摘要
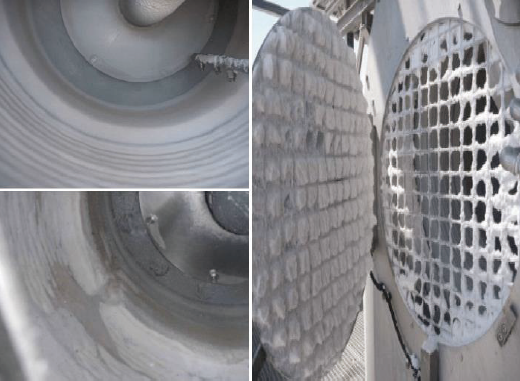
2018年台積引入機械式蒸氣再壓縮技術處理硫酸銨廢液,2021年將此技術由中科導入至竹科與南科。竹科與中南科非同系統商建造,其系統設計有部分不同,故在實務運轉之操作參數亦有差異;F12B藉由控制結晶顆粒大小來穩定推進式脫水機運轉,再將高濃度離子廢液導入廠內氨氮處理系統進行處理,控制系統內部液體濃度、溫度與壓力等各項參數,達到產能提升並實現硫酸銨資源化目標。本文針對最佳化推進式脫水機入料參數、高濃度離子廢液導入氨氮處理系統與其對各系統負影響進行探討,以作為未來硫酸銨結晶系統設計參考。
TSMC applies mechanical vapor recompression technology to treat ammonium sulfate waste in 2018. This technology will be applied to Hsinchu Science Park and Southern Taiwan Science Park in 2021. The two systems are not built by the same system manufacturer. Their system designs are partially different, so the operating parameters in actual operation are also different. F12B dehydrator operates stably by controlling the size of crystal particles, and then introduces high-concentration ion waste liquid into the CWD system for treatment. Control system liquid concentration, temperature and pressure to increase production capacity and realize the utilization of ammonium sulfate resources. This article discusses the optimization of the feed parameters of the pusher dehydrator, the high-concentration ion waste liquid is introduced into the CWD system and its negative impact on each system, as a reference for the design of ammonium sulfate crystallization systems.
1.前言
