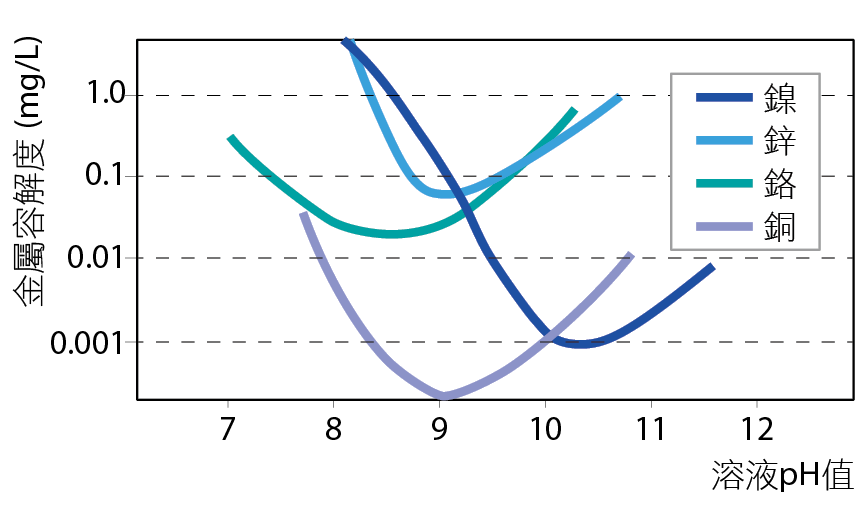
計畫方法
W-LDPP雙氧水去除系統建立規劃
本文規劃新增雙氧水去除槽來進行酵素處理,將廢液儲存槽新配置管路與雙氧水去除槽連接,於雙氧水去除槽中進行雙氧水去除反應,待廢液中雙氧水去除後輸送至廢水金屬沉降系統,含銅金屬經由沉降處理後的廢液符合廢水放流標準,如此即可避免廢液槽車清運,僅保留其功能作為緊急應變時的備案,整體W-LDPP廢液排放系統流向架構 圖4。
圖4、W-LDPP排放流向系統架構圖
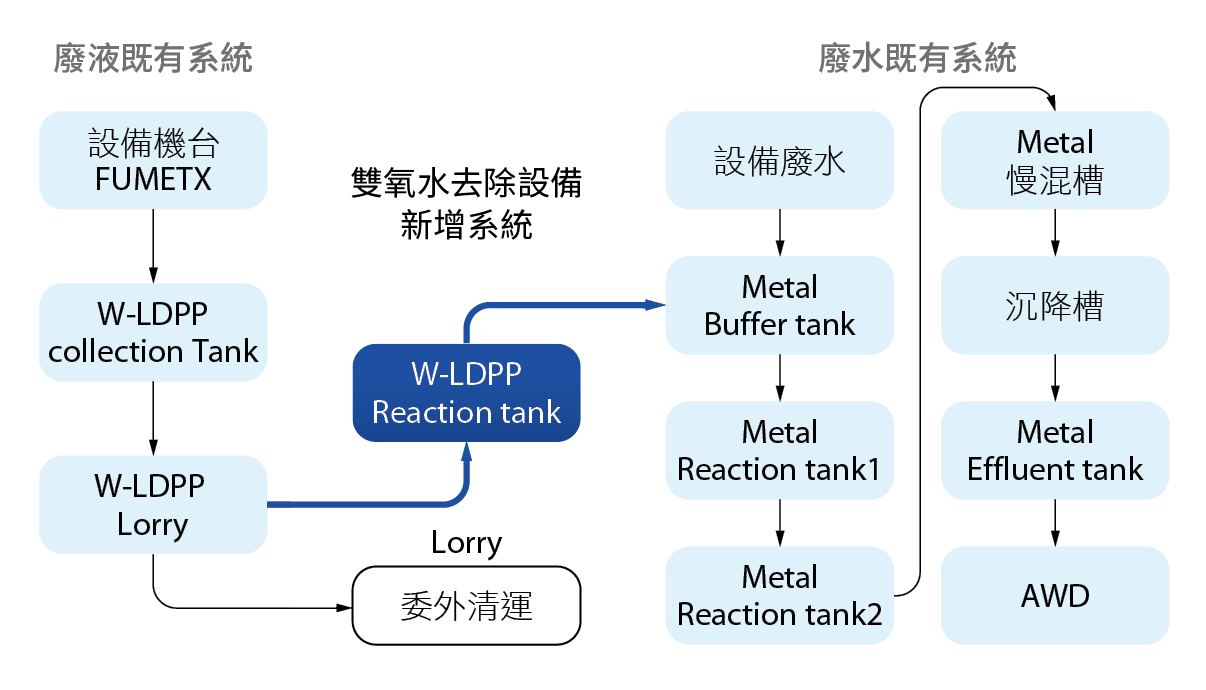
不同酵素濃度測試去除H2O2效果
實驗規劃添加不同種類酵素觀察處理效率,筆者採用三種不同廠商酵素(實驗組1:鋒×/實驗組2:帆×/實驗組3兆×),觀察添加酵素於W-LDPP後雙氧水剩餘濃度,由Jar-tester實驗顯示,實驗組3於30分鐘內可將W雙氧水濃度由5%降至<5ppm,轉化率達99.9%,處理後雙氧水濃度幾乎檢測不到,符合排放至廢水金屬沉降系統處理條件,可證實此酵素處理雙氧水具明顯效果,另外由對照組實驗結果可發現,依雙氧水本身具自我分解特性,W-LDPP即使不添加酵素也會自我降低雙氧水濃度,但此曝氣法去除雙氧水效率低,因此不適合應用於大量需處理廢液,本次反應實驗結果如 表3、圖5。
![]() |
||||||||
酵素實驗組別 |
廢液 (pH) |
廢液H2O2濃度 |
反應時間(min) |
處理後廢液H2O2濃度 |
轉化率 |
|||
---|---|---|---|---|---|---|---|---|
0 |
10 |
20 |
30 |
|||||
對照組 |
7 |
53000 |
53000 |
52400 |
52100 |
51800 |
51800 |
2.2 |
實驗組 1 |
53000 |
28000 |
10800 |
