摘要
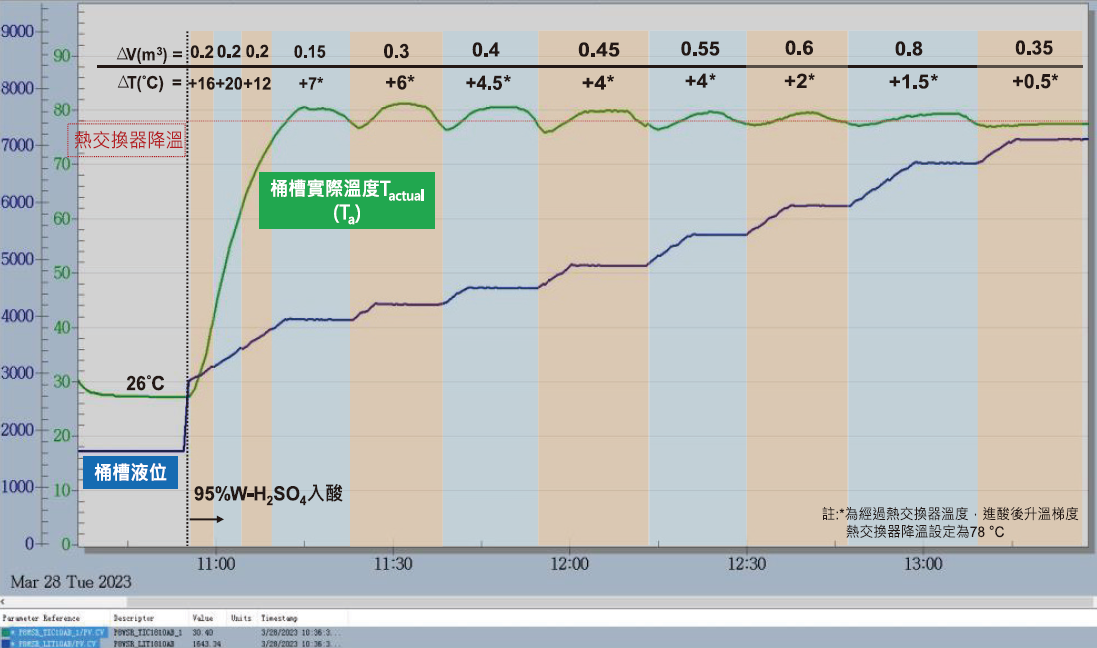
高濃廢硫酸再利用創新改良-廢硫酸稀釋法實務應用
Keywords / Sulfuric Acid7,Hydrogen Peroxide7,Hydraulic Acid,Catalyst2,Chloride2,Exothermic Reaction
廢硫酸回收系統(Waste Sulfuric acid recycling system)有其運轉規範要求,針對新建廠初期即面臨廢硫酸濃度過高、雙氧水(Hydrogen peroxide)濃度過低之狀況,若採用現況操作方式_鹽酸(Hydrochloric Acid)催化(Catalyst)法,為提高反應溫度添加過量鹽酸,不僅反應過程時間長且硫酸產品氯離子(Chloride)濃度高,甚至衍生操作安全疑慮,耗時又耗能。本研究藉硫酸稀釋放熱(Exothermic reaction)特性,提供後續雙氧水與鹽酸反應所需要之熱能,不僅縮短反應時間,大幅降低鹽酸用藥量,提升再利用硫酸品質穩定度,達綠色環保生產目標。
In the early running stage of semi-conductor plant, waste sulfuric acid is usually high concentration and comprises of low concentration of hydrogen peroxide. Since the regeneration process doses large amount of hydrochloric acid into the waste sulfuric acid, the whole reaction is not only time consuming but also under great risk and the product contains high concentration of chloride. Therefore, It is difficult to implement hydrochloric acid catalyzation in the reclamation system.
This study proposes using the exothermic reaction characteristics of diluted sulfuric acid to provide the necessary heat energy for the subsequent reaction between hydrogen peroxide and hydrochloric acid. This approach not only shortens the reaction time but also significantly reduces the amount of hydrochloric acid used. It improves the stability of the recycled sulfuric acid and helps achieve green and environmentally-friendly production goals.