半導體製程所產生之氨氮廢水藉由脫氣膜與再生硫酸結合產生硫酸銨廢液,再將硫酸銨廢液委外清運處理,此舉雖能減少外排廢水中氨氮含量,但也使硫酸銨廢液躍升為廠區最大宗廢棄物,且其委外處理成本高。因此中科F15A於2018年建置台積首座硫酸銨蒸發結晶系統,將硫酸銨廢液再生活化,並於年底成功產出台積第一批工業級硫酸銨成品委外銷售;而竹科每月約產生2200噸硫酸銨廢液,其亦為竹科廢棄物之冠,年處理費用高達六千萬,因此於2021年將此蒸發結晶技術導入至竹科F12B,冀能完成硫酸銨廢液資源化,落實綠色製造目標。
F12B硫酸銨結晶系統在實務運轉上,數次因結晶高含水率、原母液內雜質量,使推進式脫水機穩定度不佳;系統因長時間蒸發結晶,結晶罐內無法排出的雜質持續堆積,且硫酸銨回流濃縮密度上升,導致蒸發量減少使熱回收量大幅降低,兩者成為產能提升的阻礙。為此針對脫水機入料顆粒大小、含水率、設備運行程序研究探討,經測試穩定的入料顆粒大小,可減少脫水機運轉負荷、提升脫水機轉速則能改善再生產品含水率;母液內雜質量可經由定期排放高濃度廢液來降低,經測試當每日固定排放3噸以上之高濃度廢液,可有效增加處理產能,高濃度離子廢液排放路徑,則修正原廠設計,原為高溫、高濃度廢液定量直接排放至氨氮處理系統,改以低溫、固定濃度少量多餐方式排放,有效利用脫氣膜將硫酸銨廢液中氨氮與離子雜質分離,提升硫酸銨系統處理量,且對氨氮系統影響降至最低。
2.文獻探討
再生廢硫酸與氨氮廢水形成硫酸銨廢液,其中再生廢硫酸含離子雜質,如氯離子(廢硫酸回收系統加鹽酸而來)。因硫酸銨結晶系統為連續式操作,會使這些離子雜質在母液中累積,若母液離子雜質濃度超出臨界值,會影響晶體生長速度、晶體型態。其中推進式脫水機的穩定性,取決於晶體顆粒大小、晶體含水率與母液雜質含量;細小顆粒會穿越濾籃柵網滯留於濾網內,使脫水效果降低,晶體含水率提升;而高含水率晶體會產生阻力,於推進時產生反作用力至設備,加速脫水機設備零件耗損;若未維持脫水機高潔淨度,則易影響後段流化床烘乾程序。因此穩定離子雜質濃度與推進式脫水機運轉,為提升硫酸銨結晶系統產能一大瓶頸。
2.1 高濃度離子廢液影響硫酸銨結晶
Buchfink[1]提到硫酸銨液體在不同濃度鐵離子下,如圖1(本篇以鐵離子為例),對結晶生長速率有強烈影響,對溶解速率影響較小。當鐵離子濃度增加至10ppm時,硫酸銨結晶生長速率降低50%,大於100ppm後生長速率趨近於0。硫酸銨液體溶解度在含有10ppm鐵離子濃度時大幅降低25%,大於10ppm後,對硫酸銨溶解度則較無明顯影響。
圖1:鐵離子對生長速率(左)和溶解速率(右)的影響
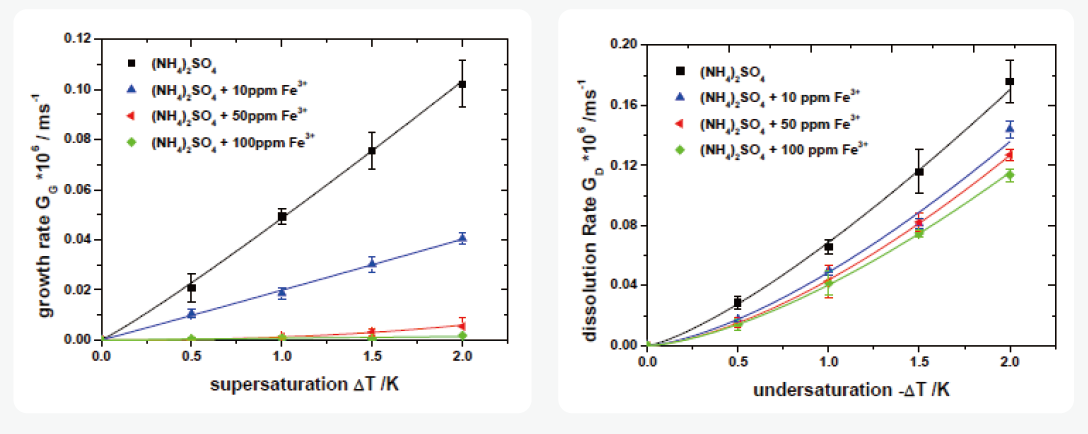
系統蒸發效率與結晶罐內母液雜質含量密不可分,高含量雜質會直接影響內部溫度傳導,而雜質含量提升主要因硫酸銨結晶系統經長時間連續蒸發,使結晶罐內雜質濃度提升(如氯離子、鐵離子等)。由F15A實際運轉所記錄之指標參數,當氯離子濃度大於500ppm、鐵離子大於10ppm時,皆會降低10~15%硫酸銨廢液處理產能(表1)[2]。
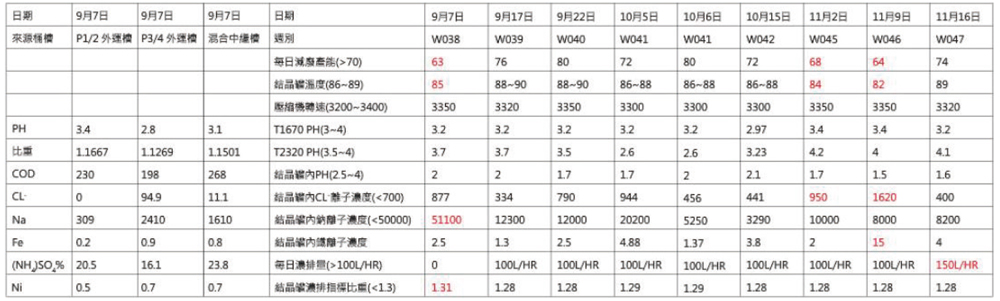
參考實際運轉經驗,藉由調節含高濃度雜質硫酸銨液體排放量,進而降低硫酸銨母液雜質濃度。因此F12B運轉首要針對排放量與雜質濃度進行探討,次要則針對排放高濃度雜質硫酸銨液體內之氨氮提取,以達到硫酸銨結晶系統產能提升之目的。