3270 |
3270 |
93.8 |
||
實驗組 2 |
53000 |
16000 |
4200 |
1190 |
1190 |
97.7 |
||
實驗組 3 |
53000 |
6550 |
230 |
3 |
3 |
99.9 |
圖5、去除H2O2效果實驗組比較圖
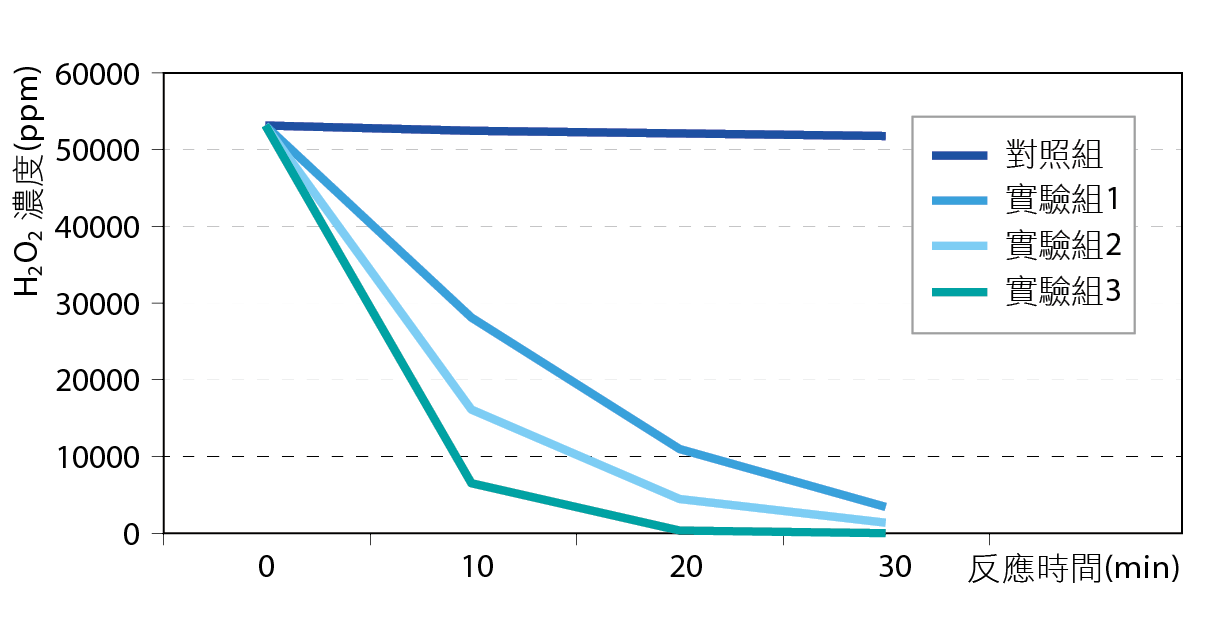
相同實驗條件下進行酵素濃度升溫實驗,實驗發現當酵素與廢液接觸後,開始進行反應約10分鐘左右釋放溫度達最高點,實驗中最高溫度不超過40℃ 圖6,這證實酵素處理雙氧水效果迅速且初始階段快速釋放熱能與氧氣,此時氣泡反應最為劇烈,實驗分析數據如 表4。
圖6、酵素處理溫度變化曲線圖
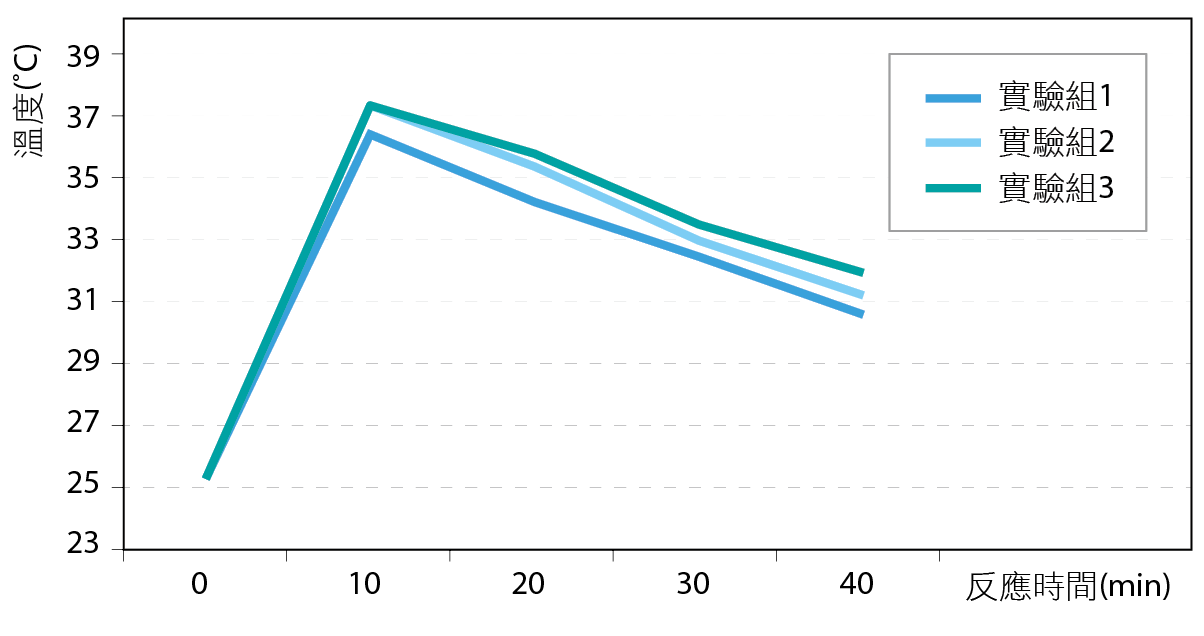
反應時間 (min) |
添加酵素濃度(ppm) |
||
---|---|---|---|
實驗組1 |
實驗組2 |
實驗組3 |
|
30 |
40 |
50 |
|
0 |
25.3°C |
||
10 |
36.4°C |
37.3°C |
37.3°C |
20 |
34.2°C |
35.4°C |
35.8°C |
30 |
32.5°C |
33°C |
33.5°C |
40 |
30.6°C |
31.2°C |
31.9°C |
廢水沈降處理效果實驗
確認酵素能有效去除高濃度雙氧水廢液後,仍需確保可排至廢水金屬沈降處理系統,因此實驗中針對原始金屬沈降槽(Metal廢水)與經處理雙氧水後廢液進行實驗,結果如 表5,W-LDPP廢液經金屬沈降後銅離子濃度由122ppm降至1ppm,證實處理雙氧水廢液排入廢水金屬沈降處理系統是可行的。
樣品 |
Metal |
AP2B LDPP |
Metal廢水/W-LDPP De-H2O2 (1:1) |
---|---|---|---|
Cu濃度 (ppm) |
