摘要
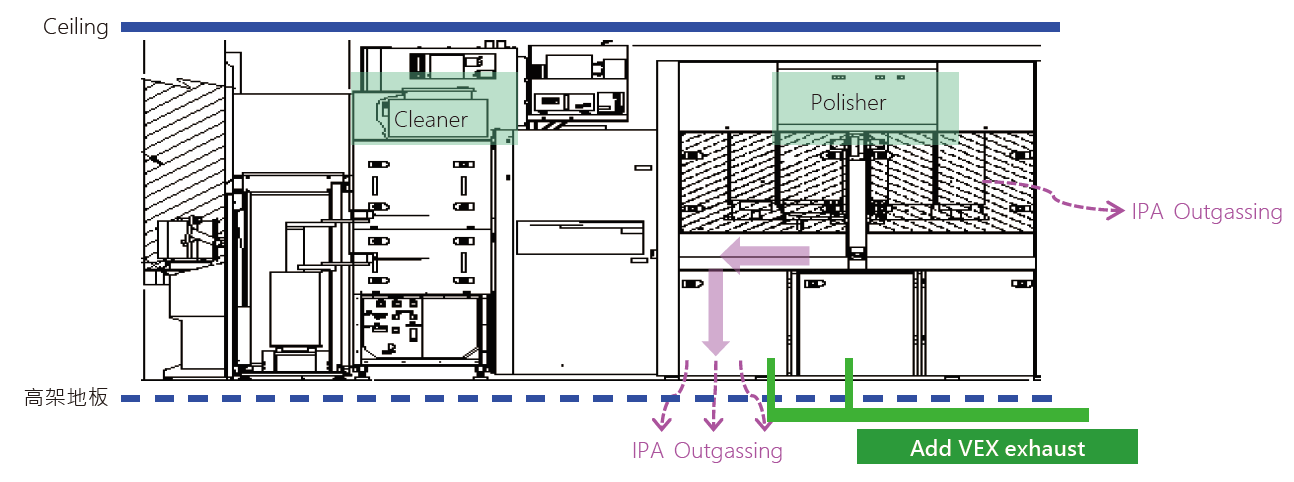
前言
異丙醇(Isopropyl Alcohol, IPA)在半導體製程中為不可或缺的原物料,其主要功能為去除晶圓上之水份,在部分機台製程過程中會被大量使用到,使用情況可分為生產需求和保養需求,A廠區針對IPA洩漏時更換濾網作業就佔總更換濾網作業的37%,因此有效的管控IPA使用及洩漏防治是重要的,其有效控管的方式除了解各機台特性之外(生產需求),也需透過機台PM作業觀察才能全面掌握廠內IPA的使用情況(保養需求),藉由分析廠內各機台使用IPA之製程,可了解哪些區域可能會有IPA逸散之現象,以A廠區為例約有51.5%的CMP研磨機台有洩漏問題;而奈米擴散製程約有14%。
原則上最佳的AMC控制策略方式就是有效的控管源頭,影響無塵室AMC污染的來源與原因相當多,將這些問題歸納分類後,主要可從外氣污染、廠房構造設計、人員PM行為與製程生產使用的化學物品等四個原因有關。不同特性的污染源需以不同的量測儀器去測定,因此選用適當的量測技術,才能迅速找出污染源並且能對症下藥有效的解決問題,本文將著重於研磨製程及擴散製程的IPA改善案例,期望能減少30%以上的濾網花費,如 表1為統整廠區內使用IPA製成機台數量的TOP10排名。
排名 | 系統製程 | 排名 | 系統製程 |
---|---|---|---|
1 | 奈米CMP薄膜 A製程 | 6 | 奈米CMP薄膜 D製程 |
2 | 奈米CMP薄膜 B製程 | 7 | 奈米擴散 C製程 |
3 | 奈米擴散 A製程 | 8 | 奈米CMP薄膜 E製程 |
4 | 奈米CMP薄膜 C製程 | 9 | 奈米CMP薄膜 F製程 |
5 | 奈米擴散 B製程 | 10 | 奈米擴散 D製程 |
文獻探討
關於AMC與Particle的污染,Muller等人[1]的研究中提出,在Class 100的潔淨室內總有機氣態污染物濃度約100 µg/m3,粒狀物濃度則約為20ng/m3,兩者的濃度相差約5000倍,所以氣態分子污染物沉積於晶圓表面之質量沉積可能為微粒的數千倍以上,因此潔淨室等級與AMC的污染濃度無直接關係,AMC的氣態污染去除主要還是依靠化學濾網去除,而粒狀物污染則是以HEPA filter(0.5µm,99.99 %)或是ULPA filter(0.1~0.2µm,99.999%)去除。