2.2 推進式脫水機入料設計與控制
推進式離心脫水機主要由雙層濾籃與推進機構組成(圖2),第一層濾籃具預過濾功能可於內部進行增稠,使推進循環的每個過程保持自由入料區[3],確保入料穩定不易破碎與阻塞;第二層濾籃具晶體顆粒主要濾水功能,最後再藉由推進機構將晶體顆粒推至出料口,完成固液分離。因硫酸銨液體極易結晶之特性,濾籃內部會因運轉時間增加,使其緩慢阻塞濾網內層並滯留於濾籃內 [2](圖3),最終晶體含水率會隨時間遞增。晶體高含水率會影響後段流化床烘乾製程,因此定期清洗脫水機為穩定運轉首要,故在內外濾籃皆有設計自清管路(圖4),並使用系統回收熱水進行清潔。
圖2:推進式脫水機雙層離心結構
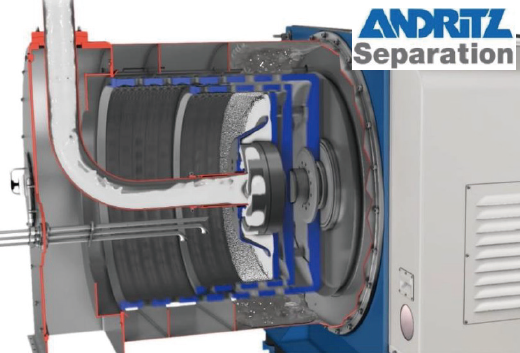
圖3:F15A長時間運轉晶體殘留推進式脫水機濾籃
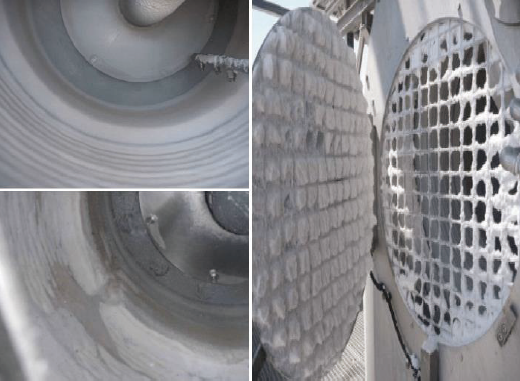
圖4:外濾籃自清潔設計
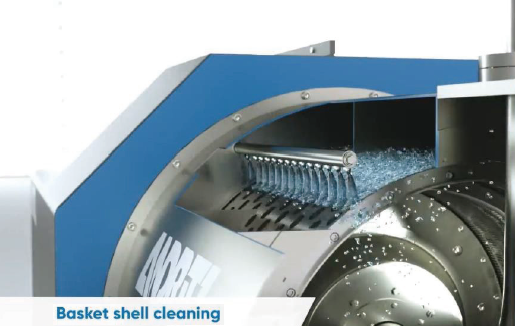
而脫水機脫除與清潔的水份(圖5),其內部皆含有硫酸銨,因此可將其回收至前處理桶槽中,再進入結晶罐內部進行蒸發結晶。綜合參考脫水機設備與系統設計,若要穩定運轉且提升產能,需考量最佳化脫水機入料顆粒大小,以延長脫水機設備穩定運轉時間,增加硫酸銨晶體處理產量;最佳化脫水機運行時間,以利在脫水機設備潔淨度與系統重新蒸發所占處理量之間取得平衡。
圖5:硫酸銨晶體脫水與濾籃清潔
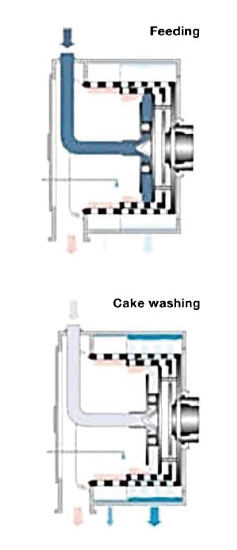
2.3 影響固料脫水效果與離心設備運轉的因素
Xiaolei Dong[4]在進行精煤離心脫水效果提升測試時,提到濾籃篩條間隙與離心機轉速是影響脫水機脫水效果的主因因素;濾籃篩條背寬則是影響離心脫水機濾籃設備耗損速度的主因。當濾籃篩條間隙越大(δ),水流較易通過脫水效果較佳,當濾籃的篩條背寬(B)較大,篩條較不易損耗使濾籃壽命較長(圖6)。濾籃篩條間隙調整測試中,以未改造篩條間隙的濾籃(對造組)與增加10%篩條間隙的濾籃(實驗組)進行比較,使用對造組濾籃離心脫水後的精煤,測定固料含水率穩定於11-12%;使用實驗組濾籃離心脫水後的精煤,測定固料含水率穩定於8.8%,結果顯示較高的篩條間隙,因水流較易通過,使固料產品有較好的脫水率(圖7)。
圖6:濾籃與篩條結構示意
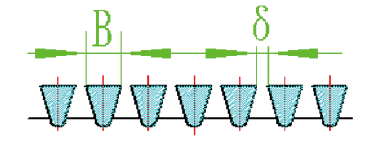
圖7:濾籃不同篩條間隙與含水率比較
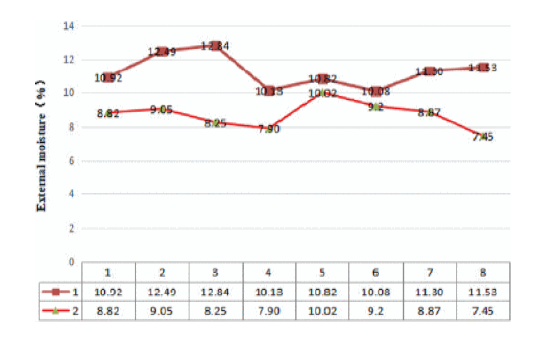
在離心脫水機轉速調整測試中,不同精煤廠進行轉速提升,皆觀察到固料產品含水率明顯下降(圖8)。各精煤廠將離心脫水機轉速由570rpm提升30~50rpm,固料產品含水率下降0.5~2.5%。
圖8:離心脫水機轉速與含水率關係
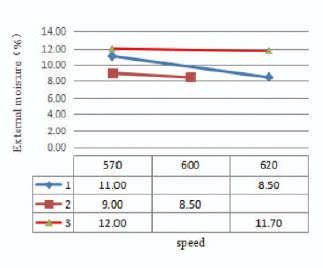