1.前言
半導體晶圓製程中,硫酸主要用於為光阻去除後之矽晶圓清洗,清洗後產生之廢硫酸,但因廢硫酸中具雙氧水成份,如直接使用於廠務處理系統,將導致具薄膜單元處理系統包含硫酸銨之薄膜透氣過濾(Membrane Degasifier)及回收之逆滲透薄膜(Reverse Osmosis Membrane)氧化性反應,使單元造成不可逆之化學結構破壞,因此本公司自民國104年成功導入廢硫酸再生系統,使雙氧水濃度降低至<0.005%,再回歸用於廠內促進資源活化,減少外購工業級硫酸,同時減少委外處理費用,達資源循環。
然而廢硫酸再生系統操作有其運轉規範要求,普遍製程穩定廠區廢硫酸濃度小於70%,但對於新建初始運轉廠或製程污染廠,為符合供酸品質要求,硫酸供給系統上線前或製程開始前需持續進行管路及機台晶圓製程室(Chamber)化學藥劑清洗(Chemical flush),將導致廢硫酸濃度大於70%,甚至近96%原液濃度之廢液,若以現況廢硫酸回收系統操作方式進行,大幅影響系統穩定度及產酸品質,導致高濃度廢酸須委外清運處理,硫酸外購勢必無法避免。此外,品質不佳之硫酸若用於氨氮脫氣膜處理系統,硫酸銨中氯鹽濃度過高,將影響後續硫酸銨結晶回收再利用產能及效率。因此高濃度廢硫酸回收不宜採既有操作方式。
為解決廢硫酸回收系統運轉限制,以增加廢硫酸回收系統操作彈性為目標,導入創新突破操作模式硫酸稀釋法(如圖1),搭配傳統既有鹽酸催化,打破硫酸濃度過高無法再利用之框架,本文將針對硫酸稀釋方式、溫升反應及產酸品質等方向探討,並比較單用傳統鹽酸催化法之操作結果,據以列為廢硫酸回收系統標準操作模式之參考。
圖1:高濃度廢硫酸回收系統操作創新模式比較
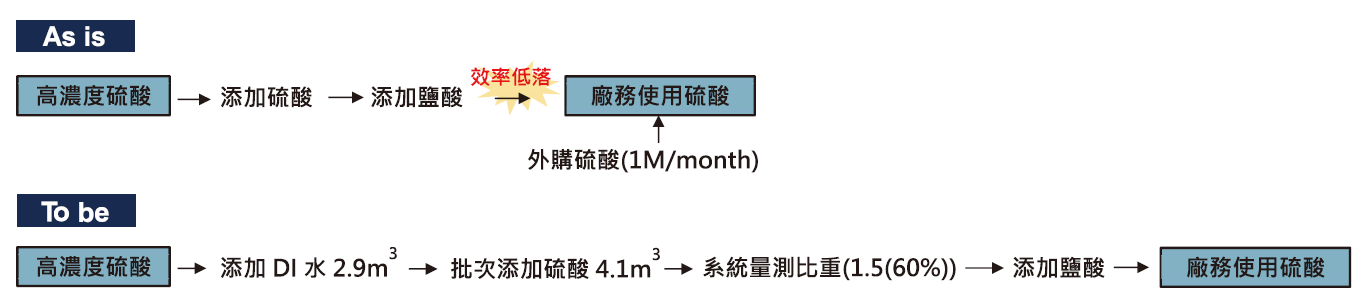
2.文獻探討
為解決廢硫酸回收系統運轉限制,以增加廢硫酸回收系統操作彈性為目標,導入創新突破操作模式硫酸稀釋法,搭配傳統既有鹽酸催化,打破硫酸濃度過高無法再利用之框架,本文將針對高濃度硫酸稀釋手法、溫升反應及鹽酸添加參數等方向探討,並比較單用傳統鹽酸催化法操作,據以列為廢硫酸回收系統標準操作模式之參考。
2.1 廢硫酸來源與探討
目前晶圓清洗技術大致可分為乾式與濕式兩大類,濕式法仍為主流。濕式晶圓清洗目的是以整個批次(batch type)或單一晶圓(single wafer type),藉由化學品的浸泡或噴灑去除晶片表面所有的污染物,如微塵粒(Particle)、有機物(Organic)、無機物、金屬離子(Metal-Ions)等雜質。