TOC可能會導致的異常包括氧化層不當成長、CMOS上Contact阻值增加、閘極氧化層崩潰電壓(voltage breakdown)的破壞因素等原因[2]此種模式的崩潰會造成產品良率的損失,其發生的原因與製程(顆粒、有機污染、金屬雜質)的原因,一般半導體廠最常用濕式清洗來確保閘極氧化層的品質的方法,SC1(standard clean 1)用於鹼水及侵蝕表面,以便於清除微粒子。同時可去除有機物及金屬污染物。而SC2(standard clean 2)主要用於清除金屬污染物[3] 。
若環境中有酸性的AMC物質在晶圓上殘留或有沉積時 ,會使得鋁線產生腐蝕,因此需管理具有腐蝕性的酸性物質(Cl-、F-),而SO42-會與NH3反應(NH3)2SO4附著在晶片上,破壞氧化膜的絕緣性,而微影製程對於鹼性物質(如 : NH3)造成的瑕疵是為敏感的,鹼性物質與光阻劑發生酸鹼中和反應造成瑕疵(T-topping)[4],另外還會影響線寬的改變導致尺寸的誤差。
在高科技產業中,以半導體產業產生之污染問題最為嚴重,其次為光電產業。而半導體製程中以黃光製程、封裝製程為主要揮發性有機污染物來源。其揮發性有機物廢氣的來源除製程使用的光阻劑、去光阻劑、顯影劑外,主要為清洗過程使用的異丙醇、丙酮、乙酸丁脂、甲苯、二甲苯、含氯有機物等。半導體製造業,指從事積體電路晶圓製造、晶圓封裝、磊晶、光罩製造、導線架製造等作業者。半導體製程是由原料晶圓片,經由不斷的重覆光學顯影(黃光製程)、蝕刻、薄膜沉積等步驟,最後經由封裝製造而成。蝕刻便是用化學方式(強酸、電漿或強氧化劑)將晶圓上的某一部份物質去除[5],下 圖1為半導體晶圓相關製造與廢氣產生源示意圖。
圖1、半導體晶圓相關製造與廢氣產生源
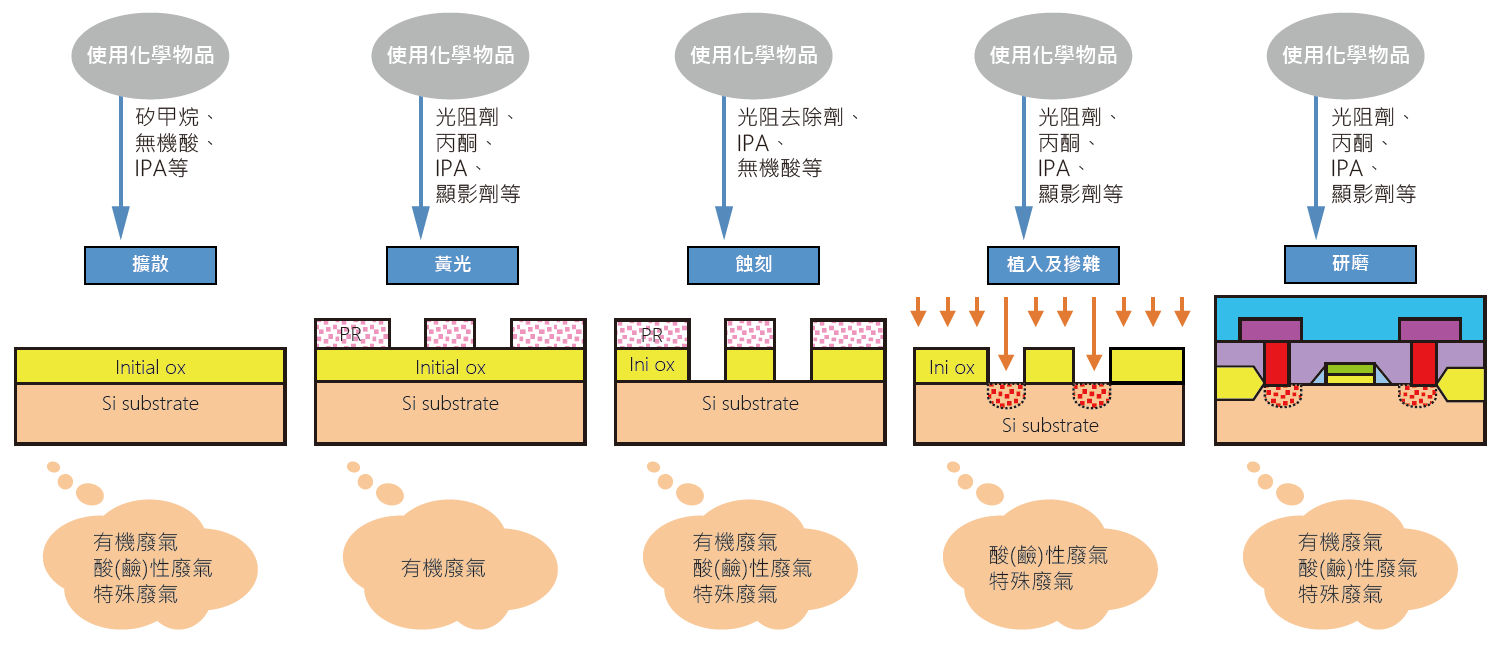
研究方法
文獻中提到有機氣體會造成氧化層崩潰電壓,而廠內有機氣體洩漏事件中光IPA洩漏事件佔了將近34%,增加了約40%的濾網花費,因此減少廠區晶圓被有機氣體污染的機會點以改善IPA的洩漏是最有效的方式。