此外,文獻提及固體物料需保持均勻進料,若進料不均勻或間歇性入料易導致產品含水率波動且造成離心脫水機震動;固體物料還需保持粗顆粒入料(文獻以80目區分;0.18mm),最高以不超過15%細顆粒入料,可大幅控制固料產品含水率與離心脫水機震動。由文獻可知,保持良好的水流通道、控制顆粒粒度與提升離心脫水機轉速對含水率與設備穩定有正相關的影響。F12B在離心脫水機選型已固定篩條間隙(35目;0.5mm)的情況下,可利用控制離心脫水機轉速與顆粒粒度達到良好的水流通道,以穩定固料產品含水率與離心脫水機運轉。
3.實驗方法
3.1 硫酸銨蒸發結晶系統架構
半導體製程所排放含氨氮廢液,可利用脫氣膜與再生硫酸進行吸附結合,製成約30%液態硫酸銨,再將其導入系統進行結晶固化處理。硫酸銨結晶系統由板式熱交換器作為初始啟動加熱設備,達運作溫度後轉以串級蒸氣壓縮機將蒸氣加壓升溫作為系統主熱源供應,再利用殼管式強制加熱器傳遞熱能予結晶罐內硫酸銨母液,達成熱循環使用。當系統連續蒸發會使結晶罐母液濃度上升,直至溶液達40%~50%過飽和濃度後,結晶罐內部開始析出晶體顆粒,較小的晶體顆粒利用內循環泵浦抽取結晶罐上層溶液打入分級角,將較小的晶體顆粒揚起回結晶罐內增大;而較大的晶體顆粒則沉澱至結晶罐分級角,以出料泵抽取含晶體顆粒溶液,輸送至中段離心脫水機進行固液分離,其再進入後段乾燥製程去除殘餘水份,最終以真空輸送設備傳送至包裝系統打包,此為硫酸銨結晶系統結晶固化全流程(圖9)。
圖9:F12B 硫酸銨結晶系統流程圖
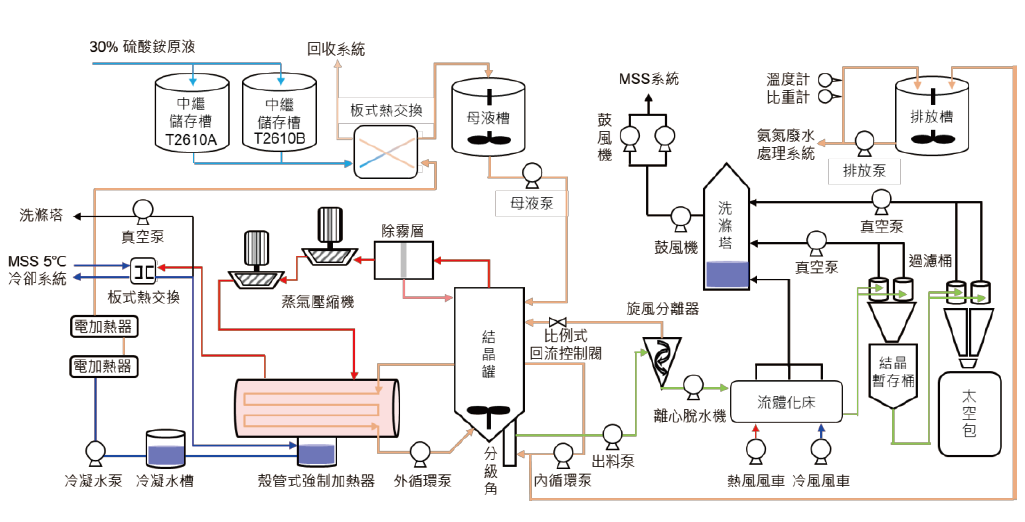
3.2 高濃度離子排放與處理產能測試
硫酸銨廢液其中本含有大量的離子,而再生硫酸是由鹽酸法去除雙氧水,往往再生硫酸產品中會伴隨著氯離子殘留。如文獻與F15A實際運轉所提,當硫酸銨蒸發結晶系統連續運行,因內部殘留離子雜質(氯、鐵、鈉等)無法依靠結晶沉降往後端製程排出,長時間於結晶罐內部堆積直接影響蒸發效能與晶體生成,若蒸發效能降低則會直接影響系統產能。F12B結晶系統設計由內循環泵排放含高濃度離子雜質之硫酸銨母液,排放設計量為每小時200L,將其排放至氨氮處理系統。初期試車運轉,因高濃度離子雜質之硫酸銨母液內含40%~50%氨氮,會瞬時影響氨氮處理系統產水,影響放流水氨氮值;另外,含高濃度離子雜質之硫酸銨母液其pH值約為5~7、溫度約達75~80℃,將增加液鹼使用量,且高溫硫酸銨母液對氨氮處理系統脫氣膜可能造成不可逆傷害(圖10)。鑑於上述負面因素考量,進行排放路徑修改(圖11、圖12),先將含高濃度離子雜質之硫酸銨母液加水稀釋,同時監測其濃度與溫度,當監測指標到達後再排入桶槽暫存,最終以少量多餐形式,排入相對應廢水系統進行處理。本實驗將含高濃度雜質之硫酸銨母液依修改後排放路徑進行排放測試,實驗結果主要探討:①遞增高濃度雜質排放量,直至達原設計排放量,監測結晶罐內部離子雜質濃度、硫酸銨廢液處理產能,探討控制離子雜質濃度與處理產能之間的關係;② 監測高濃度離子雜質排放對於各廢水處理系統的負面影響,做為未來系統設計評估。
圖10:脫氣膜最大操作溫度與壓力

圖11:高濃度廢液原始排放路徑
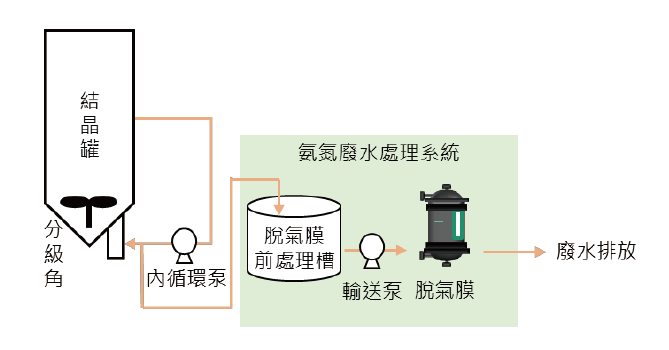