9.17 |
122.2 |
1.09 |
實驗照片 |
|
|
|
雙氧水去除槽安全設計
酵素處理雙氧水效率佳,因此短時間內將釋放大量熱能與氧氣,因此雙氧水去除槽安全設計必需考量氧氣釋放量與冷卻系統設計,以先進封裝廠為實例說明依設計理論應用。
雙氧水去除槽氧氣釋放量理論計算
以最惡狀況(Worse Case)條件為去除槽每小時處理W-LDPP廢液500L,其中含8% H2O2,依式(1)質量不滅定律計算,氧氣產出量約為19m3(式4-5),根據亞佛加厥定律,雙氧水(H2O2)分解反應會生成水(H2O)和氧氣(O2)
2H2O2→2H2O+O2(H2O2密度為1.463 g·ml-1;分子量為34g·mol-1)
..............(4)
..............(5)
理想氣體的莫耳體積為22.4L·mol-1,以 圖6酵素處理溫度實驗結果假設反應前溫度為25℃溫度,反應後溫度為40℃,並根據式(2)理想氣體方程式計算酵素分解雙氧水產出之氧氣於40℃膨脹體積為約20m3 (式6):
PV=nRT於等壓定量條件下可為查理定律,即
..............(6)
以實驗結果顯示,添加酵素後約10分鐘時,H2O2分解反應最劇烈,依最惡狀況評估,H2O2於10分鐘內去除率99.9%狀況下,產出氧氣量為2CMM(式7)。
..............(7)
以此結果確認抽風設計適切性;標準桶槽排氣管設計為4吋風管,在抽風速率為8min·sec-1的條件下控制抽風量為3.7CMM,其抽風能力餘度尚有46%,足夠將產出氧氣安全地排出。
雙氧水去除槽冷卻系統安全性理論計算
針對AP2廠區W-LDPP廢液H2O2濃度最高達8%,首先須計算雙氧水分解反應產生之化學反應熱對於桶槽內部溫度影響,才能選擇適當的冷卻系統掌控升溫的風險。