廣泛為各製造廠所接受的是RCA標準清洗法(RCA clean)[1],RCA clean包含四種化學混合液APM、HPM、DHF、SPM,成份及清洗目的如表1。
清洗混合液種類 | 成份 | 目的 [02] |
---|---|---|
APM | NH3 H2O2 UPW |
去除微塵粒(Particle) |
DHF | HF UPW |
去移除二氧化矽薄膜層(SiO2) |
HPM | HCl H2O2 UPW |
去除無機殘餘物 (Heavy metals,alkalis, and metal hydroxides) |
SPM | H2SO4 H2O2 UPW |
去除有機物(Organic impurity) |
其中SPM用於光阻去除後之矽晶圓清洗,依照製程需求,硫酸(H2SO4)添加過氧化氫(H2O2)以不同調配比例配置後(Piranha solution)清洗矽晶圓表面上之有機物,使有機物氧化分解,因此產生廢硫酸。機台排放廢硫酸濃度約50%~70%左右,過氧化氫濃度約3%~7%左右。
2.2 廢硫酸反應溫升探討
2.2.1 鹽酸溫升機制
在半導體製程中,過氧化氫普遍用於晶圓清洗製程程序中,清洗後產生之廢硫酸憑藉添加鹽酸作為催化劑與過氧化氫反應。
H2O2 + HCl → H2O + HOCl
HOCl + HCl ↔ H2O + Cl2
HOCl + H2O2 → H2O + HCl + O2
H2O2 + Cl2 → 2HCl + O2
根據上述化學反應式,反應過程中產生之氯氣會再與硫酸中之過氧化氫持續反應,反應過程因雙氧水分解產生放熱反應。過氧化氫反應劇烈主要原因為含過氧酸官能基(Peroxy function group),被視為極不穩定且具活性,尤其溫度改變影響更為顯著。
劇烈反應(Runaway reaction)通常可依一觸即發反應與否(tempered or non-tempered system)作為分類[3][4],非一觸即發反應系統(non-tempered)定義係反應熱可藉由汽化潛熱(Latent heat of vaporization)相互抵消,因此反應環境具高蒸氣壓或可控制之溫度; 相反地,一觸即發反應系統因反應熱會大量保留在反應系統中,通常反應環境為低蒸氣壓或瞬間溫度飆升之狀況產生。
本公司所採用之鹽酸催化反應去除雙氧水依照文獻定義為一觸即發反應方式[5],依Lu, 2006以RSST 動態軌跡模擬溫度起火-消滅曲線(Critical ignition, extinction temperature curve)結果,隨著溫度增加廠內使用之鹽酸催化過程為由穩定區域(Stable area)進入非穩定區域(Unstable temperature area,即溫度起火及消滅曲線間),但若雙氧水濃度過低,穩定區域面積愈大(詳圖2示意圖),反應愈不容易,需藉由添加大量鹽酸方能提高反應溫度,與友廠試俥結果一致(如表2)。