圖12:高濃度廢液修正排放路徑
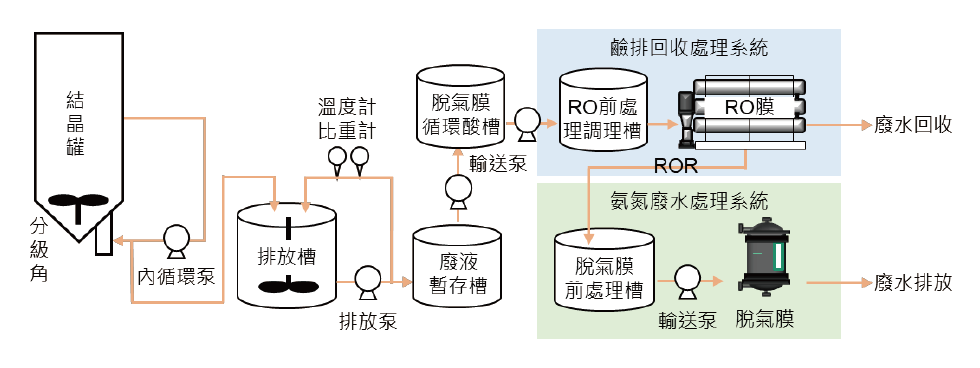
3.3 結晶顆粒控制與推進式離心脫水機穩定測試
推進式離心脫水機能長時間穩定運轉,為維持產能重要條件之一。其主要由離心馬達帶動濾籃藉由離心力進行固料脫水,再由往復馬達帶動推進機構將固料推進。當設備運轉異常時,馬達運轉電流與設備震動值會提升,因此本測試以此作為監控項目。F15A實際運轉經驗,濾網內層因運轉時間增加而滯留結晶,導致運轉後期結晶含水率提升,含水率提升亦會增加馬達運轉負荷,使運轉電流與震動值提升。大顆粒結晶可保有良好的脫水通道,可降低設備負荷進而減緩運轉電流提升;增加推進式離心脫水機轉速可降低結晶含水率進而降低設備負荷。本實驗設計藉由控制內循環泵浦與推進式脫水機轉速進行運轉測試,實驗結果主要探討:①內循環泵浦流量與結晶顆粒性質關係;②推進式離心脫水機轉速與結晶含水率關係;③結晶顆粒特性與馬達電流、設備震動值關係。
4.結果與分析
4.1 高濃度離子穩定排放測試結果
由於硫酸銨結晶系統連續運轉,無法帶出的離子會於結晶罐內持續濃縮,若無法將雜質排出,會影響硫酸銨廢液蒸發與結晶生長。由實際運轉測試結果觀察(表2),在相同運轉參數條件下,可觀察到當結晶罐內含有較高的氯離子濃度,平均每日減廢產能則較低(圖13);當逐漸增加高濃度離子雜質廢液排放時,結晶罐內濃度平均每日減廢產能則逐漸提升,但當高濃度廢液排放量大於3000L時,再提升高濃廢液排放量對於減廢產能提升的效果較不明顯(圖14)。總體測試結果得知,減廢產能與結晶罐離子濃度呈反比,與高濃廢液排放量成正比,因此需要定期檢測結晶罐氯離子濃度,將其控制於400ppm以下;控制高濃廢液排放量大於3000L,兩者達成便可維持良好的減廢產能。
日期 | 6月8日 | 6月15日 | 6月27日 | 7月6日 | 7月13日 | 7月20日 | 8月10日 | 8月17日 | 8月24日 |
---|---|---|---|---|---|---|---|---|---|
周別 | W224 | W225 | W227 | W229 | W230 | W231 | W233 | W234 | W235 |
平均每日減廢產能(噸) | 56 | 61 | 82 | 81 | 78 | 76 | 85 | 92 | 90 |
結晶罐Cl−濃度(ppm) | 1232 | 912 | 652 | 476 | 532 | 442 | 383 | 202 | 198 |
平均每日高濃廢液排放量(L) | 500 | 500 | 2500 | 2500 | 2500 | 3000 | 3000 | 4000 | 5000 |
圖13:結晶罐Cl-濃度與每日減廢產能
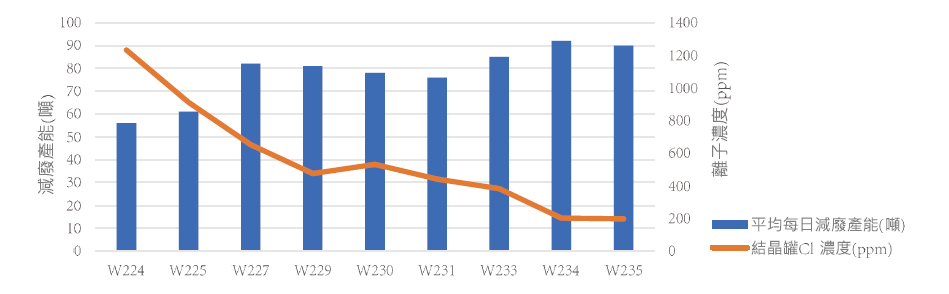
圖14:高濃廢液排放量與每日減廢產能
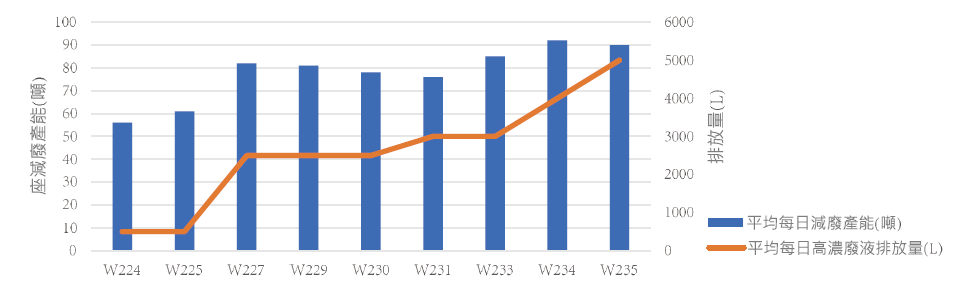
4.2 相關廢水處理系統測試結果