H2O2密度為1.463g·ml-1;分子量為34g·mol-1,以同樣條件每批次處理500L,雙氧水去除槽基礎液位3,000L,評估化學反應熱及溫度變化。H2O2分解反應所產生的化學反應熱(ΔH°)為98.2KJ·mol-1,熱力學定義為自發性放熱反應,並計算500L的W-LDPP分解產生的總化學反應熱(式8)。
..............(8)
H2O2熱容量為2.619J·g-1K-1,依式(3)熱力學定壓比熱公式,計算出W- LDPP廢液溫度變化(式9)。
..............(9)
假設反應槽初始廢液於室溫下,溫度保持於25℃,因此未冷卻狀況下反應槽內廢液溫度將達到43℃,滿足自我劇烈反應條件,因此需設立冷卻系統進行降溫,冷卻系統採用廠區12℃製程冷卻水進行冷卻,相同模式應用於AP3封裝廠區,W-LDPP中雙氧水濃度約5,000ppm,每次處理量2噸,在此條件狀況下反應熱能大幅下降至42,254KJ,桶槽溫度僅上升3℃,因此經評估後無須設立冷卻裝置,升溫評估結果如 表6。
先進封裝廠 |
處理條件 |
廢液中 |
每次廢液 |
廢液 |
H2O2反應後 |
廢液 |
處理槽 |
處理槽 |
---|---|---|---|---|---|---|---|---|
AP2 |
最惡條件 |
8 |
500 |
1,721 |
169,002 |
18 |
25 |
43 |
真實狀況 |
5 |
500 |
1,076 |
105,637 |
11 |
25 |
36 |
|
AP3 |
最惡條件 |
1.2 |
2,000 |
1,033 |
101,411 |
7 |
25 |
32 |
真實狀況 |
0.5 |
2,000 |
430 |
42,254 |
3 |
25 |
28 |
結果與分析
高濃度雙氧水去除系統運作流程
依實驗結果進行處理流程設計規劃,將W-LDPP經泵浦傳輸到新增Reaction tank,添加液鹼至中性後再添加酵素,待系統濃度計分析雙氧水濃度低於50ppm,再經泵浦傳輸至廢水Metal系統進行金屬沉降處理,處理邏輯架構流程如 圖7。