圖2:起火消滅曲線簡易示意圖
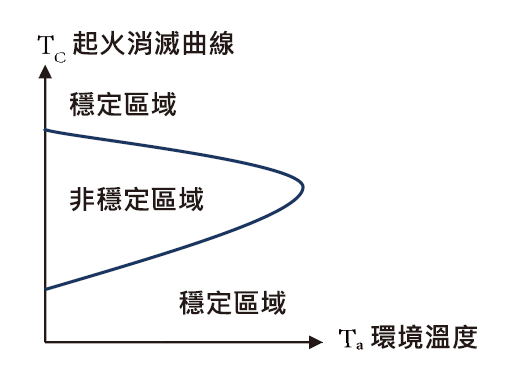
來源酸 | 反應條件 | ||
---|---|---|---|
Tank | D | 反應溫度 (℃ ) | 43.5 |
反應量 (L) | 5,131 | 一次鹽酸秒數 (s) | 5,100 |
來源 H2O2(%) | 0.81 | 二次鹽酸秒數 (s) | 15 |
反應 + 產酸時間 (hr) | 55 |
2.2.2 硫酸稀釋溫升機制
❶水合反應(hydration reaction)
硫酸為二元酸強酸,具高腐蝕性、脫水性、吸水性與氧化性,室溫下穩定,但純硫酸熔點高(283.4K/10.3℃),為方便運輸製成常見之98%硫酸。硫酸與水之所以高度放熱主要因為水合反應,過程中釋放氫離子,由酸度解離係數(acid dissociation constant)得知硫酸與水之強親和性。
H2SO4+ H2O → H3O+ + HSO4− pKa1 = 2.8
HSO4− + H2O → H3O+ + SO42− pKa2 = −1.92
❷溫升放熱焓值(enthalpy)變化
將硫酸與水混合後,硫酸迅速解離H2SO4(l) → H+(aq)+HSO4−(aq),以標準莫爾生成熱計算過程中焓值變化,可大致分為兩種計算方式[6]:
▪無限制量稀釋: 通常適用於一次性方式稀釋(batch dilution process)
H2SO4(l)、H+(aq)、HSO4−(aq)分別為−813.989kJ/molrxn、0kJ/molrxn、−855.75kJ/molrxn
▪固定量稀釋: 通常適用於緩慢添加方式計算(continuous dilution system)
假設熱卡計測量為理想環境,即熱量無任何被吸收及散失,透過比熱容公式計算得知最後稀釋升溫溫度,即可概略得知溫升結果:
q = −qrxn = mS∆T = mS(Tfinal−Tinitial)
依據A. Getnet模擬比對結果如圖3,逐步加酸過程中溫度梯度變化(delta T, ℃)及負載(heat duty, kcal/kg)最大分別為165.04℃及72.81kcal/kg,因此可藉由放熱解決前述2.2.1章節提到之雙氧水濃度過低,鹽酸與雙氧水反應不夠劇烈之問題,一旦溫度升高後,鹽酸與雙氧水反應即進入非穩定溫度區域,取代大量添加鹽酸升溫反應。