高濃度廢液依修改後排放路徑排放,流程為先將含高濃度離子雜質之硫酸銨母液加水稀釋後排入廢液暫存槽,再以少量多餐模式排入脫氣膜酸循環槽,脫氣膜酸循環槽為鹼排回收系統RO前處理調理槽調整pH值使用,後由RO濃縮廢液排至氨氮廢水處理系統,最終利用脫氣膜進行氨氮處理後排放。
由高濃度排放實驗觀察,因高濃度廢液稀釋後仍含有25~30%硫酸銨,其氨氮值高達200,000ppm,少量多餐排放過程中, RO前處理調理槽與脫氣膜前處理槽,桶槽氨氮值皆有上升(表3)。觀察氨氮廢水系統產水出口氨氮值於高濃廢液排放量2,500L時上升約10~11ppm(圖15),經計算對於放流水氨氮值增加約0.6ppm。觀察鹼排回收處理系統,RO產水導電度亦受到影響,於高濃廢液排放量 2,500L時上升約20us/cm(圖16)。
日期 | 5月24日 | 5月25日 | 5月26日 | 6月27日 | 6月28日 | 6月29日 |
---|---|---|---|---|---|---|
RO前處理調理槽氨氮值(ppm) | 435 | 519 | 404 | 625 | 677 | 634 |
脫氣膜前處理槽氨氮值(ppm) | 3120 | 3530 | 3270 | 4170 | 4860 | 4530 |
平均每日高濃廢液排放量(L) | 0 | 0 | 0 | 2500 | 2500 | 2500 |
圖15:氨氮廢水處理系統產水氨氮值
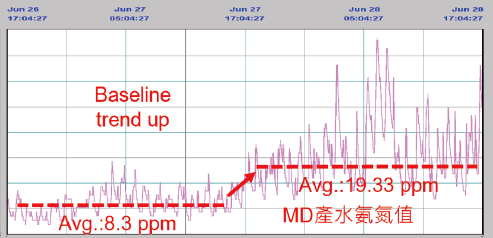
圖16:鹼排回收處理系統RO產水導電度值
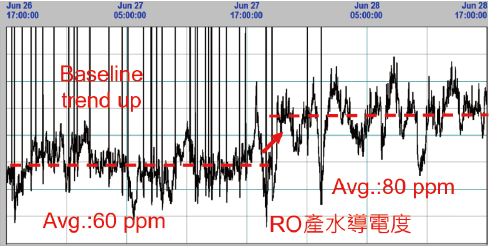
4.3 結晶顆粒分析與脫水機穩定測試結果
4.3.1 內循環泵浦流量與結晶特性
藉由調整內循環泵浦流量,將細小結晶顆粒揚起回結晶罐循環養晶,待形成大結晶顆粒後進行脫水取樣,最後再利用秤重進行粒徑分析觀察兩者關係。由實驗測定數據可以觀察到(表4),各內循環泵浦流量所形成的結晶,顆粒大小落於0.5-1.0mm皆占有約50%,差異在於小於0.5mm與大於1.0mm占比不同(圖17)。當內循環流量上升,可觀察到小於0.5mm逐漸減少、大於1.0mm逐漸增加。依照章節2.3所提,穩定運轉須保持良好的水流通道,因此選擇較大結晶顆粒的運轉參數,使結晶顆粒間能保持良好的脫水通道,減少推進式離心脫水機運轉負荷。
量測次數 | 1 | 2 | 3 | 4 | 5 | 6 |
---|---|---|---|---|---|---|
內循環泵浦流量(CMH) | 8.5 | 8.5 | 9.5 | 9.5 | 10.5 | 10.5 |
<0.5mm(%) | 30.3 | 32.8 | 25.4 | 26.8 | 22.0 | 21.2 |
0.5~1.0mm(%) | 51.9 | 48.8 | 52.4 | 50.1 | 48.8 | 53.2 |
>1.0mm(%) | 17.8 | 18.4 | 22.2 | 23.1 | 29.2 | 25.6 |
圖17:結晶粒徑取樣分析。由左至右>1.0mm;0.5-0.1mm;<0.5mm
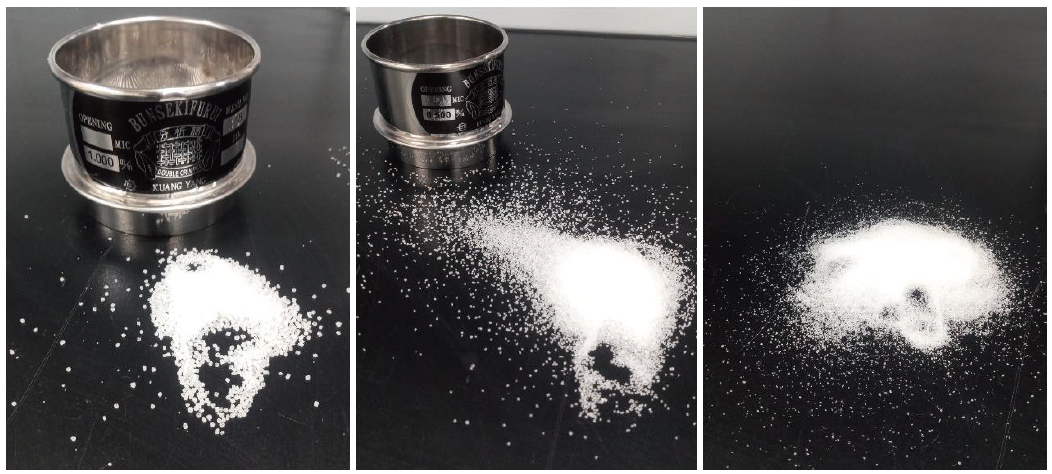
4.3.2 推進式離心脫水機轉速與結晶含水率