目標為改善減少廠內重點區域或重點機台的污染,透過分析手法及量測手法將污染源找出並改善源頭。本文第四章提出兩個改善項目供給讀者參考,主要為重點區域的異丙醇濃度高,導致重點機台暴露在被污染的風險之中,輕者停機暫停生產;重者可能影響產品良率,造成晶圓產生電性相關的缺陷。
本文主要以內部作業之污染作為研究探討,從空白晶圓到出貨之間有數百到製程,所以必須要釐清哪一道製程才是真正產生問題的元兇,進而縮小實驗範圍,然後再以各種實驗分析污染的來源,在確定問題製程範圍後,下一步便是尋找污染路徑,此步驟在於澄清在問題製程中的製程機台是否受到污染或是問題來自機台本身,本文透過廠務量測設備及實驗室量測設備分析各種AMC氣體濃度,量測AMC使用儀器表如 表2及各儀器或設備外觀如 圖2。
類別 |
系統別 |
儀器 |
量測物質 |
量測頻率 |
單位 |
resolution |
|
---|---|---|---|---|---|---|---|
FAC |
Online |
IMS-NH3 |
NH3 |
8小時 |
ppb |
1.5 ppb |
|
Online |
IMS-HCL |
HCL |
8小時 |
ppb |
0.5 ppb |
||
Online |
API-TS |
TS |
8小時 |
ppb |
0.4 ppb |
||
Online |
GC-FID |
TOC |
8小時 |
ug/m3 |
1 ug/m3 |
||
Offline |
Picarro |
CXF |
Real time |
ppb |
0.03 ppb |
||
Offline |
API-TS |
TS |
Real time |
ppb |
0.4 ppb |
||
Offline |
API-NH3 |
NH3 |
Real time |
ppb |
0.4 ppb |
||
Offline |
PID |
TOC |
Real time |
ppb |
1 ppb |
||
Offline |
MiTAP |
TOC |
Real time |
ug/m3 |
0.1 ug/m3 |
||
類別 |
系統別 |
採樣設備 |
分析儀器 |
量測物質 |
量測頻率 |
單位 |
resolution |
CHAD |
Online |
NA |
ATD-GCMS |
TOC |
12小時 |
ug/m3 |