圖7、酵素處理雙氧水邏輯流程圖
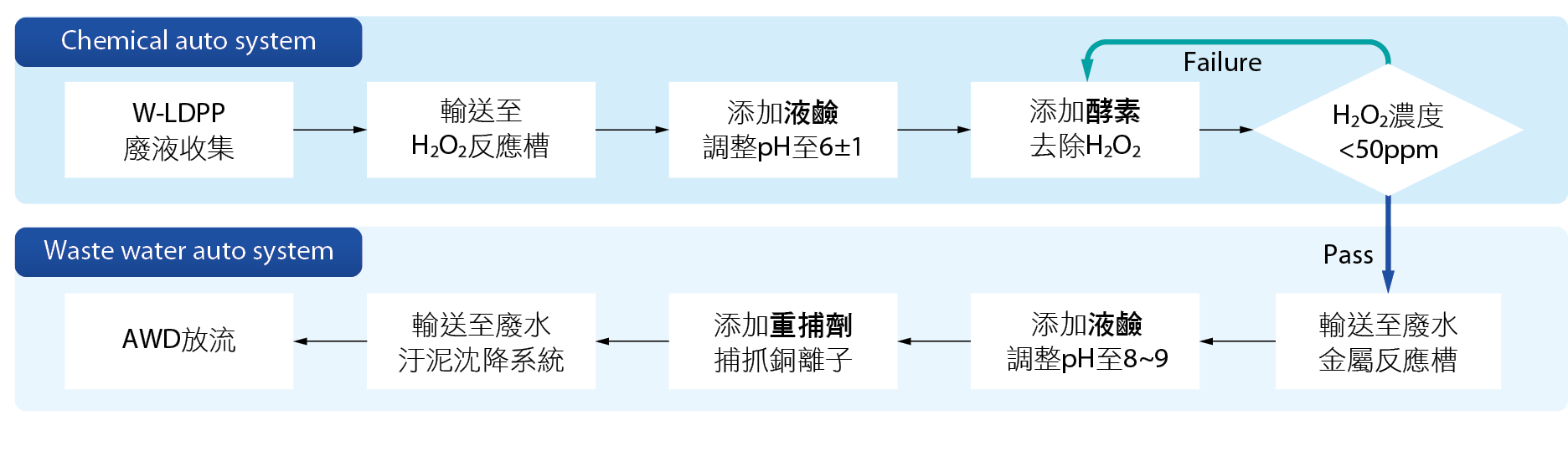
系統防禦機制與運作邏輯
廠區新增雙氧水去除槽來進行酵素處理,將廢液透過泵浦轉移至Reaction tank,透過泵浦循環監控去除槽內pH狀態並利用PIC控制閥自動計算添加液鹼NaOH將廢液pH值由酸性調整為中性,本系統為達到高效率的反應混合在去除槽內配有攪拌棒之設計,使槽內廢液造成擾流達到短時間高混合比,並藉由蠕動式泵浦定時定量添加酵素進入去除槽。
此步驟會將廢液中H2O2進行分解,反應過程產生熱能與大量氣體,考量安全風險下,設計冷卻系統將反應時泵浦進行內循環並透過熱交換器降低反應熱,將反應後溫度控制於<40℃,並配置緊急注水管路,當異常升溫時開啟管路上自動控制閥注水至槽內,降低溫度與稀釋濃度達避免持續反應狀況發生。針對桶槽內氧氣釋放量安全設計,需確保桶槽排氣裝置足夠容許反應後氣體體積,但因無法控制機台端所排放的廢液濃度因此本系統建立第二道排氣防線為破裂片與緊急排氣設計,Reaction tank設計與31%H2O2純液比較規格,可發現純液(破裂片/桶槽材質/溫度計)與廢液桶槽防禦機制(透氣孔/緊急加水)皆有 表7,為降低桶槽因桶內壓力過高導致桶身破裂的風險,整個系統架構如 圖8,並列出系統安全設計項目如 表8。
項目 |
系統類別 |
純液供應桶槽 |
廢液收集桶槽 |
廢液處理桶槽 |
---|---|---|---|---|
1 |
化學品名稱 |
H2O2 |
W-TS100 |
W-TS100 |
2 |
H2O2 濃度 |
31% |
20% |
20% |
3 |
桶槽體積 |
10000L |
20000L |
12000L |
4 |
桶槽材質 |
SUS304/PTFE |
FRP |
SUS304/PTFE |