系統在相同運轉參數下(脫水機入料流量:6.3 CMH、內循環泵浦:10.5CMH、蒸氣壓縮機:10000rpm),進行推進式離心脫水機轉速調整,分別測試1351、1363、1375rpm,結晶產品含水率。測試結果顯示,當轉速提升12rpm,結晶產品平均含水率由3.06%下降至2.49%,降低0.57%;轉速再提升12rpm,結晶產品平均含水率由2.49%下降至2.04%,降低0.45%。由實驗結果顯示(圖18),提升脫水機轉速對產品含水率有正相關影響,因此參考設備設計值後,選擇1375rpm作為推進式離心脫水機運轉參數。
圖18:脫水機轉速與結晶產品含水率
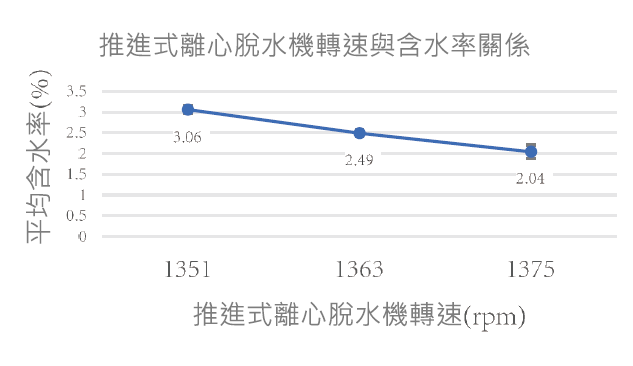
4.3.3 結晶顆粒特性與馬達電流、設備震動值關係
利用章4.3.1分析結果參數,以不同顆粒分布進行入料(固定參數為脫水機入料流量:6.3CMH、推進式離心脫水機運轉轉速:1375rpm),觀察脫水機馬達電流與震動值,找尋脫水機運轉最長時間,換取系統可處理原液時間以提升產能。內循環泵浦流量8.5CMH,測試結果顯示運轉210分鐘後,各項數值爬升速度逐漸增快,於270分鐘便進行推進式離心脫水機清洗(圖19);內循環泵浦流量9.5CMH,測試結果顯示運轉270分鐘後,僅震動值爬升速度逐漸增快,馬達電流則在300分鐘有較明顯爬升,於330分鐘便進行推進式離心脫水機(圖20);內循環泵浦流量10.5CMH,測試結果顯示運轉330分鐘後,各項數值爬升速度逐漸增快,於360分鐘便進行推進式離心脫水機清洗(圖21)。
圖19:脫水機運轉指標與時間(內循環泵浦流量8.5CMH)
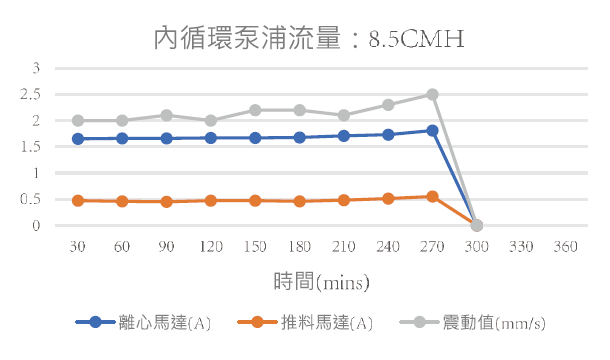
圖20:脫水機運轉指標與時間(內循環泵浦流量9.5CMH)
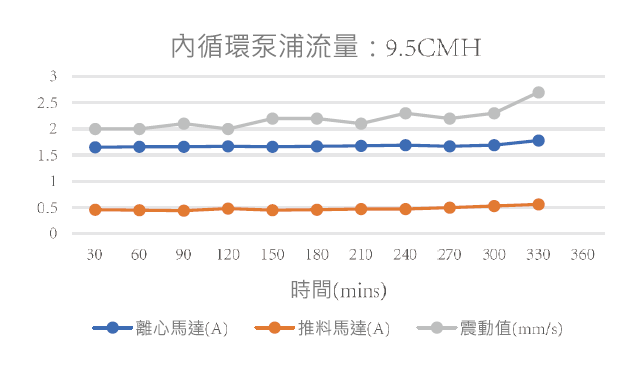
圖21:脫水機運轉指標與時間(內循環泵浦流量10.5CMH)
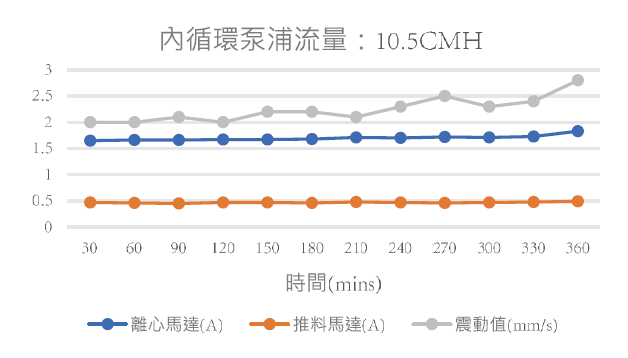
4.4 最佳化系統運轉參數
綜合上述測試得出最佳化結晶系統操作參數,包含每日高濃度廢液排放量、內循環泵浦流量、脫水機運轉速率等,並將各參數改善後的差異彙整如表5,以下操作參數及改善成果,可作為結晶系統運轉之參考。
參數 | 調整方式 | 調整前後差異 | 改善效益 |
---|---|---|---|
平均每日高濃 廢液排放量 | 提高系統每次廢液排放量(L) : 500→4000 L | 每日減廢產能(噸) : 56→90 | 有效提升每日減廢產能(+60.7%) |
內循環泵浦流量 | 調整內循環泵浦流量(CMH) : 8.5→10.5CMH | 小顆粒結晶(<0.5mm) 分布(%) : 30.3→21.2% |
|
脫水機轉速 | 調整脫水機運轉轉速(rpm) : 1351→1375rpm | 降低再生產品硫酸銨結晶 含水率(%) : 3.06→2.04% | 改善再生產品品質 |
5.結論