圖3:連續稀釋溫度梯度變化及熱負載變化
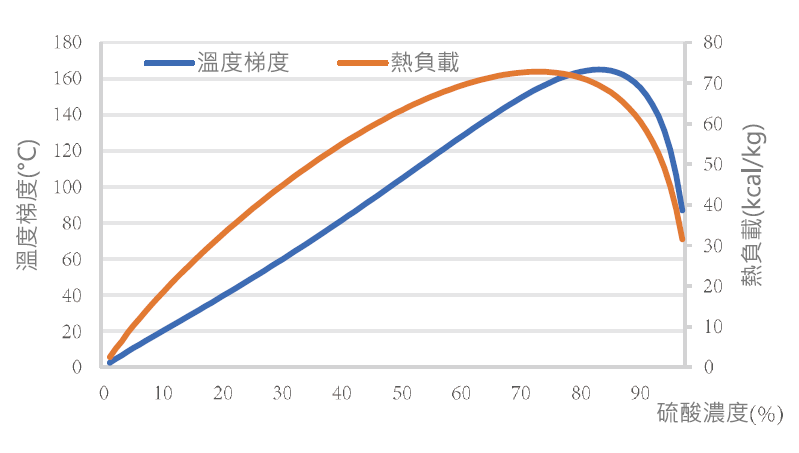
3.實驗方法
本研究為了解硫酸稀釋放熱行為,並進一步探討稀釋法適用硫酸濃度範圍,首先①從源頭分流高低濃度硫酸,進酸前;②水酸混合比例確認,進酸稀釋過程中;➂放熱溫度試算及;➃熱交換器降溫能力預估,作完整溫升判斷,確保稀釋法穩定產酸及供酸,提供予設計部參考並列為標準化設計。
3.1 W-H2SO4高低濃分別收集
為了解現況機台排酸狀況及稀釋法前置作業,與氣化課合作將廢酸源頭切開收集(如圖4),桶槽A專收機台排放雙氧水混合後之低濃度廢酸,桶槽B專收氣化課Flush高濃度廢酸。分開收集結果,桶槽A: 硫酸濃度約75%,雙氧水濃度約0.63% ; 桶槽B: 硫酸濃度約95%,雙氧水濃度約小於0.001%。
圖4:廢酸桶槽高低分流收集對比
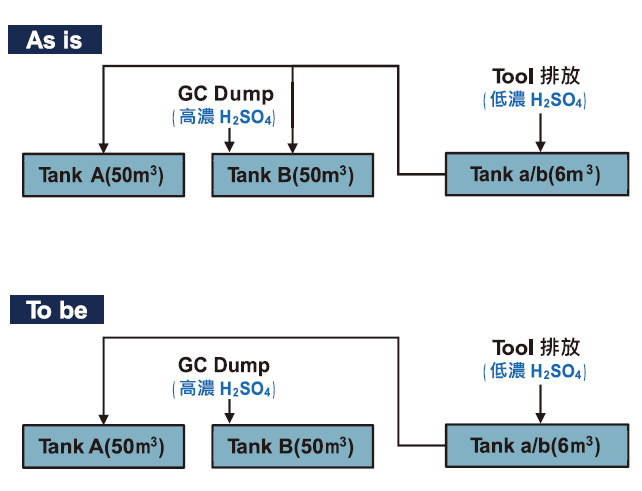
3.2 水酸混合比例確認
首先為確保最終混合後硫酸濃度為60%,透過稀釋前後比重計算稀釋水量體,以酸批次加入水中方式緩慢稀釋。稀釋過程反應溫度上升,比重因體積膨脹而變小,但因變化較小,本文暫忽略計算。試算表如表3所示。
水酸比例 | |
---|---|
稀釋前硫酸 %(w/w) | 95% |
入酸密度 | 1.82g/cm3 |
稀釋後硫酸 %(w/w) | 60% |
稀釋後密度 | 1.5g/cm3 |
總體積 | 7500L |
水體積 | 3017L |
酸體積 | 4483L |
3.3 放熱溫度試算
因反應桶槽氣密完整及保溫效果佳,熱量散失小,反應過程視為理想環境下進行,逐步添加酸至水中。然實驗過程為求謹慎,考量稀釋放熱過程較為劇烈,故採無限制量稀釋計算方式(詳2.2.2節),視為酸一次投入而非緩慢加入。
3.4 熱交換器降溫能力預估
市面上熱交換型式依照流體流向大致分為垂直向流交換(Cross flow)、順向流交換(Concurrent flow)及逆向流交換(Countercurrent flow),本方法採逆向流交換,相關設計圖面及參數如圖5及表4。以95%濃硫酸試算結果,批次添加體積為100L/次至300L/次,添加速率約1L/秒方式添加,稀釋放熱溫度約7-16℃,進熱交換器後降溫效率約1℃/分,因此為符合廢硫酸回收系統運轉溫度不高於90℃再加上安全考量,擬設定78℃為熱交換器啟動溫度。
圖5:廢硫酸熱交換器形式