5 |
桶壁厚度(外/內) |
5/2.4mm |
8mm |
5/2.4mm |
6 |
緊急排氣口大小 |
8" |
- |
8" |
7 |
破裂片大小 |
6" |
- |
6" |
8 |
破裂片耐壓 |
1.8kg |
- |
1.8kg |
9 |
Exhaust設計尺寸 |
- |
4" |
4" |
10 |
透氣孔 |
- |
4" |
6" |
11 |
緊急排放口大小 |
2" |
- |
2" |
12 |
溫度感測器 |
V |
V |
V |
13 |
溫度alarm設定 |
V |
V |
V |
14 |
緊急加水管路大小 |
NO |
1" |
1" |
15 |
設計壓力 |
0.19MPa |
非壓力容器 |
0.3MPa |
圖8、W-LDPP雙氧水去除系統架構圖
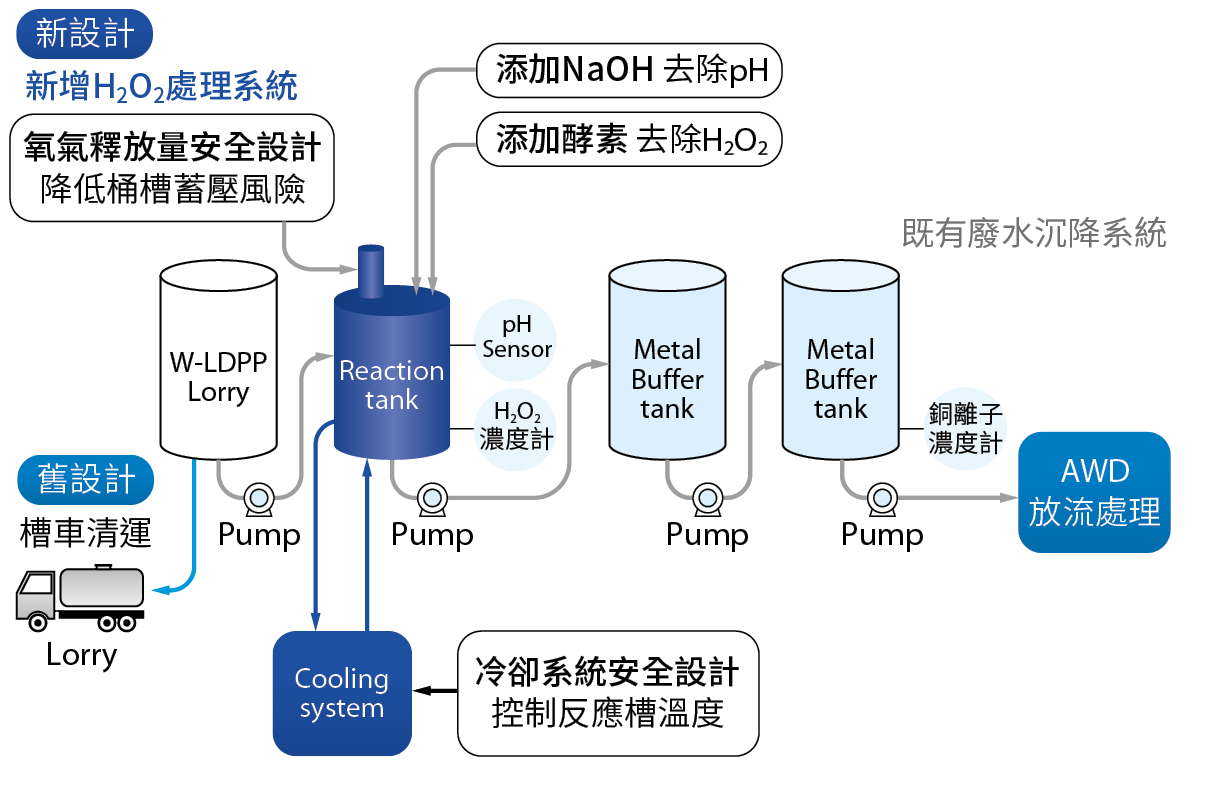
系統 |
防禦機制 |
---|---|
處理桶槽 |
桶槽採耐壓設計(SS/PTFE)×1 |
配置2種type溫度monitor (接觸式和貼付式) |
|
裝設破裂片與緊急排氣管至戶外 |
|
自動緊急加水與H3PO4功能 |
|
Exhaust設計量為產氣量之2倍大 |
|
裝設獨立Dike |
|
加藥控制 |
定量酵素控制並設立load cell做第二道確認 |
反應路徑 |
桶槽裝設攪拌器並藉由冷卻系統循環控制 |
雙氧水分析系統監控反應後濃度 |
|
pH meter dual設計 |
系統實績驗證
AP2與AP3廠區於2018年底完成W-LDPP處理槽建置,採批次式處理H2O2,處理量可依操作需求調整液位高低。以AP2 W-LDPP處理系統為例,每小時批次處理500L W-LDPP廢液,每次將待處理廢液打入處理槽,處理槽內每次預留3噸已處理廢液,如此將可稀釋反應槽內廢液之雙氧水濃度與提升pH,降低酵素催化雙氧水時所產生之反應熱能和產氣量。