0.1 ug/m3 |
Offline |
IC impinger |
IC |
陰陽離子 |
ENV : two weeks / Tool : weekly |
ppbv |
0.024 ppb |
|
Offline |
Canister |
GCMS |
TOC |
ENV : two weeks / Tool : weekly |
ug/m3 |
0.1 ug/m3 |
|
Offline |
8"晶圓片 |
ICP-MS |
硼/磷 |
一週兩次 |
E11 atom/cm2 |
10 E11 atom/cm2 |
圖2、AMC儀器及設備外觀圖
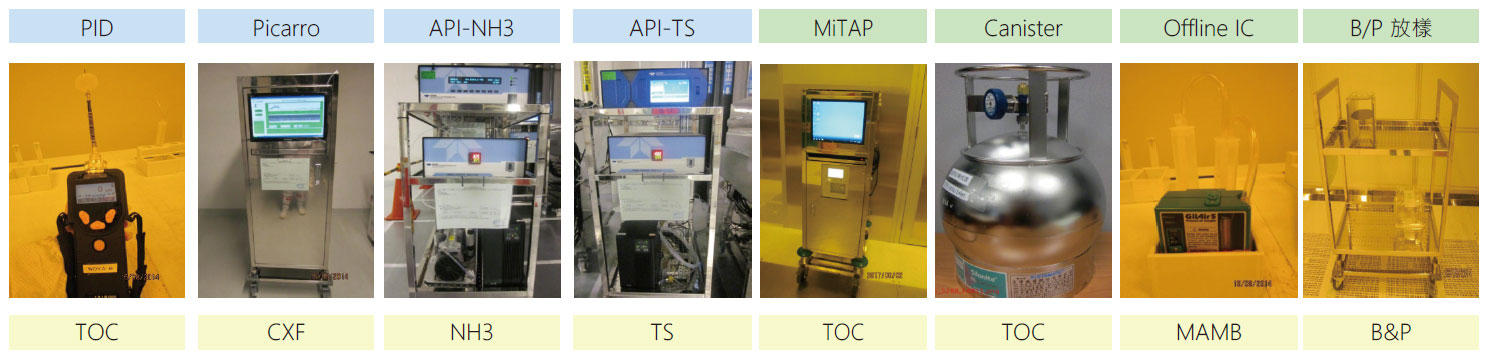
本文主要針對IPA進行分析,而IPA屬於有機物,廠內主要離線偵測有機物質之儀器有三種(廠務兩種,實驗室一種):
- 氣相色譜質譜(GC-MS),GC(Gas chromatography,氣相色譜法)是使用溫度控制的毛細管柱,將混合物分離成單獨的成分。低沸點的小分子會比高沸點的大分子更快地通過管柱。MS(Mass spectrometry,質譜法)用來辨別質譜中不同的成分,在廠內可使用採集桶(Canister)採集氣體再將氣體打入儀器內進行分析。
- PID手持式量測儀器,PID光離子原理由於PID反應快速 ,可根據外氣TOC的不同游離電位(Ionization Potential, IP)選用不同材質的燈泡,台積無塵室因大多數設備保養機台時使用IPA所以廠內皆選用氧化鎂燈泡,因偵測極限為ppb所以主要用來快速找尋漏源。
- MiTap VOC(揮發性有機物)微型氣相分析儀,此台儀器偵測極限與實驗室之GC-MS相似,但使用之儀器不同,因此讀值也不盡相同,所以與廠內實驗室合作,透過定性且定量分析,以不同濃度(低、中、高)檢測廠商量測儀器,比對與台積電合格儀器之減量線差異性,再利用環境量測修正減量線,最後調整減量線(校正曲線)使儀器更符合在廠內應用,如 圖3。
圖3、減量線調整方式
現場氣體採樣方式建議可彈性採樣,垂直方向低、中及高或水平方向東、西、南及北,在正常情況之下可量測水平走道上,如 圖4,若發現異常則可對該點機台進行三維的多點量測,針對機台上、下、前、後、左、右進行量測,依經驗可優先從左、右、甚至機台下方進行地毯式量測,可利用此方式找尋漏源,也可透過此方式確認可能洩漏的方向,進而找到異常機台。