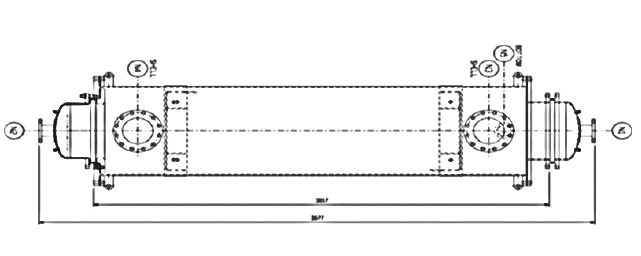
設計條件 | |||
---|---|---|---|
項目 | Shell | Tube | 單位 |
流體 | 水 | 硫酸 | - |
設計壓力 | 4 | 4 | kg/cm2 |
設計溫度 | 90 | 90 | ℃ |
熱交換量 | 217.7 | W | |
入液溫度 | 26 | 85 | ℃ |
出液溫度 | 34.5 | 35 | ℃ |
流量 | 9,000 | 2,400 | L/hr |
熱傳量 | - | 88.7 | W/m2K |
熱交換面積 | - | 102.2 | m2 |
平均熱傳速率 | 24.1 | ℃(ΔTLM) | |
材質 | SUS 304 | PFA | - |
4.結果與分析
本研究欲探討廢硫酸稀釋溫升放熱結果,並進一步比較稀釋溫升搭配鹽酸催化與傳統鹽酸催化方法之反應區別,作為後續新廠標準設計及實廠運轉參考依據。
4.1 稀釋溫升探討
本節依廢酸濃度稀釋結果又細分為低濃度及高濃度探討。
4.1.1 低濃度廢酸稀釋溫升
桶槽內預先置入2.5m3之去離子水,以3m3之75%(w/w)廢酸分批加入(加藥速率公升/秒),最終桶槽內硫酸濃度約50%(w/w)。依據實廠測試結果(圖6)桶槽溫度在前期添加廢酸約0.7m3時,桶槽內硫酸濃度約21%(w/w),放熱結果最為劇烈約0.04℃/公升。繼續添加廢酸1.7m33,桶槽內硫酸濃度約43%(w/w),放熱溫度上升斜率趨緩約0.007℃/公升。最後添加0.6m3廢酸時,溫度由最高溫70℃下降至68℃,由前述可知當添加進去之廢酸濃度與桶槽內硫酸濃度差愈來愈小時,放熱效果愈來愈不明顯,甚至溫度不升反降,當稀釋目標濃度提高,溫度會持續下降,因此低濃度廢酸稀釋過程較為安全。
圖6:75%廢酸稀釋溫升結果
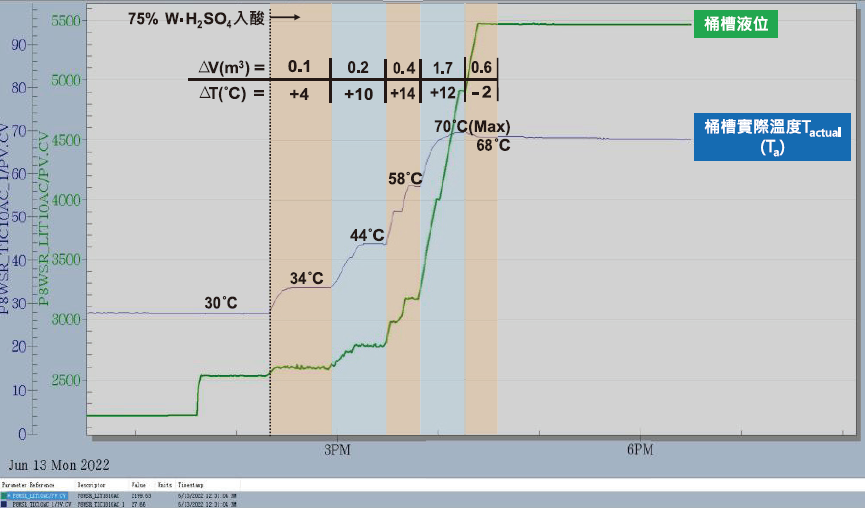
本研究理論計算採無限制量稀釋計算方式(詳2.2.2節),升溫計算結果與實廠稀釋結果趨勢相符(圖7),溫度梯度結果亦同,隨著濃度梯度愈來愈小,最終溫度有開始下降趨勢,結果顯示再加入之廢酸放熱反應不足,故推測稀釋方式適用最低濃度約70%硫酸。
圖7:75%廢酸稀釋實廠結果與理論計算
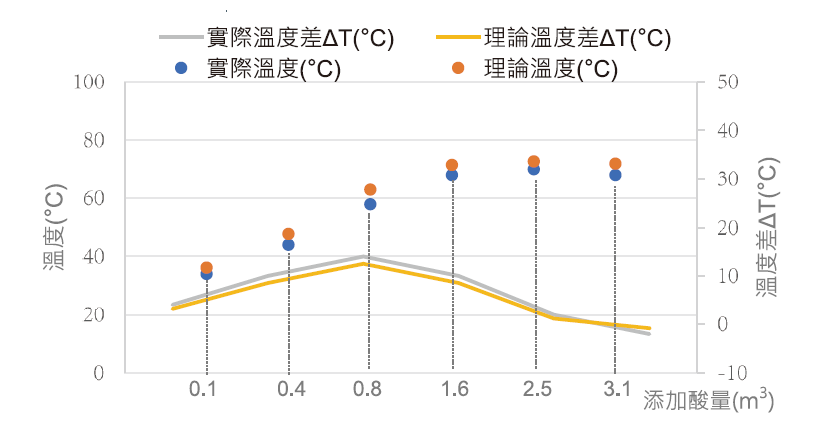
4.1.2 高濃度廢酸稀釋溫升