透過系統即時儀錶得知,添加液鹼可將廢液pH實際由原先酸性提升至中性確保酵素活性 圖9,再添加酵素進行降低雙氧水濃度作業,經由分析儀測定結果得知,W-LDPP廢液經處理槽後,雙氧水濃度可大幅降至<50ppm 圖10,即可排到既有廢水處理系統,由廢水金屬沈降處理系統抓取銅金屬後,依系統最終變成外排放流水,由 圖11與 圖12得知,經由新增的廢液處理去除W-LDPP中雙氧水後,廠區廢水處理系統有足夠能力處理並且不影響放流水濁度與銅離子殘留等問題。
圖9、添加液鹼後pH變化圖
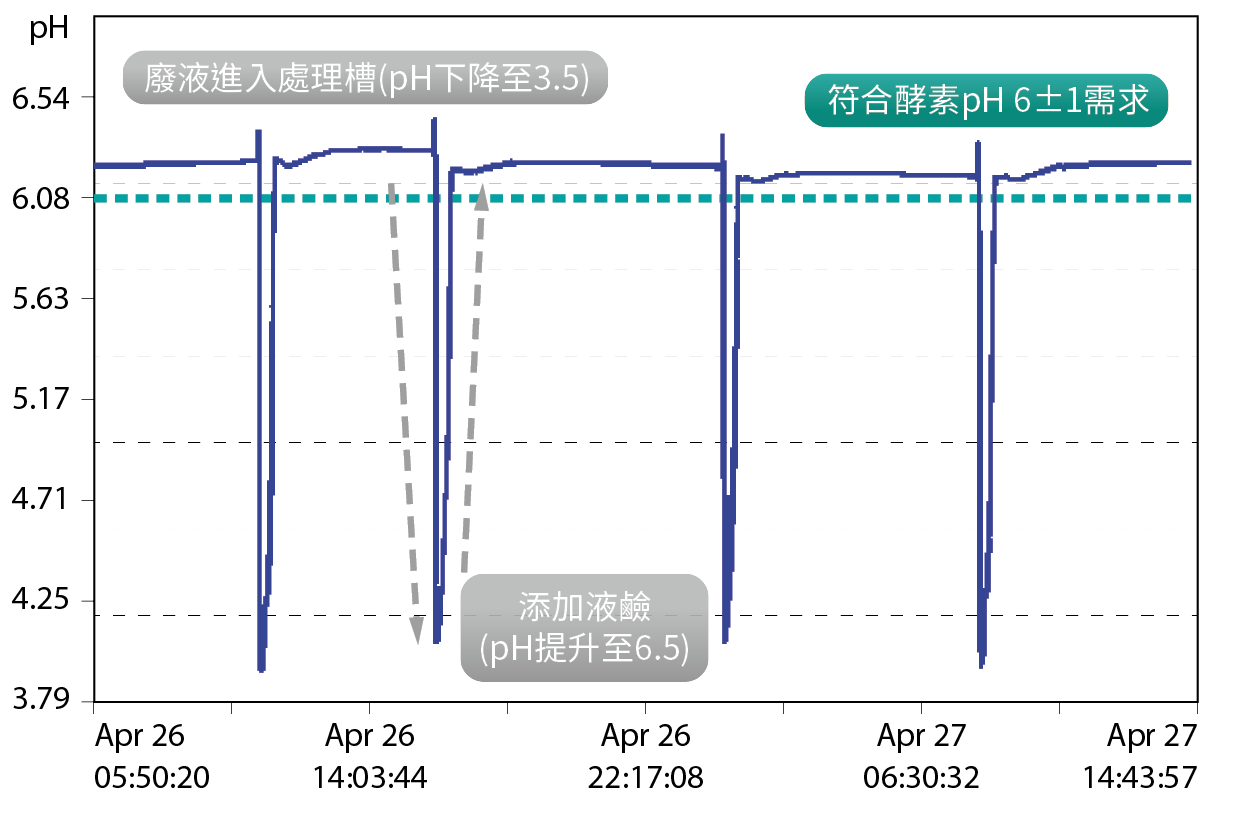
圖10、添加酵素後H2O2濃度變化圖
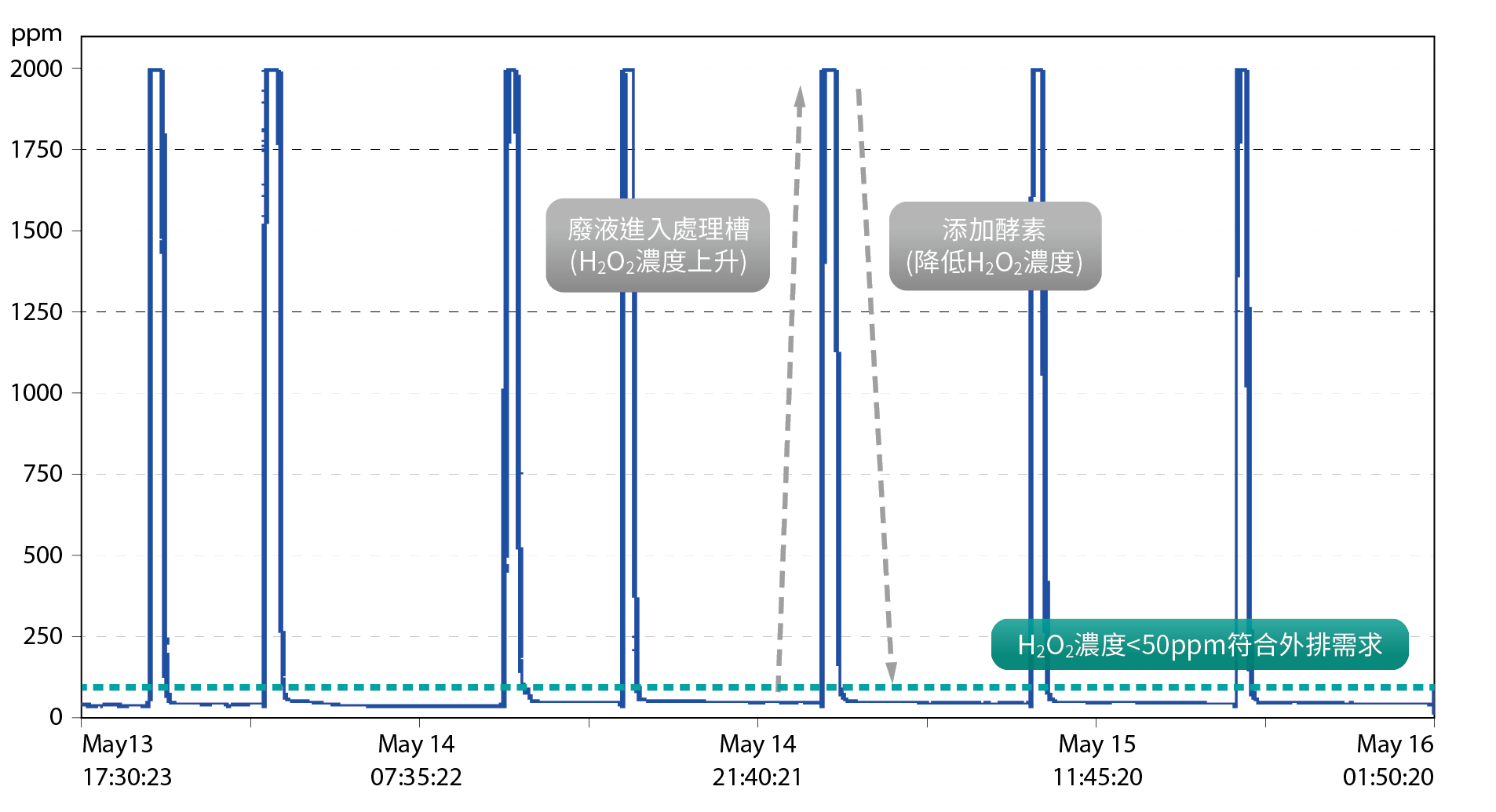
圖11、廢水放流銅離子變化圖
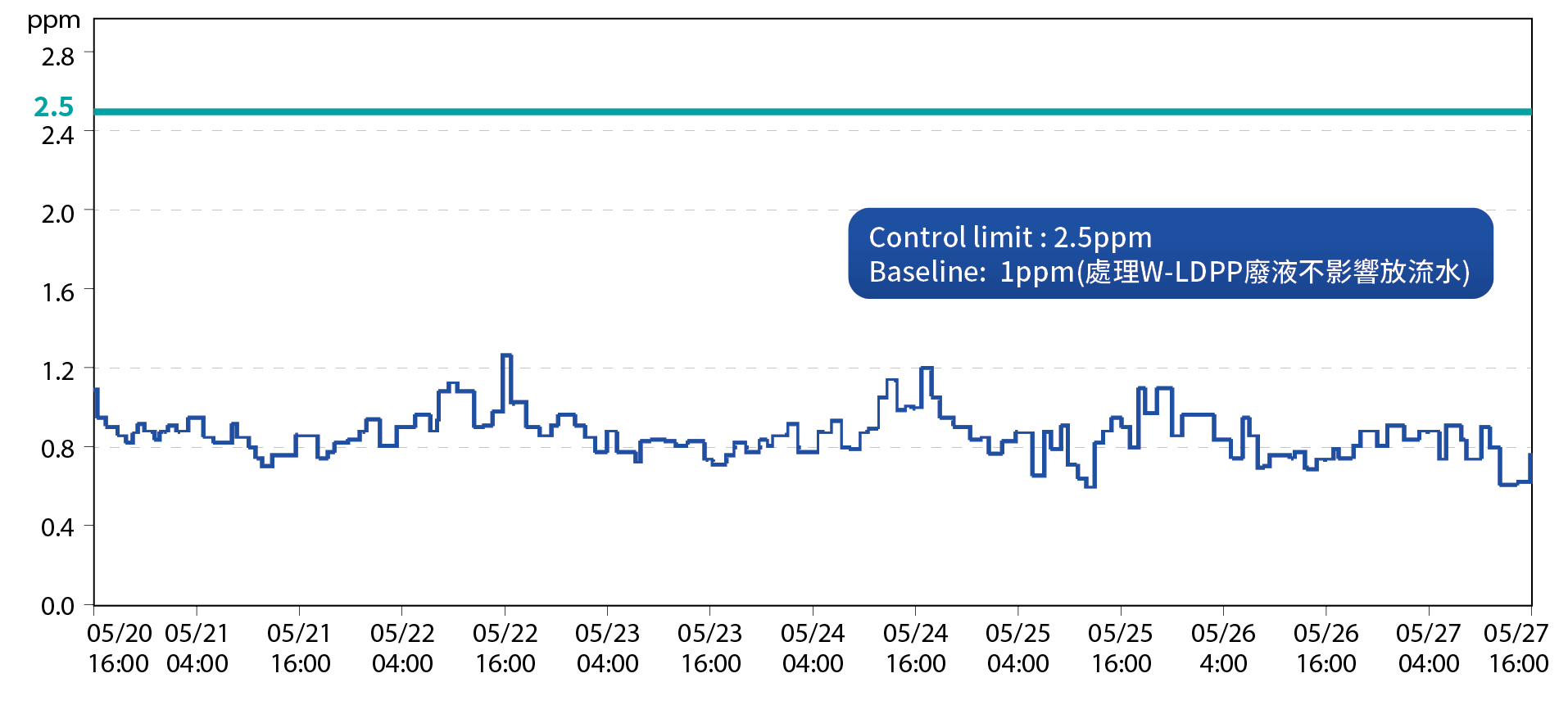
圖12、廢水放流濁度變化圖
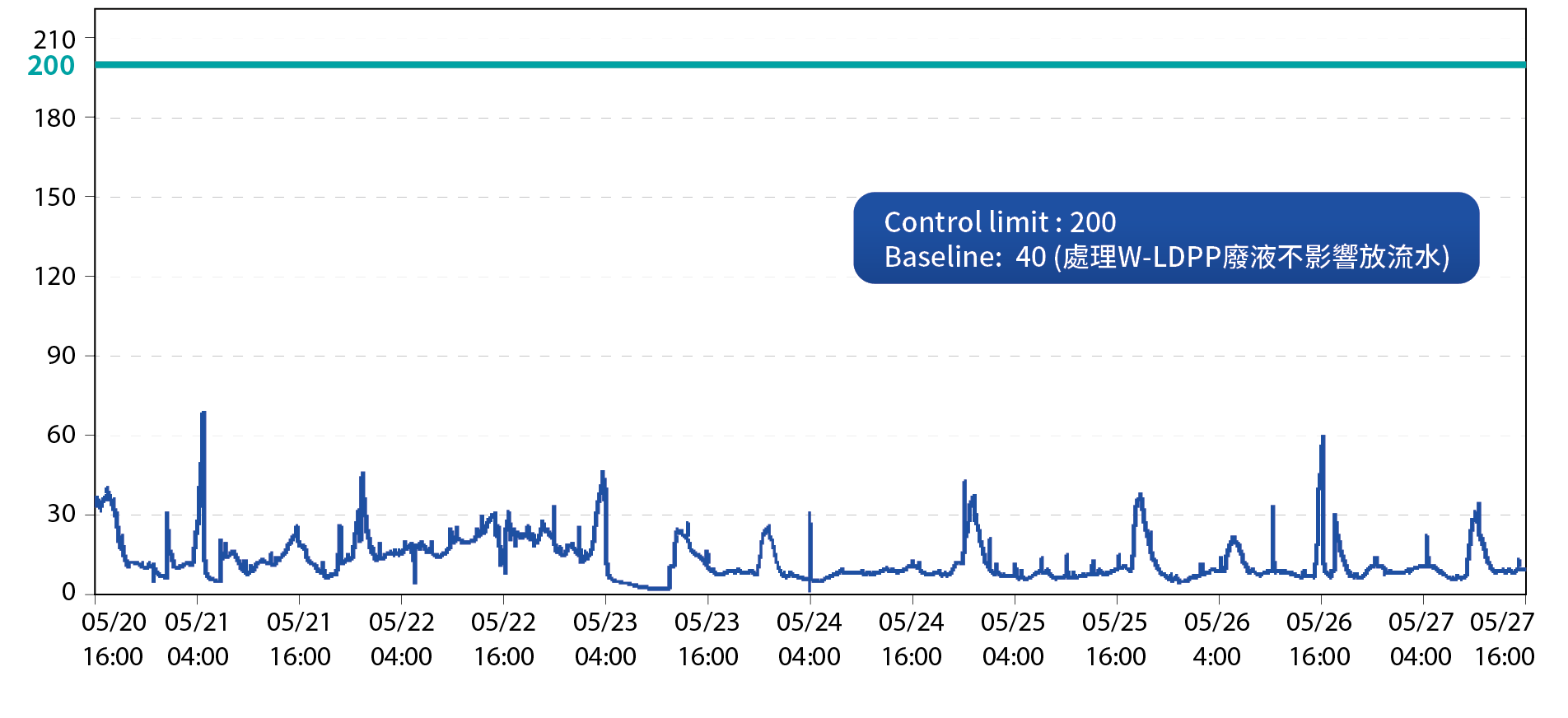
結論
先進封裝廠與前段廠區廠區特性不同,廢水量僅前段廠15%,因此前段廠區處理廢液模式無法直接應於於封裝廠,本文針對封裝廠最大宗廢液進行探討,藉由酵素實驗確認反應過程中濃度與溫度的變化,規劃廢液處理系統設計。在廢液處理中最重要的是安全性,因此針對系統氣體容積量與溫度變化是否需達冷卻標準皆有所規範,依此條件進行系統建置後,成功於2019年讓系統實際運轉上線。
處理高濃度雙氧水銅蝕刻廢液(W-LDPP)方法包含 : W-LDPP化學品廢液經處理槽添加pH至中性以確保酵素活性,再添加酵素進行去除H2O2,可穩定降低雙氧水濃度由50000ppm降至1ppm,藉由溫控與冷卻系統,有效控制處理過程所產生大量反應熱及氧氣;將去除雙氧水廢液排入廢水金屬沉降槽,調整加藥濃度透過混凝沉降後移除金屬離子,再將上層廢水打至酸鹼廢水(AWD)調勻,實際應用可透過系統監測訊息得知放流水濁度與銅離子皆無顯著變化,代表能在不影響廢水處理狀況下將W-LDPP處理後達外排放流水標準,變成符合排放標準的放流水。