圖4、採樣管偵測方式
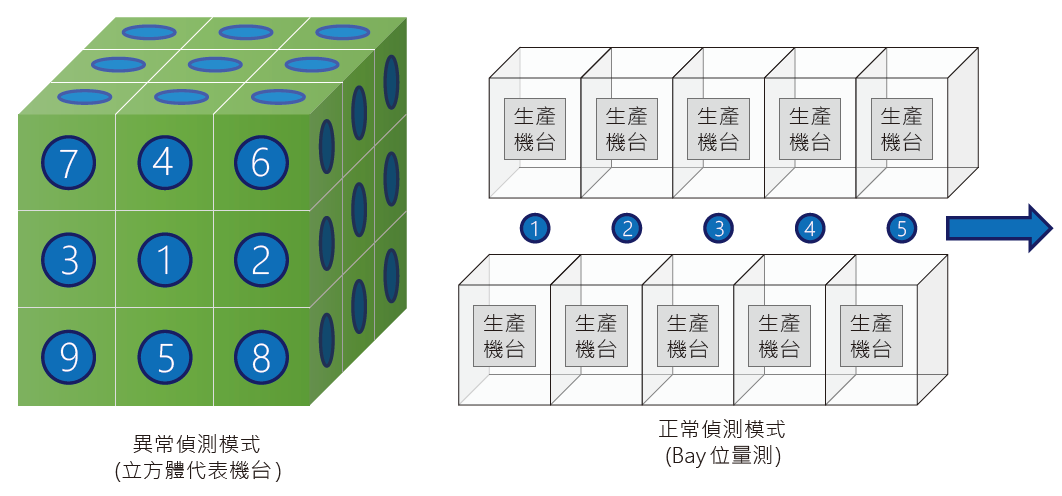
結果與分析
廠內控管AMC的方式有三種 : ①透過有機溶劑作業單進行稽核巡檢,②利用小瓶酸系統調查每日保養機台使用化學物品,③不定期的自主巡檢稽核,每週透過報表分析有機溶劑使用狀況、各單位PM狀況及自主巡檢結果,如 圖5,才能有效控管廠內AMC正常,使廠內穩定運轉。以下兩個改善案例由GC-MS量測讀值異常再分析異常區域各機台特性,配合不定期的自主巡檢稽核及作業觀察,才能找到機台的異常點,並設定短、中、長期的解決方式進行機台改善,解決廠內IPA洩漏問題,最後透過廠內各種量測氣體儀器紀錄讀值變化、IPA的即時濃度趨勢是否有明顯下降及濾網更換頻率是否變長才能驗證改善方向是否正確。
圖5、AMC巡檢統計圖

4.1.案例一 : 前段機台逸散IPA改善
此案例經由日常巡檢(offline)及線上即時分析(online)發現該區有IPA外洩問題,該採樣點設置於機台旁作為該區環境點,但經由作業觀察確認該設備並無使用IPA進行保養或生產,最後透由上述所分析的使用IPA機型中,發現該區域有5台機台有使用IPA,展開作業觀察後發現該機型並無隨時使用IPA,所以較難及時發現是否有IPA洩漏,使用TOC量測儀器PID(RAE3000)觀察發現當機台進行某特殊製程過程中會使用IPA,利用量測九宮格方式找尋漏點,共發現三處有IPA洩漏狀況 : ①機台踏板下方,②機台下方(高架地板下),③機台桶槽存放處的外殼都量到濃度極高的IPA,經由密集討論,短解處理方式為暫時用保鮮膜密封加上使用CV助抽,整個改善計畫分成三階段,第一階段為增加VEX管路助抽;第二階段加強機台氣密性;第三階段使用新開發之IPA濾網安裝在此區域。
此案例改善結果成效顯著,如 表3所示,濾網花費約節省74%/年,而該區氣體濃度異常警報總次數由51次降為1次,IPA濃度減少84%,各個階段IPA濃度值的趨勢圖(inline GC-MS),如 圖6,可看出IPA濃度逐漸降低,並穩定不觸發警報,大量減少系統運轉風險。