桶槽內預先置入2.9m3之去離子水,以4.1m3之95%(w/w)廢酸分批加入(加藥速率:1公升/秒,加藥及間隔時間分別為200秒與30秒),最終桶槽內硫酸濃度約60%(w/w)。依據實廠測試結果(如圖8)桶槽溫度在前期批次加入廢酸約0.2m3時,放熱結果極為明顯約0.07℃/公升至0.08℃/公升。廢酸添加至0.75m3後,達熱交換器啟動設定溫度(78℃),後續反應亦持續進熱交換器,隨著廢酸量增加,廢酸濃度與桶槽內硫酸濃度梯度逐漸縮小,每一次之溫度波峰逐漸降低。
圖8:95%廢酸稀釋溫升結果
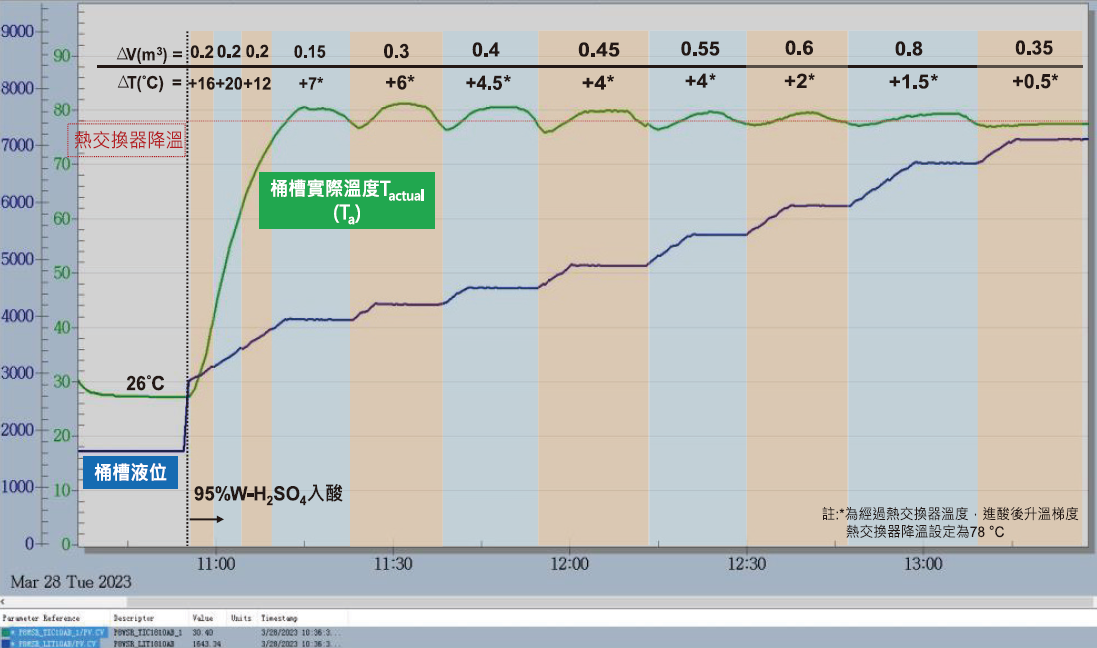
高濃度廢酸稀釋溫升因達熱交換器啟動設定溫度,因此熱量計算上須考量熱交換器降溫效果(詳3.4節),經實際桶槽升溫與理論計算比較(如圖9),隨著廢酸量添加,理論及實際之溫度梯度逐漸放大,其一原因可能為熱交換器降溫效率可能因為現場冷卻水流量(25-30CMH)影響,因此造成偏差,但理論溫度與實際溫度仍非常相符。
圖9:95%廢酸稀釋實廠結果與理論計算

4.2 產酸品質探討
依據友廠測試結果,低濃度雙氧水之廢酸因雙氧水濃度過低,反應溫度及效率極為不佳,需添加過量鹽酸,過程中溫度僅60度左右,反應時間最長達3日左右。相較稀釋溫升後再搭配鹽酸法,可利用溫升達80度以上,根據實廠改善案例,整體系統反應溫度控制於85℃上下,能有效縮短批次反應時間,同時突破傳統鹽酸催化能障,並添加少量鹽酸後即可反應完全,產酸品質由300-400ppm大幅降低至30ppm以下,反應時間由2至3日減少至8至12小時。(表5)
傳統鹽酸法 | Parameter | 稀釋溫升+鹽酸法 |
---|---|---|
>0.4% |
廢酸H2O2 (initial, %) |
<0.1% |
<10 |
產酸H2O2 (final, ppm) |
<10 |
5,000 | HCl dosing(s) | 80-100 |
300-400ppm |
Cl− (final, ppm ) |
<30ppm |
2-3days | Batch duration | 8-12hr |
60-70 |
Reaction Temp. (℃) |
75-82 |
5.結論
本研究欲探討硫酸稀釋溫升是否適用於各廠之可行性與實用性,同時比較文獻回顧之理論計算及實廠試俥之測試結果,結論如下:
- 低濃度廢酸升溫效果理論及實廠測試結果相符,如稀釋目標濃度增加,溫度將下降,因此預期當硫酸濃度小於70%時,升溫效果無法達適合反應溫度。
- 高濃度廢酸雖稀釋溫升急遽,以批次固定添加量及速率,再搭配熱交換降溫效率,可將反應溫度控制於82至83度內,為後續適合反應溫度。