自系統啟用後W-LDPP廢液槽車每月清運次數降為0次,AP2與AP3廠區預估可降低公司整體清運量約1萬噸,節省清運費用達6千萬新台幣,成功達環保處理、安全提升、降低成本三贏功效。
參考文獻
- 郭亮,焦練洲,劉有智,許承騁,劉文麗,李靜,高級氧化法中H2O2對COD的測定影響及消除,中國含能材料期刊,第22卷第6期,2014
- 邱品嘉,以Fenton法及Photo Fenton法降解含磺胺甲基噁唑之廢水,碩士論文,國立中興大學環境工程研究所,2014
- 陳建達,以活性碳處理含雙氧水廢水反應行為之研究,碩士論文,崑山科技大學環境工程研究所,2014
- 蔣崴,以活性碳及含銅離子活性碳分別處理含雙氧水之半導體廠清洗製程廢水及電化學電鍍製程清洗廢水之研究,碩士論文,崑山科技大學環境工程研究所,2010
- 吳旻學,黃志彬,以過氧化氫酶酵素處理高科技廠含H2O2廢水之研究,碩士論文,國立交通大學工學院永續環境科技學程,2013
- 趙怡欽,高濃度過氧化氫分解觸媒及觸媒床之研發設計,行政院國家科學委員會專題研究,計畫編號:NSC93-2622-E-006-014-CC3,2005
- 王聖文,含雙氧水系統桶槽體積對緊急排放管徑影響之研究,碩士論文,崑山科技大學環境工程研究所,2015
- 陳昭義,製程反應失控預防技術手冊,經濟部工業局財團法人工業技術研究院環境與安全衛生技術發展中心,2004年9月初版,2004
- 李崑池,雙氧水與銅離子於半導體電化學電鍍製程應用反應相容性研究,行政院國家科學委員會專題研究,計畫編號:NSC94-2211-E-168-004,2005
- 張玉霞,無機汙泥減量技術,台灣綠色生產力基金會_廢水汙泥減量減容技術講習會,2004
留言(0)