Item | OOS/C | OOW | Filter cost(年) | PID量測 | MiTap量測 | 燈號 |
---|---|---|---|---|---|---|
爆發期 | 16 | 0 | - | 100% | 100% |
🌑 |
短解時期(CV) | 11 | 18 | 100%/Y | 81.50% | 82% |
🌑 |
第一階段(VEX) | 3 | 2 | 53%/Y | 18.10% | 40% |
🌑 |
第二階段(氣密) | 0 | 1 | 42%/Y | 2.60% | 24% |
🌑 |
第三階段(Filter) | 0 | 1 | 17%/Y | 1.30% | 16% |
🌑 |
共減少 | 100% | 95.20% | 83.00% | 98.70% | 84% |
👍 |
圖6、各階段IPA濃度狀況
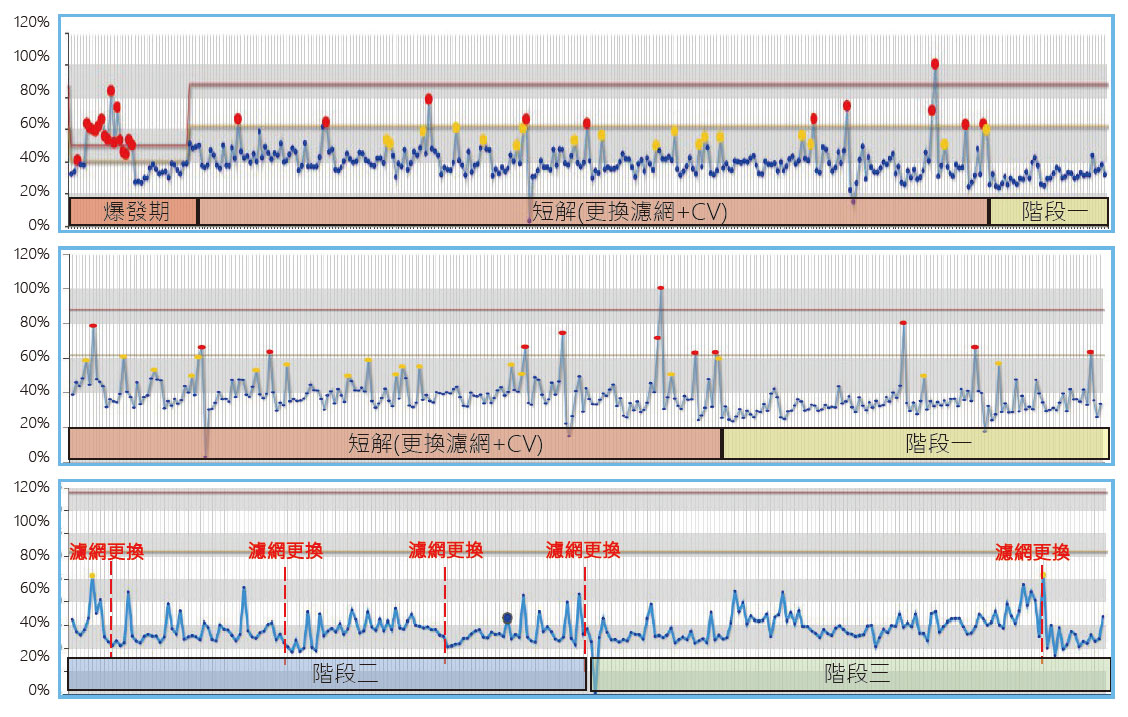
4.2.案例二 : 後段機台逸散IPA改善
此案例多廠皆有發生過此問題,主要源自於後段區域的機台進行IPA製程時會從機殼側邊及底部溢散出大量的IPA。因該洩漏區域臨近高敏感區域,而可能會造成敏感區域的製程產生電性上的缺陷,所以初期除了將洩漏機台簡單的包覆外,也需要花費大量的濾網費用在維護敏感區域區,案例二與案例一不相同之處為,案例二的IPA運作的時間較長,因此更容易影響到其他區域的IPA濃度,其改善的方案,如 圖7,將底部加裝VEX抽氣讓機台內形成負壓並把有機氣體抽離,最後再將側機殼部分加以密封強化氣密,減少溢散風險。
圖7、後段機台側視圖及改善方案
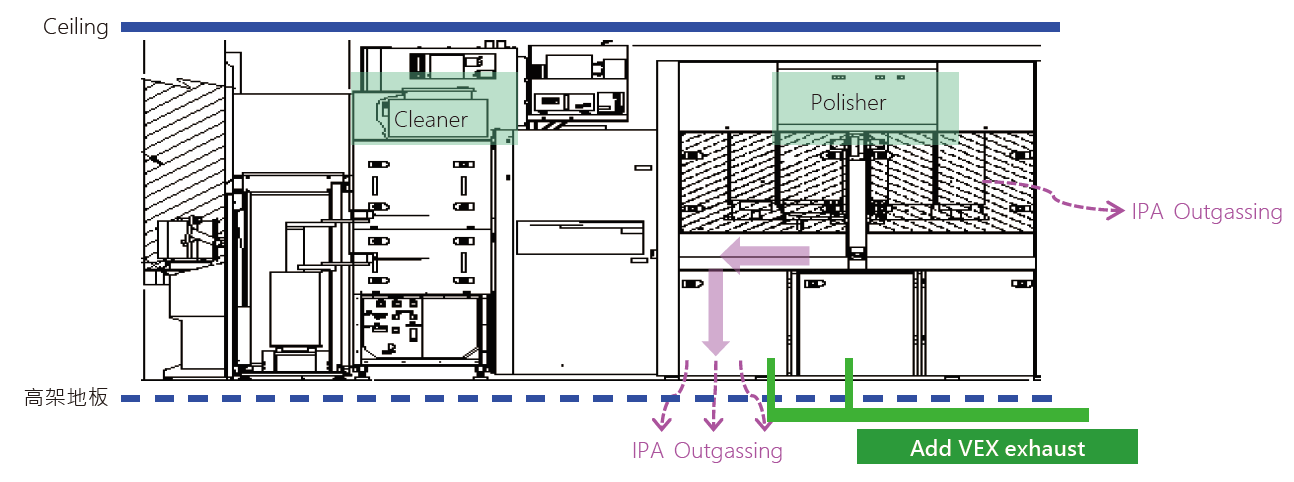
改善分為三個階段,如 圖8,第一階段為加裝氣密條與增加PVC垂簾;第二階段為機台下方增加抽氣管路;第三階段為機台側邊加裝VEX管路。使用PID氣體偵測器量側改善前後的狀況,IPA讀值經由改善後下降100%。
圖8、後段機台各改善階段PID量測結果圖
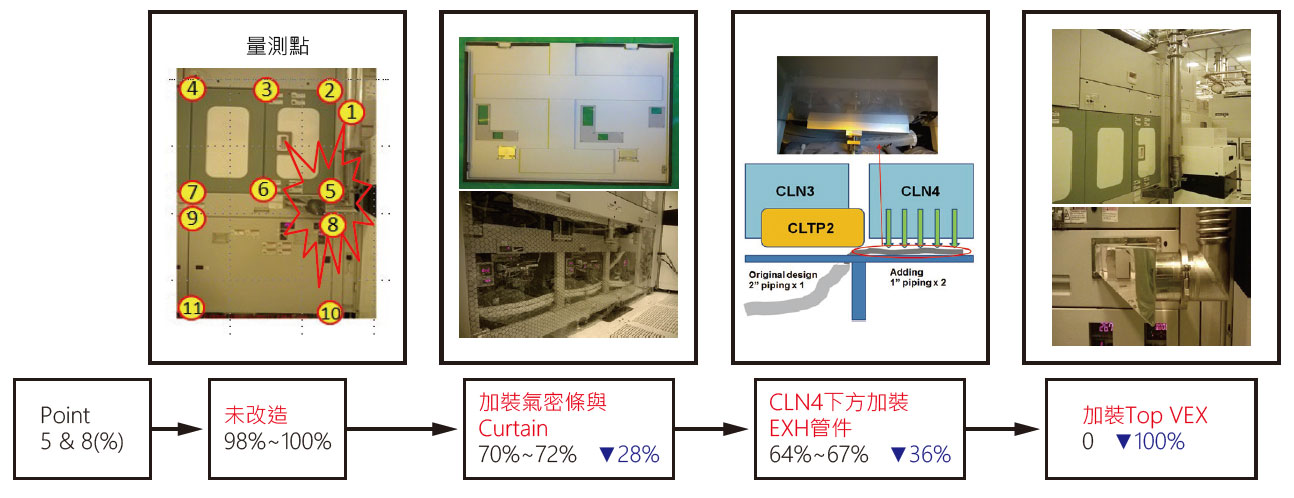
因洩漏IPA區域有鄰近的兩個區域受到影響而成IPA讀值偏高,將這三區的Inline GC-MS的趨勢圖合併分析效益,如 圖9 圖10,改善完後的效益為IPA減少70%以上,區域一改善後濾網年減23%;區域二改善後濾網年減39%,兩區總和每年共減少32%的濾網花費,如 表4所示。