- 低濃度雙氧水之廢酸經比較傳統鹽酸催化法及稀釋溫升搭配鹽酸催化法之鹽酸品質,殘餘氯鹽濃度低,有助於硫酸銨結晶乾燥系統穩定,甚至對於後續公司推動廢棄物再利用有顯著之幫助。
- 新廠建廠初期因供應品質及潔淨度要求,使用大量化學品沖洗桶槽及灌充與供應管線,因此廢酸濃度幾近原酸,藉由稀釋法搭配鹽酸催化法,系統可以較安全方式進行,並解決新建廠初期外購硫酸之問題。
參考文獻
- 李國智,低濃度氫氧化氨、雙氧水混合物在深溝渠式記憶體,2009,國立交通大學。
- Ohmi, T.,“Total Room Temperature Wet Cleaning of Silicon Surface.”, Journal of the Electrochemical Society, vol. 143, issue.9, pp. 2957-2964, 1996.
- J.C. Leung, H.K. Fauske, Runaway system characterization and vent sizing based on DIERS methodology, Plant/Oper. Prog. 6(2) (1987) 77–83.
- J. Singh, Sizing relief vents for runaway reactions, Chem. Eng.(1990) 104–111.
- K.T Lu, C.C. Yang, P.C. Lin, The criteria of critical runaway and stable temperatures of catalytic decomposition of hydrogen peroxide in the presence of hydrochloric acid., Journal of Hazardous Materials B135(2006) 319-327.
- A. Getnet, A. Jejaw, A. Bekele, C. Venkatachalam, Thermal System Design for Sulfuric Acid Dilution Device - A Case of Awash Melkassa Aluminum Sulphate and Sulfuric Acid S. Co., International Journal of Recent Technology and Engineering(IJRTE) ISSN: 2277-3878(Online), Volume-8 Issue-5, January 2020.
留言(0)