竹科硫酸銨廢液原為竹科廢棄物之冠,透過硫酸銨結晶系統設置與運轉,已成功讓原需費用清運之廢液轉變為可銷售之產品。透過執行循環經濟,導入循環的商業模式,也成功達成廢棄物減量,並持續朝環境永續發展,善盡社會責任的公司ESG方向邁進。
本研究參考文獻與中科運轉試車經驗,於F12B針對硫酸銨結晶系統影響產能提升之兩項因素:結晶罐離子雜質控制與推進式離心脫水機運轉進行探討。探討結晶罐離子雜質對於結晶系統的影響,並如何處理高濃度廢液排放以達綠色製造;另外探討如何延長推進式離心脫水機運轉時間,降低設備異常與減少停止處理原液的時間。結論如下:
❶實際運轉結果顯示,當高濃度離子廢液每日平均皆穩定排放3000L以上,平均每日減廢產能可處理90噸硫酸銨廢液,檢測結晶罐其氯離子濃度含量皆小於400ppm,可作為未來系統運轉控制指標之一。高濃度雜質離子排放去除,其對於硫酸銨結晶系統提升產能有正向關係,但當排放量達系統需求量後,產能提升效果便較不明顯;且此對其他相關廢水處理系統,仍有些許負面影響。因此可不需一昧追求高濃度離子排放量,當達系統產能提升所需排放量且可穩定高產能處理廢液時,便將目標轉為降低影響其他廢水處理系統副作用。
❷推進式離心脫水機若要長時間穩定運轉,依實驗測試結果歸納參數調整方向:控制結晶顆粒於粗顆粒分布(粒徑小於0.5mm含量需低於25%),以保持良好的脫水通道;提升推進式離心脫水機運轉轉速,以降低結晶產品含水率。當推進式離心脫水機可延長處理硫酸銨結晶固料時間,便是將其轉換為處理原液之產能,達到處理產能提升效果。
其他建議:①減少硫酸氯離子;②高濃硫酸銨廢液不排入氨氮處理系統:
❶由於氯離子進入結晶系統後,依經驗僅能由排液動作進行移除,目前廢硫酸系統使用鹽酸作再生,故再生後之硫酸含有氯離子,如改善處理流程或應用其他新處理方式(例如硝酸法),直接於源頭減少氯離子殘留,則更可減輕對系統之影響。
❷竹科結晶系統濃液依修改後路徑排放,雖採用少量多餐的方式進入氨氮處理系統,但仍會對系統處理單元(如RO膜)、處理後水質等有負面影響,故如能改由其他方式移除高濃度廢液,亦能降低廠內氨氮處理系統運營成本(減少換膜頻率、降低液鹼使用量等)。
參考文獻
- BUCHFINK, Herrn Dipl-Ing Robert. Effects of impurities on an industrial crystallization process of ammonium sulfate.
- 曾俞勳、田鎰菁,硫酸銨乾燥系統運轉實務與維護保養,廠務季刊,40卷,頁38~44,2020。
- https://www.andritz.com/products-en/group/separation/filter-centrifuges/krauss-maffei-sz-pusher-centrifuge
- Dong, Xiaolei. "Analysis of Factors Affecting the Dehydration Effect of Centrifugal Dehydrator." 2020 7th International Forum on Electrical Engineering and Automation (IFEEA). IEEE, 2020.
留言(0)