圖9、後段改善前各區域IPA Trend Chart
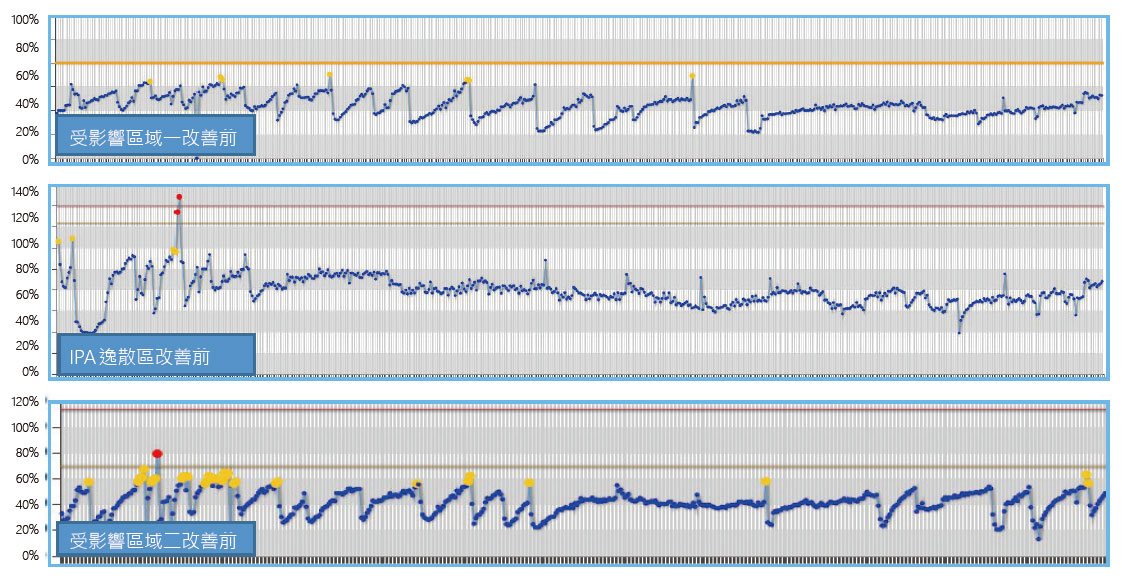
圖10、後段改善後各區域IPA Trend Chart
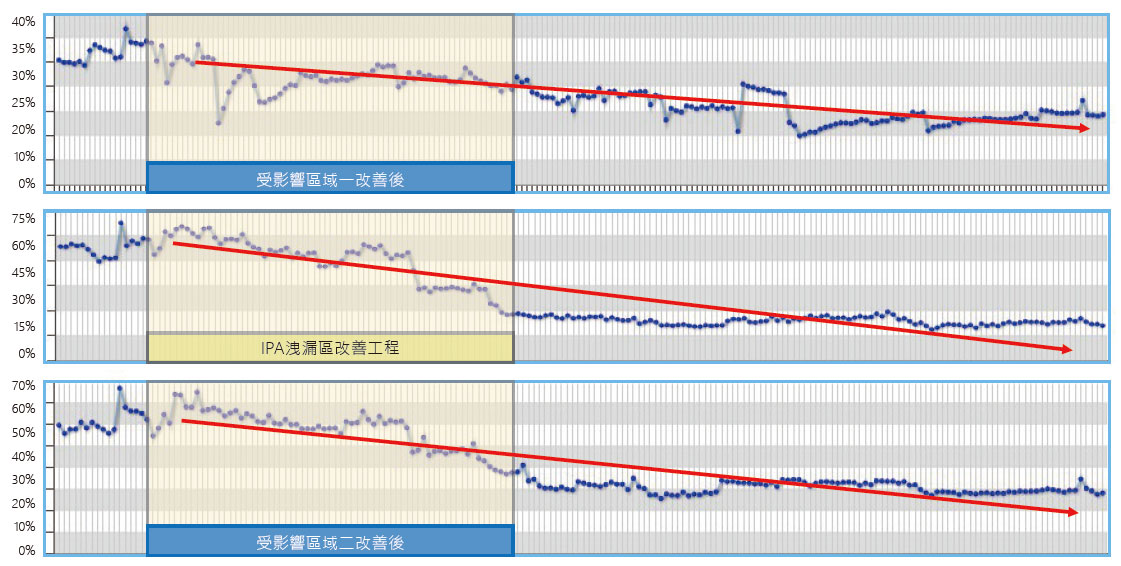
Area | 改善前 | 改善後 | ||||||
---|---|---|---|---|---|---|---|---|
OOS/C | OOW | Filter cost(年) | IPA Baseline | OOS/C | OOW | Filter cost(年) | IPA Baseline | |
IPA逸散區域 | 2 | 3 | - | 100% | 0 | 0 | - | 30% |
受影響區域一 | 0 | 6 | 100% | 100% | 0 | 0 | 77% | 23% |
受影響區域二 | 1 | 22 | 100% | 100% | 0 | 0 | 61% | 30% |
效益 | ||||||||
Area | Alarm reduce | Filter cost reduce(年) | IPA reduce | ![]() |
||||
% | 減少次數 | |||||||
IPA逸散區域 | 100% | 5 | - | 70% | ||||
受影響區域一 | 100% | 6 | 23% | 77% | ||||
受影響區域二 | 100% | 23 | 39% | 70% | 相對區域圖示 |
結論
影響無塵室內的AMC濃度的原因有許多種且看不到也摸不到,需透過系統化的調查才能有效率的找出問題,面對常發生的污染問題需建立預防SOP才能減少相同或類似的事件再次發生;但面對首次發生的問題需花費大量的人力及時間佈點採樣,因此熟知每個區域會使用的化學品是相當重要的課題,上述兩項案例對於A廠區濾網總花費共減少49%/年,並可藉由此經驗傳承在新廠區有相關製程時可在運轉前進行改善,直接減少濾網花費。
廠內發生AMC污染時需執行的三大步驟 : ①搜尋污染源,②防堵(關閉)污染源,③設備改善(包覆、氣密及抽氣) ,其中80%的時間消耗在搜尋上面,有效減少搜尋時間除了經驗以外還需要藉由可靠的設備,如廠務的AMC量測設備(PID、Mitap、Picarro),因此量測儀器的穩定度及偵測極限是查尋漏源的關鍵。
完整的微污染控制策略需要隨時監控無塵室內AMC的濃度,除了手動量測以外,依據OI規定無塵室內每個獨立區域(迴風區)需設置一個採樣點代表該區的AMC濃度,才能確保環境的穩定與否,且在執行改善專案時才能監測無塵室的AMC濃度變化,並隨時調整改善策略。
AMC來源的分析與防治建議未來發展總結為以下幾個方向:①發展電子化系統(如製成原料、機台、管路),並與化學品流通資料庫結合。②設計適用於無塵室環境AMC巡檢機器人加強巡檢並建立AMC濃度地圖。③發展無塵室氣流模擬系統,減少搜尋時間。④設計廠區時將髒區及高敏感區域分隔,雖然可能造成OHT系統移動時間,但可減少大量的濾網更換費用。
參考文獻
- Muller, A. J., Psota-Kelty, L. A., Krautter, H. W., and Sinclair, J. D., "Volatile Cleanroom Contaminants : Sources and Detection," Solid State Technol., 37(9) : 61-72, 1994.
- Kinhead, D.A, "Forecast of Airborne Molecular Contamination Limits for 0.25 Micron High Performance Logic Process," Technology Transfer Report 95052812A-TR, SEMATECH, May 31, 1995.
- Ogawa Hiroki、Horiike Yasuhiro著,嚴誠廷譯「半導體潔淨技術」普林斯頓國際有限公司,2003。
- D.Ruede, M.Ercken, T. Borgers. The impact of airborne molecular bases on DUV photoresists.Solid State Technolo gy, 2001.
- 林育旨以GC/MS偵測高科技工業區內空氣中揮發性有機物濃度之研究,2010。
留言(0)